The Sustainability Benefits of CDE's Processing Plant for Velde Pukk
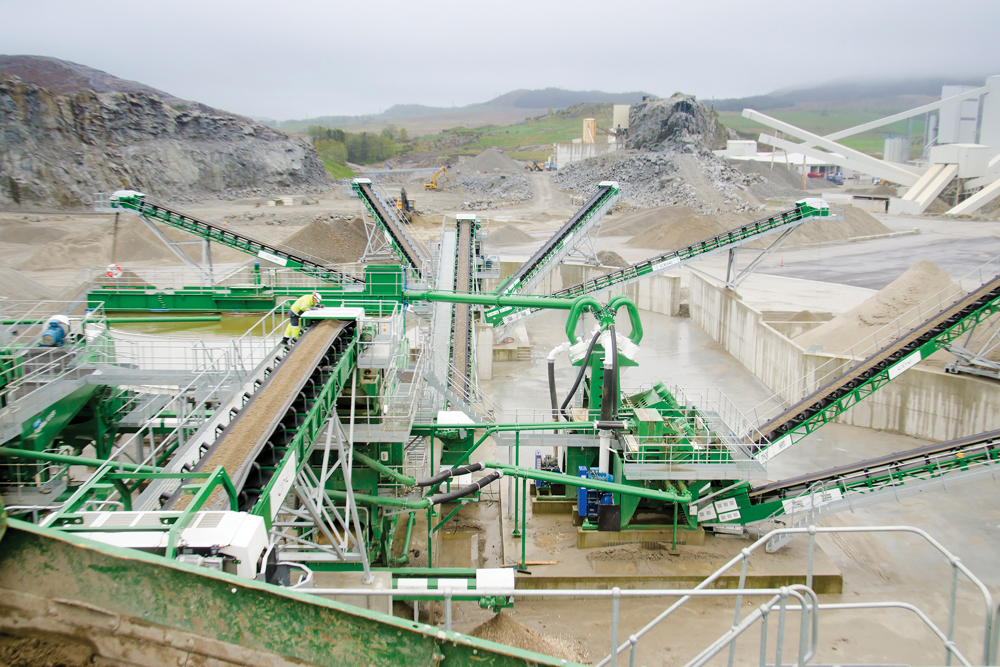
First published in the October 2016 issue of Quarry Management as Change for the Better
Working in close collaboration with CDE Global, Norwegian quarry operators Velde Pukk are proving their green credentials by reducing the use of primary materials and maximizing the production of recycled aggregates. QM takes a look at the sustainability benefits of the company’s CDE processing plant in Stavanger that will divert 600,000 tonnes of construction and demolition (C&D) waste from landfill every year
A new CDE washing plant operating at Velde Pukk’s Sandnes Quarry in Stavanger, Norway, is producing high-quality recycled materials from C&D waste. The 300 tonnes/h wet-processing plant – said to be the first of its kind in Norway – is also recovering good, clean rock from waste overburden on the same site.
Egil Velde, managing director of Velde Pukk, commented: ‘We opened discussions with CDE a number of years ago as we saw the huge opportunities presented by the recycling of C&D waste to high-quality, high-value recycled sand and aggregates across a wide range of applications.
‘As a result, we visited a number of existing CDE installations and have watched very closely the technological innovations developed by CDE in recent years that have maximized material quality and minimized waste from the process.’
The delivery of the CDE project was initially led by Eoin Heron, CDE regional director for Europe and Russia, who pointed out it was the flexibility offered by the equipment that proved to be an important factor in winning the contract.
He recalled: ‘We looked at the overburden for Velde and determined that we could design a plant that would allow them to not only recycle the C&D waste but also to recover material from the overburden, which could subsequently be used in their integrated operations.’
As well as operating the quarry, Velde specialize in the production of ready-mixed concrete and asphalt (and laying), while the business also runs it own transportation fleet around Sandnes and Stavanger.
The North Sea oil industry is a big driver for the economy in this part of Norway and the short trip from Stavanger airport to the quarry in Sandnes reveals a huge amount of infrastructure development on the ground – matched only by the number of helicopters transporting people back and forth from the oil rigs off the coast.
