There’s More to Crusher Performance than TPH
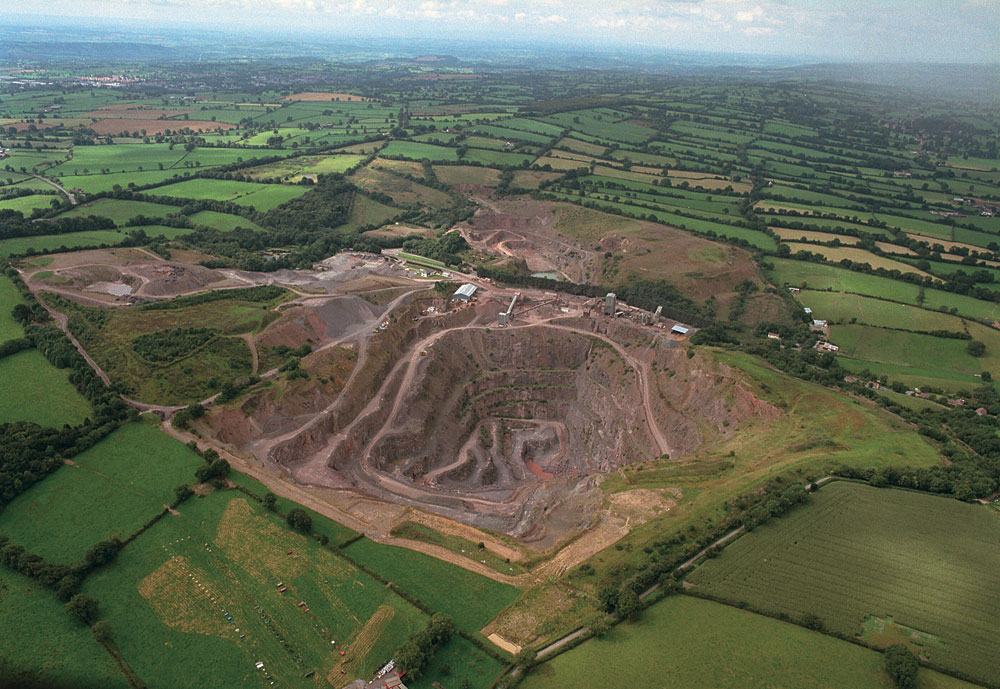
Final-stage crushing comparisons provide data for change
By Hugh Glandfield, Sandvik Mining and Construction Ltd
The following case study illustrates well two very significant aspects of crusher performance. First, the actual yield of final products in the crusher discharge compared to the throughput, and secondly, the effect of utilizing an automatic control system to maximize productivity while reacting under load.
John Wainwright & Co. Ltd are an independent quarrying company who have been trading since 1891. Their Moons Hill Quarry complex consists of three sites near Radstock in Somerset where they quarry a basalt hardstone unique to the region. The company place great emphasis on producing material, in particular for surface dressing, that has a flake index of less than 25%. This high-quality aggregate is supplied to Somerset and surrounding counties as far afield as West Sussex and Oxfordshire. The company also supply their own surfacing division, which was established in January 2001.
There are two material-processing operations at the quarry, one is a mobile plant and the other a fixed plant which is used for the production of chippings. The following case study relates to the operation of the fixed plant.
From the mid-1990s until Christmas 2001 primary, secondary, tertiary and quaternary crushing on the fixed plant were carried out as outlined in the following description.
‘Primary crushing is achieved by means of a single-toggle jaw crusher, fed from a vibrating primary grizzly screen separating at 75mm. Minus 75mm that passes through the vibrating primary grizzly feeder is screened at 28mm or 40mm depending on conditions, with the undersize producing scalpings. The oversize product is combined with the primary crushed material and fed directly to the primary stockpile. Generally, this produces a –200mm feed which is fed directly into the secondary crusher from this stockpile.
The secondary crusher comprises a standard cone crusher, operating at a nominal capacity of 325 tonnes/h with a close-side setting (CSS) of 60mm. The secondary product is fed, via a short conveyor, directly into the tertiary crusher — a short-head machine with an appropriate chamber. Historically, the capacity of the tertiary crusher has been sufficient to provide a feed to quaternary crushers 1 and 2 and a 36in Hydrocone (quaternary number 3). However, it has been recognized that, as and when the capacity of the plant is increased, the tertiary crusher will become a bottleneck, as the capacity of this machine is restricted to around 220 tonnes/h.
