Customization is the key at Brooksby
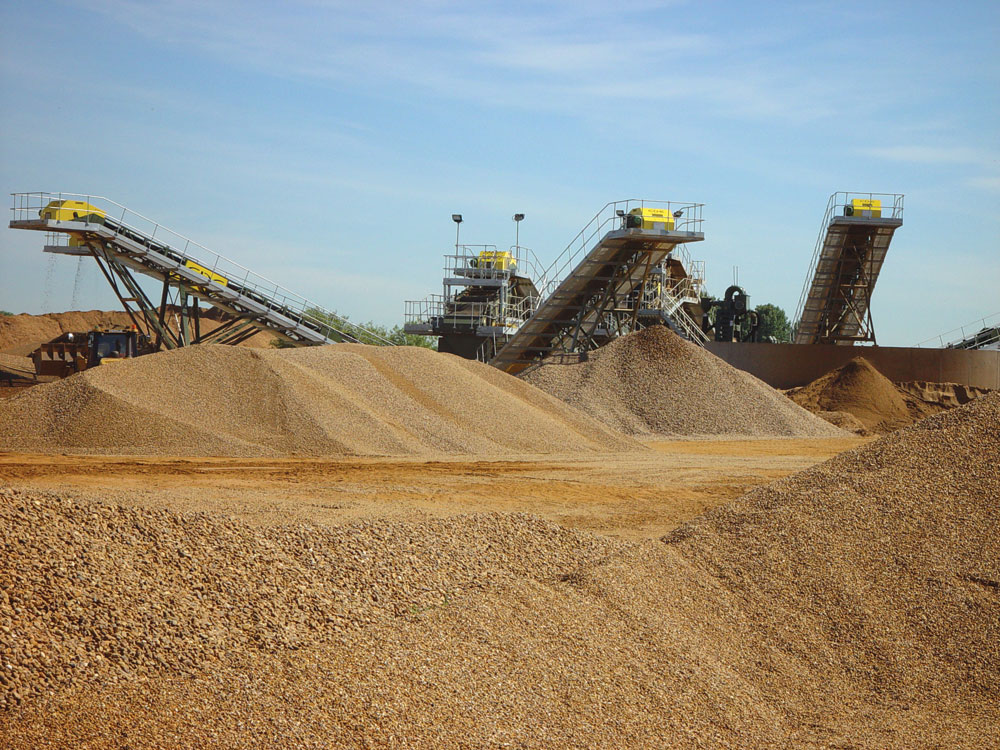
Increased efficiencies at a Lafarge sand and gravel quarry following the introduction of a turnkey washing plant from CDE Ireland
Brooksby Quarry, near Melton Mowbray in Leicestershire, is a relatively new addition to the Lafarge portfolio, having opened for business in early 2007. The company has a licence to extract 300,000 tonnes per annum of sand and gravel from the site, which, at current capacity, will allow for 15 years’ production. As extraction progresses the site will be progressively restored to agricultural land and a complex of lakes.
Lafarge opened discussions with CDE about a new washing plant at Brooksby in late 2007, as a result of difficulties they were experiencing in processing the sand and gravel at the site. The presence of clay in the raw feed was proving to be a problem for the quarry’s original off-the-shelf processing system, which, in turn, was having a significant impact on the quality and commercial value of the final products.
A key factor in the selection of CDE to provide the solution to this problem was their ability to customize the new plant to suit the specific characteristics of the feed material. ‘We had already been down the off-the-shelf route and it had not been successful,’ explained quarry manager Will Laycock. ‘We set very high standards in relation to final product quality, and these standards dictated that we should seek to address the issues raised by the level of clay in the feed material.’
Tackling this issue began with detailed materials testing at CDE’s laboratory in Cookstown, Co. Tyrone. A substantial quantity of the raw material was analysed to gain a clear picture of the typical grading that the plant would be required to process. Once this had been determined, CDE’s technical design engineers were then able to put together a bespoke plant capable of producing the final products required by Lafarge – in this instance three aggregate grades and two sands (coarse and fine).
For their part, Lafarge were able to provide CDE’s engineers with detailed information on the gradings of the required final products, and from this the constituent parts of the plant were adapted by CDE to produce the results.
Given their previous experience at the site, Lafarge were also keen to include a number of performance guarantees within the order for the new washing plant. These covered gradings for all the final products and the lagoon water, as well as the final moisture content of the sand products. ‘The introduction of the performance guarantees on the plant was a critical factor for us in order to ensure that this considerable investment delivered the required results,’ explained Andy Morris, Lafarge’s national production manager in the UK. ‘We were very impressed with CDE’s willingness to work with us on these guarantees, which demonstrated a level of confidence in their capability that is not the norm in our experience.’
In turn, a key factor for CDE in accepting the performance guarantees requested by Lafarge was the level and clarity of information made available to them prior to the deal being done. ‘With access to the amount of information provided by Lafarge, we were able to produce a large amount of data outlining what our plant would achieve,’ explained Dermot Murphy of CDE’s technical specification team. ‘Over the last 17 years we have continually analysed plant performance and made design adjustments where required. We know what our plants are capable of and this confidence allows us to enter into agreements around final product specification, such as the one agreed for the Brooksby plant.’
