The New Barmac VSI
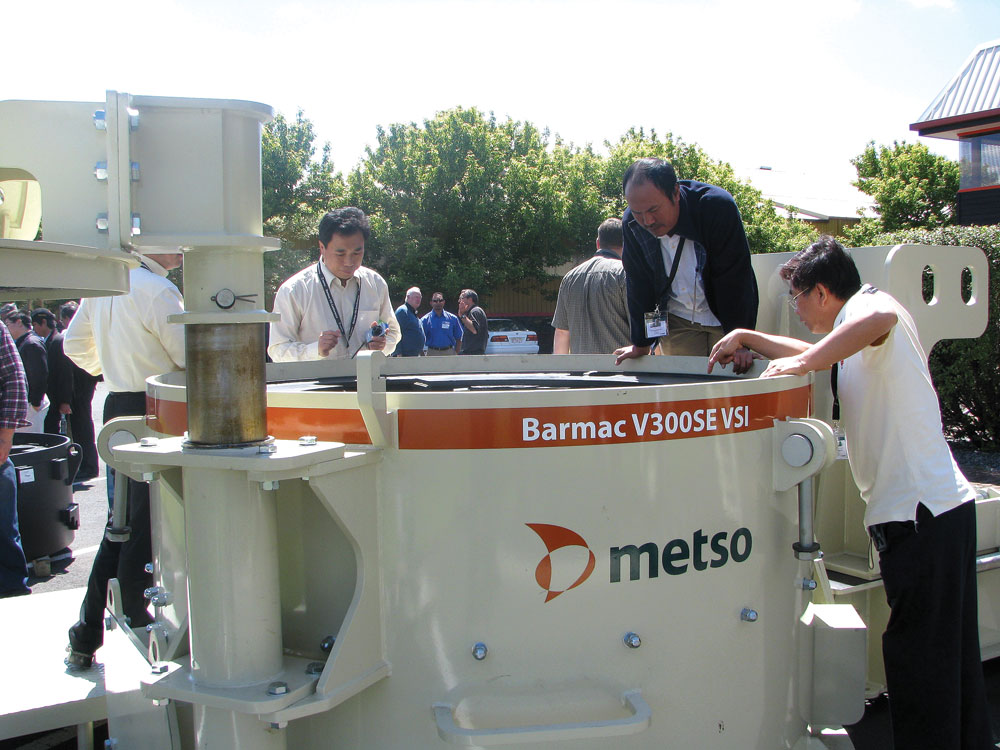
Metso Minerals hosted their traditional Barmac VSI conference in Matamata, New Zealand, from 10–13 November 2008. The event brought together 40 quarry professionals from 14 countries to learn more about the company’s latest-generation Barmac V-Series V300SE vertical-shaft impactor. Damian Christie reports
Since the 1990s, Barmac VSI crushers have become the mainstay of many quarrying operations globally. The Barmac B-Series VSI, in particular, has over 4,000 units operating in aggregate and mineral- processing installations around the world. The B-Series is considered unique because, unlike most other types of crusher that use metallic parts to crush rock, it uses the rock fed into the machine to crush itself, promising a higher-quality shaped aggregate.
The new Barmac V-Series V300SE VSI was on show for conference delegates at Metso Minerals’ Matamata factory. It has a total operating weight of 15,550kg, a single-drive configuration with maximum power of 260kW, and a throughput capacity range of 115–415 tonnes/h. Its rotor size is 950mm, it can operate between 1,100 and 1,800 rev/min and its maximum feed size is 125mm.
Available for both fixed plant and mobile applications, the V300SE features three rotor configurations: open rotor (table) and anvil, closed rotor and anvil and a closed rotor and rock-shelf option. The open rotor and anvil configuration is best suited to large-feed, low-abrasion and high-reduction applications, while the closed rotor and anvil configuration is best suited to reduction in fine-feed, low-abrasion applications. The closed rotor and rock-shelf option allows for greater flexibility in a single machine and offers the ability to handle fine abrasive feeds and produce excellent particle shape in coarse aggregate and manufactured sands.
