By-product to Commercial Output
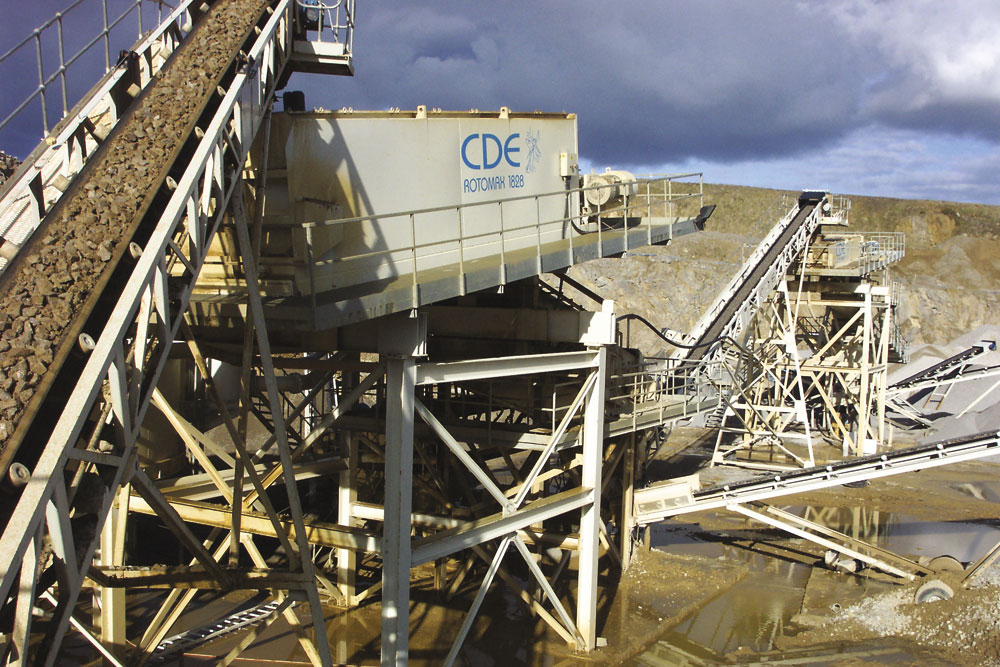
Lagan Group increase production with CDE washing plant
More than 200,000 tonnes of material have passed through the CDE washing plant at Irish Asphalt’s Duleek Quarry, in Co. Meath, since its installation in the summer of 2003. In July 2004 the plant’s ownership will transfer to Irish Asphalt, part of the Lagan Holdings Group, having been operated on a price-per-tonne basis by CDE since its installation. The Euro 1.5 million contract represented a major investment for Northern Ireland company CDE, and while their processing systems have previously been chosen for applications ranging from specialist sand classification to quarry-dust washing, the raw material at Duleek provided them with a considerable challenge.
The Lagan Group are one of Ireland’s largest quarry operators with sites both north and south of the border and a combined production capacity of over 2 million tonnes. They are also a major supplier of asphaltic material, and their bitumen division is at the leading edge of binder and emulsion technology. Lough Neagh in Northern Ireland, the largest freshwater lake in the British Isles, is the base for the Group's sand division, while Lagan’s concrete division operates one of the most modern concrete block and brick-making plants in Europe.
The Duleek site is situated on what is essentially a Carboniferous limestone deposit but bands of heavy and extremely plastic clay are prevalent. Large stockpiles of overburden and clay-bound material had been building up as waste by-products for some time and were seriously compromising the efficiency of the operation. Identifying and responding to this, Lagan’s regional quarry manager, Paul Tuite, initiated discussions with CDE in early 2003. Mr Tuite commented: ‘We demand the highest-quality aggregates for both in-house use and external sales, and it was clear that our existing process could not achieve this. Our partnership with CDE has been rewarded with consistent quality aggregates and production capacity has increased by more than 30% on initial figures.’
Other prominent CDE washing plants and contracts have been established throughout Ireland, the UK and Sweden, and the experience gained from these, together with CDE’s growing reputation for innovation, led to the Lagan Group contract.
The plant born of these negotiations has already attracted numerous visitors from the UK and further afield. What draws them is the consistently high quality of the sand and aggregates produced by the plant, in spite of the poor-quality raw material. Up to 25% of the –90mm raw feed, and often up to 50% of the –5mm fraction, can be less than 75µm. Since final commissioning the plant has consistently supplied clean and dry outputs comprising 20mm, 14mm, 10mm, 6mm and concrete sand, allowing Lagan to offer customers commercial Type 1 and concrete constituents, all from a material previously regarded as waste.
Processing plant
A shovel-loaded 50-tonne capacity feed hopper and belt-feeder arrangement discharges the raw feed material on to a 20m long inclined conveyor. This feeds a 1.5m x 4.0m CDE 2SG60 grizzly screen that removes any +90mm oversize, which falls into a walled bay. Previously tested grizzly bars had a tendency to block owing to the highly plastic nature of the material, especially in wet weather. This led to a new design of high-tensile offset finger-bars, which are now a standard CDE specification. These offer maximum flexibility and ensure that capacity is not compromised, even with variations in the raw material. The –90mm material is conveyed by a second 20m conveyor to a CDE Rotomax 1828 twin-shaft log-washer. This 8m long machine is believed to be one of the largest log-washers currently operating in Europe, with each shaft measuring 1.8m in diameter from tip to tip. The unit can accept up to 250 tonnes/h of –90mm material, and retention time can be easily adjusted by altering the inclination and running speed, aided by the single motor and gearbox design. CDE say that unlike many log-washers, the special Rotomax design allows feed containing up to 30% –5mm material to be efficiently handled without the need for preliminary fines screening. Each shaft is fitted with heavy-duty chrome-molybdenum tips for maximum wear resilience.
