Sandvik aid switch to mobiles for both Ennstone and Barr
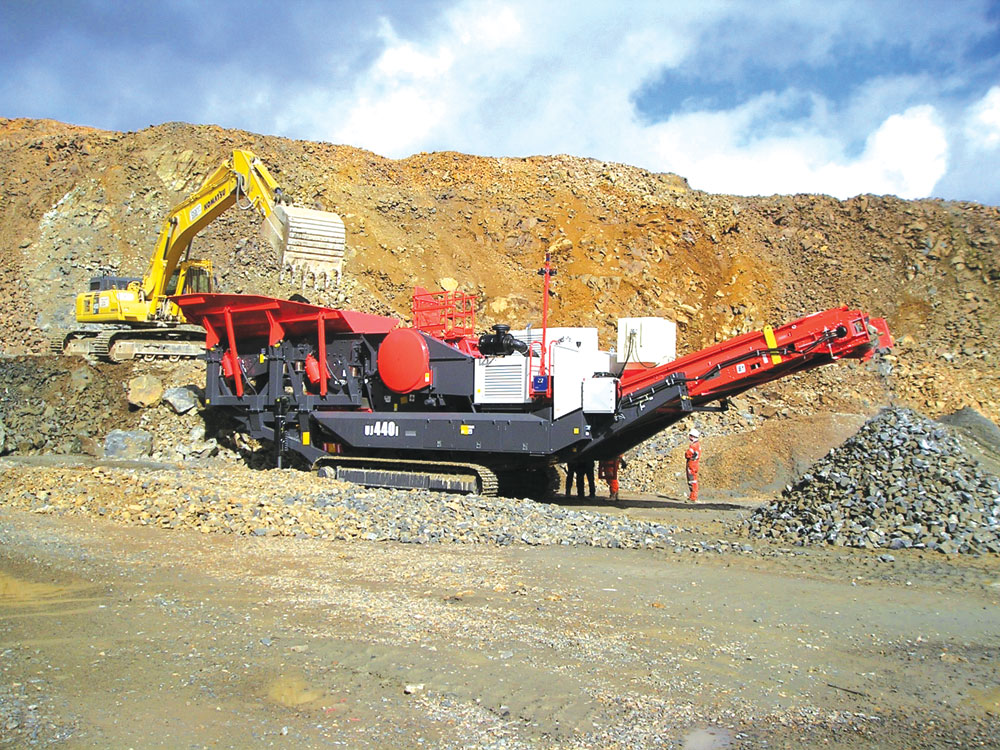
Ennstone Johnston are currently utilizing a pair of Sandvik track-mounted mobile crushers to upscale production at Leaton Quarry, near Telford. The two 43-tonne UH440i units, which feature Sandvik CH440 cone crushers specifically designed for hard rock applications, have proved to be more than a match for the hard, igneous olivine dolerite that is being extracted at the 52ha quarry.
Acquired as part of Ennstone’s purchase of Johnston Roadstone in 2004, Leaton is the only quarry supplying hard rock products to the Ennstone group in England. The site, which was opened in the 1920s and has some 7 million tonnes of reserves, currently supplies eight asphalt plants within the group.
Leaton Quarry’s main crushing plant utilizes a Svedala Superior crusher to reduce blasted material from 110mm down to 48mm, this feed going forward to two H200 hydrocone machines for further reduction. Oversize product is returned to an additional H200 hydrocone, to maximize the fines products. These units have been in place since 1984 and 1988, respectively, and have maintained an annual production of 350,000 tonnes.
However, when Johnston Roadstone were acquired by Ennstone, an increased production target of 750,000 tonnes per year was set to meet the group’s growing materials demands. ‘Having looked at the alternatives, we decided that mobile crushers were more suitable than a replacement static plant,’ said Western region production manager Kieren McCabe. ‘A static plant would have cost several million pounds but the mobiles are just a fraction of that cost. In addition, they afford us considerable operational flexibility, allowing us to follow the blasting pattern and reduce haulage costs.’
Mr McCabe added that the selection process was made easier by the company’s long history of running Svedala static plants. ‘The Svedala statics were extremely reliable, so the thought of dealing with the company behind the Svedala brand gave us some additional confidence,’ he said. ‘Sandvik also claimed that we could produce four different products with a single mobile machine, which would allow us to remove another crusher from the production process. Once they proved that, the choice was easy.’
