Intelligent Quarrying 2015 Conference Report
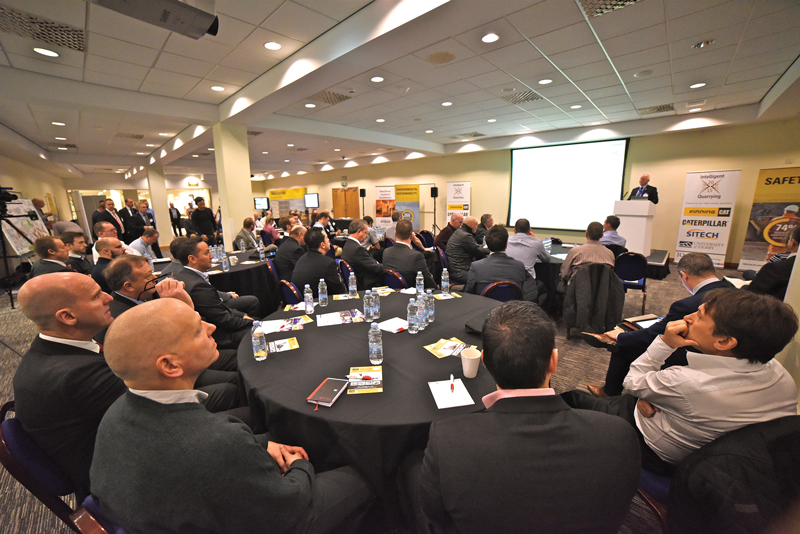
First published in the January 2016 issue of Quarry Management
The 2015 Intelligent Quarrying conference, organized by the Institute of Quarrying (IQ) in association with the Building Research Establishment (BRE) and run over two days (24–25 November) at the Ricoh Arena, in Coventry, explored various themes and ideas affecting the mineral extractives industry, with a particular focus on how leadership, employee engagement and motivation will play a part in delivering continuous improvements in business performance, health and safety, skills and innovation.
The proceedings on day one, which was aimed at senior-level managers from across the industry, commenced in the early afternoon with a brief welcome and introduction by IQ President Anthony Morgan, who commented on the industry’s need to operate in an innovative manner and how leadership, employee engagement/motivation and continuous skills development will play a pivotal role in delivering ongoing improvements in business performance, particularly health and safety.
The first main speaker of the session was Peter Hansford, Chief Construction Adviser to the UK Government, who, in his final presentation after three years in post, provided a ‘View from the construction sector’. With the global construction market forecast to grow by more than 70% over the next decade, Mr Hansford began with an overview of ‘Construction 2025’, the joint industrial strategy which sets out how the construction industry and the UK Government will work together to put Britain at the forefront of global construction over the coming years.
He explained how, by working in partnership, industry and government jointly aspire to achieve: a 33% reduction in both the initial cost of construction and the whole-life cost of assets; a 50% reduction in the overall time from inception to completion for new build and refurbished assets; a 50% reduction in greenhouse gas emissions in the built environment; and a 50% reduction in the trade gap between total exports and total imports for construction products and materials.
Mr Hansford said this clear set of aspirations for UK construction was based around five broad themes: People (an industry that is known for its talented and diverse workforce); Smart (an industry that is efficient and technologically advanced); Sustainable (an industry that leads the world in low-carbon and green construction exports); Growth (an industry that drives growth across the entire economy); and Leadership (an industry with clear leadership from the Construction Leadership Council).
To help achieve these ambitions between now and 2025, Mr Hansford said the Construction Leadership Council, which was created in 2013 to lead the transformation of the industry, was being streamlined from its initial 30+ members to around a dozen members from across industry and government. These members, he said, would champion and lead six key workstreams – people & skills; green & sustainable; supply chain & business models; smart & innovation; exports & trade; and industrial communications – with resulting actions owned and delivered by industry bodies. Urging the quarrying sector to become more involved in these workstreams, Mr Hansford said the key issues for the minerals industry were the skills shortage, innovation and productivity.
On the skills shortage, he commented on the industry’s lack of ethnic and gender diversity, and the negative perception that many people have of working conditions in the sector. Mr Hansford argued that to become an industry of choice, quarrying needed to transform its image by inspiring and engaging with pre-teenage youngsters, and their teachers and parents. Firms within the construction sector had been encouraged to adopt a school, and quarrying should do the same, he said.
