The Benefits of High-Performance Screen Media
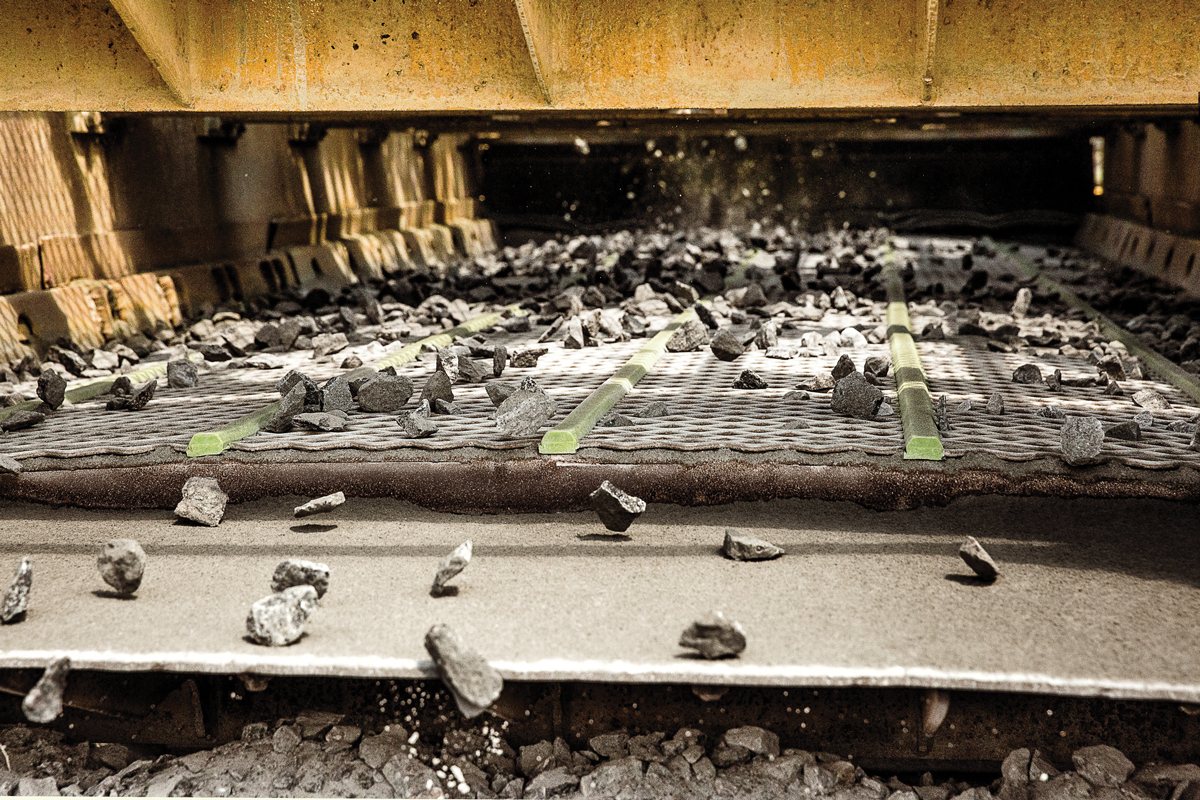
First published in the February 2020 issue of Quarry Management
Serge Raymond, manager of product technology at MAJOR, outlines how non-traditional media often improve wear life and product quality over woven wire
Choosing screen media for a screenbox is not as simple as it used to be. What once was just woven wire now includes a variety of alternative options, such as rubber, polyurethane, metal plates, high-vibration wire, combinations of different materials and more. With each type come countless new options for customizations of a screen deck to provide enhanced efficiency and throughput – whether by using one type of media or blending multiple types.
Standard woven wire is often the cheapest – at first sight – option, but that is no reason for these alternative options to be passed over without careful consideration. Depending on the application, these innovative products can improve wear life, reduce pegging and blinding, speed up the stratification process and better remove fines, thereby increasing the overall quality of the screened product.
The following are a few reasons to consider high-performance screen media.
Prolong wear life
Most types of specialized screen media offer a much longer wear life than traditional woven wire. Thick rubber and steel plate media clearly mean greater durability, but sometimes sacrifice open area. High-performance media is made up of highly engineered wires held together with polyurethane strips, which eliminate cross-wires with high wear spots that are common to woven wire and a few types of self-cleaning media. This results in optimal open area and a wear life as much as five times longer than wire alone.
Minimize screening issues
High-performance screen media can offer exceptional open area – in some cases 30% more than traditional woven wire and 50% more than traditional polyurethane and rubber panels. It is often a good solution for issues such as pegging, blinding or material contamination. Some media is tapered to help solve these problems, while others use unique designs to allow wires to vibrate independently from hook to hook under material contact. The result is high-frequency vibrations from the wires, in addition to the vibration from the screenbox. This virtually eliminates near-size pegging on the top decks and fine material blinding and clogging on the bottom decks. It also means less risk of material contamination and cleaner retained product through the middle decks.
Improved efficiency
Because screen machines are often placed at both the beginning and end of production, the right screen media can be key to the quality and volume of production. High-performance media can offer the necessary efficiency boost because some kinds accelerate stratification and increase material separation.
High-vibration wire screens operate at a high frequency to accelerate the stratification process. That frequency can be as high as 8,000 to 10,000 cycles per minute, as much as 13 times higher than the standard vibration of a screenbox. The increased screening action spreads material over the entire screen’s surface area on all decks. This moves the material faster, while maximizing contact to ensure optimal throughput with no carry-over. The result is a higher-quality end product.
This type of screen media can also be extremely effective in removing fines. The result can be less water required to wash material or, sometimes, a complete elimination of water use.
Using one particular type of screen media is not always the best option, but a better solution may not always be immediately obvious. Operators should consult with a dealer and manufacturer to determine the best type of media to solve screening problems and improve performance. The right solution could mean turning a screen that was a bottleneck into a profit-maker.
- Subscribe to Quarry Management, the monthly journal for the mineral products industry, to read articles before they appear on Agg-Net.com