Productivity Climbing for Penhill
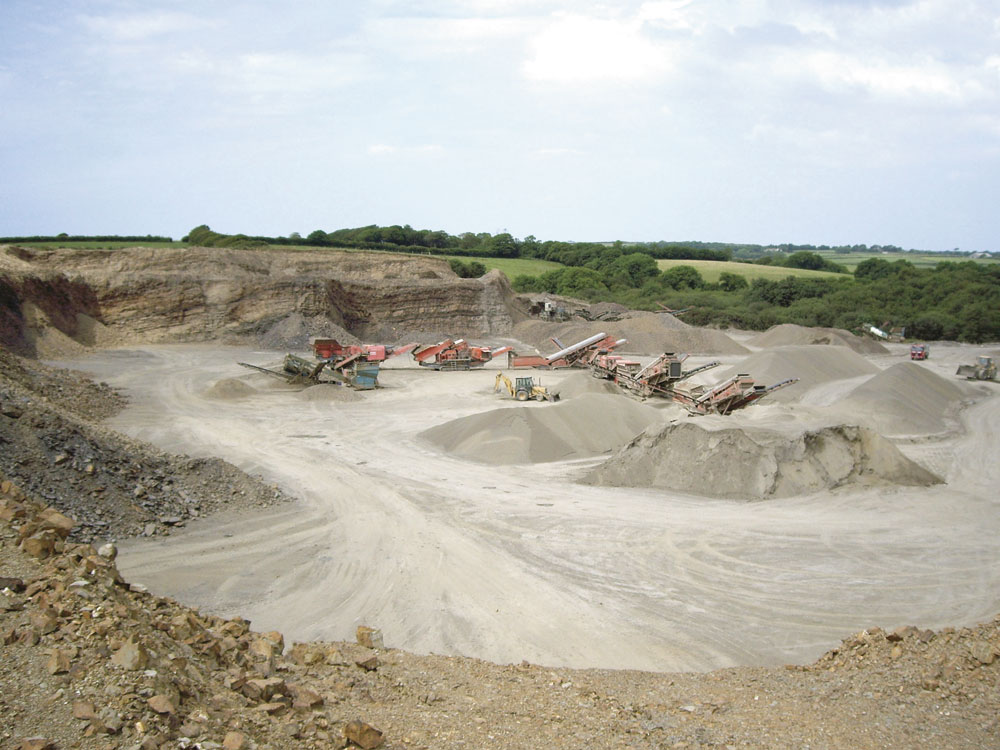
Terex Finlay boost production at Cornish quarry
Penhill Quarry and Haulage Ltd have purchased a third phase of equipment from Finlay Plant SW Ltd, aimed at delivering both increased production and a reduction in waste at their gritstone quarry in Cornwall.
High-PSV aggregate from Penhill Quarry and Haulage’s Pigsdon Quarry is particularly suitable for stone-mastic asphalt and road surfacing, although a high shale content within the aggregate requires meticulous processing in order to meet the required specification.
In 2006, brothers Roy and Jimmy Pengilley, owners of Penhill Quarry and Haulage, first approached Finlay Plant SW – part of the Finlay Group of companies – with the intention of purchasing a jaw crusher and a four-way-split screening plant to operate at the quarry face. They subsequently purchased a Terex Finlay J1175 jaw crusher and a Terex Finlay 694 Supertrak.
Several years earlier, the company had purchased a static secondary screening and crushing plant, consisting of three static screens and a Pegson 1000 Automax with a medium-coarse, long-throw specification, to process the aggregate. The introduction of the two Terex Finlay machines introduced further crushing and screening capabilities.
In 2008, Penhill Quarry and Haulage purchased a Terex Finlay C1540 cone crusher complete with integral pre-screen, again from Finlay Plant SW. The pre-screen eliminates the majority of fines from the product, allowing the crushing chamber to receive clean aggregate and increasing production by up to 20%.
The acquisition of the Terex Finlay C1540 also made it possible to primary crush the blasted aggregate at the face in conjunction with the Terex Finlay J1175 and Terex Finlay 694 Supertrak.
It was imperative to manage the aggregate through a three-stage crushing process (jaw–cone–cone), in order to reduce the shale content while keeping the flake content within the recommended specification. However, with the customer performing the first two stages at the quarry face, then having to transport all of the crushed and screened product across the quarry to the third processing stage, the process was proving laborious and costly.
As a result, Finlay Plant SW approached Penhill Quarry and offered a system that would further increase their production and reduce their waste considerably.
In order to increase the amount of ‘in spec’ aggregate and also reduce the quantity of dust produced, Terex Finlay devised a strategy which would marry the customer’s existing units, yet modify and totally change the production process, cutting the amount of waste produced and reducing downtime, with the entire crushing operation carried out at the quarry face.
After considerable consultation, Penhill Quarry and Haulage worked with Finlay Plant SW and Terex Finlay crushing experts on a specification for three new Terex Finlay units – another C1540, together with two Terex Finlay 693 Supertrak screens. The specification was also developed to maximize the potential of the equipment previously purchased.
Gareth Johnson, managing director of Finlay Plant SW, said: ‘The process is now complete and the entire system comprises the Terex Finlay J1175 jaw crusher complete with sensor on the head drum, which gauges the feed delivery to the existing Terex Finlay C1540 extra-coarse, long-throw machine.
‘Following this first cone crusher is the new Terex Finlay 693 Supertrak. This 20ft x 5ft three-way split screen features a 12mm top deck and a 5mm bottom deck. The largest of the three products is conveyed directly to the latest Terex Finlay C1540 medium-coarse, short-throw cone crusher.’
According to Terex Finlay, the short throw is beneficial in this situation as less dust and more aggregate is produced, which is well suited to the customer’s needs. Both C1540s are also hydrostatic, giving the added advantage of being able to slow the rev/min in order to improve shape, production or dust content.
‘Following this are two further screens, the Terex Finlay 694 Supertrak, which the customer purchased in 2006, and the other new Terex Finlay 693 Supertrak,’ continued Mr Johnson.
‘All these units all work in unison, with the vibrating feeder on the jaw crusher stopping automatically when a designated level is reached in the first cone crusher. The existing cone crusher has a self-regulating feature and these two units work well together, in turn keeping a constant, consistent and efficient feed flowing to the remaining plant.’
Penhill Quarry and Haulage are currently producing ‘in spec’ +20mm, 20mm, 14mm, 10mm, 6mm and dust at the quarry face and say the production of saleable aggregate has risen by 25%.
As well as delivering substantial economic and environmental improvements, the company also has the reassurance of a comprehensive service and spares offering from Finlay Plant SW to keep the entire operation running effectively, with just one point of contact for all their machinery.
‘Productivity at the quarry has certainly benefited from the introduction of the new machinery,’ concluded Roy Pengilley of Penhill Quarry and Haulage Ltd.