CEMEX's Recently Opened Wharf at Dagenham
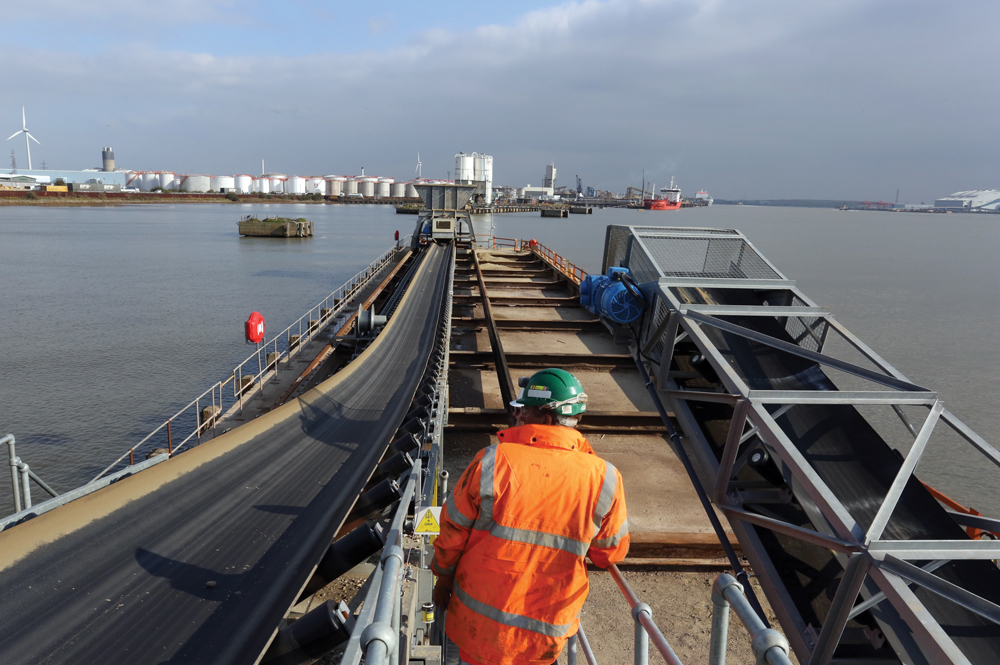
First published in the May 2016 issue of Quarry Management as Ship to Shore
Designed and built by DUO plc, CEMEX’s recently opened wharf at Dagenham is now the closest aggregate production plant to central London on the north side of the Thames
Officially opened at Dagenham late last year, CEMEX’s newest aggregate processing plant is said to be the closest aggregate production site to central London on the north side of the river Thames. Designed and installed by DUO plc, it can produce in excess of 500,000 tonnes of aggregate per annum, most of which will go into concrete for use in construction projects in the capital.
Previously the site of an asphalt plant that was decommissioned in 2009, the Dagenham facility was then used as a depot for limestone brought in from quarries in North Wales for use in the London market. The whole site took six months to convert into a fully operational wharf, with DUO Manufacturing providing a complete upgrade of the ship-to-shore system.
Ship to shore
Today, marine-dredged aggregate is delivered to Dagenham by a 10,500-tonne capacity chartered vessel with the ability to discharge its cargo up to 2,000 tonnes/h. The project brief called for the supply of a ship discharge system with associated conveyors to feed the marine-dredged aggregate to the processing plant stockpile.
DUO Manufacturing designed and manufactured a 2,000 tonnes/h discharge system incorporating a powered traversing feed hopper mounted on existing rails. The system feeds the sea-dredged material on to a short jetty-mounted conveyor for transfer to a 207m long ship-to-shore conveyor which, in turn, feeds a radial stockpiling conveyor located adjacent to the processing plant.
A 400 tonnes/h barge-loading system comprising a feed hopper with associated conveyor to the jetty plus a radial barge-loading conveyor was also supplied by DUO Manufacturing, together with belt weighers for both conveyor systems.
DUO Manufacturing director Dudley Lloyd commented: ‘Installation of the ship-to-shore and the barge-loading conveyors was not a straightforward job, as we were required to design and manufacture the conveyor gantry sections so that they landed exactly on the existing concrete pontoons, all of which was completed satisfactorily.’
As well as the design, manufacture and installation of the new equipment, DUO Manufacturing were also tasked with the removal of all the existing ship-to-shore equipment.
