New Aggregate Drying Facility At Eaton Hall
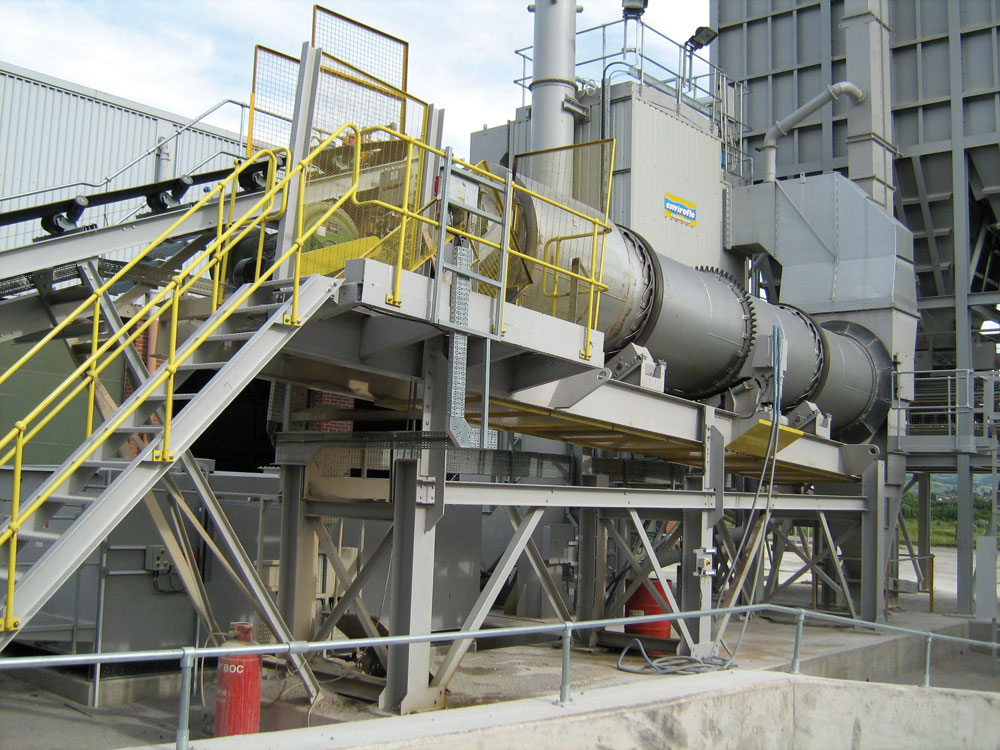
BG Europa of Wickhambrook have recently been involved in a project at Eaton Hall Quarry, near Congleton, Cheshire. Owned and operated by Tarmac Aggregate Products, the quarry supplies sand to the Trupak bagged aggregate business, which has one of its 18 bagging plants located within the Eaton Hall site, supplying dry mixed cementitious products to the DIY and builders merchants’ markets. Annual output from the Trupak site is approximately 50,000 tonnes per annum, with the products being sold and distributed in 15–25kg plastic bags to customers across the UK.
Having made the decision to upgrade the site, Trupak have recently commissioned a new bagging plant, supplied and installed by main project contractors GT Project Engineering of Consett. As part of the material-handling equipment specification within the project, BG Europa supplied an SD1.5 drying drum to Enviroflo Engineering of Wolverhampton.
The SD1.5 is a parallel-flow drum designed primarily for low-temperature drying. Widely used within the sand, slag and mineral drying industries in the UK and Europe, the parallel-flow design ensures that the material discharge temperature is close to that of the exhaust gases, achieving material temperatures just above dew point.
To facilitate drying of the aggregates before delivery to the bagging plant, the 1.5m diameter x 9.0m long dryer was specified to dry 14–6mm and 5–1mm aggregate blends with 1.2–2.6% and 5.3% moisture removal, respectively, at a rate of 45 tonnes/h, and also top dressing with 8% moisture removal at 30 tonnes/h. The energy requirement for 1.2 % moisture removal at 45 tonnes/h was calculated at 3.6 MBtu/h (8.2 MBtu/h for 8% moisture removal at 30 tonnes/h). Material discharge temperature is set at between 85–100°C.
To achieve this capacity with the flexibility in output required, BG Europa also supplied an American Hauck Starjet SJ075 burner rated at a maximum 12.1 MBtu/h with a 7:1 turndown. This was supplied with heat shield, oil control valves, modulating control motor with external high/low fire limit switches and oil line shut-off solenoid valves, oil filtering and pressure-regulating equipment.
The burner control was supplied to regulate the drying of the material to a predetermined discharge temperature via a Land RT80A. To complete the specification an electrical control panel was supplied to IP65 standard and a burner maintenance platform with handrails and access stairway was provided to one side of the drum chassis.
Mounted on a heavy steel base frame, the drum has a discharge height of 1m and trunnion rings are fitted to the drum shell to allow for expansion. Fully supported by four roller stools, the Barber Greene (BG) design ensures that the trunnion roller assemblies have full face contact with the trunnion rings at all times. Internal taper roller bearings lock all thrust forces into the roller assembly. In comparison with a plummer block bearing, the BG design ensures that the forces exerted by the tracking of the drum are not transferred to the inner race of the support bearings, thereby eliminating any movement on the shaft.
An exhaust stack base and knock-out box complete with lined discharge chute were also supplied by BG Europa to feed a BG hot elevator (supplied under separate contract to GT Project Engineering). Designed to handle 14–6mm and 5–1mm aggregate blends at 55 tonnes/h and top dressing at 35 tonnes/h, the elevator features bolt-on removable panels to the rear of the head and tail sections, allowing access to the head and tail sprockets.
Fabricated from mild steel, each individual bucket features a flat bar reinforced lip on the front for extra wear and stiffness. Elevator drive is supplied by a motor with belt drive to a torque-arm shaft-mounted reducer complete with back-stop. The elevator was also supplied with a secondary inlet chute to accept bag filter dust, as well as a discharge chute with removable covers to allow access to the ABRO wear-resistant steel liners.
Trupak director Cliff Ogden commented: ‘The dryer was installed on time and is now fully operational supplying dried aggregates to match our customers’ demands for bagged cementitious products. We are very pleased with both the installation project and the current performance of the equipment.’
BG Europa (UK) Ltd, Pipers Drove, Giffords Road, Wickhambrook, Newmarket, Suffolk CB8 8PQ; tel: (01440) 821155; fax: (01440) 821156; email: sales@bgeuropa.co.uk