Moisture Reduction Success at Eaton Hall
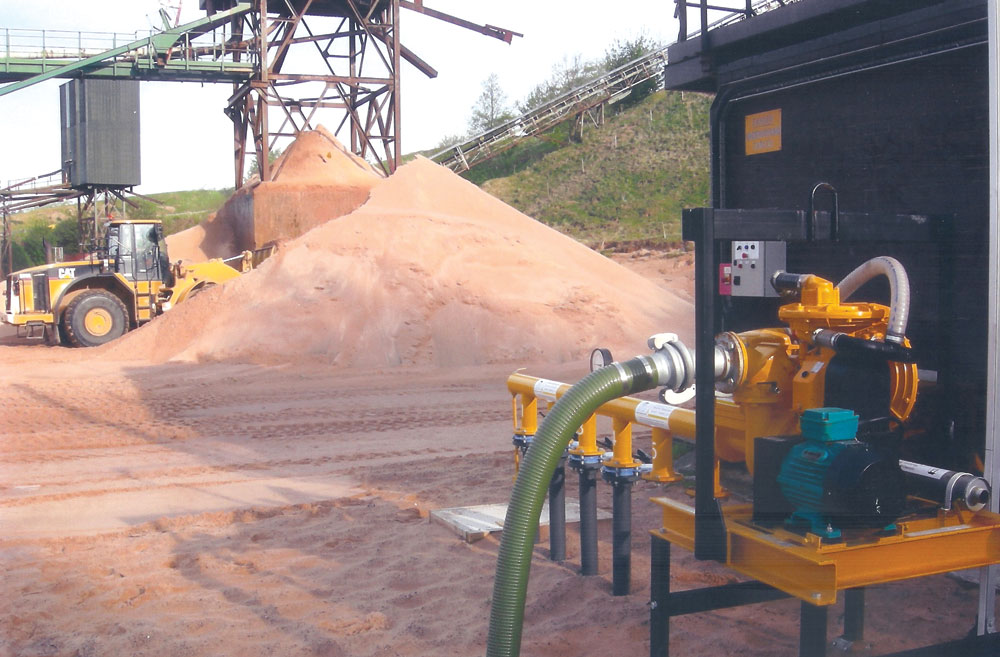
Tarmac install sand-drying system to help improve business efficiency
As part of a recent business efficiency exercise, Tarmac Ltd engaged the services of specialist materials drying and pumping company Moisture Reduction Systems Ltd (MRS) to install a sand drying system at Eaton Hall Quarry, near Congleton, Cheshire.
Following several pre-planning meetings with MRS, and acting upon their free drawdown pumping test data, Tarmac’s management team concluded that it would be beneficial to have an MRS vacuum-assisted accelerated moisture reduction system installed beneath the coarse and fine silica sand stockpiles, as these materials were having to spend a considerable amount of time in the site’s fluid-bed dryer following a period of gravity drainage.
An additional benefit would be an improvement in materials handling at the site, as the dewatering installation would also remove the large residue of washing water present at the base of the stockpiles.
The final design methodology agreed upon involved installing a 7.5kW, three-phase, twin-prime, large air handling 100mm Selwood moisture reduction pump, coupled to a six take-off manifold (only four take-offs were required in phase one of the site improvement, the other two being available for further system extension at a later date).
Correspondingly, underground vacuum/water conveying pipelines were laid from the manifold to each of the four cyclone-fed stockpiles. These were interconnected to non-deteriorating geotextile filter-wrapped perforated drainage pipe, with sufficient percentage open area to suit the established(K) = 10-4m/s permeability values of the silica sands. This was derived from D10 particle size sieve analysis and falling-head testing information calculated by MRS following the initial drawdown pumping test assessments.
As part of the installation, an impervious membrane was installed to exclude any upward or horizontal recharge of ground water, while at the same time containing the upper perched water from the stockpiles, which was required for reuse to help reduce ongoing wash water consumption costs.
To ensure longevity of the system and to prevent any migration of fines in the subsequent flow paths, an appropriately sized gravel filter media was placed above the perforated abstraction pipe to act as a drainage blanket/filter pack, to prevent any silting up from occurring.
According to MRS, the benefits being realized by Tarmac, and other sand processors who have had similar patented moisture-reduction systems installed, include:
- greater fuel efficiency by eliminating the need for forced drying
- drier product in a shorter period of time than gravity drainage and, therefore, an improvement in production/turnaround times
- improved handling for front-end loaders
- no pollution of surrounding water bodies
- no stockpile slumping, resulting in safer working conditions
- no frozen stockpiles in winter months
- in some cases, same-day loading direct from stockpile due to the accelerated drawdown effect
- reuse of clean abstraction water to meet washing and/or other on-site water requirements
- elimination of double handling from one stockpile to another, particularly beneficial at sites with limited storage space.