Annual Conference 2004 Review
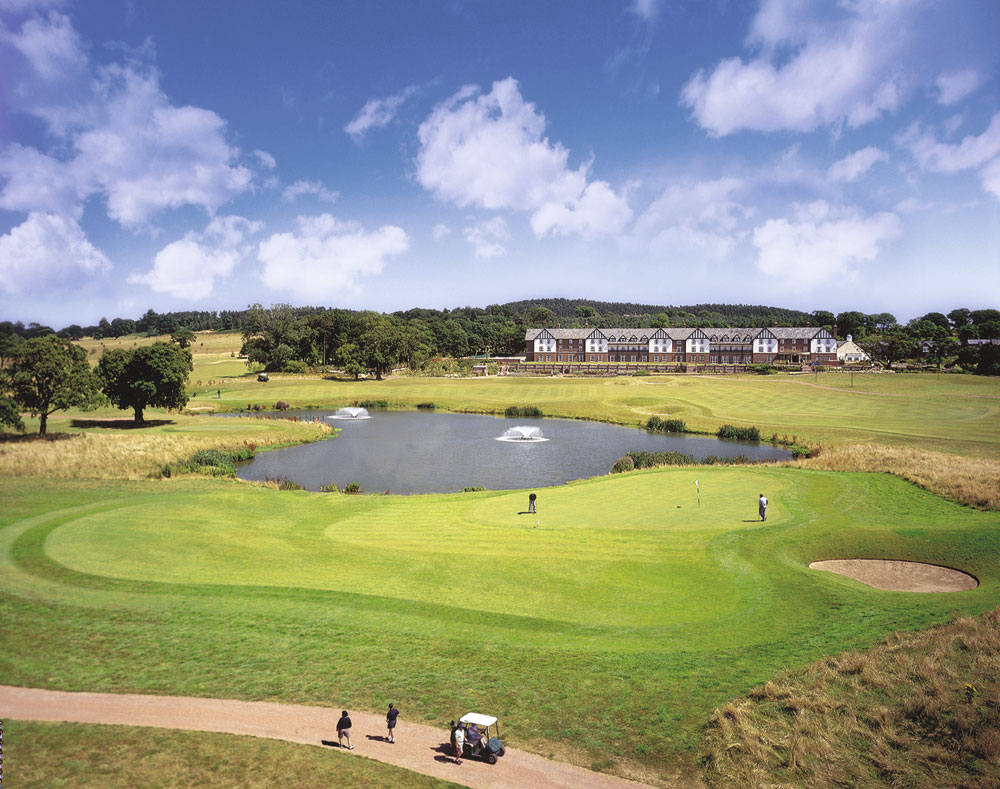
A report on the proceedings of The Institute of Quarrying's annual conference symposium
The annual conference 2004 was hosted by the North Wales branch in the splendid Carden Park Hotel near Chester, which is surrounded by two golf courses and parkland. Indeed, nearly 50 persons competed in a golf competition organized on the day following the symposium.
The symposium entitled ‘Developing a culture of health and safety’ was intended to review the improvements achieved by the implementation of the policy of ‘Revitalizing health and safety’ and the ‘Hard target’ initiative, the first stage of which concludes next year. The programme for the symposium was arranged with the active co-operation of the Quarry Products Association and the Health and Safety Executive, which ensured that the subjects of the presentations were extremely relevant and that the information presented was fully up to date. The importance of the subject allowed The Institute to attract executives, senior managers, industry experts, public figures and consultants to address the delegates.
As measured by the number of delegates registered for the symposium, the conference was an overwhelming success, well exceeding the planned number and even exceeding the numbers attending Minerals 2002 and ECMP ’99. On the day, more than 230 members and non-members had booked for the event, which stretched the catering facilities. Indeed, the planning numbers were also exceeded for all of the social events.
This year the symposium was arranged as two consecutive sessions chaired by Terry Last, newly elected president, and Cedric Hollinsworth, chairman of Council. In order to cover a wide range of subjects within the general theme, the traditional format of the programme had been modified to include 14 succinct presentations instead of only seven or eight. Although this produced some over-run of the morning session, this format seemed to be appreciated by the delegates.
The proceedings began with a welcome by Geraint Roberts, chairman of the North Wales branch, who introduced the newly elected president, Terry Last. In his turn, Terry introduced the keynote speaker, Bill Callaghan, chairman of the Health and Safety Commission, who had kindly agreed to present the prizes in a ceremony that commenced with the awards for the Institute’s Professional Examination.
