Denham Quarry Comes On Stream
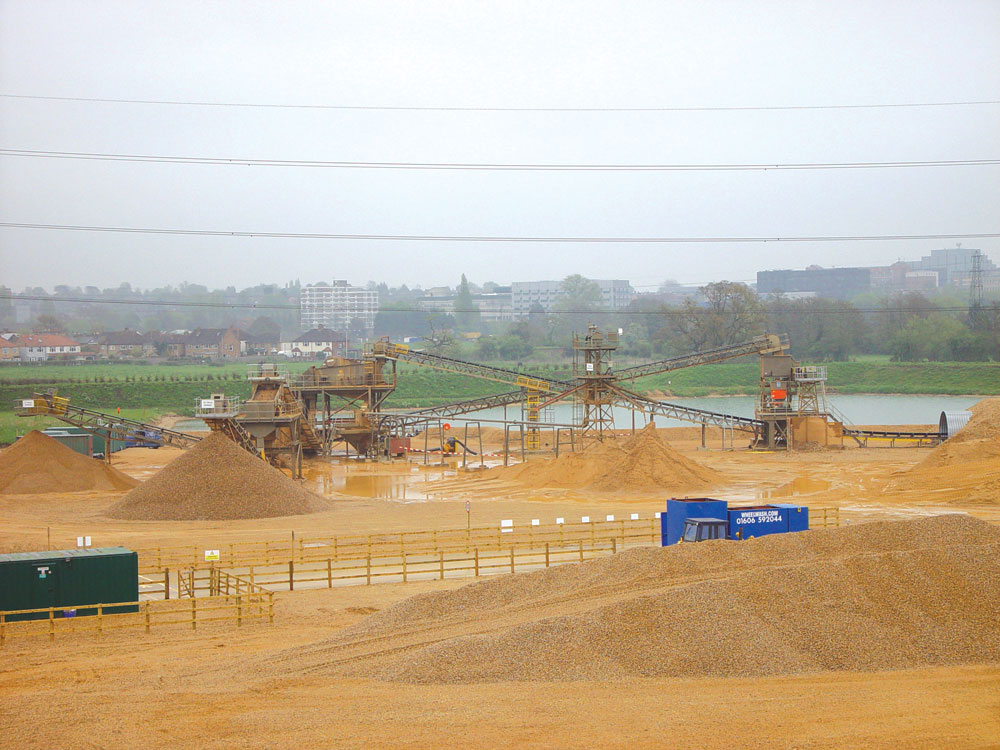
Summerleaze open new sand and gravel operation west of London
Since their foundation over 80 years ago, sand and gravel extraction has been at the core of Summerleaze Ltd’s operations and today provides a solid base for the company’s more recent diversification into waste management, sustainable energy and power generation. Aiming to make the most of under-valued resources, the privately owned company’s operations now encompass anaerobic digestion of organic waste, the production of renewable hydrogen and oxygen by electrolysis, and the marketing of wood pellets for biomass heating.
Quarrying, however, continues to play the leading role in Summerleaze’s portfolio of activities and the location of the company’s principal sand and gravel sites on the Berkshire/Buckinghamshire border, in close proximity to the M4, M25 and M40 motorways, means the firm is exceptionally well placed to supply materials into west London and the conurbations to the west of the capital.
In early 2007 Summerleaze successfully secured planning permission to extract 2.4 million tonnes of high-quality sand and gravel over a 12-year period from greenfield land south-west of Denham, in Buckinghamshire, close to the intersection of the M25 and M40. Following initial site development work and plant installation and commissioning, this £4 million operation came on stream at the beginning of 2009 and is now set to supply a significant proportion of its 200,000 tonnes/year output to an on-site ready-mixed concrete plant, owned and operated by London Concrete Ltd, under the terms of a supply agreement.
This mutually beneficial arrangement between the two companies means that not only is there a convenient supply of high-quality sand and gravel available to the concrete plant, but there are little or no transport costs, fuel consumption, traffic problems or related emission issues to contend with in getting it there. Planning permission has also been obtained for an on-site bagging plant located close to the concrete facility, and a similarly beneficial third- party supply agreement for bagged aggregates is expected in the future.
Planning process
The 57ha site, near Denham, had been earmarked as a ‘preferred area’ for sand and gravel extraction in Buckinghamshire’s Minerals Local Plan for more than 10 years and was also identified in earlier minerals plans dating back as far as 1978. The land itself is owned by Buckinghamshire County Council and, in recent years, has been used for crops and horse grazing by three tenant farmers.
In the mid-1990s the area had been viewed a possible site for a new rail freight depot, but in 2001 the county council set about marketing the site as a potential extraction opportunity. The following year Maidenhead-based Summerleaze secured an option to take out a lease on the land and soon afterwards embarked on what proved to be a protracted and complex mineral planning process. The company’s formal planning application was eventually submitted in January 2006 and, after consultation, finally received unanimous approval – albeit with a total of 73 conditions attached. These requirements took Summerleaze several more months to fulfil before full permission was finally granted in March 2007.
