A Unique Resource
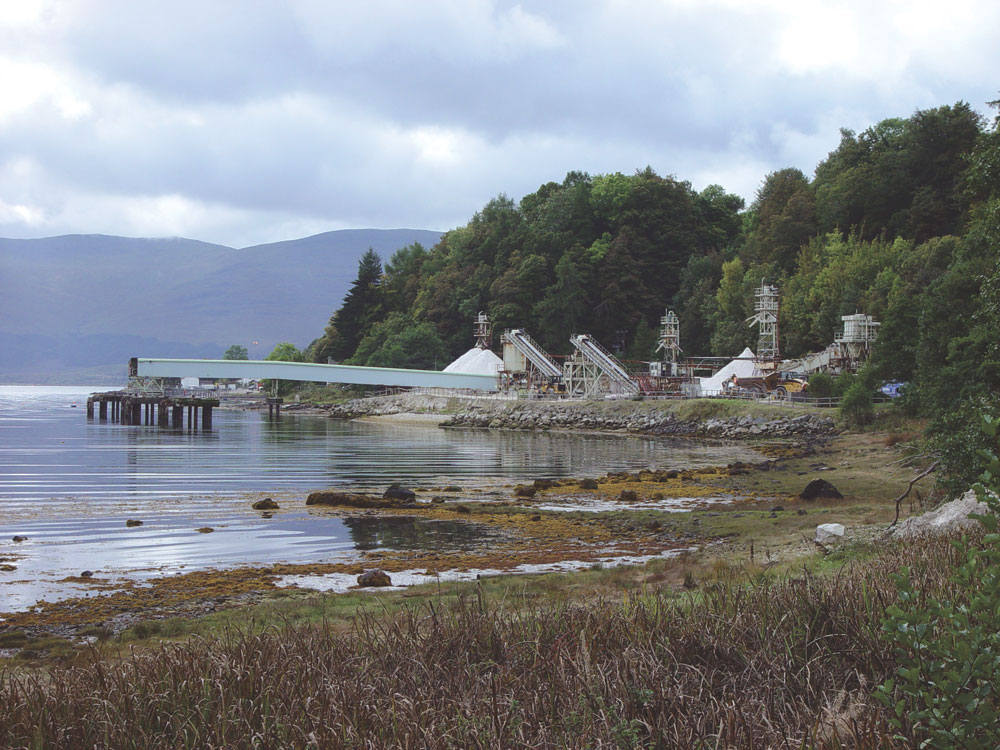
Lochaline Silica Sand Mine — Tarmac’s only underground mine
Tucked away in a quiet corner of Scotland is a unique and unusual mineral operation that has been in production since 1940 yet over the years has attracted little attention in either the technical or popular press. Lochaline Silica Sand Mine, situated on the remote Morvern Peninsula on Scotland’s west coast, some 40 miles from Fort William, is the only underground mine in the Tarmac portfolio and the only UK silica sand deposit capable of producing the raw material required to make the highest-quality domestic and decorative glassware.
Despite its highly prized product, it is perhaps not surprising that few people know of the site’s existence, as the mine workings and associated processing plant are naturally camouflaged by cliffs and forestry, while the remote coastal location allows the processed material to be dispatched by sea to the advantage of both the local environment and mine economics. In fact, the only evidence of the site is its ship-loading jetty which extends into the tranquil waters of Loch Aline and can be glimpsed by passengers on the Isle of Mull ferry which berths nearby.
History of the mine
Since 1940 the Lochaline Silica Sand Mine has been worked continuously, first by Tennant, Sons & Co. Ltd, then by Tilcon and now Tarmac. However, the deposit was first unearthed as far back as late the 1800s, but because of the remoteness of the location mining was considered uneconomical at that time. Another study in 1925 confirmed the deposit as one of the purest silica sandstones in the world, largely free from impurities and perfect for making high-quality glass, but once again the economics did not stack up and the material was left untouched.
In the end it was the Second World War which acted as the catalyst. When the German invasion of Belgium halted the import into Britain of silica used in the manufacture of submarine periscope lenses and gunsights, a new source of silica was urgently required. Suddenly the Lochaline deposit became an attractive proposition and a much-needed part of the war effort. The first shipment took place in 1940 with the sand destined for use in high-quality optical glass for the munitions industry, as well as for use in the ceramics and chemical industries.
After the war production continued to grow, providing vital employment in this remote and rural area, and by the 1950s some 65 people were employed at the mine. For the majority of the mine’s life the ex-works price of the product was probably the lowest of any underground mine in western Europe, a factor which often inhibited exploration and development. Nevertheless, various modernization programmes have taken place over the years including the construction of the ship-loading jetty, the relocation of the processing plant and the introduction of dumptrucks and electric–hydraulic drilling equipment. Today Lochaline employs 12 people and produces c.100,000 tonnes of silica sand annually.
Geology of the area
Comprising one of the few marginal deposits of the Cretaceous chalk sea preserved in the British Isles, the pure white silica sand forming the basis of the Lochaline sandstone was laid down some 135 million years ago on top of Mesozoic limestones and shales. The deposit was originally quite widespread and has been preserved from later erosion in the Lochaline area by a covering of younger Tertiary volcanics (basalt lavas) originating from the Mull volcano.
The silica sandstone seam, which varies from 3–12m in overall thickness, is grey, coarse and rich in alumina and iron oxide in its upper horizons, but after 1–2m becomes pure white and virtually free of impurities for a thickness of 5–8m before gradually grading into a greensand deposit at its base. Only the middle five metres of highly pure sandstone are extracted for processing. At the top of this productive layer hard bands or ‘ribs’ of recrystallized silica sandstone ranging in thickness from a few centimetres to 0.5m define and form the roof of the mine.
