New-generation Screening Systems From Powerscreen
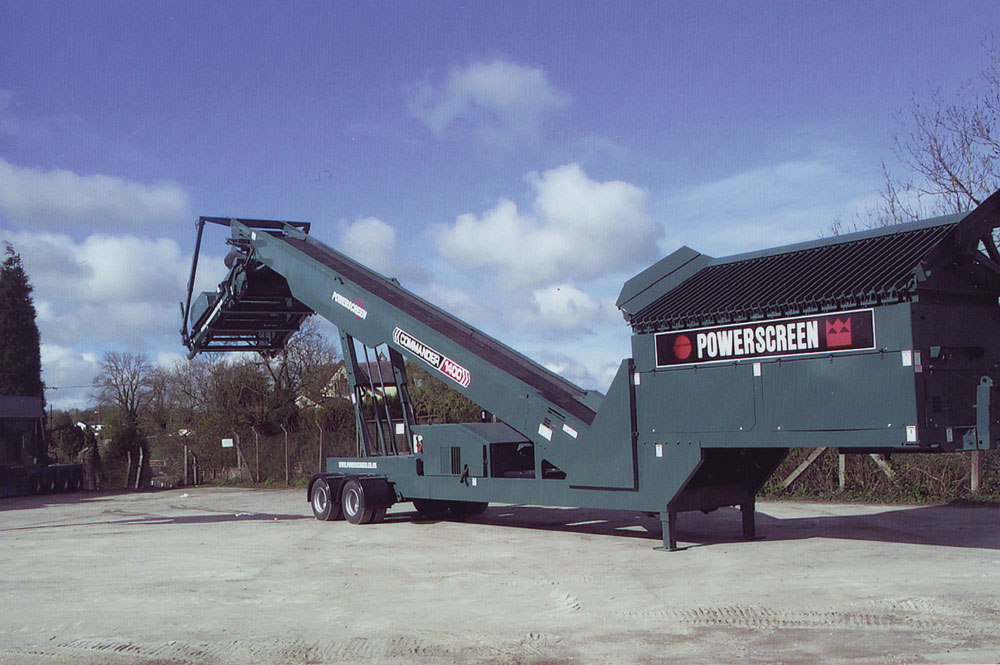
New equipment for dry and wet screening applications
Dungannon-based Powerscreen International Distribution recently unveiled to the press a range of new equipment for dry and wet screening applications. These latest machines form part of a wider raft of equipment launches which herald what the company says is ‘a move towards a new generation of plant for screening, washing and recycling’. While some of this equipment represents the development of earlier successful models, much of it is completely new and all of it is designed to work in tandem with existing Powerscreen products. For screening applications, the new products comprise the Commander 1400 mobile screening unit, the tracked Warrior 1400 and Warrior 1800 three-way-split screening and stockpiling units, and the new 20 x 6 two- or three-deck static screen.
Commander 1400
In a rationalization of their successful Commander series of washing and screening units, Powerscreen have developed the new Commander 1400 which, with its wide range of features, optional processors and configurations, replaces the entire Commander range with a single, highly versatile unit that combines all the proven benefits and performance characteristics of the previous models. Designed for rapid set-up in around 15min and capable of a high output of up to 500 tonnes/h (depending on mesh size and material type), typical applications include sand and gravel washing and processing, coal and crushed stone treatment and the recycling of construction and demolition waste, where a single product is the end requirement.
The new machine features a 6.3m3 feed hopper and an adjustable-angle tipping grid with radio-controlled double-acting tipping rams and self-cleaning grid bars. The dry-screen unit has a rugged, huck-bolted, double-deck, four-bearing screen box with a free-floating vibration system to eliminate the need for ‘fine tuning’. The rinser unit is similarly constructed and available in two double-deck screen-box sizes featuring side-tensioned mesh and six spray bars to both the top and bottom decks. An optional three-deck 10 x 5 rinser is also available.