‘We are a well-established and respected name in this area and are providing material to a large number of local projects on a daily basis,’ said Mr Velde. ‘Our investment in the first wet-processing plant for C&D waste in Norway reflects our success – people expect innovation from us because of our history and we hope that our investment in the CDE plant is taken as a symbol of the potential that exists for this highly valuable resource to be turned into high-quality, high-value recycled sand and aggregates.’
Formed in 1984 by the father of the current managing director, the success story of Velde has been one of continuous investment and diversification. ‘When my father started the business we were producing aggregates for road and pipe construction from the quarry in Sandnes,’ said Mr Velde. ‘Now, my father has retired and I run the business in partnership with my two brothers, Harald and Reidar.’
The company has expanded significantly in the last decade, beginning with the installation of an asphalt plant at Sandnes Quarry in 2006. By 2007, the company had built what it says is ‘the largest, most modern and environmentally friendly production facilities for crushed rock processing and asphalt production in the world’. Other key developments followed; a new contracting division for road construction was established in 2008 and the business invested in a ready-mixed concrete plant in 2009.
‘Our business has always been about doing things the right way,’ said Mr Velde. ‘Our ambition to grow and build on the strong foundations that our father built always run in tandem with a desire to ensure that the business we build is sustainable and has minimal environmental impact.
‘In CDE we have found a company that shared this ethos and our desire for this project to be much more than a business transaction. We want to build long-term relationships with our partners based on trust and respect that will allow us to achieve our growth ambitions while maintaining a focus in our people, our customers and the world around us.’
Winning combination
According to Velde Pukk, working in partnership with CDE on the recycling plant has delivered significant efficiencies during the project delivery phase. CDE project manager Colum Bryson said that he believed the level of engagement with Mr Velde and his brothers, and the wide operations at Sandnes, was critical to the success of the project.
‘This is one of the largest mechanical installations that CDE has ever completed and, as with all projects, there were some very specific challenges to overcome during the design and delivery phase,’ explained Mr Bryson.
‘Sandnes Quarry is a very busy working site so the installation and commissioning phase had to take into account of the essential daily operations of the crushed rock processing plant, ready-mixed concrete plant and asphalt production facility. Thanks to the engagement and commitment of the Velde staff members, we were able to not only manage these issues but actually reduced project delivery time by 40%.’
During the transportation phase, there ‰ were 55 lorries involved in the delivery of the new washing plant at Sandnes quarry and, due to space limitations, it was essential that staged deliveries were organized. It was also important that this was carried out in such a way that minimized crane hire requirements on site.
‘Due to space restrictions on site, the project posed a number of challenges if we were to ensure that there were no additional costs incurred, ‘ said Mr Bryson. ‘We were able to achieve this as a result of the commitment that Velde demonstrated to the project from the outset. The value of getting the new plant up and running in the shortest possible time is often underestimated but not in this instance.’
Velde’s commitment to doing everything in the right way was immediately apparent and a visit to Sandnes Quarry demonstrates how far the operators have gone in preparing and ensuring the plant runs smoothly and efficiently. For example, a concrete pad was constructed and a variety of concrete product bays were built to facilitate the numerous radial product conveyors on the plant.
‘The concrete pad at Sandnes is an example of how all projects should be accommodated,’ said Mr Bryson. ‘The long-term benefits of this are huge: easier and more efficient movement of vehicles around the site; and quick, simple and safe access for essential plant inspection and maintenance.’
The specification of several radial stockpile conveyors for the washed recycled sand and aggregates is a fine example of Velde’s commitment to reducing the environmental impact of their operations.
‘Reducing our transport movements on site has resulted in significant cost savings,’ commented Harald Velde, operations director for Velde Pukk. ‘This also eliminates unnecessary double handling of our products. In addition to the cost benefits, the reduction in transport movements reduces on-site health and safety risks, as safer, happier people are far more productive. This was a important factor for both us and CDE in the design of the washing plant.’
