Added Value for Yorkshire Aggregates
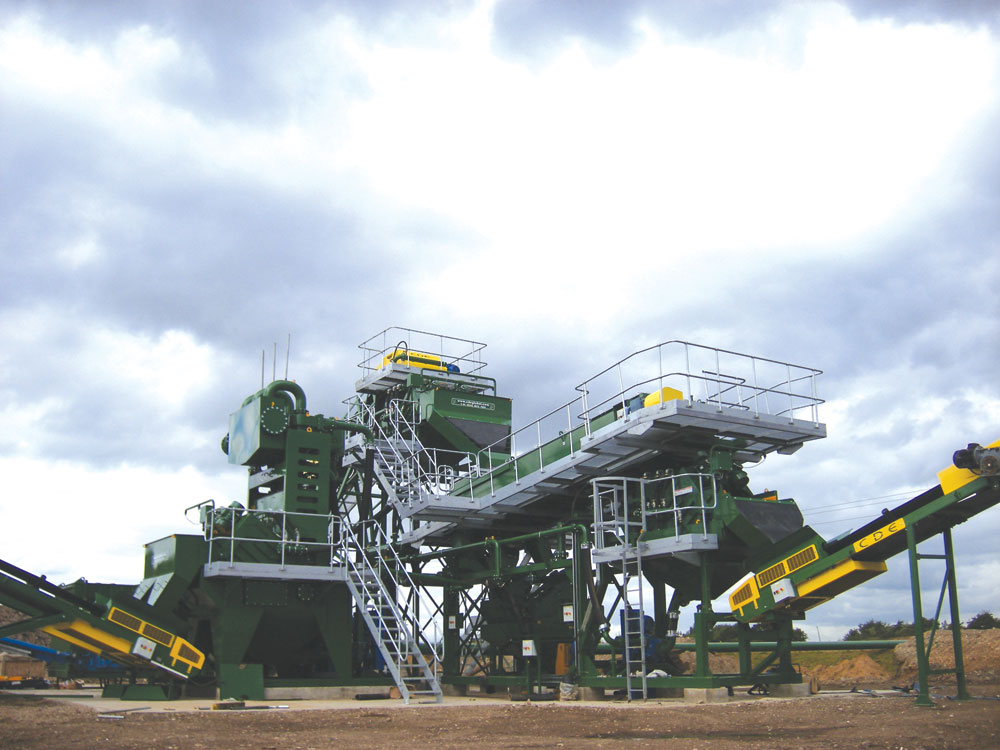
New CDE recycling plant comes on stream adjacent to Robin Hood Airport
Yorkshire Aggregates have become the latest company to install a recycling plant from Co. Tyrone-based CDE Ireland with an 80 tonnes/h plant now operational at their site in Doncaster, South Yorkshire.
Yorkshire Aggregates are one of the most prominent names in the construction products and recycling industry in the north of England with a number of branches to the business. In addition to the new recycling plant, they also operate three other businesses. Yorkshire Readymix supply a large number of customers in the local area with products from their processing plant at Wroot Road Quarry and Maltby. Yorkshire Horticultural Supplies (YHS) offer tipping services for green waste and untreated timber, which is then processed and sold as a high-quality compost product. In November 2008 Yorkshire Aggregates also opened a new tip for inert soils in an Environment Agency-approved restoration scheme. The site for this particular venture is an old RMC sand quarry in Doncaster, located at the end of the Robin Hood Airport runway.
Yorkshire Aggregates recently celebrated 21 years in business and have introduced the new plant from CDE to allow effective processing of the construction and demolition waste that they receive at their site. In addition to waste material processing, the plant will also process natural sand and gravel, with the split being approximately 50/50.
Highly variable feed
‘We needed to invest in a new plant as our previous set-up did not facilitate the effective processing of the waste material,’ explained Paul Rudkin of Yorkshire Aggregates. ‘Because the C&D waste is much dirtier than the natural sand and gravel we process, we needed a system that could handle the high level of variation in the feed, and the high level of contaminants such as wood and plastic in the C&D waste.’
Mr Rudkin first started discussing the options available with CDE in early 2008 through their sales manager for the North of England, John McGuinness. ‘Once I met with Paul and he explained the problems they were having with the C&D waste material, it was clear that the requirements of this project were very similar to those of a number of our existing recycling customers,’ said Mr McGuinness.
The problem was apparent on a visit to the site with stockpiles containing over 60,000 tons of –12mm material immediately visible. This was material that the existing plant was not able to process effectively. In addition to this, the +12mm products were not achieving target price as a result of the system’s inability to effectively clean the material.
‘Our business is moving more and more towards the recycling of construction and demolition waste material, and the inability of the current system to deal with this material meant that a new processing system was essential,’ explained Mr Rudkin. ‘CDE were able to demonstrate impressive experience in this field and we visited a number of their previous plant installations to learn more about the specific processes involved.’
As part of a contract with one of the largest building and civil engineering companies in the north of England, Yorkshire Aggregates will have large quantities of C&D waste material to process over the coming years. Once this waste material has been processed, a number of the final products will be sold back to their customer for use on a variety of construction projects.
In addition to tackling the 60,000 tons of stockpiled –12mm material, the new plant is also required to produce a number of different aggregate products as well as a coarse and fine sand products.
Customized plant
The system specified for this project was built to specifically tackle the issues raised by Mr Rudkin in his discussions with CDE. ‘One of the key things at the outset was the customization of the plant to deal with our specific issues,’ he explained. ‘We had tried the off-the-shelf option and it was just not working for us. CDE spent a lot of time analysing our material in the first instance and making adjustments to their set-up to ensure that the plant delivers the products we require, and most importantly, improves the quality of our final products.’