Among the numerous hurdles that had to be overcome at various stages during the planning process were specific requirements relating to site access, archaeology and hydrogeology. In addition, the site’s close proximity to Heathrow Airport and RAF Northolt, and the fact that the quarry is to be worked wet with final restoration to lake-based activities, necessitated lengthy negotiations with British Airports Authority and Defence Estates over ways to reduce the risk of bird strike. Eventually, mitigation was achieved in the form of a bird-management plan that allows for limited restoration to lakes and includes an undertaking to monitor and control particular bird species.
Highway authority insistence on the construction of a new 65m diameter, five-exit roundabout at the entrance to the quarry on the busy A412 was another significant hurdle for the company, and one that had to be completed before any development work on site could begin. But despite yet another lengthy process, this time involving design, licensing and construction work, the finished roundabout junction does provide an important benefit by ensuring vehicles have safe access to the site without passing through nearby residential areas.
Another difficulty that came to light early on in the site investigations was the discovery of evidence of prehistoric flint working. Archaeological investigations revealed the presence of several isolated areas or ‘scatters’ containing thousands of ‘knapped’ flints dating back to the Mesolithic period. Although deemed to be of national and/or regional importance, Summerleaze were unable to justify the cost of excavating these scatters and have instead made a slight modification to their original extraction and restoration plans in order to protect and preserve several of these areas in situ, while others will be removed under close and effective supervision or intermittent watching brief as extraction progresses.
Considerable mitigation work was also carried out to reduce the impact of the site on Southlands Manor, a Grade-II listed building that sits adjacent to the north-western boundary. Existing hedges, together with a new 2m high acoustic fence and the lowering of the ready-mixed concrete plant area by some 2.5m, have effectively reduced site noise and visual impact to acceptable levels. Other properties and residential areas in close proximity to the site are separated from the development by 150m wide stand-off/buffer zones.
Hydrological and hydrogeological conditions also had to be carefully considered, as the economic deposits at the site are underlain by around 5m of clay, beneath which groundwater is present under artesian conditions. Again, considerable effort was expended in designing the extraction operations to prevent any possibility of this clay layer being breached and, as a consequence, the full depth of sand and gravel cannot be extracted in some areas of the site. Moreover, as the site is bounded to the west and east by the rivers Alderbourne and Colne, respectively, a detailed flood risk assessment had to be carried out. This revealed that the phased development of the site would actually have a beneficial effect by increasing flood storage capacity from its current level. Both of these rivers are to be protected from the extraction operations by 30m wide corridors, while Rusholt brook, a small watercourse that previously flowed through the middle of the site, has been diverted around the north-east periphery.
Other restrictions on site include the presence of three overhead high-voltage power lines and seven pylons, which will remain within the extraction area, as well as a public footpath that follows the northern boundary of the site and crosses the quarry access road. Here, an electrically operated gate and traffic light system, activated by users of the footpath, has been installed to overcome any potential safety issues.
Site development
With planning permission formally granted on 30 March 2007, site development work began almost immediately, the first task being the construction of the new roundabout and the site’s bunded/landscaped access road. This project was awarded to Ashridge Construction, who commenced work in April and completed the contract in September 2007. Next came the initial muckshift involving around 250,000m3 of material. This included the stripping and placement of soil and overburden into temporary storage and perimeter screening bunds, the re-profiling and regrading of the main plant area to raise it above the water table, and the creation of the first fresh-water lagoon.
The site is to be worked in five main phases, each of which will be divided into a number of smaller sub-phases. Extracted material from each successive working area will be fed to the processing plant by field conveyor, which will reach a maximum length of around 900m. The aim of the sequential method of working is to allow for mineral extraction and the joint creation of silt lagoons, while permitting progressive replacement of the stripped soils and overburden for restoration purposes.
The depth of the sand and gravel deposit varies from a minimum of 2.5m to a maximum of 8m, but averages around 5m across most of the site. The material itself is fluvial in origin and comprises approximately 70% gravel and 30% sand. With groundwater conditions at Denham dictating a wet method of working, a long-reach excavator, on hire from Rayner Plant, is currently being used to extract the deposit, while two fully-specified Volvo L150F wheel loaders equipped with ‘boom suspension’, both on long-term hire from John Hanlon & Co., fulfil field conveyor loading and other material-handling duties.
Processing plant
Representing an overall investment of around £4 million, at the heart of the Denham operation is a 180 tonnes/h processing plant comprising a combination of brand new equipment, together with a number of second-hand items salvaged from Summerleaze’s former Eton Aggregates joint-venture processing operation at Dorney Reach, including half of the main feed conveyor (first rise), the second rise, two screens, a crusher feed box and a 10mm product conveyor. Leicestershire-based Wileman Engineers Ltd were appointed as principal contractors and successfully managed the integration of the old and new elements of the plant during a six-month build programme, which began in June 2008. Following trials and commissioning in December, the plant became fully operational at the beginning of January 2009.
