Investing For Change At Lightwater Quarries
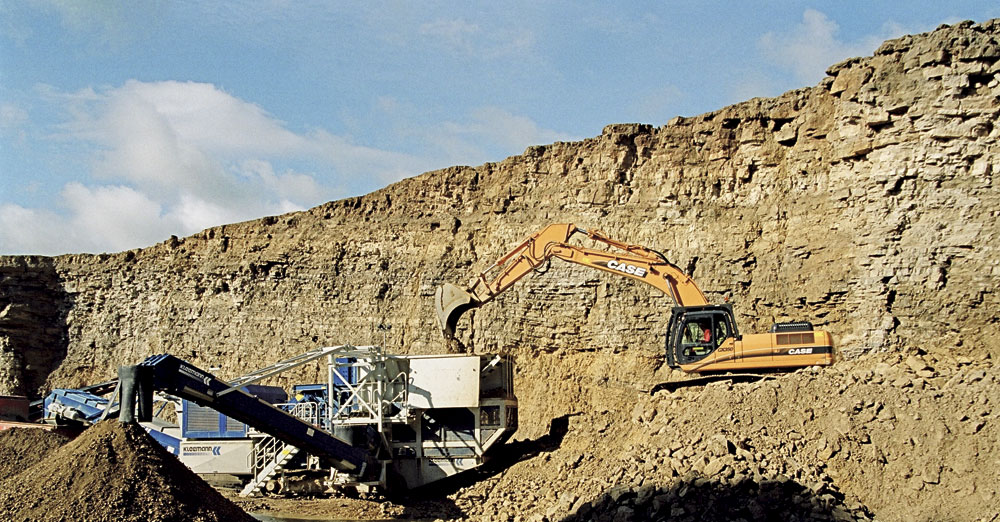
Despite difficult geological conditions, Potgate Quarry maintains its viability by changing extraction methods. Roger Lindley investigates.
In the 1980s, the Staveley family, large landowners in North Yorkshire, began to diversify into the ‘pick-your-own’ business and found they needed water for irrigation purposes. While drilling the borehole, they hit rock which they realized was of marketable quality.
The rest, as they say, is history. The site is today the well established Potgate Quarry, close to Ripon, in Yorkshire, supplying a hard Magnesian limestone for road construction and other applications throughout Yorkshire. The material is processed to meet Type 1 sub-base requirements, washed single-size 10mm, 20mm or 40 mm concrete aggregate, and –5mm sharp sand.
Like many Magnesian limestone deposits, the deposit at Potgate is subject to extensive faulting and clay, which requires careful management to maximize extraction amounts without adding costs. As the quarry is progressing, so the face is entering areas where the clay is likely to increase significantly, yet the stone is harder than ever, achieving a 10% fines value of over 200kN.
Traditional extraction methods were used initially, but as the quarry face progressed the level of faulting became more variable and one area became impossible to work with the existing plant due to the poor quality of the geology. As other areas began to reveal the extent of the faults, the quarry management had to make radical decisions on the extraction methods being used if the viability of the quarry was to be maintained.
Kevin Parker, general manager, explained: ‘We considered different options. One, of course, was to work around the heavily faulted areas. However, this would reduce the available reserves, increase costs, reduce royalty income and impede restoration. Furthermore, there was no certainty how much material we might have to abandon. As such, it was not a real option.’
As part of good quality control and efficiency it was deemed better to assume that faults filled with clay would continue to appear, therefore the management had to find a way of economically processing the material as the existing plant was proving to be incapable of separating the clay, especially in wet weather.
A wobbler grizzly (a screen with rotating elliptical rollers) was one solution. However, due to space restrictions, it was not feasible to simply replace the existing feeders and grizzly screen with a wobbler unit, and the cost involved in moving the aging plant at the central crushing and processing station did not make economical sense.
‘We evaluated various alternatives, a trommel screen being the only one which appeared to offer a solution. However, the cost was substantial, it did not provide the throughput and could not be easily integrated into the existing plant,’ said Mr Parker. ‘There was also a problem with the trommel rolling the clay into balls, which the washing plant struggled to break up.’
With the distance from the faces to the plant increasing, the company decided to take a radical approach and look at the entire extraction, processing and handling demands. As the existing crushing and processing plant was over 20 years old and nearing the end of its serviceable life, the company undertook a detailed analysis of material content, production demand, haul distance, employee numbers, and associated cost factors with different solutions such as haul units versus conveyor systems, shovels versus excavators etc.
The solution that is now being implemented, with the first phase already operational, includes the use of a Case hydraulic excavator as primary loader feeding a customized Kleemann mobile crusher with integral wobbler grizzly. This will be developed further with a conveyor system replacing the current haul units.
Quarry operation
The quarry works a 15m high face. Depending on the situation, 4,000 to 18,000 tonnes of material is released by the drill-and-blast programme, which takes place as required, typically every nine days. The drilling contractor uses 105mm holes charged with ANFO on a 4m x 4m grid pattern.
All loading is carried out by a single 36-tonne Case CX350 excavator. This replaced a 45-tonne excavator which was under-utilized due to idle time waiting for the dumptruck. The Case machine is well matched to the Kleemann crusher, achieving many more cycles in a day but never standing idle. The new excavator was supplied and is serviced under warranty by Guisborough-based Case dealers C.J. Leonard & Sons.
