Colchester Quarry Replant Completed
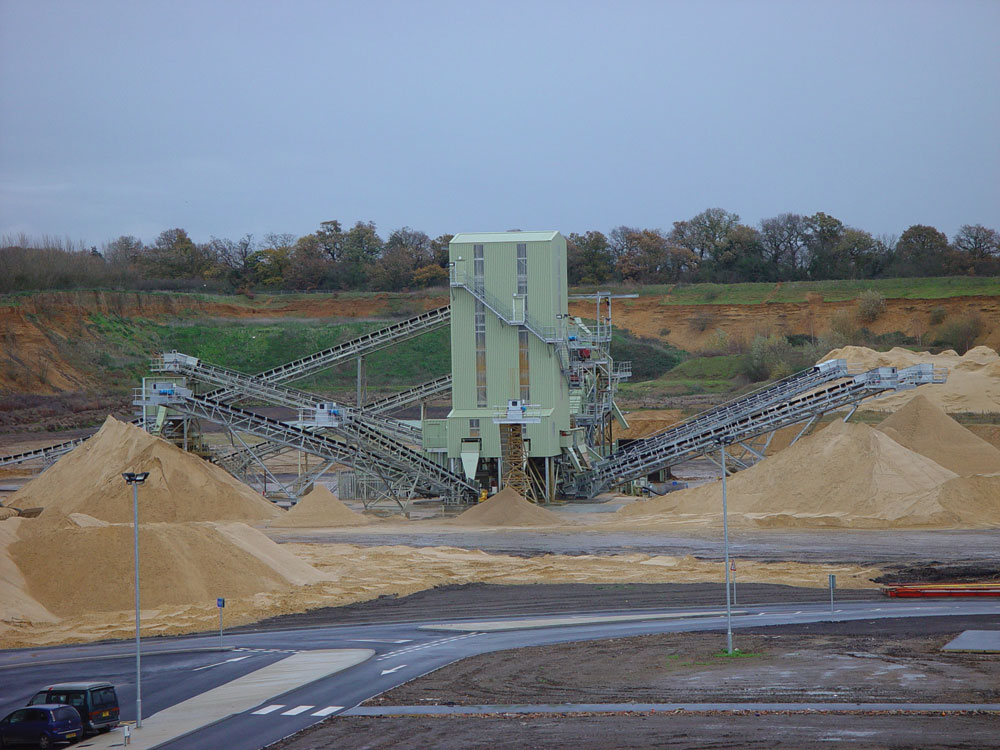
Tarmac invest in state-of-the-art processing technology at key East Anglian sand and gravel operation
Located on the outskirts of the Essex county town from which it takes its name, Colchester Quarry is Tarmac’s largest and most important unit in the East Anglian region, with sand and gravel, ready-mixed concrete, asphalt, recycling, dry silo mortar (DSM) and landfill operations, together with a regional administration office, all occupying various parts of the site.
The site has been in existence for around 35 years, although it originally comprised two discrete and separately owned quarries (Bellhouse and Stanway) located on either side of Warren Lane. Later, having both been acquired by Tarmac, the two sites were combined and their operations linked by field conveyor via a tunnel under the road.
Until recently extraction operations were centered on the former Stanway site, with material being conveyed to Bellhouse for processing and distribution. However, with diminishing useable material at Stanway and significant reserves still remaining beneath the 20-year-old Bellhouse processing plant, some two and a half years ago Tarmac took the decision to, in effect, reverse the operation.
In order to release the sterilized deposit at Bellhouse, the company opted to construct a brand new state-of-the-art sand and gravel plant on previously worked land at Stanway, shut down and dismantle the Bellhouse processing facility and then reverse the existing field conveyor to supply the new plant, thereby adding to (and eventually supplanting) the current supply of raw feed from the Stanway site. All of these changes were permissible under the site’s existing planning consent.
Based on previous successful projects, the two main contracts for the new processing plant were awarded to LJH Group Ltd, the manufacturing division of DUO (Europe) plc, and sand plant specialists Linatex. The brief from Tarmac was to deliver a plant capable of producing two sizes of gravel (20mm and 10mm) and two grades of sand to precise specifications, the latter comprising around 85% of the plant’s total output.
Maximum utilization of existing reserves and, in particular, the efficient production of high-quality sharp sand, were key drivers for the new plant, however the subsequent development of a DSM plant at the Stanway site – part of Tarmac’s ongoing expansion of their dry silo mortar business in locations close to existing sand reserves – provided added impetus and a welcome bonus.