Rock on rock vs rock on metal
While it is not a revolutionary departure from its predecessors in the B- and VI-Series, the V300SE is, according to Krish Amirthalingam, Metso Minerals’ global product manager for Barmac VSI, an important evolution, because it offers customers versatility over the traditional VSI machine, while incorporating many of the common features which have made the Barmac B-Series and V-Series so popular within the construction, mining and industrial minerals industries over many years.
‘In a closed rotor and anvil configuration, you can take a feed size up to 2.5in (60mm) and you will get high reduction with good product shape,’ explained Mr Amirthalingam. ‘In some applications, the customer may want to feed material larger than 2.5in, at which point you can use the open table rotor and you can feed material up to about 5in (125mm). The open table allows you to do that. So, feature for feature, in the closed rotor and anvil, how you apply it is very similar [to the B and VI-Series] except that the open table will allow you to have a bigger feed size.’
Mr Amirthalingam added that while a fixed-plant operator whose application dictated rock on rock from day one would probably use a B-Series VSI, the V300SE would be suitable for a contractor who moved from place to place.
‘A contractor moving from one site to another may prefer the versatility of the V-Series where he can have the rock-on-rock or the rock and anvil configuration on a single machine,’ he elaborated. ‘It may not be the most efficient configuration, but that’s not what a contractor is after. He wants to get the job done and so having versatility is a lot more important than the absolute efficiency of the machine.
‘We think the three rotor configurations in the V300SE will be very popular in the contractor market. When you move from one place to another, you don’t know what you are going to crush next and having one machine with three different configurations is almost like having three different machines, so it makes a lot of commercial sense.
‘The V300SE is going to be more popular for the mobile market because the contractor market is more mobile. You can have it on wheels or tracks, you can take it from one place to another and, based on the tasks and types of material to be crushed, you can decide which of the three configurations is the best to get the job done.’
According to Mr Amirthalingam, the V300SE could be easily adapted for a quarry operation, depending on the requirements of the customer, ie higher reduction versus higher-quality end-product shape. ‘If it is a very abrasive application, you would want to select the rock on rock function as your first choice rather than rock and anvil,’ he explained. ‘That’s just the nature of the crushing mechanism – rock on rock means less metal contact and, therefore, less wear. Rock on metal gives you higher reduction but rock on rock gives you superior product shape.
‘There are various requirements to consider,’ he added. ‘Typically, the abrasion index, the gradation and the end-product shape that the customer wants would be the major factors. Again, with high reduction, we are also saying that if the customer wants to produce more sand, you want as much reduction as possible. But, by the same token, if you want high reduction as well as excellent product shape, it is necessary to identify which configuration will best fulfil the customer’s requirement with the least operating cost. Sometimes, due to feed material characteristics, it is not possible to achieve both with one machine, at which point the customer has to weigh the importance of one requirement over the other, coupled with investment costs. If reduction is more important, the V-Series would be the obvious choice. If excellent product shape is required, then it would be the B-Series. If both reduction and excellent product shape are required, then perhaps both would be chosen. We have to evaluate all of these factors to find a happy medium.’
Improved safety and maintenance features
In developing the V300SE, Metso Minerals incorporated many of the safety and automation features of the Barmac B-Series VSI. ‘We’ve added the VSI Operational Control System (VOCS) and we’re able to automate the V-Series in a similar way to the B-Series,’ explained Mr Amirthalingam. ‘VOCS is standard on all V-Series machines.’
The V300SE also has an advanced safety interlock system on the inspection door and a roof lifter, allowing safe inspection and servicing of internal components. In addition, a pivoted motor mount allows for safe, ‘upright’ servicing of motor sheaves rather than having to work under the machine.
The working life of the V300SE prior to servicing and parts replacement is again dependent on its application. ‘It depends very much on how hard you are running the machine and how abrasive the material is,’ said Mr Amirthalingam. ‘V-Series machines in anvil configuration are meant more for non-abrasive applications, such as crushing limestone. Everything else being equal, non-abrasive material will cause less wear and tear. Each application is unique and each customer has different operating principles. Some customers will operate the crusher below its maximum capacity, while others will operate the machine to its fullest, both of which will have different operating costs. Hence, we work closely with customers on the application and operational requirements and then pinpoint the parts replacement and servicing interval.’