‘With a daily output target of 2,000 tonnes, the reliability of the equipment was of paramount importance,’ said Mr Parker. ‘We had to choose a mobile crusher and a primary loader sized to meet the daily throughput requirement — the loader being the most critical as there would be no back-up alternative. We considered various options and decided on the Case CX350, which, with proven Sumitomo technology, would provide the reliability and productivity demanded.’
The excavator was delivered in January 2006 and is equipped with a purpose-built Miller UK heavy-duty rock bucket. The bucket, which is 48in (1,220mm) wide and has a 1.5m3 capacity, is designed to fit inside the crusher feed hopper to help clear blockages. For maximum wear life it is fitted with a Kverneland master lip plate and Kverneland bolt-on penetration teeth. ‘The excavator has lived up to expectations. We have had no downtime since the machine was delivered and the operator finds it extremely responsive,’ said Mr Parker.
To assist in loading difficult materials, the CX350 features an automatic Powerboost function, which detects more demanding situations and increases breakout force at the bucket by up to 10% for a period of 8s, from a standard breakout force of 24,840daN to more than 27,000daN, regardless of whether the machine is being operated in heavy, standard or light work mode. For improved fuel efficiency, the 185kW Isuzu engine can also be set to automatically return to idle when demand is no longer required.
The CX350 is configured with a 3.20m long dipper arm to give the machine optimum reach (up to 10.37m) over the bench, thereby minimizing machine repositioning. An ‘X’ type undercarriage design provides high levels of rigidity and improved stability, while the high ground clearance of 480mm allows the excavator to travel across the rough quarry terrain safely.
For added protection in dusty environments, the excavator is equipped, as standard, with an ‘Ultra Clean’ hydraulic filtration system, which effectively filters contaminants as small as one micron. This has the benefit of reducing costs by extending servicing intervals to 5,000h.
The Kleemann MRB122RR mobile primary impactor fed by the CX350 is fitted with a 12-roller wobbler grizzly and was built to a bespoke specification including a 7.5m radial side belt, stairway access instead of a ladder (for safety) and speed sensors on the conveyors to stop the feeder in the event of a system failure.
‘Kleemann were chosen because the MRB122RR has the capacity and ability to handle the deposit, and the company were willing to customize the machine to incorporate the many small changes that we felt we needed,’ explained Mr Parker.
The unit is also enhanced with an auxiliary power socket and a larger than normal fuel tank. Demonstrating the company’s safety and environmental policies, Lightwater Quarries also insisted that the fuel tank be capable of being filled from ground level to reduce the risk of spillage and falls.
According to Lightwater, the performance of the wobbler feeder section has exceeded expectations. The elliptical rollers remain clear and separate the stickiest clay from the stone. When the rock pile is pure stone the undersize from the wobbler can be diverted on to the main conveyor to combine with the crushed rock.
With a capacity of 450 tonnes/h, the 85-tonne machine features a 6.5m3 feed hopper, a 1,270mm x 1,000mm crusher opening, a vibrating feeder under the crusher, a 1,400mm wide main belt and a DC12 Scania engine with a 540kVA Leroy Somer generator.
The Kleemann MRB122RR feeds a Finlay 693 twin-deck screen unit producing Type 1, clean 75/50mm and clean 125mm, as required, while the 65mm scalpings from the mobile crusher are taken to the washing plant for further processing.
Currently, the material is moved to the stockpile area using a rigid dumptruck loaded by a wheel loader. However, as the haul distance is already 600m, the company is planning to install a field conveyor system within the next two years to provide greater economies and flexibility as the quarry face advances. The alternative would be an additional haul unit plus driver.
‘Our decisions so far appear to have been the right ones. The equipment is proving reliable and able to handle the difficult material. We are getting the throughput required and have only minor disruptions,’ commented Kevin Parker.
Annual production at Potgate is 350,000 tonnes per year, which means that with current reserves the life expectancy of the quarry could be another 10 years, assuming the quality of material is such that it can be processed economically. The total quarry area available exceeds 64ha.
Managed environment
The Staveley family, which owns the quarry and surrounding land, having been farmers for over 400 years, are aware of the importance of preserving the environment. Potgate Quarry is a good example of an environmentally managed quarry. Landscaped bunds located on the quarry perimeter ensure that there is no visual impact and exhausted areas of the quarry are quickly reverted to pasture land.
When advancing the face, the layer of topsoil, typically 300mm, is carefully removed and stockpiled for reuse. The 0.5–8m (in the deepest dip) of overburden is also stockpiled for use in landscaping the worked-out areas.
Where applicable, equipment purchased has to comply with pollution prevention and control authorization. To minimize disturbance from noise, equipment only works between 7.30am and 6.00pm Monday to Friday, and Saturday morning. The quarry employs seven operatives plus administration and senior management. A single weighbridge is sufficient to manage the flow of highway trucks.
Lightwater Quarries Ltd, a company wholly owned by the Staveley family, also operate Gebdykes Quarry, approximately 11km away. The weighbridge at Gebdykes is fully automated and linked by computer to Potgate.
Acknowledgement
The editor wishes to thank Lightwater Quarries Ltd for their co-operation in the preparation of this article.