Blackwater Aggregates Take-off At Bradwell Quarry
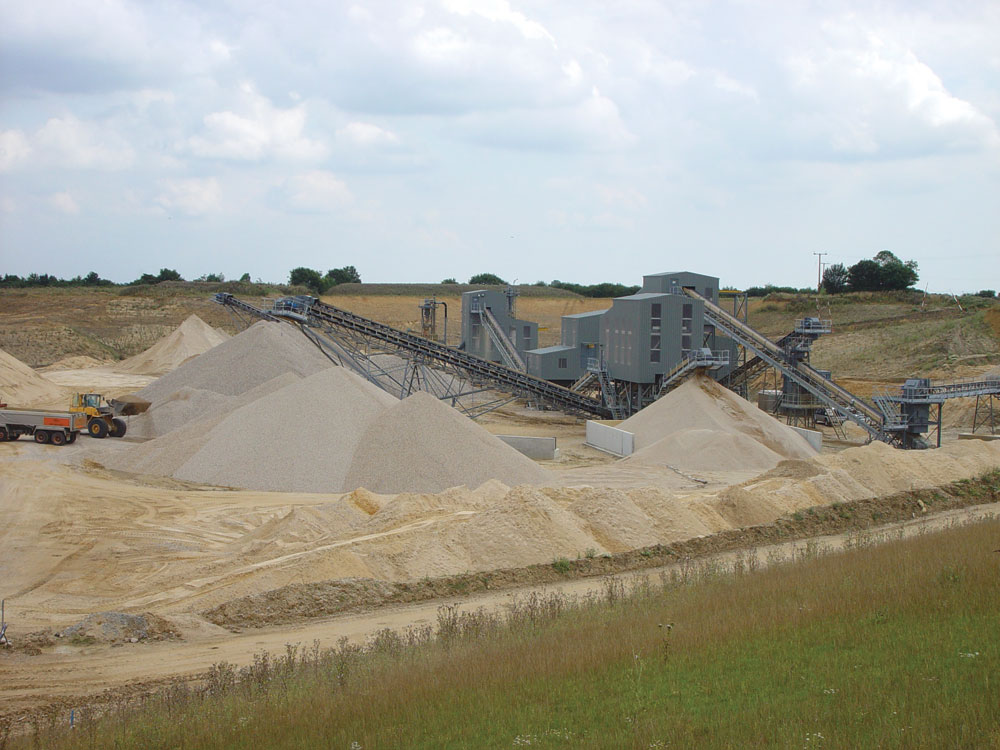
RMC Aggregates’ major sand and gravel joint-venture quarry comes on stream
Earlier this summer a new £5 million sand and gravel and ready-mixed concrete operation came on stream at a disused World War II airfield near Braintree, in Essex. Known as Bradwell Quarry, the development is being operated under the banner of Blackwater Aggregates, an equal partnership between RMC Aggregates (UK) Ltd and the site’s landowners, Gent Fairhead Aggregates Ltd.
The quarry has been developed on land that, until a year-and-a-half ago, was worked by Hanson Aggregates. The site is also very close to RMC’s former Coggeshall Quarry, which finally closed down at the end of July 2002 after 13 years of operation.
In 1998, more than five years after planning approval was first applied for, consent was finally granted for Blackwater Aggregates to extract sand and gravel from the northern part of the former Rivenhall United States Air Force base. Development of the site required the widening of the nearby A120 road between Braintree and Coggeshall and the construction of two new bridges across the river Blackwater, as well as a new 1.6km access road, built by RMC Surfacing.
Lying directly on top of Tertiary London clay, the deposit itself comprises a 6–8m thick sequence of glacial sand and gravel which in turn is covered by 8–12m of glacial boulder clay. This necessitates a carefully co-ordinated approach to overburden removal and mineral extraction to ensure the correct balance of operations is maintained. The 7in thick concrete runways and taxiways which form part of the old airfield are an additional factor in this equation, as these too have to be broken up and removed progressively as mineral extraction advances.