On innovation, Mr Hansford said the world was being transformed by digital design, advanced materials and new technologies, and that in the transition to a digital economy and the rise of smart construction, quarrying needed to fully embrace the Internet of Things (IoT), Building Information Modelling (BIM) etc.
On productivity, Mr Hansford said that while there were undoubtedly ‘exciting years ahead’, the massive scale of projects in the pipeline, such as HS2, Hinkley Point C, the Thames Tideway, Crossrail 2, the Northern Powerhouse, a new London runway, and the £15 billion roads programme, meant that the challenges facing the sector were unprecedented in modern times. He said the industry urgently needed to transform itself to ensure it was fully fit for purpose to be able to match supply to demand.
Next to take the stage was Dr Miles Watkins, group business development director with BRE and Chairman of the IQ, who, in a presentation entitled ‘Our leadership challenge’, put forward his four top tips for becoming the supplier of choice. The first tip, he said, was to ‘embrace and engage with the digital agenda’, as all future projects will take place in the digital space and BIM is going to inform the language of construction going forward. He also called for social media to be grasped with both hands, citing CEMEX as prime example of a company that has done just that. Although this would not be without its risks, he argued that this would happen anyway and that the free flow of information was a good thing. Moreover, with the creation of online personalities, great ‘industry characters’ would begin to appear digitally in future.
Tip number two was to ‘be close to your customers’. Dr Watkins said quarry companies were there to solve customers’ problems, not just sell them a load of rock, and that early conversations and collaboration could make a huge difference through a better understanding of customers’ needs. Attention to detail and thinking projects thorough is key, and much of this is down to the action of individuals, he explained. He urged quarry companies to engage with their customers’ work from the start, offer them what they need and help make them look good, thereby making themselves indispensible.
Tip number three, to ‘show innovation’, was about demonstrating greater levels of innovation to improve industrial processes and productivity, and how companies should come together to develop joint/repeatable solutions, to ensure supply matches demand. Dr Watkins said the industry should seek to lead and drive change through greater innovation to create an extractives industry that is fit for the future. This is not something that is going to happen by incremental steps, he argued.
With society becoming increasingly interested in what the industry produces and where it comes from, Dr Watkins’ fourth and final tip, to ‘be accountable’, focused on responsible sourcing and managing the industry’s impact on society and the environment. He encouraged producers to reduce waste, look at new ways of using existing products, think about things from a re-use perspective and become part of the ‘circular economy’.
For the remainder of the afternoon, Peter Hansford and Dr Watkins were joined on stage by Peter Baker, Chief Inspector of Construction with the HSE; Alan Gibbon, development director with MIRO; and Oliver Novakovic, technical and innovation director with Barratt plc, for a panel session chaired by Colin Jenkins, managing director of Jenco Consultancy. A wide range of questions from the audience on issues such as improving leadership skills, boosting research and development, increasing diversity within the workforce and engaging with the ‘Minecraft’ generation, drew an even broader range of responses from the panel, although a common thread that appeared to run through much of the feedback was the need for greater openness, more collaboration and more innovation.
For the first time at an IQ conference, the day’s proceedings were summarized in the form of an novel graphic display, which was hand-drawn in real time during the event by John Ashton of Crackerjack Visual Thinking. His large and detailed representation (see fig. 1) highlighting the key points raised was designed to engage delegates and help stimulate a conversation using the power of visual thinking.
Day one of the conference concluded with an overview of the full range of mineral product course programmes on offer at the University of Derby, by Mark Osbaldeston, Head of the Centre for Mineral Products Professional Development at University of Derby Corporate, followed by the annual IQ student awards, presentation of IQ Honorary Fellowships, the awarding of the President’s Trophy, the announcement of a new Corporate Professional Competence (CPC) member, and the awarding of prizes for the IQ’s ‘Quarries Rock’ photography competition winners (see this month’s IQ News section for further details).
Aimed specifically at quarry managers, supervisors and operatives working in the mineral products and extractives industries, day two of the conference featured a plenary session keynote address by Colin Mew, HM Principal Inspector of Quarries with the Health and Safety Executive (HSE), followed by a busy seminar programme comprising 15 high-quality presentations covering a range of topics including: health and safety; innovation; and people and skills. The seminars ran throughout the day across two locations, giving delegates the opportunity to choose the presentations that were of most interest and relevance to them.
