Full Steam Ahead at Angerstein
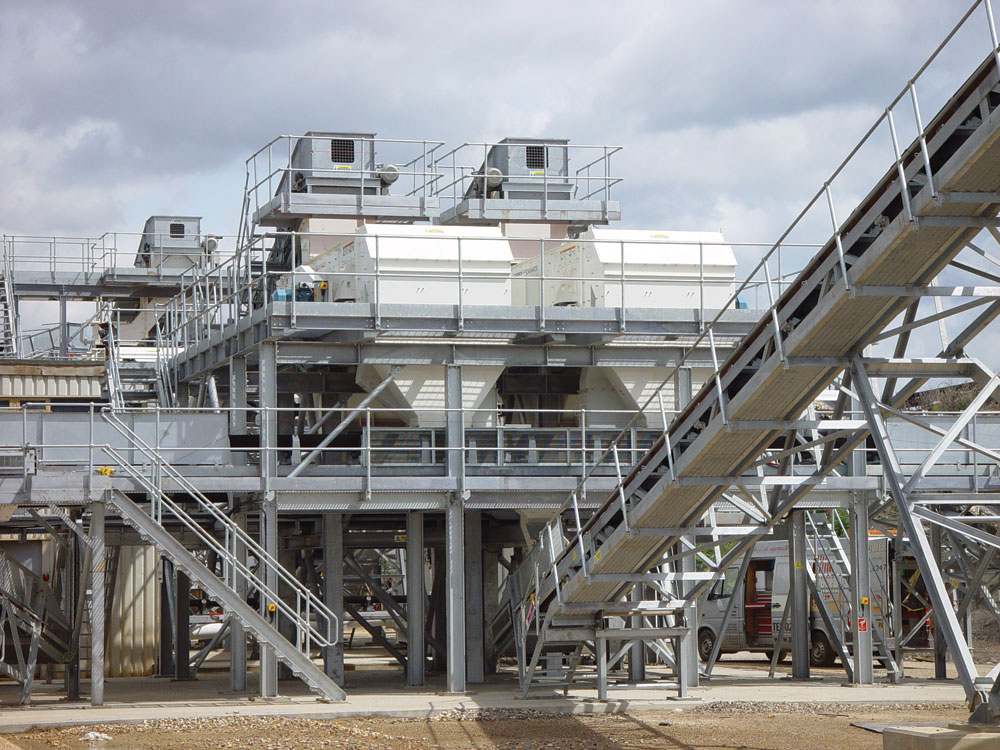
Fire-damaged wharf back on course following £2 million replant
Earlier this year CEMEX completed a major reconstruction project at their Angerstein Wharf marine aggregates facility on the south bank of the Thames, just a few hundred metres downstream from the Millennium Dome in Greenwich, as part of an ongoing, year-long, £60 million national investment programme spanning their entire UK business.
Developed as a replacement for the former Orchard and Barking wharves on the north side of the river, Angerstein Wharf was originally established in 1991 by St. Albans Sand & Gravel (subsequently part of the RMC Group) to produce 10mm and 20mm gravels and a single grade of sharp sand. The facility was constructed at a cost £12.5 million (including piling works etc) on freehold land that had been acquired by the company some two years earlier.
The recent £2 million replant at Angerstein was required to bring the plant back on stream following a serious fire at the site in October 2004 (prior to CEMEX ownership) – an incident which began during routine maintenance work when sparks from a welding torch inadvertently set light to a rubber lined pipe. The ensuing blaze quickly spread to other parts of the plant, destroying two screen houses together with associated conveyor equipment and resulting in the complete cessation of processing operations at the site.
Despite this setback, new owners CEMEX continued to service the wharf’s customers during the subsequent demolition and clearance work by sourcing materials externally. In August 2005, some 10 months after the fire, the situation was eased when a fully mobile, 200 tonnes/h Powerscreen sand and gravel plant, supplied by DUO (Europe) plc, was installed at the site to provide a stopgap processing capability.
Operated on a double-shift (20h/day) basis, this plant was more than capable of producing 70,000 tonnes per month and proved to be a highly effective interim solution to CEMEX’s immediate supply problem. Indeed, the plant was so successful both commercially and operationally that DUO (Europe) were subsequently awarded a ‘one-stop-shop’ contract for the supply and installation of the replacement fixed plant at Angerstein.
Whereas the original twin-line 750 tonnes/h plant had been considerably over-complicated in its design, and in reality never achieved more than 450 tonnes/h, the new plant would comprise a much simpler modular arrangement, again with twin processing lines but this time with a nominal output capacity of 400 tonnes/h. In contrast with the previous plant’s eight screens, single crusher, 19 conveyors, 28 pumps and seven staff, the new plant would achieve similar end results using just four screens, one crusher, 15 conveyors, one pump and four staff.
Following the placement of concrete foundation pads and the installation of mains water and electricity supplies, DUO commenced work on site in late December 2006, with the main plant build taking place during January 2007. Operation of the adjacent mobile plant was maintained throughout the build phase to ensure continuity of supplies.
The raw material processed at Angerstein Wharf is obtained from licensed dredging areas in the Thames estuary and Eastern Channel by CEMEX’s Sand Fulmar and Sand Falcon dredging vessels. An average of three shiploads are landed at the wharf on a weekly basis, each load comprising around 7,500 tonnes of sand and gravel. The as-dredged materials are known as Greenwich Light East, which largely comprises –70mm gravel with coarser sand, and North and South Lowestoft, which largely comprises 10mm gravel and finer sand, respectively.