Washing plant
With a brief to provide three end products (concrete sand, 10mm and 20mm), with any +20mm to be crushed in a closed-circuit arrangement, DUO plc designed a 250 tonnes/h washing plant incorporating a Terex AggreSand 165 processing system featuring a rinsing screen, sand plant, stockpilers and all associated pipework and electrics on one modular chassis. DUO also supplied a water and silt-management system and the recirculatory system which feeds the oversize to the crusher to produce –20mm.
DUO director Fintan McKeever commented: ‘The Terex AggreSand system combines aggregate washing and screening with sand processing on a modular chassis, which was the ideal solution for the Dagenham operation. It brings together tried and trusted Terex Washing Systems components in an innovative modular design, setting itself apart from other washing systems in the marketplace.’
Stockpiled material is fed into a 9m3 feed hopper which features a remote-control tipping grid. From here material is fed on to an inclined conveyor which delivers the it to the first processing stage of the Terex AggreSand 165 – a 4.8m x 1.5m triple-deck rinsing screen.
Utilizing individually controlled spray bars on each deck, the two-bearing screen is fitted with polyurethane modular media on all three decks. The upper protection deck removes any +20mm material which is delivered to the crusher feed conveyor.
The middle deck is a 10–20mm passing deck while the bottom deck produces 0–10mm and the required sand. Integral to the chassis are two conveyors which deliver the 10mm and 10–20mm gravels to their respective stockpiles.
Oversize material from the primary rinsing screen is fed up an inclined crusher feed conveyor and delivered into a surge bin and feeder ahead of a TC1000 cone crusher. After reduction, this material is fed back to the rinsing screen for reprocessing.
The sand fraction from the AggreSand 165 is delivered to a 200 tonnes/h sand plant for processing. Comprising one 250/200 Linatex centrifugal pump, two G4-660mm cyclones, and a 4.3m x 1.8m dewatering screen, this produces a clean in-specification concrete sand which is delivered to a radial stockpile conveyor.
The entire plant is controlled via a state-of-the-art control panel featuring a full-colour graphic HMI (Human Machine Interface), automated sequential starting/stopping of all plant items, and automated sequential shutdown upon fault detection. All key parameters are displayed on screen, including cyclone feed pressure, hydraulic oil level and temperature, and all motor load currents and voltages. The operator has full radio control of plant start/stop functions, the sand conveyor radial drive, tipping grid raising/lowering, and plant lighting (on or off).
Water and silt management
The water-treatment plant at Dagenham clarifies and recycles the dirty process water from the washing plant and concentrates the resulting sludge, which is achieved through the addition of a prepared polymer flocculent solution. A flocculent controller takes regular samples and measures the settling speed, transferring this information to the PLC which automatically adjusts the dosing pump flow to optimize flocculation efficiency and flocculent consumption. Optic cells are also utilized to determine the turbidity of the recycled water and thereby adjust the coagulant dosing accordingly.
The concentrated sludge that settles at the bottom of the thickener tank is drawn off by pump, with the sludge pumping cycles controlled according to the resistance on the tank scraper mechanism. This provides reliable information about the quantity and consistency of the sludge at the bottom of the thickener. If an overload is detected, the scraper is automatically lifted to its uppermost position and then progressively lowered to help dilute the sludge.
The clean overflow waters are discharged into a water storage tank from where a water pump recycles it back to the washing plant.
The entire water- and silt-management treatment plant is controlled via a PLC with touchscreen to display the synoptic and to give access to the settings. The main switch and control panel are located inside a technical cabin which is sited on a static bridge. This room also contains the flocculent preparation and dosing unit, the flocculation controller and the main switch and control panel, as well as the scraper drive unit and fresh-water box.
CEMEX unit manager David Whitby commented: ‘Having used many different water-treatment systems in my 30 years of wharf production, I have been impressed with the ease of use and the elimination of any waste from production.’
CEMEX, aggregates operations director Rob Doody added: ‘Following the slowdown in construction, the recovery has resulted in severe materials shortages, particularly around the London area. We have similar wharf operations at Northfleet and Angerstein, close to Dartford, but they are both south of the river. It made strategic sense, therefore, to revitalize the site at Dagenham, to service the growing markets in central and north London.’