The machine’s main feed conveyor has a planetary gearbox drive, hydraulic variable-speed control and is fully skirted and sealed to prevent spillage. The standard power unit is a Deutz diesel engine which develops 72kW at 2,200 rev/min, although an electric/hydraulic drive option is also offered with two motors, each developing 22kW, and a separate screen motor which produces 7.5kW output. All pumps and motors are rugged, high-performance units from renowned manufacturers such as Danfoss, David Brown and Commercial Hydraulics.
Warrior 1400
Another machine which will be making its official debut during this year’s busy ‘exhibition season’ is the highly mobile Warrior 1400, a new, high-capacity, heavy-duty unit capable of screening, three-way splitting and stockpiling a wide variety of materials in difficult and demanding applications, including face blasted material and crushed stone, coal, and construction and demolition debris. Despite its compact size, in optimum conditions the machine offers a potential output of up to 400 tonnes/h.
Weighing around 25 tonnes, the Warrior 1400 is mounted on rugged, low-ground-pressure tracks and fitted with a highly aggressive, heavy-duty, two-bearing screenbox which is able to operate with finger screens, woven mesh and punch plate on the top and bottom decks (the top deck can also operate with Bofor bar). Screen angles are hydraulically adjustable and the bottom deck features a speedharp or self-cleaning ball-deck system. The bottom screens can be easily accessed for changing or maintenance.
The machine has a large-capacity feed hopper with Hardox steel sides and a hydraulically folding rear door to accommodate direct feed from a crusher working in tandem. The variable-speed inclined feeder belt is equipped with impact bars and discharges on to the screenbox from above to prevent bridging.
All the stockpiling conveyors on the Warrior 1400 are oversized, hydraulically folding and angle adjustable. The mid-size material falls directly on to the mid-product conveyor, which also features a special ‘slide-up’ system that allows easy access to the bottom deck meshes for cleaning, overhaul or replacement.
Optional extras on the Warrior 1400 include an apron feeder belt, a Cat engine and a Hardox-lined screenbox.
Warrior 1800
With an operating weight of around 30 tonnes, the new top-of-the-range Warrior 1800 screening and stockpiling machine offers an output of up to 500 tonnes/h and features many similar attributes to its smaller stablemate described above. With an equally quick set-up time of 15min, the Warrior 1800 is designed for large-volume, heavy-duty tasks and features a 10mm stroke, two-bearing screenbox and a large hopper with hydraulically folding sides and an enlarged 1.2m wide hopper exit to allow the screening of larger items.
The fines and mid-product conveyors are hydraulically folding and angle adjustable, while the oversize conveyor features variable-speed control and is also angle adjustable with a ‘slide-up’ system for quick and easy access to the bottom-deck meshes.
A number of optional extras are also available on the Warrior 1800 including: a heavy-duty Hardox apron feeder instead of a belt feeder; Hardox or mild steel punch-plate screens; finger screens on the top or bottom decks; and ‘Z’ meshes complete with ball deck and self-cleaning system.
20 x 6 static screen
Meanwhile, on the static screening side, Powerscreen say their latest piece of equipment is versatile enough to stand alone as a static screener or to form an integral part of a washing plant. Of modular construction, the 20 x 6 static screen is available in a two- or three-deck configuration with 11.15m2 of screen area per deck and a 6.0m x 1.8m two-bearing screenbox which is huck-bolt fastened for added strength. Side-tensioned screens produce uniform material flow and the meshes are fully interchangeable. Uniform material washing throughout each deck is via 18 or 28 spray bars on the two- and three-deck versions respectively.
For ease of maintenance and extended life, the 20 x 6 static screen has a rolling chute system to provide easy access to the middle and bottom decks. Automatic greasing allows simple and quick bearing lubrication for trouble-free running, while the catch box has a fully sealed rubber lining which eliminates wear. In addition, all walkways and handrails are fully galvanized.
Optional extras on the 20 x 6 static screen include: hydraulic screen angle adjustment; a rubber-lined transfer box; adjustable and rubber-lined division plates; hydraulic drive; and brass or plastic nozzles.