First among the prize winners was Joe Cookson who won both the Clugston and Preston Awards and came runner-up in the Ransome & Rapier Award. Clare Chadwick also won three prizes, namely, runner-up for both the Clugston and Preston Awards and winner of the Rexnord Award. Two other students won two prizes. Richard Savage won the Ransome & Rapier Award and was runner-up in the Rexnord Award. Jonathan Banner won the Coles Award and was runner-up for the Tilcon Award. James Whittaker won the Goodwin Barsby Award and Doreen Spratt was runner-up for the Coles Award. Regrettably, neither John Leighton, winner of the Tilcon Award, nor Paul Kiely, runner-up for the Goodwin Barsby Award, was able to attend the conference.
The Marston Award for the best paper presented to a branch meeting was given to Carmella Barbour for her paper discussing the value to a business of internal customers. Just recently, Carmella was appointed manager of Ivonbrook Quarry and is a member of the Midlands branch committee. The Ruston Bucyrus Award went to Ed Reed for his paper describing a strategy for sustainability presented to ‘Minerals 2002’.
Over many years, starting in 1994, The Institute has worked on the development of occupational standards for quarry managers and the certification of competence. This work culminated in 2002 with the accreditation of NVQs in Health, Safety and Environmental Management in Quarries, commonly described as SHE NVQs, to be awarded by EPIC Awarding Body. During this year the first candidates successfully completed the assessment process and were invited to the conference to be awarded their certificates and congratulated by Bill Callaghan. The very first were Andy Aplin at level 3 and Ian Southgate at level 4 to be followed shortly by Paul Fisher, Steve Thatcher and Kevin Traves at level 5.
Finally, the president invited Steve Cole, chairman of the West of England branch, to accept the President’s Branch Trophy from Bill Callaghan in recognition of the efforts of the branch committee to recruit new members and promote CPD.
The keynote address was given by Bill Callaghan, who compared the performance of the quarrying industry to industry in general and took the opportunity to present the recently published strategy of the HSC for 2010 and beyond. Nationally, industry had responded to the ‘Revitalizing’ initiative for health and safety, which had a target of 10% reduction of injuries and fatal incidents, but improvements seemed to be stagnating. By comparison, the quarrying industry was exceeding targets towards a 50% reduction and could be a model for others. The strategy had four principal elements: partnerships, promotion of benefits of safe practices, concentration of resources, and communication. In these respects, he was pleased to see partnerships between the TUC and the quarrying industry to train safety representatives and between EPIC, The Institute of Quarrying and the HSE to create a competent and, thereby, safe workforce. He congratulated Foster Yeoman on the introduction of a rehabilitation scheme to get people back to work. In the formulation of future ‘Hard targets’ he stated that it was important to consider occupational diseases and ill-health in addition to physical injury.
The second speaker was Robbie Robertson, chief executive officer, Tarmac Group, who stated that concern for the health and safety of employees was not only a moral imperative, but good business. Tarmac had set a more demanding target of zero lost-time injuries by 2005 and he was pleased to report that substantial improvements had been made. For example, 90% of operations had suffered no lost-time injuries for over a year and the business was 20 times safer than in 2000. He was convinced that the target was achievable provided that everyone was totally committed.
In his response, Tom Mellish, TUC health and safety policy officer, expressed his disappointment that ‘Revitalizing health and safety’ had not proven to be as radical as promised. He claimed that 2004 had been a very bad year for fatal injuries at work and stated his concerns about the policy to seek to manage risks and not eliminate them, the low investigation rate of incidents and the movement towards providing advice rather than enforcement. In support of his argument he lamented the fact that the HSE’s budget had been frozen until 2006.
Next to speak on behalf of the workforce was Colin Evans, a quarry supervisor at Hanson’s Penderyn Quarry, and well known for his contributions to creating a safer workplace. He described the day-to-day practicalities of instilling safe behaviour into the workforce.
Last to speak in this session was Ken Riley, chairman of EPIC Training and Consulting Services Ltd. He described the management, funding and work of EPIC, stressing that this training organization belonged to the industry through QPA and was responsible to the industry through its Council. EPIC existed to carry out projects requested by industry. With respect to creating a competent and safer workforce EPIC offered a variety of NVQs for operators, the SHE NVQs, training courses and videos, the contractors safety passport scheme and skill cards. He encouraged industry to make more use of EPIC.
In the next session devoted to improving occupational health, Dr Jonathan Cleeland of Private Health Care tackled the difficult problem of monitoring for work-related stress. While there is no clear definition of stress, nor the consequent diseases or disorders, there is a need to consider monitoring under the ‘management regs’. Stress may be the cause of ‘adjustment disorders’, which may be manifested as symptoms in both organizations and individuals. Examples are absenteeism, reduced performance, irritability, loss of sleep and carelessness leading to unsafe incidents. He recommended companies to take medical advice so that common causes and symptoms could be recognized and to monitor employees periodically by questionnaire.
