New ‘Ventura’ Dryer From Ventilex
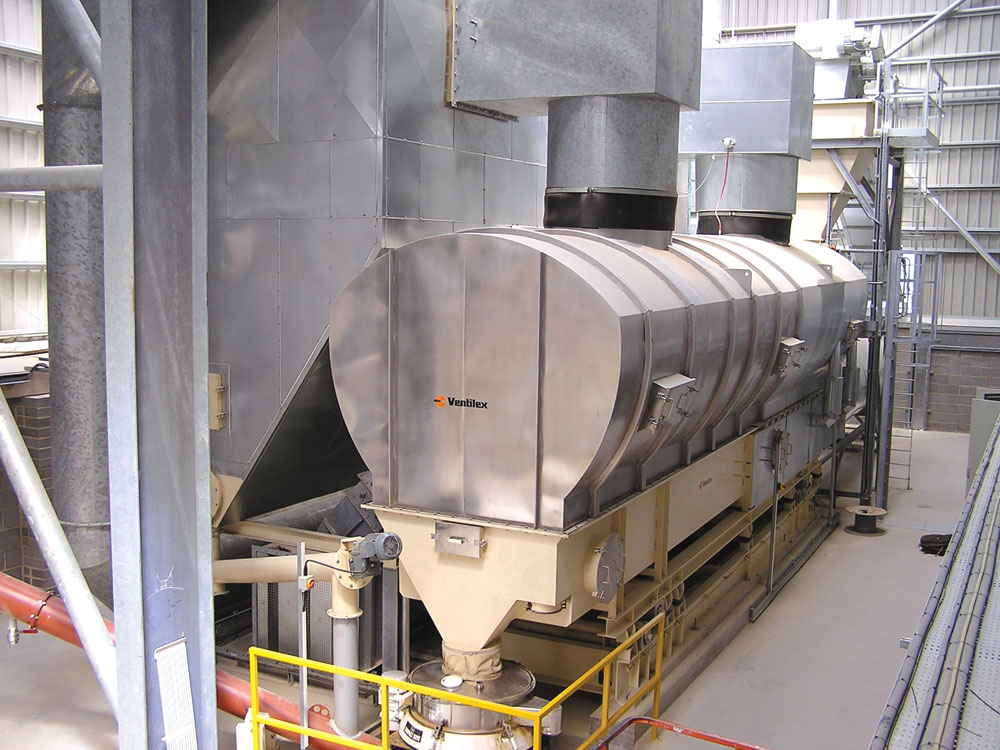
The Dutch company, Ventilex, known internationally for their high-efficiency, continuous fluid-bed dryers, have recently introduced a new version, the Ventura two-stage drying system. This new design is said to offer greater thermal efficiencies than the best achieved by previous designs of Ventilex dryer, which, as has been reported previously, can deliver fuel savings of 30–40% in the drying of sand and other minerals compared with the performance of a typical rotary drum dryer.
The table below shows fuel-consumption figures for a typical rotary drum dryer, fluid-bed dryers with and without evaporative cooling, and the new Ventura dryer.
The extra fuel saving achieved by the Ventura compared with the best result previously obtained with a Ventilex dryer is around 25%. A like-for-like comparison of the performance of a typical rotary drum dryer with that of the Ventura shows that the latter consumes about 40% of the fuel needed by the rotary drum. This result is obtained by recovering and reusing almost all of the latent heat of evaporation involved in the first stage of the drying process.
The Ventura dryer is split into two sections, the first of which operates at a high temperature (up to 500°C). The exhaust air in this section is recirculated in a loop, which is fed with a relatively small volume of fresh air supplied by the combustion air fan. A volume of air, saturated with moisture and equal to the amount fed in, is taken from this loop and passed through a water/air heat exchanger.
Here, the moisture is condensed and almost all of its latent heat is transferred to the flow of cooling water. The hot water produced by the heat exchanger is passed through a second heat exchanger, where it heats up a supply of ambient air, which is further heated by a small burner and a gas-to-gas heat exchanger to allow the system to cope with changes in the feed, and to limit the size of the dryer.
This flow of air is then used as the drying agent in the second stage of the dryer, where the product is heated up to a controlled temperature of not more than 40°C. In the case of sand and most other granular minerals cooling is, therefore, not necessary. It is possible to use the small amount of residual heat left in the second-stage water loop to heat the exhaust air in order to eliminate any visible steam exhaust plume. This is effective in all except extreme weather conditions, such as fog and temperatures below 5°C combined with a relative humidity greater than 95%. Particulate emissions are guaranteed not to exceed 10mg/Nm3.
All Ventilex dryers, including the Ventura, are mounted on inflated rubber bellows. Product transport is achieved not by vibration but by means of a relatively low-frequency eccentric cam mechanism, which induces a motion with a high vertical lift component. This produces the Ventilex sub-fluidization effect, which contributes substantially to the reduction in energy requirements. The Ventura, and other dryers in the Ventilex range, could not function as they do without a highly sophisticated control system, the software for which has been developed entirely in house by Ventilex.