In his keynote address, Colin Mew reiterated the importance of delivering health and safety best practice in the quarrying sector. While the industry has made significant progress towards the Target Zero initiative, Mr Mew said there was still a lot of work to be done to create a sustainable safe working environment for the benefit of all employees and visitors. He went on to explain the key factors in improving health and safety in the quarry workplace including: a stronger, visible felt leadership; building competence; and ensuring staff involvement at all levels.
In a joint presentation, Roy Bush, HM Inspector of Quarries, and Mike Phillips, general manager of the Institute of Quarrying, discussed the role of the Quarries National Joint Advisory Committee (QNJAC) and how it is gathering toolbox talks which provide essential health and safety guidance throughout the industry.
Since 2000 there has been an 85% reduction in accident rates across the quarrying sector and Mr Bush highlighted QNJAC being part of this remarkable journey, having promoted more than 50 forms of guidance.
Examples include: a contractors’ road map to safety; traffic management; guidance on quarry specific RIDDOR requirements; and downloadable forms for use in workforce site inspections.
For the industry to achieve zero preventable accidents (under Target Zero), Mr Bush said he believed QNJAC has an even greater responsibility to ensure health and safety standards are met in the wider quarrying industry. He emphasized the next step for the Committee was to compile a single series of QNJAC-branded toolbox talks, which will be approved by the HSE and published for use within the sector.
Mr Phillips spoke about the challenges and opportunities for QNJAC going forward, including the need to create a clearer identity for the Committee and a better understanding of the work it does. He also urged the sub-committees and their members to embrace digital technology and social media (eg Twitter, LinkedIn, Facebook etc), which has led to the dual development of the revamped QNJAC website (www.qnjac.co.uk) and free App, both of which now provide a wealth of easily accessible, approved content in a quick and intuitive format.
Later, Julian Smallshaw, IQ’s head of educational development spoke about how businesses can secure future profits through continuous improvement of processes and people; Anthony Comber, technical support manager for Renishaw UK, gave a talk on best practice in blast optimization for improved performance; and Mick Knight, business manager for Finning, discussed in detail the importance of supplying bespoke solutions and helping customers manage their equipment assets and associated costs.
Douglas Eskdale, founder and innovator of WorkSAAS, an integrated SHEQ compliance management system, covered some of the toolkits and techniques available to help businesses measure and monitor their health and safety performance. Using a case study, he highlighted the safety and cost-savings benefits gained from implementing a WorkSAAS solution, which provides an appropriate management infrastructure for identifying, monitoring and communicating risks associated with work task activities.
Continuing the theme of health and safety best practice, Simon Day, regional general manager for Hanson, provided an update on the current progress made by the QNJAC plant and contractors working group, while Paul Joel of Tarmac outlined the progress that was being made in developing the latest QNJAC geotechnical guidance on best practice for quarry workers and operatives.
One of the biggest challenges facing the quarrying industry is addressing the alarming skills shortage and Brit Wagstaff, a consultant for recruitment specialists Austin Fraser, highlighted some of the major barriers to overcoming diversity in the sector. In particular, she demonstrated and recommended the use of specialist recruitment agencies in finding, attracting and retaining high-calibre staff for businesses.
The final concurrent presentations on the day came from Dr Hugh Datsun, senior environmental scientist for DustScan Ltd, who spoke about the importance of dust monitoring in the aggregates industry and the assessment of mineral dust impacts on planning, while Penny Lewin (events operations manager) and Harvey Sugden (showground event manager) from QMJ Publishing Ltd, gave a ‘behind the scenes’ presentation on the biennial Hillhead exhibition.
Penny provided an historical insight into the show, including some of the site development milestones reached and measures taken to accommodate the growing number of exhibitors and visitors to the event, and Harvey spoke about the marketing and promotion of Hillhead, giving a brief insight into the health and safety challenges and processes involved in organizing the world’s largest working quarry show.
Presenting a new challenge for 2016, he said exhibitions now need to be CDM (Construction Design and Management) Regulations compliant. This will involve putting together a construction phase plan for the next Hillhead show, demonstrating how the work will be managed safely, including: details of the site rules; daily briefing arrangements; and fire/emergency procedures and action plans for the control of specific risks (eg falls from height, collapse of structures, crane operations, heavy lifting etc).
- Subscribe to Quarry Management, the monthly journal for the mineral products industry, to read articles before they appear on Agg-Net.com