Michelle Wyart-Remy, secretary general of the Industrial Minerals Association – Europe, attempted an even more difficult task of informing delegates of the likely regulation by the EU of respirable crystalline silica (RCS). The issue was confused by the scientific controversy surrounding the definition of RCS as a carcinogen. Inhalation of RCS can cause silicosis, which increases the risk of lung cancer in humans. It is possible that RCS may be classified as a dangerous substance for purposes of labeling or it may be banned from public products or it may be classified as a carcinogen and given a very low occupational exposure limit (OEL) of 0.05mg/m3. Michelle advised the quarrying industry to be concerned and interested in the debate.
The effectiveness of reward and incentive schemes for safe work was discussed by Ivan Carr of Collinson Grant Consultants. From his experience he concluded that reward and incentive schemes do work but they must be simple and the linkage must be obvious. The reward should not be linked to the outcome of fewer reported incidents and trade unions are opposed to such schemes that may result in incidents going unreported. Similarly, the reward should be given if production is maintained and not conditional on any increase in production. In the most effective schemes the rewards are paid for inputs such as implementation of safe systems of work and removal of hazards. Ivan also speculated on the effectiveness of including directors’ bonuses in the safety incentive scheme!
In the final presentation before lunch, Roseanne Hayward, development director, EPIC Training and Consulting Services Ltd, outlined the new services offered to industry by EPIC using an acronym, ABC — Always Be Competent. A guide to N/SVQs for employees has been prepared and is proving very helpful in removing the ‘mystery’ surrounding NVQs. The company is now an assessment centre employing assessors who are available to the industry and can provide on-line assessment and qualification of assessors through OCR. EPIC has developed special training courses for hauliers and environmental courses, is actively involved in the recruitment campaign for the industry and has produced a CD-ROM promoting careers to young people.
During lunch and breaks for refreshments, delegates were able to visit the exhibition stands of suppliers of safety equipment and advice to the industry.
The delegates had been kept waiting in trepidation for the first presentation after lunch, in which Rob Pearce, Principal Inspector of Health and Safety, announced the expectations of the HSE especially in respect of enforcing the requirement to provide demonstrable evidence of competence. Rob began by illustrating a number of dangerous occurrences and incidents that had caused injury. His purpose was not just to grab attention, but to deliver the message that tragic incidents like these were avoidable especially if the workforce is competent. In his opinion, the management of the industry needed to know more about the quarrying process, to understand the consequences of its decisions and to involve the workforce. He cited the Royal Commission on Quarries which concluded that many managers were better acquainted with commercial matters than working a quarry.
With respect to demonstrable evidence of competence he cited NVQs, registration with the Engineering Council or Chartered professional status and continuing professional development (CPD), and he expected all employees to be able to produce this evidence by 2010. He stated that long experience alone did not prove competence and that evidence of underpinning knowledge was required in addition. He was, therefore, concerned about the dwindling number of courses and educational establishments dedicated to training people from the mining and quarrying industries.
Geraint Morris of Lafarge Aggregates then reviewed the progress of a Working Party of the Quarries National Joint Advisory Committee (QNJAC) that has the objective of providing guidance on good practice and a standard specification for access to mobile plant. He explained that statistical analysis had shown that egress, exit and access to mobile plant for inspection, cleaning and operation was a significant cause of incidents. Efforts to reduce these incidents were not assisted by the lack of a common specification agreed between the major operating companies and the consequent compliance with minimum standards when better was achievable. He illustrated both good and bad examples of providing access.
The theme of the conference was addressed directly by the next speaker, Tony Metcalfe, health and safety director of Wates Construction. He stated that the construction industry contained many bad practices and had a poor safety record. His company had examined practices overseas and found the best culture in Finland, where workers considered that keeping the workplace safe and clean was part of their job. Following their example, Wates had introduced excellent welfare facilities for workers, controlled access to sites, innovative technology, guidance on PPE, a travelling safety roadshow, and were now obtaining sustained and substantial improvements.
A montage of video clips showing innovations to improve health and safety was then presented by Martin Isles of the Quarry Products Association. Each clip related to an entry in the QPA Best Practice competition and demonstrated what could be achieved by aware and motivated employees at relatively little cost.
The symposium was concluded most appropriately by Professor Peter McKie, CBE, formerly chief executive officer of Dupont, who delivered the triennial McPherson Memorial Lecture entitled ‘Visible Felt Leadership’. He began by giving the reasons for concern with health and safety that had been mentioned by previous speakers and continued by proposing four elements which, when combined, determined the level of safety, namely: equipment, systems/procedures, people, and leadership. It is known that 90% of incidents are caused by people so, in his opinion, the key element is visible felt leadership to change the behaviour of the people. The quarrying industry has made good progress but the ‘low hanging fruit may have been harvested’. From his point of view the industry had a number of problems to overcome including: a lack of conviction by some that zero incidents was possible, a culture based on production and long hours, a belief in engineering solutions, and an autocratic style of management that created a dependent state of mind in the workforce. Above all else it was essential to convince the workforce that management was committed to achieving improvements through ‘visible felt leadership’.