One Machine, Two Applications
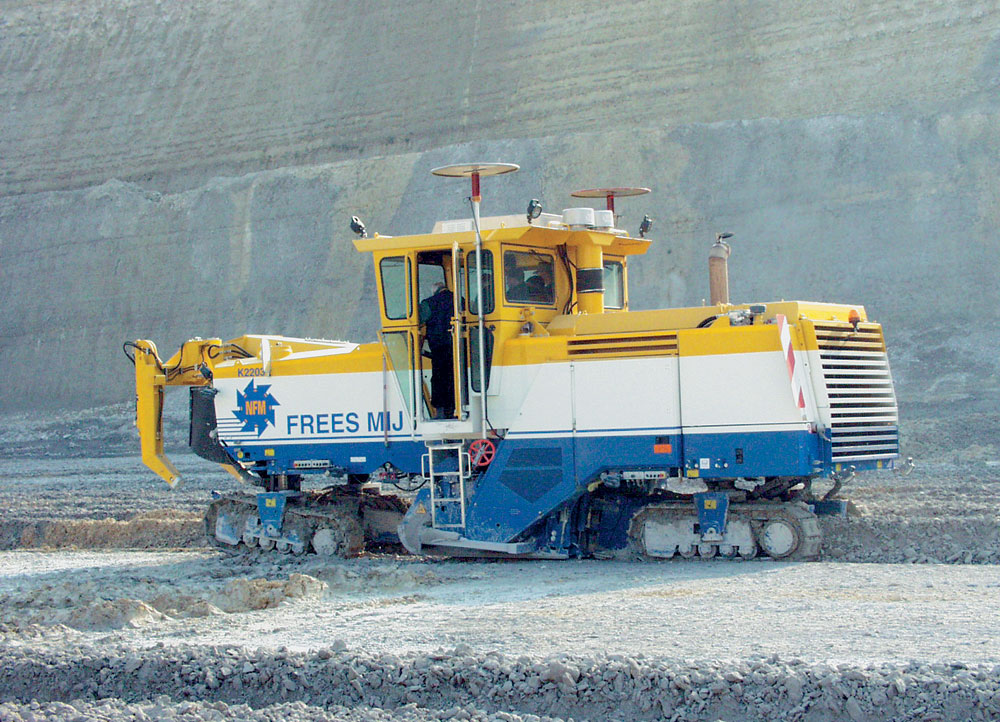
Dual role for a Wirtgen 2200SM surface miner
A surface miner is designed to operate in a mine or to cut required profiles in earthmoving, rock and road construction, whereas only a cold-milling machine is suitable for pavement milling.’ Essentially, this statement is correct, but it is one that is strongly refuted by German equipment manufacturers Wirtgen GmbH. This is because their ‘2200’ family of machines, in particular, is based on a large number of identical machine components which are used for both the 2200SM surface miner and the W2200 cold-milling machine, thereby allowing either of these machines to be used for two quite different applications with just a few relatively straightforward changes.
This dual functionality has already been demonstrated by the Dutch company NFM Frees MIJ, who rented their Wirtgen 2200SM to ENCI (Eerste Nederlandsche Cement Industrie) on a long-term contract basis. ENCI own a large limestone deposit on the outskirts of Maastricht, the upper section of which was previously worked using conventional methods. However, for over two years now the company has been working at a depth of around 30m below ground water level, exploiting the last remaining resources at the site using the 800hp 2200SM surface miner.
The raw material at this depth is so hard that an earlier attempt to use excavators for extraction purposes was abandoned after only a few days, and blasting below the ground water level is not permitted. However, these conditions proved ideal for the 2200SM, which, according to the site manager, not only saved on labour but also worked much faster and crushed the material more effectively, delivering average hourly outputs of between 250 and 300 tonnes/h. A further benefit of the surface miner was that it eliminated the need for any intermediate crushing at the site.
Conversion in one day
Despite the 2200SM and W2200’s largely identical design, it is not possible to put a surface miner to work on the road without first converting the machine, however the effort required to do this is within reasonable limits. The most important component when converting the machine is the cutting drum, as the cutting tools fitted to it are specially matched to the mining application. Here, the design of the individual tools plays an important role, as do the toolholders, the spacing of the tools and their setting angle.
Exchanging the cutting drum for a milling drum is greatly facilitated by the machine’s hydraulic height adjustment — the cutting drum is simply lowered on to a mounting trolley located beneath the machine, allowing it to be easily pulled out once the connections have been unscrewed, the pulley housing removed, the three power bands unhinged and the pulley dismounted. The milling drum is then pushed underneath the chassis and fitted in reverse order.
The conversion operation is largely complete once the hydraulic hoses and water supply lines have been connected and the protective housing and the V-belt pulley have been fitted. And due to then good accessibility of the individual components, the time needed to carry out the changeover is kept to a minimum.
Mounting the discharge conveyor (in the quarry the machine creates windrows without the use of a conveyor) and exchanging the air-conditioned operator’s cabin for a simple canopy (if necessary) can be completed quickly using standard workshop equipment. In the quarry the machine’s crawler tracks are padded with robust steel double-grouser pads, but these can easily be replaced with crawler tracks featuring heavy-duty polyurethane track pads for operation on the road.
When comparing the technical specifications of the 2200SM and the W2200, the difference in their operating weight, in particular, is noticeable. With full tanks the 51-tonne 2200SM weighs exactly 4 tonnes more than the cold-milling machine. For mining operations, this extra weight is essential to be able to achieve high cutting performances and to ensure that the machine runs smoothly in medium-to-hard material. Generally, however, this increased weight is not required when working on the roads, although in certain conditions it can have a positive effect on the milling performance.
On the road
After two years working in ENCI’s lime-stone quarry, NFM Frees’ 2200SM surface miner was equipped with a standard 2.2m wide milling drum and W6 type cutting tools and put to work on a Dutch cross-town road in the vicinity of Breda. Here, the machine works at a milling depth of between 15cm and 20cm, and only the additional weights and the protective steel plates bolted to the sides of the crawler tracks reveal that the unit is also suitable for arduous work in a quarry. Like any other Wirtgen road-milling machine, the adapted 2200SM loads the milled material on to waiting trucks via a wide loading conveyor.
Because of its dual application, NFM Frees say the machine’s utilization rate has been improved and idle times reduced, thereby improving its overall efficiency. This concept has not only convinced users in Europe, but has also been adopted in Japan and Algeria. So far some six 2200SM’s and W2200’s have left the Wirtgen factory in Windhagen equipped with the respective installation equipment to allow both the mining of raw materials and cold-milling operations on the roads.
Wirtgen GmbH, Hohner Str. 2, 53578 Windhagen, Germany; tel: +49 2645 1310; fax: +49 2645 131 499; email: marketing@wirtgen.de; website: www.wirtgen.de