As-raised sand and gravel is delivered to the plant surge pile at a rate of 200 tonnes/h by the part-new, part-refurbished field conveyor with its cantilevered stockpile tower section. Fitted with a 750mm wide belt, a 45kW drive drum and horizontal tension unit, this conveyor also features a Wileman PP800 motorized clay picker to remove any unwanted large lumps of clay. Material reclaim from the 180-tonne live-feed section of the surge pile is achieved by means of a 700mm x 700mm Rowecon motorized cut-off door and 1.17m x 800mm Skako vibratory tray feeder combination, located within a generously proportioned (4m diameter) Armco recovery tunnel. A 68m long x 1,000mm wide plant feed conveyor delivers the reclaimed material to a 6m x 2.2m Hewitt-Robins two-and-half-deck horizontal wet screen for primary separation and washing.
Designed to accept up to 290 tonnes/h of –200mm material (including up to 90 tonnes/h of –20mm crushed gravel), the top half-deck on this unit takes out the +100mm reject fraction, while the lower deck takes out the –6mm sand fraction. Meanwhile, the –20mm +6mm intermediate fraction is conveyed to a 5m x 1.8m Parker Rapide single-deck inclined screen for separation into two final product gradings (–20mm +10mm and –10mm +6mm), while the +20mm component is sent for crushing via a 45.2m long x 650mm wide returns conveyor and 10-tonne capacity crusher surge bin equipped with an overflow facility and Skako vibratory tray feeder. This feeds into a brand new Sandvik CH430 cone crusher, powered by a 90kW motor, to produce a nominal –20mm product, which is recirculated to the primary screen in a closed-circuit arrangement.
At the same time, the –6mm fraction is pumped to a Linatex sand plant comprising a modified no. 7 coarse-sand tower, a 200 sand pump and a no. 5 regulating sump. This equipment was originally acquired from the Falkland Islands in the early 1990s and subsequently commissioned at Summerleaze’s site at Bray, before being resurrected at Denham, albeit in a revised form complete with a new classifier, new sections of pipework and the latest motorized feed boot and wind turbine arrangement on the sand tower. Owing to the nature of the mineral deposit at Denham, the dewatered sand product tends to be very coarse and is, therefore, blended with imported fill sand to bring the final product into the correct grading.
Other new facilities at Denham include a 100-tonne capacity VS500S weighbridge supplied by Precia-Molen, a Wheelwash Rhino Multi vehicle-washing system, and a solar-powered loop recorder supplied by CA Traffic Ltd, which automatically counts vehicle movements in and out of the site. A new manager’s office, new weighbridge office and new workshop facilities, together with second-hand mess facilities, complete the site infrastructure for the quarry’s five permanent staff.
Markets
One of the main markets for the 200,000 tonnes/year operation will be London Concrete’s new on-site ready-mixed concrete plant, which is expected to take up to 80,000 tonnes/year, while in due course a substantial amount will also be supplied to the proposed on-site bagging plant. Thanks to the quarry’s strategic location close to the M25 and M40 motorways, the bulk of the remaining output will be supplied into markets to the west and north-west of London, mainly within a 10-mile radius of the site and largely by way of collect trade.
With the aggregates market currently suffering the effects of a severe downturn, the opening of the Denham operation will provide Summerleaze with a timely opportunity to temporarily shutdown their other major processing facility at Bray, near Maidenhead. This plant has been working almost constantly since 1990, at times reaching throughputs of around 500,000 tonnes per annum, and is currently in need of major refurbishment.
Site restoration
As operations advance, the Denham site will be progressively restored to conditions suitable for eventual mixed use for amenity, nature conservation and recreation purposes, including three separate lakes, while minimizing any increased risk of bird strike which could affect London Heathrow and RAF Northolt. To mitigate this risk, the proposed water bodies will represent no more than 40% of the final restoration and their potential for use by large, flocking water fowl will be minimized by steep-edges and deep water with limited marginal vegetation. However, achieving the specified area of open water will be dependent upon the use of imported infill, and to this end Summerleaze have applied for a PPC licence to permit the filling of flooded worked-out areas with some 500,000m3 of inert fill to raise the ground level.
Across the remainder of the site, widespread broadleaf woodland, willows and tall grassland will be used to further minimize the site’s attractiveness to large flocks of birds, and by the time final restoration is accomplished, Summerleaze will have planted a total of 78,000 trees and bushes.
On completion of the restoration work, Buckinghamshire County Council, as the landowner, will, once again, take on full responsibility for the long-term management and use of the site, including the development of proposed recreational facilities for sailing, rowing and nature conservation.
Acknowledgement
Thanks are due to Summerleaze Ltd and London Concrete Ltd for permission to visit their respective operations at Denham, and, in particular, Mike Lowe, director of Summerleaze; Steve Rackley, quarry manager; and Tony Leng, concrete plant manager, for their help in preparing this article.