The deposit at Colchester Quarry comprises an 18m thick sequence of glacial sands and gravels, which sit on top of the London Clay. Five distinct layers are present within the sequence: upper gravel, upper pales, middle gravel, lower pales and lower gravel. Notwithstanding the gravel layers, sand-grade materials predominate throughout the sequence, while pugs of clay of varying size occur to a greater or lesser extent in all five layers, with some more significant lenses occurring within the upper gravel. As far as possible, these unwanted clay deposits are removed prior to processing by means of clay pickers mounted on the field conveyor.
Although the new plant is fully capable of handling ‘as-raised’ material, careful selection and blending of the various sand and gravel layers is carried out at the face to ensure that the plant receives a balanced feed, which in turn helps maximize the production of the primary sand products.
Washing plant
From the face, a series of three new ground conveyors, supplied by Continental Conveyor & Equipment Co., deliver the feed material to the new 360 tonnes/h washing plant, which was designed, supplied, installed and commissioned by LJH Group Ltd. On arrival in the vicinity of the processing plant, the final ground conveyor discharges on to a 58m long x 900m wide inclined conveyor. Rated at 400 tonnes/h and equipped with an Eriez permanent magnet and metal detector, this deposits the –150mm sand and gravel feed stock on to a 4,000-tonne live-capacity surge pile.
Material recovery from the surge pile is via three 2.5m long x 800mm wide belt feeders, each rated at 360 tonnes/h, mounted in a 34m long square-section precast concrete tunnel. All three feeders are capable of working individually or in combination, although only one is used during normal processing operations. For maintenance purposes, hydraulically adjustable slide gates/protection plates provide the capability to safely isolate each feeder from the overlying surge pile.
From the surge pile an inclined section of the 90m long x 900mm wide recovery conveyor discharges the sand and gravel, via a boiling box, on to a 6.0m long x 2.2m wide Metso Ellivar 13 twin-deck rinsing screen with fitted 65mm apertures on the top deck and 5mm apertures on the bottom deck. This first screen scalps off all +65mm material and any remaining lumps of clay, which are discharged by chute to a ground bunker, while the –5mm underflow is sent by flume to the Linatex sand plant. The remaining –65mm +5mm fraction is discharged directly into an Eagle Iron Works coarse-material washer supplied by Syscom BV in the Netherlands.
The scrubbing action of this 18ft long twin-screw unit featuring 36in diameter paddles liberates any remaining clay particles and fines that may be clinging the coarser aggregate material. These are discharged with the overflowing waste water into the sand plant flume, while the clean aggregate is discharged directly on to a second 6.0m long x 2.2m wide Ellivar 13 rinsing screen; this time a triple-deck unit fitted with 20mm apertures on the top deck, 10mm on the middle deck and 5mm on the bottom deck. This unit removes any remaining –5mm material, which is flumed to the sand plant, while the –10mm +5mm and –20mm +10mm final product fractions are delivered to 2,000-tonne ground stockpiles via two 30m long x 600mm wide stockpile conveyors, each rated at 150 tonnes/h.
Alternatively, when necessary, either or both of these final products, along with the –65mm +20mm oversize, can be crushed to produce additional manufactured sand, a beneficial process that was previously not possible with the old processing plant. A 37m long x 600mm wide inclined conveyor equipped with a permanent magnet delivers the materials from the screen to a 40-tonne live capacity surge bin equipped with a crusher by-pass chute. A vibrating tray feeder discharges the material into the inverter-driven 150 tonnes/h Ore Sizer vertical-shaft impactor, while the crushed material is returned to the second screen in a closed-circuit arrangement via a 39m long x 600mm wide conveyor equipped with a belt weigher. By adjusting the feed rate to the crusher and/or the crusher speed, the material flow from the washing plant to the sand plant can be fine-tuned to help maximize downstream sharp sand and DSM sand production.
Sand processing
In the early 1980s Linatex introduced their ‘sand on recipe’ concept, whereby raw sand would be separated into distinct fractions and stored in silos. Subsequent mixing of these fractions in the correct proportions could then be carried out to produce any required particle size distribution in the final product. Since then further improvements in computer control and automation have led to the development of the Linatex dual in-line blending system (DIBS), which allows two or three separated fractions to be accurately reblended by computer in one continuous process, with the computer storing the settings for any desired final product.
