Securing mineral reserves still a problem
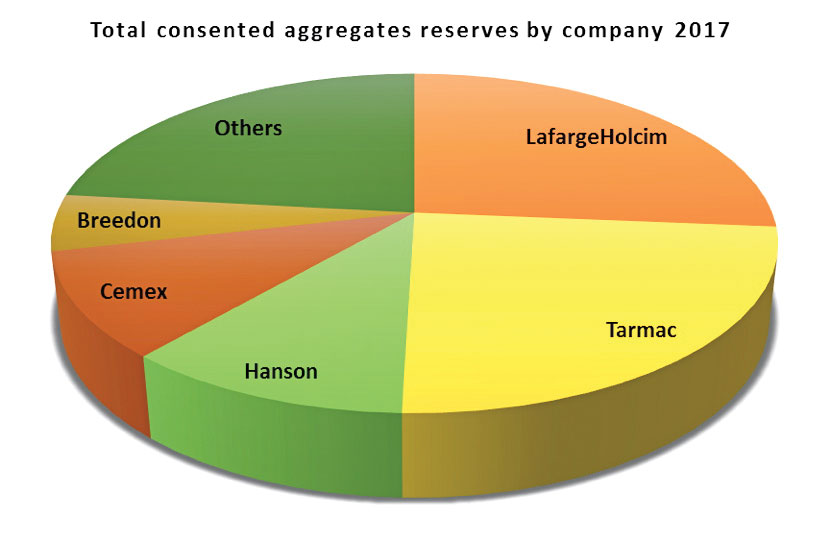
First published in the July 2017 issue of Quarry Management
It is vital for mineral planners, aggregates companies and other interested parties to know the current state of aggregates reserves. There is a generally held view that reserves are declining. This is correct, but the supporting evidence is often lacking. Information contained in published reports is usually at least a year old, often much older. In some parts of the country data are virtually non-existent. To help fill this information void, BDS have just updated their report entitled ‘Estimated reserves of pits and quarries in Great Britain’. Reserves’ life and quantities are shown in the report as at the end of 2016, taking into account planning decisions up to the day of publication. The report is also site specific, listing all active and inactive sites. This is also breaking new ground – no other report goes into this level of detail.
There is a general belief that diminishing reserves are a problem of the South East. The BDS report shows that the situation is more complicated. Some of its conclusions are:
- The industry sand and gravel landbank is now estimated at 14.5 years
- Whilst some parts of the South East struggle to replenish reserves, other areas are relatively well off
- At the end of 2016, Yorkshire & Humberside was estimated as having the lowest sand and gravel landbank
- The companies with the greatest levels of sand and gravel reserves are Tarmac, Hanson and CEMEX
- The landbank for crushed rock is calculated at more than 40 years. Most quarries will be able to sustain production, but there are specific areas where reserves could become a problem
- Aggregates Industries, Tarmac and Hanson have the highest levels of crushed rock reserves.
BDS have been flagging up the problems of replenishing aggregates extracted for some time. In any recent typical decade, only in one year out of the 10 will the industry fully replenish its reserves, and even then, only due to a small number of major consents. A majority of applications for additional reserves are granted, so it could be argued that the problem of replenishment is due more to companies not bringing forward proposals.
The industry is not going to suddenly find itself without aggregates. Pits and quarries will close, and materials will be brought in from further away. However, there are issues that aggregates companies need to address if their strategy is to be appropriate for future markets.
More than a quarter of pits and quarries with reserves are currently closed. Some have never opened after planning consent was granted; others closed during the recession and have not reopened. It will need significant investment at many of these sites to bring them on stream. It may not be economic to develop all of these sites – due to poor mineral quality or the high cost to access the reserves. In these cases, the stated landbanks will turn out to be lower.
The reserves position in crushed rock is better than sand and gravel, although reserves at some high-PSV quarries are a concern. This has ongoing national repercussions for this important material. It is also noted that three of the largest rock quarries in the country – in Somerset and Leicestershire – have 15 years or less reserves remaining. This still gives the companies sufficient time to secure additional reserves. However, it can take at least five years to locate suitable resources and obtain planning consent. The companies concerned need to be developing their longer-term strategies. It may be that a further lateral extension is no longer possible at these quarries. Future operations may depend on working reserves below the existing processing plant and/or bringing in materials from a mineral-bearing site nearby. This would have repercussions for both capital and operating costs.
It is still possible to develop new aggregates sites. However, this process would be too slow for any new market entrant wishing to establish several operations in a short space of time. The planning process tends to favour existing companies that can, if necessary, trade off existing reserves with resources at a better location.
There are small but noticeable changes occurring in the added-value ready-mixed concrete and asphalt markets. The planning process makes it easier to develop new facilities for these markets than for aggregates. In these sectors, any plants that close are invariably operated by one of the leading players, yet any new plants are usually installed by a local independent operator or market entrant. This has been confirmed by a recent client project. The recent closure of two asphalt plants in the same area prompted an independent company to commission BDS to analyse the potential to establish its own plant.
Therefore, there is a different trend occurring in the market shares of the larger companies in aggregates, compared with added-value aggregates markets. The planning process tends to favour existing aggregates companies, which will see companies broadly maintain their existing shares. In added-value markets, the combined shares of independent companies are increasing – slowly but interminably.
In conclusion, there are challenges ahead to both maintain and grow businesses. The successful companies will be those that understand the underlying trends and implement the most appropriate strategies.
- Subscribe to Quarry Management, the monthly journal for the mineral products industry, to read articles before they appear on Agg-Net.com