Scrubbed material is fed directly to an R2M108 twin-deck primary rinsing screen. This 1.8m x 6.0m unit was one of the first of CDE’s latest-generation rinsing screens, incorporating rubber and polyurethane decks. The top deck is fully enclosed by a splash-proof cover, ensuring maximum water retention and a clean operative environment. Five spray-bars per deck (with individual controls) and flexible rubber screen seals for each bar are included. The top deck separates +24mm material, which is conveyed to a mobile impact crusher for reduction to commercial Clause 804 specification. The underflow from the lower deck, comprising a –4mm water, sand and clay slurry, is flumed to the sump of a CDE C-62 compact sand plant.
Another 20m conveyor carries the rinsing screen’s –24mm +4mm intermediate product to a second log-washer, a 7m long Rotomax 827 that removes any residual clay particles from the aggregate; the success of this is evident from the clean nature of the finished products. As with the primary log-washer, the speed and inclination of this unit are easily adjusted to accommodate variable feed materials and tonnages. Material from the log-washer is delivered directly to a dewatering screen mounted over the final dry-classification screen. The Dw43 dewatering screen is equipped with spray-bars in the first screen section to give the material a final light rinse. This unit includes modular polyurethane panels and side protection as standard. Filtrates from both the dewatering screen and the log-washer overflow to a ground sump for recovery. The recovered water/fines slurry is returned, by means of a Warman QV65SP submersible pump, to the primary rinsing screen. This offers increased fluidization of the feed material, retains water within the system and is a valuable aid to site cleanliness and plant wash-down. Aggregates are classified into four final products by a D2M60 1.5m x 4.0m twin-deck dry screen with a split bottom deck. The efficiency of the CDE dewatering screen is highlighted by the unusually dry aggregates produced; moisture content is consistently less than 5%.
Sand production
Sand slurry leaving the primary rinsing screen is piped to the C-62 compact sand plant, which is rated at 120 tonnes/h. The compact sand plant is CDE’s best-known single product and has no trouble handling the high clay volumes in the feed (the –4mm can contain up to 50% clay). The plant consists of a hydrocyclone mounted over a dewatering screen and sump. Slurry is fed directly into the sump and is then sent to the custom-sized hydrocyclone by a Warman 10/8E-M pump. The silt cut-point can be set to suit customers’ specific product requirements, but here the sand consistently contains less than 3% –75µm material, with typically 50% passing 600µm. Sand and residual water exit from the base of the hydrocyclone and pass to a dewatering screen mounted underneath before the sand is discharged, via a rubber-lined chute, to the sand conveyor at a typical 12% moisture content. The waste water containing clays passes directly to an 8m diameter CDE T-08 high-rate thickener, complete with a fully automatic polyelectrolyte dosing station, for further treatment.
Waste-water treatment is perhaps one of the most crucial elements of the entire plant. Given the dirty nature of the feed, many traditional treatment systems would demand large volumes of water, which is not always practical in quarry applications. Here, the complete plant operates at up to 220 tonnes/h, which equates to 44 tonnes/h of waste solids. Polyelectrolyte dosing is carefully monitored to ensure correct sludge settlement/compaction without any risk of flocculant carry-over in the recycled water. A freshwater storage tank is located adjacent to the thickener and the primary rinsing screen, so only a relatively low-power recycled-water pump is required. The sludge is sent to a remote lagoon for further settlement, this being approximately 200m away with a 35m head. The material is sent to the lagoon by a Warman 4/3C-AH pump. Final solids content in the sludge is typically around 40–50%. CDE say an interesting point to note is the relatively compact size of the T-08 thickener unit. Alternative treatment systems would, they say, generally require a much larger unit than the 8m diameter model specified here, but this particular unit has proven to be well able to cope with the 450m3/h of water within the cycle, and overall only 50m3/h of top-up water is required.
CDE and the Lagan Group are currently in discussions aimed at moving the plant to a more permanent on-site location. This move is expected to see the addition of the latest-model CDE plate-and-frame filter press. This technology will achieve maximum water recycling with top-up requirements reduced to a mere 20m3/h. The waste material will be offered as easily handled dry cakes, completely eliminating the need for settlement lagoons. Current investigations are exploring the possibility of using this dried clay in Lagan’s newly commissioned cement plant.
Anticipating the plant’s handover from CDE in July 2004, Terry Lagan, director of Irish Asphalt, commented: ‘This CDE installation represents a new generation of washing plants for problem materials…we are now able to fully exploit this quarry, handling materials that were previously stockpiled as waste — but, crucially, making commercial-grade products from them.’
Acknowledgement
The editor would like to thank both the Lagan Group and Iain Walker of CDE for their co-operation in producing this article.