Materials processing
Feed material is first delivered to two R2500 primary screening units (located side by side), each featuring an integrated apron feeder that splits the feed across two separate 150 tonnes/h processing lines.
From the feed hopper, material is sent to the R2500 machine while +90mm material is removed via a double-deck grizzly screen (5m x 1.5m). The remaining material is discharged on to two horizontal feed conveyors.
Products, notably 0–90mm, are delivered to two AggMax 151 modular log-washers where a pre-screen removes 0–4mm material which is then fed directly to a EvoWash 201 sand washing plant.
‘The pre-screen is essential at this stage to ensure the efficient operation of the AggMax,’ said Eoin Heron. ‘Not only does it ensure that the aggregate fraction is satisfactorily scrubbed but it minimizes wear in the AggMax logwasher and maximizes sand production.’
After aggressive scrubbing in the two AggMax units, 4mm–90mm recycled aggregate is sent to a ProGrade P2-108 sizing screen. Both AggMax machines have a trash screen at the rear, which removes any lightweight and organic contamination from the recycled aggregate. Any sand liberated during the attrition phase is also sent to the EvoWash sand washing plant and ensures maximum product yield from the C&D waste feed.
The ProGrade P2-108 sizing screen is part of the new Infinity screening range from CDE and includes a patented side wall construction, which removes unnecessary weight and reduces the power required to run a screen.
The screen is set up to produce a range of products, including: 4mm–11mm; 11mm–16mm; 16mm–22mm; and 22mm–90mm, all of which are stockpiled via static and radial stockpile conveyors.
The EvoWash sand washing plant produces two grades of sand: 0–2mm; and 2–4mm. The former is used in the asphalt plant at Sandnes while the latter is used in Velde’s concrete operations.
Given the space restrictions on site, it was essential that full water recycling and sludge management was included on the project. The waste water from the plant is delivered to an AquaCycle A1500 thickener where it is dosed with flocculant. This forces the very fine particles of silt and clay to bind together and sink to the bottom of the tank.
Meanwhile, the recycled water overflows the peripheral weir and is stored in a concrete buffer tank before being recirculated to the washing plant. The sludge at the bottom of the AquaCycle thickener is discharged automatically at a certain pressure and is sent to another concrete buffer tank which is fitted with a set of agitators to ensure consistent sludge is delivered to a overhead beam filter press.
The filter press model specified is one of the largest available and comprises 169 plates each measuring 2m x 2m. These plates press the sludge to remove more water before the filter cake is discharged to a bay below.
‘We are currently using the filter cake that has a dry solids content in excess of 80% for the construction of embankments, which means we eliminate waste from this stage of the process,’ commented Harald Velde. ‘The only waste from the process is made up of the lightweight and organic contamination removed during the attrition phase.’
The future
The CDE plant at Sandnes Quarry is expected to divert around 600,000 tonnes of C&D waste from landfill every year. Velde Pukk aim to develop the market for recycled material in Norway in the months and years ahead through extensive testing and use of material in their own operations.
The business case for the wash plant was made on the basis of the cost savings that Velde Pukk would achieve as a result of the diversion from landfill. The Norwegian operator, however, has higher goals and see the CDE plant as an opportunity to build the brand value of recycled materials and increase its use not only in Norway but across Europe and the rest of the world.
‘We are committed to finding more sustainable ways to meet growing demand for our mineral reserves,’ said managing director Egil Velde. ‘Construction, demolition and excavation waste materials are a hugely valuable resource that can help us to extend the life of our natural reserves for future generations.’
This is a view that is shared by all three of the Velde brothers. ‘We wouldn’t accept a wasteful approach to the processing of virgin materials so it’s time that the same approach was taken with C&D waste,’ said Harald Velde.
The approach taken by Velde is refreshing and signals not only a change in attitude to C&D waste and the potential it offers but also that the industry is in good hands as it seeks to stay relevant, be viable and secure the future innovation that will lead to more waste materials being recycled.
- Subscribe to Quarry Management, the monthly journal for the mineral products industry, to read articles before they appear on Agg-Net.com