Shake off Winter Woes
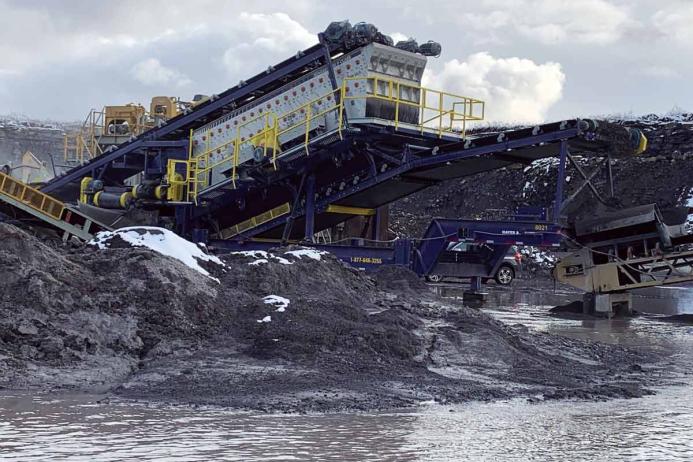
First published in the February 2024 issue of Quarry Management
Wilm Schulz, Haver & Boecker Niagara service manager, offers advice on caring for processing equipment through the winter
While vibrating screens are built for the harsh conditions in which they are used, there are best practices to ensure they continue to perform despite the season. Whether your plant shuts down for the winter or you continue to operate throughout, winterizing and preventative maintenance best practices will help ensure equipment longevity and maximum performance, in addition to making the most of any scheduled winter downtime. Not doing so could mean expensive breakdowns and repairs down the road.
Get winterizing
If you shut your plant down for the winter, as is the case for many operations in cold climates, proper winterizing is essential to a smooth and successful spring start-up. Operations should winterize equipment when temperatures are regularly below freezing.
The wash plant is the first place to start. Make sure to drain all of the water lines on the rinse screen to prevent freezing that could damage or burst pipes. Do the same thing with dedicated washing systems. Draining is usually as simple as allowing the water to flow out of the equipment, though crews can be more thorough by blowing out the lines and pump with dry air.
Next, flush vibrating screen lines with grease to remove contaminants from the bearings and slingers. Though it would be beneficial to cover a vibrating screen for the winter, it simply is not feasible for most operations. However, action should be taken to protect screen media from the elements and decrease the potential for rust and deterioration that could weaken the screen media. Move any extra screen media or components that may be on the ground nearby to a space out of the elements. The media could be covered with a tarp or placed in a storage container.
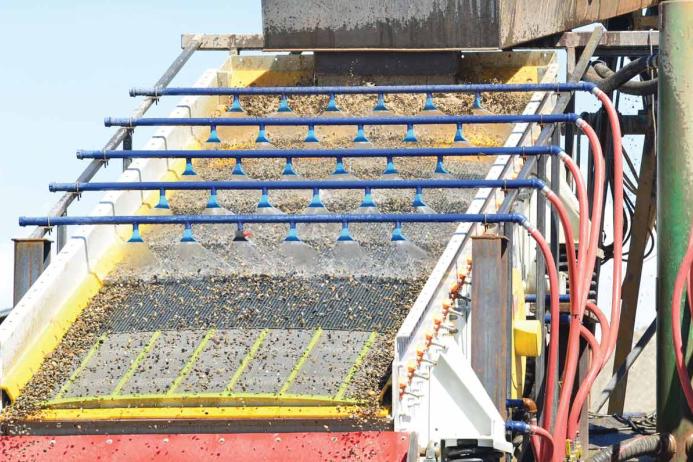
Best practices for operating during winter
Although vibrating screens do not require a lot of extra attention during the winter, a little TLC can go a long way. Just like with a car, operations should allow the equipment to run for about 10mins before use to warm up the system. If temperatures are below –10°C (14°F), standard grease should be replaced with a grease that can handle the lower digits, such as EP1.
Monitor and remove snow and ice build-up and clear the area around the screen before beginning for the day to maintain proper operation. Though unlikely, the weight of significant ice on the machine could affect the equipment’s balance and performance.