Until recently specialist earthmoving contractors CJ Pryor (Contracts) Ltd were tasked with carrying out all overburden removal and mineral extraction operations, both of which were achieved with great efficiency and attention to detail. However, last month, Blackwater Aggregates acquired two brand new Volvo A35 articulated dumptrucks and a 45-tonne Volvo excavator in order to bring all mineral extraction and around 20% of the overburden work ‘in house’, leaving CJ Pryor responsible for the remainder.
Before any mineral extraction could commence, however, some 750,000m3 of overburden had to be stripped and moved, much of it being used to create the carefully contoured screening bunds which mark the perimeter of the site and encircle the new processing plant.
In line with planning conditions, the aggregates plant itself is a ‘low-level’ facility, designed and built by Coalville-based Whitwick Engineering, with civils carried out by RMB Contractors of Ambergate. The plant operates at a nominal 400 tonnes/h and works in conjunction with a Linatex sand plant to produce five main products — 20mm, 10mm, 6mm, sharp sand and soft sand — as well as a range of blended products and oversize materials on demand. The site is also home to an existing ready-mixed concrete plant, which is run as a joint operation between RMC Readymix East Anglia and Hanson.
Processing operations
A 50-tonne capacity dump hopper and belt feeder installed a short distance from the extraction area is used to feed the as-dug deposit on to a field conveyor for delivery to the processing plant. The 1,200mm wide field conveyor, obtained second-hand from RMC’s Rugby Cement works in Rochester and refurbished at Bradwell, currently extends some 650m in length but will be increased by a further 200m as extraction operations progress.
Delivering material at a rate of 650 tonnes/h, the field conveyor discharges on to an inclined primary stockpile conveyor equipped with a Rowecon belt weigher and a Tuke & Bell clay-picker. Sand and gravel is recovered from the primary stockpile, which has a live capacity of around 950 tonnes, via a cast concrete reclaim tunnel (with an Armco emergency tunnel) equipped with two Rowecon variable-speed belt feeders with cut-off doors, each feeder rated at 400 tonnes/h. The recovery conveyor discharges on to a 45m long x 900mm wide plant conveyor, equipped with a second Rowecon belt weigher, which delivers the as-dug material to the first stage of the fully enclosed processing plant.
Material is discharged from the plant conveyor on to a Finedoor 6.0m x 2.4m double-deck washing screen which is configured to allow –40mm material to pass the top deck and –5mm fines to pass the lower deck. The –5mm slurry is ducted to a low-height feed-regulating sump which supplies Bradwell’s Linatex sand plant, while any +40mm material rejected by the top deck is fed, via a 24-tonne capacity surge bin and Skako vibratory feeder, both mounted beneath the screen, to a BL Pegson 105 primary jaw crusher with a 38mm closed-side setting. The crushed product is then recirculated back to the screen in a closed-circuit arrangement. Alternatively, the +40mm oversize can be discharged by chute to a 200-tonne ‘rejects’ stockpile.
Around 250 tonnes/h of –40mm +5mm material from the first screen is fed directly to a 5.0m long x 2.1m diameter rotary scrubber supplied by Rochester-based Sepro Group Ltd. To improve operational life and reduce downtime, the scrubber barrel is fitted with the type of heavy-duty mill liners normally reserved for extreme applications such as grinding circuits, while drive is supplied by pairs of individually powered wheels without the hindrance of interconnecting shafts.
The rotary scrubber liberates any remaining fines from the gravel and in turn discharges on to a Finedoor 6.1m x 1.8m double-deck washing screen which allows –20mm material to pass the top deck and –5mm fines to pass the bottom deck. Once again, the fines slurry is fed to the sand plant feed-regulating sump, while the –40mm +20mm material rejected by the top deck is conveyed to a second fully enclosed building housing a 50-tonne capacity surge bin ahead of the secondary crusher, a BL Pegson 900 Autocone with an 18mm closed-side setting. This is fed by a second Skako vibratory feeder and, again, the crushed product is recirculated back to the second screen in a closed-circuit arrangement. Alternatively, the –40mm +20mm can be diverted to an adjacent 200-tonne capacity ground stockpile if required.