The sandstone seam is relatively massive and homogenous in nature, showing only occasional bedding planes and dipping gently north-north-west at approximately 2°. It is cut by a number of major and minor faults trending north-north-west to south-south-east which displace the seam by several metres in a number of places. Igneous dykes ranging from a few centimetres to 40m in width also cut through the sandstone in parts of the mine.
The sandstone itself is of a very high quality, comprising 99.8% quartz with well-sorted rounded to sub-rounded grains that generally break down to around 100–500µm in size. Impurities such as alumina and iron oxide occur in no more than trace amounts.
Mining operations
The sub-horizontal and laterally extensive nature of the deposit is such that mining and haulage costs can be kept to a reasonable level. In addition, although mostly an extremely friable rock, the presence of the hard ‘ribs’ in the upper horizons (combined with the competent basalt lavas above) allows the deposit to be worked by room-and-pillar techniques without the use of additional roof support.
The entire mine encompasses an area of approximately 1,500,000m2 (370 acres), essentially on a single level but with occasional ramps providing access between between the fault-displaced zones. Mining is currently taking place in areas 1 and 6 (see mine plan) with equipment being moved from one area to the other as required. Entry to the mine is via an adit located on the loch side at a height of about 10m above sea level and just 200m from the processing plant. At its deepest point the mine lies some 140m below the surface.
Mining operations are conducted five days a week with blasting taking place once a day at the end of each 8h shift. A total of 56 blastholes measuring 38mm in diameter and 2.8m in length are required for each blast. These are drilled by an Atlas Copco H282 Boomer rig, with each hole taking less than 1min to drill in the soft but competent sandstone. Generally, two or three 5m high x 7.5m wide faces are prepared for blasting each day.
With the assistance of a Normet access platform, the blastholes are loaded with Orica-supplied Lambrex cartridged emulsion explosives. These are fired in a carefully controlled sequence lasting approximately 7.5s, with detonation achieved by means of Orica half-second electric detonators. Each blast brings down approximately 250 tonnes of stone, some 80% of which is broken down into its constituent grains in the process.
Operations in each working area involve the simultaneous extraction of material from previously blasted faces while new faces are being drilled and charged. A Caterpillar 938G wheel loader is used to load the blasted material into two 30-tonne capacity Cat 730 articulated dumptrucks which negotiate a well worn route through the dark, labyrinthine network of previously mined stopes on the 2km haul to the processing plant.
A positive-pressure ventilation system, driven by large electrically powered fans, operates within the mine to clear blast fumes and maintain a clean working environment with a constant flow of fresh air. Mains electrical power for the ventilation fans, as well as for the Boomer rig, mine pumps etc, is reticulated underground to two former Coal Board transformers at 11kV, their output being stepped down to 1,100V before further reticulation and transforming to the working 415V three-phase supply.
Sand processing
The silica sand produced at Lochaline is of exceptional purity and requires relatively little processing. Only about 20% of the raw material from the mine requires crushing and the minor amounts of impurities it contains are easily removed from the weak cement binding the quartz grains.
At the processing plant the mixture of sand and lump sandstone is drawn from the raw material stockpile by a Cat 950F loading shovel and delivered into to a vibrating hopper feeder which feeds a two-stage crushing and screening process. This comprises a primary Becorit single-roll impact breaker followed by a secondary Mogensen sizer/Hazemag blow-bar impactor arrangement. From here the sand is fed to a single-deck Allis Chalmers wet screen which makes a cut at 1mm. All +1mm material is sent to a reject stockpile for subsequent backfilling within the mine, while the –1mm sand is pumped to a cleaning circuit where it is scrubbed to remove any traces of iron oxide, alumina and fine silts.
The cleaning circuit consists of an Eagle Iron Works screw classifier and a two-cell Denver attrition scrubber. From here the remaining sand fraction is pumped to a pair of Floatex towers which operate in tandem to produce standard- and fine-grade sand respectively. These two products are pumped to three Linatex towers (two for standard sand and one for fine sand) which dewater and stockpile the two sand grades. These finished-product stock-piles are further dewatered by underground vacuum pumps to achieve a final moisture content of less than 5%. The processing plant’s 120m3/h water requirement is drawn from a flooded section of the mine, with used process water being recirculated back to the mine for settling and subsequent reuse.
Approximately 8,500 tonnes of finished product are stockplied at the site at any one time, the fine sand fraction being a lower-volume commodity which amounts to about 10% of overall production per year. All the sand is dispatched by sea on the 2,200-tonne capacity MV Stina, which calls at the site on a weekly basis. Each consignment takes about 5h to load via the site’s 450 tonnes/h covered ship-loading conveyor.
Products and markets
One of the purest silica sands in the world, most of Lochaline’s output is used in the production of container and domestic glassware. However, the sand is also a key ingredient in the manufacture of green and black silicon carbide abrasives, borosilicate glass for laboratory and scientific use, and chemical and domestic ovenware.
The bulk of Lochaline’s output is shipped to Tarmac’s depot at Runcorn on the river Mersey for onward distribution to UK customers, as well as for bagging, grinding and other value-adding processes. Smaller consignments are also shipped directly to Ayr and Northern Ireland.
With exploratory drilling at Lochaline reveal-ing potential resources and reserves of over 40 million tonnes, this unique underground operation is likely to be a major source of high-quality silica sand for domestic and overseas markets for many years to come.
Acknowledgement
The editor wishes to thank Tarmac Northern Ltd for permission to visit the site and, in particular, Tim McGurk, mine manager, and Chris Rogers and Andrew Wallace of Wardell Armstrong for their help in preparing this article.