Designed, built, supplied, installed and commissioned by Linatex, the new computer controlled sand-classification and dewatering system at Colchester Quarry is capable of handling up to 600,000 tonnes per annum (327 tonnes/h) of –5mm feed material to produce two main specification-controlled products: a close-specification concrete sand, designated ‘T5’, for use in airport aprons and runways; and a dry silo mortar sand for use by the new on-site DSM plant. The sand plant is also capable of producing other quality controlled BS sands for the concrete, mortar and asphalt markets.
The –5mm sand fraction from the washing plant (which can represent as much as 92% of the as-raised raw feed) is presented to the Linatex system, together with 454m3/h (2,000 gal/min) of process water, via a flume arrangement. The feed slurry is discharged directly into a 4.6m diameter feed-regulating sump, which ensures correct mixing and distribution of the feed solids within the process water stream and delivers a consistent feed to the downstream classification processes. A 250/200 Linapump centrifugal slurry pump draws the feed slurry from the sump and delivers it to a 760mm (1030) hydrocyclone, which acts as a pre-wash to remove the majority of unwanted –75mm silts and clays early in the process, thereby reducing downstream loading.
The underflow from the hydrocyclone is directed to a 3.0m x 7.0m HG30/70 single-deck sizing screen which, owing to the requirement for 100% passing 1mm for the DSM mortar sand product, performs a single cut at 1mm to produce a –5mm +1mm grit sand as the first separated fraction. This is collected by a 2.4m diameter sump and delivered by a 100/100 Linapump to a 610mm (HK125) separator for dewatering and presentation to the grit sand-blending tank.
Meanwhile, the –1mm underflow from the sizing screen passes to a second 4.6m diameter feed-regulating sump and 250/200 pump for delivery, via two 760mm (830) hydrocyclones, to two 3.0m diameter T-type classifiers (hydrosizers) where the second classification is carried out. Utilizing the phenomenon of ‘hindered settling’, the T-type classifiers are configured to perform a ‘cut’ at 250mm.
The coarse fraction (–1mm +250mm) underflow is directed to a blending tank as the second discrete fraction for blending purposes, while the –250mm fine fraction overflow from the T-type classifier is fed, via a 4.5m diameter sump and 250/200 Linapump, to two 762mm (HK150) separators where it is dewatered and presented to two fine-fraction blending tanks.
As settling ponds are employed to handle the effluent discharge, the entire system has been configured to maximize process water recirculation. Effluent discharges from the processing equipment are directed to a collecting tank from which two 250/200 Linapump units, arranged in series and with a combined power rating of 235kW, draw and pump 800m3/h (3,500 gal/min) of process water over 1.2km through 327mm bore pipework to the site’s settling lagoons. For level control purposes, the first pump in line is inverter controlled and linked to ultrasonic level probes in the collecting tank.
Dual in-line blending system (DIBS)
The grit, coarse sand and fine sand fractions held in the fluidized blending tanks provide buffer capacity and allow the sands to be mixed together in a continuous blending process. All the tanks are monitored using density pressure transmitters for fraction availability and are fitted with electro-pneumatic discharge valves connected to a state-of-the-art computer control system featuring a PC visualization package. This allows simultaneous production of the primary and secondary sand products to accurate specifications and ensures maximum utilization of the feed stock. Changing product specifications, once they have been set up in the computer, is a simple automated process.
The –5mm +1mm grit fraction primarily discharges to a VD18 dewatering screen for delivery, via a radial conveyor, to a 4,700-tonne capacity ‘T5’ concrete sand stockpile. The coarse and fine fractions are blended in the correct proportions by PLC controlled valves, while any unused grit fraction is directed to a VD9 dewatering screen for discharge by static conveyor to a small residue grit sand stockpile. This material can be reintroduced into the feed when there is a deficiency of this fraction in the natural deposit.
The plant’s secondary product, DSM sand, is blended according to required proportions and discharged to another 4,700-tonne stockpile via a VD15 dewatering screen and radial conveyor. Any unused fine or coarse fraction is discharged on to a VD12 dewatering screen for stockpiling by static conveyor as a residue.
Following minor post-installation adjustments by Linatex, the plant is now successfully producing the required specification products irrespective of the variable nature of the feed material.
Nevertheless, Tarmac’s carefully structured approach to the working of the deposit and the blending of the feed material within a target grading envelope is helping to maximize the quantities of the final products produced, while at the same time minimizing the rejection of material to the two residue stockpiles.
Acknowledgement
The editor wishes to thank Tarmac Southern Ltd for permission to visit the site and in particular, Mark Gibbons, quarry manager, and Craig Dewsnap, engineering manager with Linatex, for their help in preparing this article.