Vacuum Powerhouse
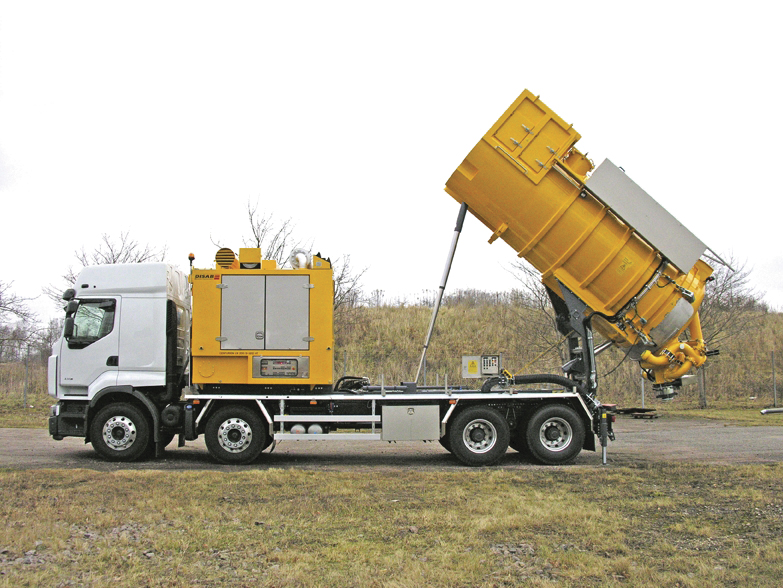
Nash Industrial Service acquire a new DISAB Centurion Vacloader to help deliver the most effective waste-management solutions for their quarrying customers
Nash Industrial Services, the Buxton-based industrial and contract cleaning services company, have added a new DISAB LN 200 Centurion Vacloader to their existing fleet of specialist waste-removal vehicles. Designed and manufactured in Sweden, DISAB’s Vacloaders have developed a reputation for delivering first-class operator standards and customer satisfaction.
While the LN 200 unit is the group’s most powerful mobile application to date, the full Vacloader range extends from smaller compact machines used extensively for industrial housekeeping and dust/waste removal to centralized vacuum systems for manufacturing plants, processing or storage facilities, aggregate screening houses and asphalt plants.
Nash Industrial invested £350,000 in the DISAB Centurion LN200/9-1817 ST based on the proven track record of their existing DISAB unit, the only difference being that the new Vacloader has a larger capacity.
A majority of work undertaken by Nash Industrial is for the local and regional quarrying, aggregates and cement companies, and with Tarmac and Lafarge among their major customers, managing director Steve Nash is keen to ensure that his company is well placed to provide and deliver the most effective equipment and materials-handling solutions.
‘We’ve grown pretty quickly since we started some six years ago, and I’m keen to make sure we continue to offer a top-notch service with a competitive edge,’ he said. ‘With a DISAB Vacloader we can do just that, especially for the type of customers we deal with – those running quarries, cement plants and aggregates equipment.
‘The DISAB Vacloader’s design incorporates a 9-litre Caterpillar donkey engine running on legal red diesel, which means both our operatives can focus on the task in hand instead of having one in the cab, as in those units that take the power from the truck’s own engine. Silo cleaning at cement plants is a major part of our work, and we use a DISAB in conjunction with other specialist equipment to deal with the large volumes of waste material in the silos quickly and safely.’
The DISAB Vacloaders have been specially designed to tackle almost any material in virtually any kind of containment that allows suitable accessibility. Manned by fully trained personnel, the Centurion LN 200 units can vacuum dry material such as sand, earth and cement, as well as slurry or liquid substances, which can then be transported to a designated area.
‘The pulling power of the DISAB means we can shift wet and dry material of almost any size, from very fine powders to large stones, in significantly less time than it takes for other less capable or powerful machines,’ explained Mr Nash. ‘Another key factor in the buying decision is our experience of dealing with the DISAB Group, along with their training and ability to supply spare parts, service and support. This minimizes any potential downtime for us and our customers.’
The Vacloaders incorporate a tipping function that allows the material in the large capacity tank to be tipped directly. The material carried by the DISAB system can also be discharged directly from an outlet either by gravity or by over-pressure (blowing function).
The LN 200 has a telescopic boom that offers ease of handling for the operator and delivers improved health and safety. In addition, the feature allows vacuuming to be achieved at a much higher height or distance. Depending on the type of material and moisture content, the LN 200 is capable of handling horizontal distances at of more than 250m.
Learn to Earn
Operator training has always been an integral part of the after-sales service and delivery of the DISAB Centurion range of Vacloaders. The group’s Learn to Earn scheme is a professionally developed and structured training programme designed to optimize both operator and machine efficiency.
So far DISAB have put more than 150 of their customers’ operatives through the Learn to Earn programme since it started two years ago, as after-sales manager Joacim Holmberg explained: ‘We’ve trained more than 950 DISAB operators through regular training sessions which began 10 years ago. The Learn to Earn programme, however, is more focused on maximizing operator effectiveness and efficiency because a Vacloader is not only an important investment for our customers but with the right training it will deliver numerous benefits very cost-effectively.’
‘With the huge amount of vacuum and thus suction and blowing power available, learning to operate a DISAB unit correctly is essential to optimize its unique capabilities in different situations,’ he continued. ‘One of our key training objectives is to show operatives how to use the DISAB Vacloader in an environmentally friendly way and avoid or minimize the risk of exposure to the material being handled, both for the operator and local environment.’