The –20mm +5mm fraction from the second screen is conveyed to a third ‰ building housing another Finedoor screen, this time a ‘dry’ 7.3m x 2.1m double-deck unit which allows –10mm material to pass the top deck and –6mm to pass the lower deck. As with the two wet screens, the synthetic deck modules used on this screen are supplied by Screening Consultancy & Supplies Ltd on a ‘tonnage’ contract basis. The top- and mid-deck products from this screen (–20mm +10mm and –10mm +6mm respectively) are delivered to two 8,000-tonne capacity ground stockpiles by two 40m long x 600mm wide radial stockpiling conveyors, while the –6mm +5mm product passing the lower deck is delivered by a 600mm wide static conveyor to a 1,000-tonne capacity ground stockpile located on a concrete base slab with a 2m high concrete retaining wall around the sides and rear of the pile.
Where necessary the various plant conveyors at Bradwell are fitted with new BMS self-adjusting and self-sharpening steel scrapers supplied by Wyko for the effective removal of any carry back. The conveyors themselves are powered by a range of drive units supplied by Rossi Gearmotors Ltd, with drums and idlers supplied by Universal Conveyors.
The –5mm slurry from the two ‘wet’ screens is pumped from the 4.5m diameter feed-regulating sump adjacent to the ‘gravel’ plant to a 2.1m diameter S-Type classifier, located a short distance away at the sand plant, by means of a Linatex 250/200 pump. The overflow from the classifier is pumped to the soft-sand tower, via a 2.4m diameter feed-regulating sump, by means of a Linatex 150/125 pump, while the underflow is pumped to the sharp-sand plant by a second 250/200 pump.
The fine sand is removed from the slurry by a Linatex HK150 sand separator, with the product discharged to a 2,100-tonne stockpile at the base of the tower while the slimes are returned to the feed-regulating sump. The sharp sand is generated by a Linatex 1036 hydrocyclone and VD18 dewatering screen arrangement, with the product being delivered to a 17,000-tonne stockpile by a 40m long x 800mm wide radial stockpiling conveyor. Process water from the screen is returned to the S-Type classifier for recirculation through the sand plant, while the overflow from the hydrocyclone is either returned to the S-Type classifier or collected and pumped back to the first Finedoor screen and scrubber barrel to make up part of the plant’s 6,000 litres/min water requirement.
With a number of ready-mixed concrete customers requiring a consistent supply of materials from Bradwell, a constant supply of clean water is crucial to the whole operation. This requirement is met by a series of five parallel and interconnected silt lagoons which provide a total volume of around 44,250m3 and hold some 35 million litres of water. These were constructed by CJ Pryor and are designed to allow periodic clean-out by long-reach excavator.
Both sand stockpiles are located on concrete slabs to allow any residual water within the product to drain freely to a collection sump for subsequent return to the silt lagoons via a silt tank and effluent pump arrangement. In addition to the Linatex equipment, the effluent pump, main booster pump and various other water system requirements were supplied by Progress Pumps Ltd of Glen Parva.
All sand and gravel processing operations at Bradwell are controlled and monitored via a PC housed in a containerized control cabin overlooking the plant. The use of Mitsubishi SCADA technology, installed and integrated by Colchester-based Industrial Electrical Services, simplifies plant control and provides sequential start-up/shutdown of the entire operation. This system operates in conjunction with a number of strategically located MultiRanger Plus level sensors from Milltronics and is complemented by a series of CCTV cameras, supplied by Vision Unique Equipment, for remote visual monitoring of operationally sensitive areas.
Acknowledgement
The editor wishes to thank RMC Aggregates Eastern Counties for permission to visit the site and, in particular, Sean Connor, general manager Blackwater Aggregates, and Jeff Mercer, quarry manager, for their help in preparing this article.