The Yorkshire Aggregates plant is set up to process 80 tonnes/h of variable feed ranging from natural sand and gravel to construction and demolition waste material. Over a 12-month period the plant will process equal amounts of each and Mr Rudkin is currently targeting 100,000 tons per year of each material.
‘Another key advantage of the CDE plant is the modular nature of the system,’ he said. ‘We have been in business for 21 years now and over that time our demands have changed in line with changes in the market. This new plant is able to accommodate any future changes in requirements whether they relate to capacity or final product specification. This gives us comfort that the new plant provides us with a long-term processing solution.’
Effective processing
The process begins with material being loaded into one of CDE’s integrated hopper and feed conveyor combinations. The hopper is this instance is a 35-tonne capacity B35 model. The integration of the FS17 feed conveyor within the hopper is an example of a focus on ‘transfer point technology’ throughout the CDE range, specifically designed to minimize spillage and, therefore, increase plant efficiency. The hopper receives –100mm material with any oversize being rejected for crushing and re-feeding into the system. The conveyor is fitted with an overband magnet at the feed end to remove any ferrous metal material, which is discharged into a skip positioned under the conveyor and later sold as scrap.
From here the material passes to an AggMax system, which undertakes a number of functions – primary stage dewatering, followed by high-level attrition and, finally, secondary dewatering prior to the classification of the material into the various product grades required by Yorkshire Aggregates.
At the primary dewatering stage the feed is delivered on to a ProGrade B-series dewatering screen where the –5mm material is removed and sent to an EvoWash 102 dual sand plant, while the +5mm material progresses to the second stage of the AggMax system. This involves subjecting the material to a high level of attrition within a RotoMax unit, which has been specifically introduced to tackle the high proportion of ‘trash’, including wood, plastic and polystyrene, present in the C&D waste feed.
‘Our previous processing system included a log-washer but this RotoMax system seems like substantial progress in relation to attrition technology,’ commented Mr Rudkin. ‘The performance of the unit, in terms of its ability to remove the ‘trash’ and allow effective product classification, is second to none.’
Attrition technology
The high-performance RotoMax has a number of product features specifically designed to cope with the special requirements of C&D waste processing, including an electrically powered floor discharge system to prevent the collection of waste material within the unit. This ensures that the plant remains fully operational for the maximum possible time for optimum plant efficiency.
As the treatment of C&D waste can also require the use of higher volumes of water than a typical quarrying application, the RotoMax unit is also fitted with an overflow weir. In addition, waste material is discharged to a trash screen where contaminants such as wood, plastic and polystyrene are removed. After this, the waste material is stockpiled in bays before being sent to landfill, while the waste water is delivered to the EvoWash dual sand plant to ensure all commercial grade sand material is recovered.
The RotoMax is particularly suited to this application as the unit is set up to accommodate changes in feed quality. This was of great importance for Yorkshire Aggregates because of the requirement for the plant to accept both ‘clean’ sand and gravel and ‘dirty’ C&D waste.
The final stage of treatment through the AggMax system involves the delivery of the +5mm aggregate material to a ProGrade C series dewatering screen, after which the material is conveyed to the aggregate classification phase, which utilizes a ProGrade D26 dry sizing screen to produce final product sizes of +40mm, –40mm +20mm and –20mm +5mm. The system has also been set up to allow for the production of a 5–10mm product when required.
A unique approach
At the sand washing phase, all the –5mm material is subjected to a two-stage cyclone treatment to ensure that the required product grades are achieved, a capability which, according to CDE, makes the EvoWash system unique.
‘What happens at the sand washing stage reflects the approach that CDE took to this whole project,’ said Mr Rudkin. ‘Rather than providing an off-the-shelf option and ending up with sand products that did not meet the specification we required, the plant was set up to ensure delivery of the products required by our customers. In our experience, this approach of starting at the end and working backwards delivers results that have not been possible with our material until now.’
In the first sand washing stage all of the material passes through the first of three cyclones and is delivered to the first side of a split high-frequency dewatering screen. The –5mm +3mm material is discharged and stockpiled while the –3mm material is discharged into a collection sump with the waste water. This material is pumped through two additional cyclones where the –63 micron material is removed unlike the remaining material is discharged on to the second side of the split dewatering screen. The –3mm fine sand material is subsequently discharged and stockpiled while the waste water is pumped to on-site lagoons. As part of the turnkey plant package, CDE dealt with all lagoon pipework and pumps in addition to the processing system.
Increased revenues
‘The sand washing phase of the plant really is delivering for us, not only in terms of the specification of the final sand products, but also the speed at which the material is ready for market,’ commented Mr Rudkin. ‘The sand typically has a moisture content of 12%, which means it is ready for market as soon as it leaves the belts. This allows us to turn our products into revenue much more quickly than used to be the case.’
With the previous plant that Yorkshire Aggregates operated at the site, the natural washed sand contained significantly higher moisture content and the plant was unable to process the C&D waste material into commercial grade products. The new plant takes both feed materials and produces two high-quality sand products that meet customers’ required specifications.
But perhaps the ultimate measure of the success of any plant such as this comes with an analysis of the increased revenues that can be directly attributed to the introduction of the plant. So, has the Yorkshire Aggregates plant been a success? ‘Undoubtedly!’ exclaimed Mr Rudkin. ‘Not only are we now able to effectively process material that we were previously unable to handle, but we have also seen the final value of our products increase across the board.’