The materials are unloaded from the self-discharge dredgers at a rate of around 2,000 tonnes/h and deposited in a reception hopper located at the end of Angerstein’s mooring jetty. From here the material is brought ashore by an inclined conveyor that discharges on to the site’s existing high-level tripper conveyor system to create a 50,000 tonne capacity stockpile of as-dredged material from the two source areas.
A 50/50 blend of the materials is collected from the stockpiles by a Volvo L180E loading shovel and fed to the new 400 tonnes/h twin-line processing plant via a 50-tonne capacity feed hopper. This unit is equipped with 100mm grid bars and a variable-speed feed belt, which in turn feeds on to a 31m long x 800mm wide inclined conveyor. Rated at 400 tonnes/h and equipped with an Eriez permanent magnet, this conveyor discharges the –100mm material into a reception chute arrangement, which also accepts a recirculated feed of crushed oversize material.
From here the –100mm material is fed on to a 20m long x 800mm wide 650 tonnes/h inclined conveyor that feeds into a two-way discharge chute/boiling box arrangement, allowing either one or both processing lines to be utilized. Material is sent forward to two double-deck 20ft x 6ft Cedarapids horizontal rinsing screens, supplied by DUO. Any oversize +70mm material is scalped off at this point and sent to an adjacent ground storage bay via a 13.4m long x 800mm wide stocking conveyor, while the –6mm underflow (sand) content is flumed to two Powerscreen Finesmaster 200 sand plants. Dewatered sand from both Finesmasters is discharged on to a 26m long x 800mm wide catenary conveyor rated at 280 tonnes/h, which in turn feeds on to a 24m long x 800mm wide powered radial stockpile conveyor. The minimal amount of waste silt produced (around 2.5–3%) is flumed to the site’s existing treatment plant, which incorporates a 10 tonnes/h Wemco belt press.
At the same time, the –80mm +6mm fraction from each rinsing screen is sent forward via a pair of 24m long x 800mm wide inclined conveyors. Rated at 260 tonnes/h, these conveyors feed two more 20ft x 6ft Cedarapids horizontal screens, again supplied by DUO. Material passing the top decks is fed on to a 30m long x 800mm wide stocking conveyor to produce a 20mm final product stockpile, while the material passing the bottom decks is discharged on to a 24m long x 800mm wide powered radial stockpile conveyor to produce a 10mm final product stockpile.
Meanwhile, the –80mm +20mm oversize material is delivered on to a 16m long x 800mm wide reversible horizontal conveyor. Rated at 180 tonnes/h, this belt feeds on to a 32m long x 800mm wide inclined crusher feed conveyor but, when necessary (eg during crusher maintenance), can be reversed to send the oversize to a ground stockpile via a 12m long x 800mm wide stocking conveyor.
Rated at 180 tonnes/h and equipped with an Eriez permanent magnet and metal detector, the crusher feed conveyor discharges the oversize into a 50-tonne capacity crusher surge bin. A Siemens Multi Ranger level sensor determines when to start/stop a Rotex vibrating tray feeder, which is used to choke-feed the Pegson 1000 Automax cone crusher. Crushed material is fed on to a 26m long x 800mm wide inclined belt conveyor for transfer back to the reception chute arrangement mentioned earlier, where it is combined with the as-dredged feed material.
The plant specification includes fully galvanized heavy-gauge steelwork and guarding throughout, remote greasing on all bearings for ease of maintenance, fully linked trip wires designed to shut down the entire plant instantaneously should any wire be activated, and multiple wash-down points for maintaining site cleanliness. A moisture-reduction system has also been installed beneath the sharp sand stockpile to increase the rate of drying. Plant operation is via a touch-screen, with full start/stop, alarm, history recording and fault diagnostic capabilities. At any time the plant can be run in full twin-line specification or with one of the two processing lines shut down.
In its current configuration, Angerstein Wharf is capable of delivering around 1,400,000 tonnes of clean sand and gravel per annum, when operating at full capacity. Already featuring significant improvements over its predecessor, the plant’s ‘future-proof’ design is such that further modifications over time will allow it to keep pace with any significant changes in demand over the next 25–30 years.
Approximately 80% of current production is supplied internally to CEMEX’s ready-mixed concrete plants at Stepney, Canning Town, White City, Hendon and Kings Cross, with a fleet of 26 tipper trucks operating out of the site to provide the necessary transportation. In addition, the company’s newly commissioned 120m3/h Liebherr Betomix concrete batching plant, located on a site adjacent to Angerstein Wharf, takes around 80,000 tonnes/year. Facilities at the site also include a 450 tonnes/h barge-loading system, which is used for the supply of washed sharp sand to CEMEX’s ready-mixed concrete plant in Fulham.
Looking to the future, CEMEX plan to develop Angerstein’s sales to the open market and are also looking to capitalize on the impending Olympic Games and Thames Gateway developments. At its peak, work on the Olympic facilities alone is expected to require up to 9,000 tonnes of construction aggregates on a daily basis. Although competition for a share of this market will undoubtedly be fierce, CEMEX believe they are now in their best–ever position in central/east London and north-west Kent, and say their Angerstein, Northfleet and Dagenham wharves form a triangle that will be ideally placed to supply aggregates and concrete direct to the heart of the Olympic construction sites via the river Lea.
Acknowledgement
The editor wishes to thank CEMEX for permission to visit the site and, in particular, David Whitby, unit manager, and Glyn Richards, regional operations manager, for their help in preparing this report.