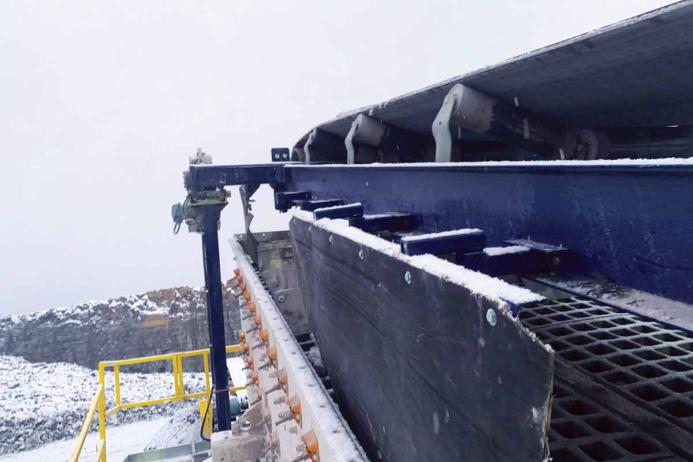
Making use of winter downtime
Whether it is regular scheduled downtime or the equipment is shut down for the season, winter is a great opportunity to fully inspect equipment, train workers, and make any changes that might improve performance and component longevity.
The best value is to partner with the equipment OEM for a service visit and inspection. As the manufacturer, they know what to look for and can give valuable insight on how to improve processes and increase productivity. OEMs often set up a regular servicing schedule where they visit the operation, evaluate equipment performance, and provide recommendations. Certain OEMs will perform the complete analysis all while the equipment is in operation, thereby increasing the operation’s uptime.
OEM-certified service technicians from some OEMs will start with a vibration analysis on the vibrating screen to look for problems easily missed by the human eye, such as a hairline crack in the side plate or twisting that will affect the machine’s longevity. These systems measure machine stroke and other vibration data to determine the equipment’s health. Abnormalities in the data can help pinpoint problems so that they can be addressed quickly to avoid downtime.
Work with the technician to check for any damage or otherwise visibly broken components on the vibrating screen. While the equipment is running listen for unusual noises, such as loose tension rails. Also, look for broken or excessively worn screen media. The screen media scrap pile can be a great place to identify common problems and diagnose how to fix them. For example, broken wires might indicate a need for a more durable media. Shiny hooks could indicate improper and loose installation, resulting in the screen media moving back and forth. Pegged or blinded media may mean a need for more open area, tapered openings or a different type of screen media.
Upon completion of the visual inspection, an OEM-certified service technician can often provide recommendations to improve machine performance and minimize unscheduled downtime. The recommendations could range from polyurethane liners for tension rails or cross beams to improve durability, to alternative screen media to address specific screening issues. They will also point out any parts or repairs needed.
It is also important to use components from the original equipment manufacturer. Though fabricated parts are cheaper, there is no way to guarantee they are built to the exact OEM specifications. A tension rail that is even a millimetre off can cause early screen media breakage and other component failures over time.
The off-season also provides a great opportunity to focus on inventory management and training. Talk to an OEM or certified dealer about refresher training on screen media installation and maintenance. Proper installation improves longevity and uptime and, therefore, increases profits.
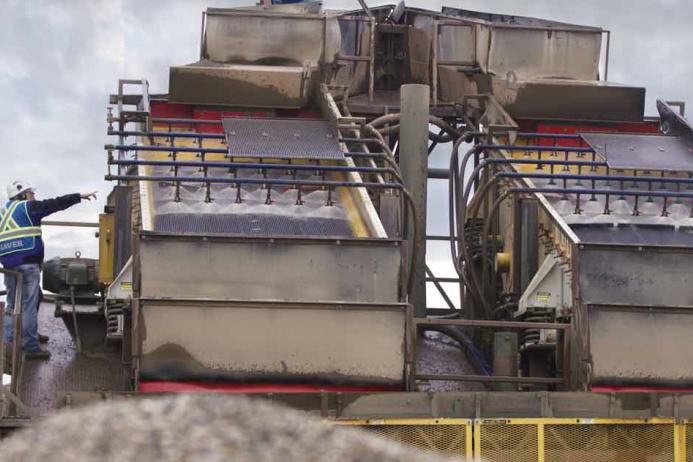
Stay proactive
The dead of winter is a tough time for both workers and equipment. Whether halting production for the year or trudging through the snowy season, maintenance and proper storage is critical for maximum performance over the winter and into the spring.
Talk to a trusted processing equipment manufacturer for best practices for winterizing and operating throughout the winter. Nothing beats having an expert look over the machines and taking the guesswork out of deciding what will allow the process to run at its maximum potential. The result could mean a productive winter and peace of mind.
Subscribe to Quarry Management, the monthly journal for the mineral products industry, to read articles before they appear on Agg-Net.com