‘Another feature of the V-Series is its compact design, which makes it popular for mobile purposes, especially if there are installation and/or travel height restrictions. Also, the machine’s footprint is quite compact. We have standard platforms that are specifically designed for this machine, so customers don’t have to design their own from scratch. It can be skid-mounted or installed on a concrete foundation. For portable plants, it can be wheel or track mounted. It really is a very simple, easy-to-assemble machine.’
Exploring new market applications
The launch of the V300SE coincided with the beginning of the global financial downturn and, as a result, Metso have had to rethink their strategy for promoting the V300SE to a contracted and more cautious international market. Mr Amirthalingam conceded that releasing a new product right in the middle of a period of economic uncertainty was not ideal, but said he was confident Metso would be able to assess the mood of the market and promote the V300SE to customers accordingly. ‘Regardless of economic conditions, a solution must bring value to a customer and there are customer needs where the V-series will be the ideal solution,’ he said. ‘The V-series fits Metso’s extensive product line-up. We will be targeting applications where a lot of versatility is required, where the material is not very abrasive, and where high reduction is required with good-quality product shape.’
Mr Amirthalingam also forecasts that just as the Lokotrack LT7150 incorporates a Barmac VSI B7150SE VSI, a Lokotrack might in the future incorporate a V300SE. It is also possible that the V300SE could play a part in reprocessing and recycling applications. ‘For example, low-quality, low-priced crusher dust can be reprocessed into high-quality and profitable manufactured sand with minimum investment cost,’ he explained. ‘There may be an opportunity, with a very small investment, to turn something that is a waste material into a higher-value premium product.’
There is even the scope for the V300SE to follow its counterparts in the B-Series by diversifying into mining. At the Barmac conference, Gerhard Lenz, who specializes in technical and application support for Barmac VSIs in South America, outlined how the Barmac VSI is being employed as an alternative, cost-effective complement to grinding mills in mining operations to achieve greater operational cost savings and/or improved production. While this is not a traditional role for the VSI, Metso have found an innovative way of applying Barmacs as a cost-effective solution. The Barmac VSI can reduce the feed size to ball mills, thus improving mill capacity and, ultimately, the efficiency of the entire mineral-processing circuit. ‘We have had mining applications where customers have seen a five, 10 or even 20% improvement by using Barmac VSI pre-grinders,’ said Mr Amirthalingam.
He is also optimistic that the diversification of a machine built primarily for quarrying into mining will, in time, bring benefits back to quarrying. ‘Once you go into mining, you see the machine being applied in more intense operations, almost 24h a day, seven days a week. There’s a greater requirement for equipment with very long service intervals, more robust construction and extra-long-life wear components. We are now starting to see many quarries operating and meeting demand almost as intensively as mining operations. These quarries are requesting features that are traditionally requested by our mining customers. Therefore, we are incorporating mining-specific features into the machines that we sell in the aggregate market.’
Exploring sustainable opportunities
Metso are key solution providers in the recycling industry and they take into account core competencies and values related to their commitment towards the environment. Mr Amirthalingam believes that the V300SE VSI could play its own part in environmentally responsible solutions. ‘We are providing solutions to customers who are venturing into the recycling business to complement their quarry operations,’ he explained. ‘For example, it is quite remarkable how advanced glass recycling applications have become. Finely crushed bottle glass is being used for a variety of applications, such as sand-blasting, replacement sand in concrete, as an addition to floor and wall tiles, in blended bunker sand as well as in filtration media. Barmac VSIs are used to produce excellent shaped crushed glass particles that provide the consistent quality that these applications demand.
‘This is all quite fascinating for us at Metso,’ he concluded. ‘Glass recycling is not our traditional industry but it’s gradually becoming a crucial industry. We believe it is an environmentally sound industry that we can assist by providing technically and environmentally sound solutions.’
The Barmac V300SE is manufactured at Metso Minerals’ Matamata factory and exported globally.
Damian Christie attended the launch of the Barmac V300SE VSI in Matamata, New Zealand, courtesy of Metso Minerals (Matamata) Ltd. His article is reproduced by kind permission of Quarry magazine, the official journal of the Institute of Quarrying Australia.