Crushed product from the tertiary crusher is conveyed to a selector screen that bypasses –6mm material direct to the final screens, with the oversize material (+6.3mm) being fed into a storage bin above the quaternary crushers. This material is then choke fed to the quaternaries via individual chutes with clamshell doors’.
Operation of the 36in Hydrocone, originally installed in 1989, was enhanced during the mid-1990s by the addition of a Sandvik ASR Plus computer control system. ASR (Automatic Setting Regulation) is a computer-controlled adaptive regulatory system that constantly monitors the motor power and Hydroset (hydraulic) pressure to maintain the required setting (CSS). By constantly monitoring these parameters, and adjusting them under load, the crusher is able to operate constantly at full load, thus producing consistent results and optimizing utilization.
When the ASR Plus was applied to the H36 Hydrocone, the crusher could be operated effectively and safely at tight settings of around 6–8mm. The production of 10mm and 6mm was optimized, without producing excessive quantities of oversize that would ultimately have to be re-crushed. Additionally, due to the control of the close-side setting, the crusher constantly produced high-quality, low flake index material.
Demand for aggregates produced at the site has been increasing steadily over a number of years. At the end of 2001, in view of the need for increased capacity to meet demand, Peter Barkwill, managing director of John Wainwright & Co. Ltd, formed a project team, which included the quarry manager and works engineer, to undertake a plant review looking particularly at final-stage crushing. Hugh Glandfield, Sandvik Rock Processing’s sales manager for central and southern England, ran a series of trials to determine the most effective use of existing plant and the most efficient plant configuration to achieve increased production. Results were extrapolated from belt samples taken and analysed by the quarry’s laboratory staff.
Quaternary number 1 has been retained only as an emergency back-up crusher, and due to its limited capacity its effect has not been included for the purposes of the following analysis.
During Christmas 2001, as part of a planned upgrade, the H36 Hydrocone was replaced by a Sandvik H3800 medium-fine (a renaming of the old Allis/Svedala H3000) together with a new ASR Plus computer control system. Installation time and cost were kept to a minimum because the operating height of the H3800 was less than the existing H36, thus avoiding costly mechanical modifications to the feed arrangement. Additionally, the H3800 fitted on to the existing H36 floating frame, once again saving time and expenditure.
A series of crusher tests was undertaken to compare efficiency and throughput of quaternary number 2 and the H3800. On the day of testing a particularly tough batch of material was being processed, resulting in the CSS of both machines being governed by maximum motor amps (power). The accompanying table shows the capacity of each of the quaternary crushers, both in terms of net production of the required sizes and also the amount of oversize produced by each arrangement. All results were achieved using maximum available motor power with ASR control of the H3800 and manual control of quaternary number 2.
In terms of increasing productivity, the results indicate that, at the settings achieved, the capacity of the H3800 is less than quaternary number 2. However, closer inspection of the test results reveals that the net production of both the 10mm x 6.3mm fraction and the 6.3mm x 3.35mm fraction is significantly greater –– 6.06 tonnes/h and 4.08 tonnes/h respectively. Further inspection also reveals that the quantity of ‘oversize’ (+10mm) from the H3800 is greatly reduced. The reduction in oversize generated by the H3800, when compared to quaternary number 2, is beneficial to the whole crushing circuit as any oversize returned in close circuit results in an immediate reduction of raw feed.
As an ongoing process of monitoring and controlling the process plant, John Wainwright & Co. Ltd have installed a computer control system that constantly measures the operational condition and status of all the fixed plant. This information can be viewed via various ‘windows’ and is available to both management and operators in either an instan-taneous or daily record format.
The graph shown in figure 1 has been extracted from the parameters measured by the control system and indicates the current (amps) loading of both quaternary crushers on a typical day from start-up at 5am until 4pm the same day. Both crushers operate with similar size motors and have the potential to achieve similar full-load amps. The H3800 is recorded on the grey line and quaternary number 2 on the green line. As stated previously, the H3800 is controlled with the ASR Plus and quaternary number 2 is manually controlled. The difference in motor loading is directly attributed to the ASR Plus and is reflected in greater reduction through the crusher.
In conclusion, effective control of any crushing circuit will ultimately produce more net product, reduce unintentional close-circuit recirculation and result in more cost-effective operation of the processing plant.
Following analysis and consideration of the above, Peter Barkwill commented: ‘The H3800 together with the ASR system has delivered on the need for increased yield in specified sizes. In particular, as we require all products to be less than 14mm for surface dressing, the ASR maximizes the production and quality of these fine fractions while affording the machine protection against feed variations. The system is so highly flexible that production changes can be accommodated at the touch of a button.’