Ultra-fine Screening Of Dry Mineral Powders
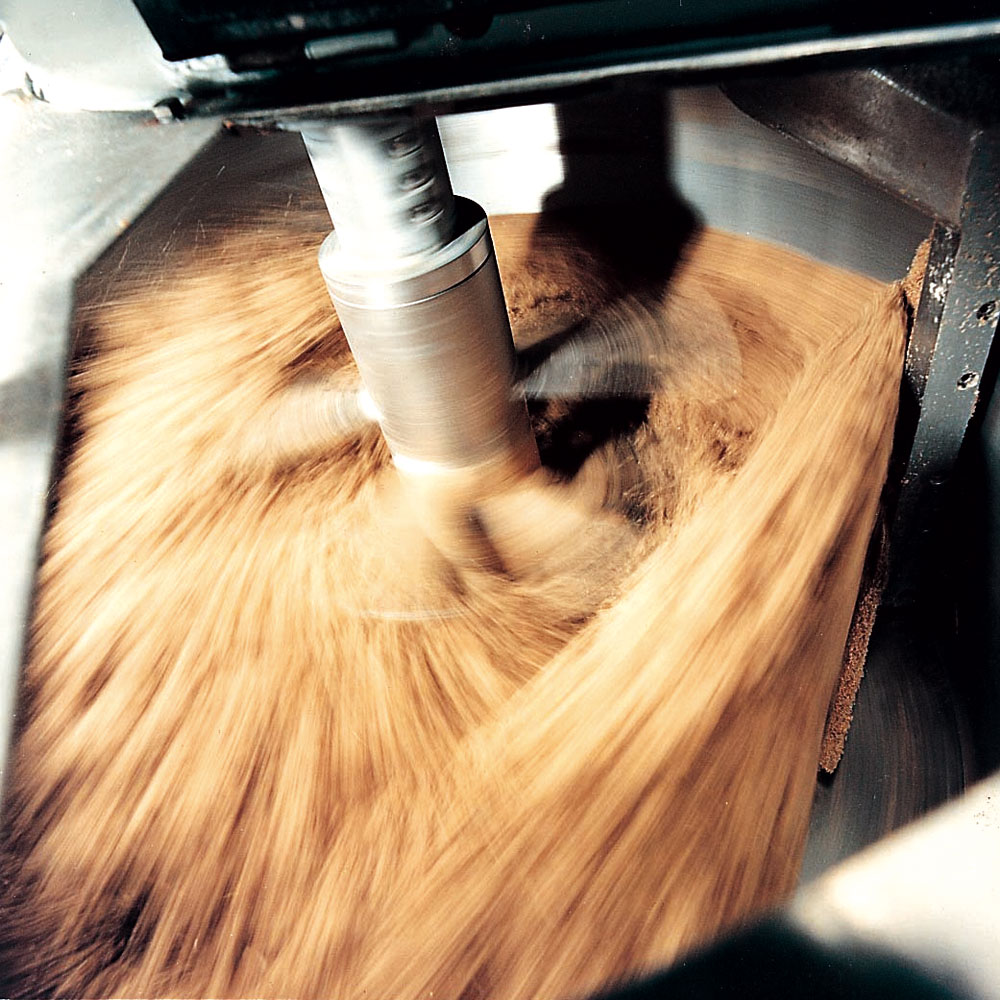
Allgaier Process Technology offer a new approach to this difficult process
A new approach to the ultra-fine screening of dry mineral powders is offered by Allgaier Process Technology GmbH, whose UK and Ireland agency has recently been awarded to Market Harborough-based Orthos (Engineering) Ltd.
The fine and ultra-fine screening (defined as the application of cut points in the range 30µm– 200µm) of powders, even when dry, is one of the most difficult tasks in the field of minerals processing. It is essential to achieve efficient recovery, at an economic throughput rate, of required products in the form of sharply defined fractions, as the products themselves are very often of high value and specification, and are widely used as constituents in pharmaceutical and cosmetic preparations, and as high-grade fillers in paints, plastics etc.