Plant set up
The final plant configuration installed at Brooksby Quarry draws on a range of equipment from the CDE portfolio, including hoppers, conveyors, ProGrade screens (for both rinsing and dry sizing), a new AggMax attrition and classification system, and an A-series EvoWash sand plant.
However, installation and commissioning of the plant was delayed following the unforeseen discovery of significant archaeological remains on site in mid-2008. ‘During preparation for the plant to be delivered to site, we discovered materials that were later revealed to be from the Palaeolithic period,’ explained Will Laycock. ‘This required some adjustments to the location of the plant and held up proceedings for a number of months while detailed on-site investigations were carried out. Throughout this process, and during the actual installation and commissioning, we were very impressed with the project-management approach adopted by CDE.’
The 180 tonnes/h plant recently completed final commissioning and initial tests on the end products have shown a considerable improvement in quality compared with the processing system previously used at the site.
The feed material is now loaded into a CDE feed hopper, which, in turn, discharges on to a horizontal ground conveyor. This transfers the material to a 28m static feed conveyor for delivery to the primary screen. Due to the levels of clay in the feed material, the feed conveyor is fitted with Hosch scrapers to ensure the belt stays as clean as possible, minimizing spillage and, ultimately, increasing plant efficiency.
At the primary screening stage, a 6m x 1.8m (20ft x 6ft) ProGrade R211 double-deck rinsing screen, fitted with polyurethane screen mats, is employed. Any oversize (+40mm) material is discharged into a concrete bay beneath the screen, while the –5mm material and waste water are sent to an EvoWash sand plant.
Meanwhile, the –40mm +5mm material is delivered directly to the new CDE AggMax system. This unit combines a RotoMax attrition system and ProGrade dewatering screen in a compact configuration that reduces the amount of space required to accommodate the plant. The RotoMax system has been introduced specifically to tackle the level of clay in the feed material, and the unit installed at Brooksby – an RX100 – is one of three models available from CDE, the largest of which is capable of handling up to 300 tonnes/h. The RotoMax uses high-specification components, such as 118 chrome molybdenum blades, and has been designed to ensure maximum attrition of any clay-bound materials.
The waste water from the RotoMax is sent to the EvoWash sand plant to recover any of the –5mm material that managed to pass the first screening stage. Meanwhile, the scrubbed –40mm +5mm material is delivered from the RotoMax on to a ProGrade C-series dewatering screen before being sent to the dry sizing screen via a 20m static transfer conveyor.
The dry sizing screen at Brooksby comprises a ProGrade D26 double-deck screen measuring 4m x 1.5m (13ft x 5ft). Equipped with polyurethane screen decks, this unit classifies the dewatered material into three final aggregate products (+20mm, –20mm +10mm and –10mm +5mm), which are transferred to their respective stockpiles by three 20m static conveyors.
At the sand washing stage, an A-series EvoWash sand plant is employed to produce both coarse and fine sands. The specification of each of these products is covered by the performance guarantees mentioned earlier, as is the moisture content of both final sand products.
The EvoWash sand plant features a 4m x 1.8m (13ft x 6ft) polyurethane screen deck, which is split to allow for dual sand production. The –5mm sand product/waste water slurry from the ProGrade rinsing screen and the RotoMax attrition system is delivered to the sand plant’s sump where it is pumped through the first of two 500mm cyclones. The material is then discharged on to one side of the split screen where the aperture is set to allow the fine material to return to the sump, together with the waste water, while the coarse sand product is dewatered on the screen. Powered by two 9kW high-frequency vibrating motors, this unit ensures maximum dewatering of the sand to provide a ready-for-market product straight from the subsequent stockpile belt.
Meanwhile, the fine sand material is pumped through the second of the 500mm cyclones. Here, the –63 micron material and waste water is removed via the cyclone overflow and sent to a ground sump in close proximity to the sand plant, before being pumped to on-site lagoons. The fine sand product is delivered to the other side of the split dewatering screen where it is dewatered to approximately 12% moisture content, once again ensuring it is ready for market straight from the stockpile belt.
High-quality products
The new CDE washing plant at Brooksby Quarry has succeeded in addressing the specific issues identified by Lafarge as being critical to the plant’s success. The system successfully deals with the clay content in the feed material to produce the high-quality sand and aggregate products demanded by the company, while the superior dewatering of the sand product, in particular, is allowing Lafarge to quickly turn their products into revenue.
According to CDE, the new plant at Brooksby provides evidence of the success that can be achieved on projects such as this when a partnership approach is adopted by both the customer and equipment supplier. They say a high level of consultation in the plant design process helps ensure that the objectives of the plant are clear to all involved, thereby maximizing the likelihood of an efficient, effective and high-quality installation.
For further information, contact CDE on tel: (028) 8676 7900; email: info@cdeglobal.com; or visit: www.cdeglobal.com
Acknowledgement
The editor wishes to thank Lafarge Aggregates for permission to visit the site.