The machines chosen were two Sandvik UH440i track-mounted mobile cone crushers: one being loaded with 95mm material for onward feeding to a pair of screens; the other acting as a secondary crusher to a primary jaw to produce a range of 6mm, 10mm, 14mm, 20mm and 32mm products.
Weighing 43 tonnes, the UH440i crushers are built around the proven and highly durable Sandvik CH440 cone crusher, which is designed to deliver an optimum combination of throughput and shape. The crusher is controlled by Sandvik’s patented Automatic Setting Regulation (ASRi) control, to give a smooth flow of material and high levels of productivity. The entire crushing process is continuously and automatically monitored by the intelligent control system, which provides the operator with valuable operational information.
‘From the moment we saw the UH440i machines, we really liked the build quality,’ said Mr McCabe. ‘In my opinion, they have the best build quality of any crusher I have seen to date. However, ease of operation is unquestionably their best feature. They have a huge program choice and the ability to change product size with no loss of production while the crusher is in operation. The control system gives the operator a lot of production modes that allow us to maintain an excellent product shape, even at maximum productivity.’
Although clearly enthusiastic about the ease of operation of the new crushers, it is their ability to produce a range of material grades that has really found favour with Mr McCabe. ‘The Sandvik machines are producing four different products to a very high quality at a rate of around 270 tonnes/h,’ he said. ‘This compares extremely favourably with the static primary jaw crusher, which was running at around 170 tonnes/h.’
Tincornhill Quarry
Meanwhile, in Scotland, Barr Ltd have recently purchased a UJ440i Trend primary jaw crusher and a UH440i tertiary cone crusher from Sandvik Mining & Construction for use at their Tincornhill Quarry operation, in East Ayrshire, as part of a process-improvement programme at the site.
With a unit output of 350,000 tonnes a year and an increased requirement for high-quality aggregate products from a reserve that contains gritstone and greywacke, the production team identified the two mobile crushing units as the best solution to replace two small fixed plants, improve the quality of the aggregates produced, increase the output and address issues contributed by the mineral.
The original requirement was to produce a consistently high-quality, low-flake and low-elongation –14mm material at a rate of 140 tonnes/h, for use in surfacing products on a runway resurfacing contract at Glasgow Prestwick Airport. Other outlets for the material would be in-house concrete and asphalt plants, thereby reducing the amount of material sourced from other units or outside the Barr Group.
A demonstration was set up in which Sandvik installed a Fintec 1080 mobile crusher fitted with a Sandvik CH430MF (H3800MF) cone crusher. This was fed with a –70mm +28mm material, which was subsequently screened into the required size fractions. Samples tested by Sandvik and Barr Ltd were found to be within the specification requirement set for the future production programme, making it an easy decision for Sandvik to accept and guarantee the conditions requested by Barr Ltd for the larger UH440i mobile tertiary cone crusher.
The standard UH44i unit is supplied with ASRi computer control, a dust collector, metal detector and rubber-lined feed hopper. Sandvik also agreed to supply an extended feed hopper to allow the mobile tertiary to be fed from the rear by a wheel loader. Quarry manager Brian McClelland has welcomed the new purchases and says he has found the ASRi control system, in particular, to be a benefit to him in maintaining the quality of aggregates on a daily basis.
Meanwhile, the primary section was required to produce 300 tonnes/h of material of an acceptable size to match the site’s existing secondary cone crusher. Owing to the high proportion of fines in certain areas of the blasted material, Barr opted for the UJ440i Trend primary jaw crusher, which incorporates a 1.2m x 4.1m live screen prior to the 1,200mm x 800mm Sandvik jaw crusher. This allows for efficient screening and discharge of the natural fines via a 7.3m side conveyor. Also fitted as standard is an automatic bearing-lubrication system, automatic hydraulic CSS setting, dust collector and rubber-lined feeder pan.
According to Barr Ltd, another major benefit of this purchase is the commonality of spares. Both mobile crusher units are fitted with Volvo TAD1252 Tier III engines, CANbus control systems, 1,400mm wide discharge belts and dry-dust collectors.