Difficulties arise, however, because the free aperture area of very fine meshes is a relatively low proportion of the whole mesh area, and because the powder particles are subject to adhesive surface forces, which cause them both to form loose agglomerates and to stick to the mesh surfaces. The unaided action of vibratory screens and low-frequency sifters is neither sufficient to shake the meshes free of a coating of powder, nor to break up the agglomerates efficiently. The results are a low throughput rate, a high degree of contamination of the coarser fraction or fractions with fine material, and inefficient product recovery.
Various screening aids have been devised in an attempt to deal with this problem. Of these, bouncing balls offer a method frequently used in the screening of fine powders in flat-deck vibratory screens, plan sifters and round tumbler screens. The balls are contained in a compartmented deck placed below the screen deck and impinge on the under surface of the mesh. This method helps to keep the mesh apertures clear but does little to break up the agglomerated material. Further disadvantages of this method are that damage to fragile mesh panels may occur, and material may be abraded from the balls, bringing about product contamination.
Other methods used in circular tumbler screens are:
- rotating perforated arms, which direct a flow of air at the underside of the screen mesh to dislodge trapped particles (this is coupled with air extraction from the lower section of the screen casing, and a filter system)
- rotating brushes placed beneath the screening surface
- a combination of the above two methods
- ultrasound.
The new approach to the ultra-fine screening of powders mentioned in the first paragraph introduces the idea of combining, in one machine, the two screening aids, air jets and ultrasound. This innovation, together with the tumbler screen features described below, leads to a much higher product yield without any loss of sharpness of fractionation. The air flows, which, because of the positioning of the air-extraction outlet, pass both up through the mesh and then back down, work to keep the mesh apertures clear, while the ultrasound, which can apply particle accelerations of up to 15,000g, breaks up agglomerates and also helps to keep the meshes free of powder build-up.
Recent screening tests carried out on various fine powders show that the two methods combined are much more effective than either on its own. The analysis of trial results in the case of a powder, in which the required product was a 0–63µm fraction, illustrate this. Using ultrasound only, the recovery of the 0–63µm fraction was 50.3% at a feed rate of 360kg/h; with air cleaning on its own product recovery was 58.3% at a feed rate of 277kg/h. The two used together, however, gave a product recovery of 83.8% at a feed rate of 515kg/h, and the product contained only 1% of misplaced material.
Circular tumbler screens are already widely used in the screening of minerals and other materials, not only in the ultra-fine range, but also in feed particle size ranges up to around 10mm. The feed is introduced centrally on to the top deck and, under the influence of the radial and tangential forces at play, follows a spiral path on the mesh. In the centre of the machine there is virtually no vertical vibration of the mesh, and the machine acts on the powder like a plan sifter and removes a proportion of the finer particles. As the radius of the spiral increases, however, the degree of vertical vibration becomes greater and more effective in the separation of the coarser particles, ie it affords the coarser material greater opportunity to reach the mesh surface. The spiral path followed by the feed material ensures that it is exposed to a long screening process within a machine occupying a relatively small area.
Allgaier machines are available in 11 diameter sizes ranging from 600mm to 2,900mm, as well as multi-deck and special configurations designed to deal with special screening requirements. Extra deck modules can be fitted easily to existing machines, and ultrasound cleaning can be installed without any problem in machines that are already equipped with air-cleaning.
In addition, Allgaier’s ‘MultiBalance’ drive system is reported to neutralize around 96–97% of all dynamic forces generated by a machine. It is adjustable and can, therefore, be matched to changes that affect the weight of the machine. Where several units are installed together, they can be switched in sequence such that small residual dynamic forces cancel each other out.
Orthos (Engineering) Ltd, No.2 The Point Business Park, Market Harborough, Leicestershire LE16 7QU; tel: (01858) 464246; fax: (01858) 434480