Maximizing Productivity At Naylor Hill Quarry
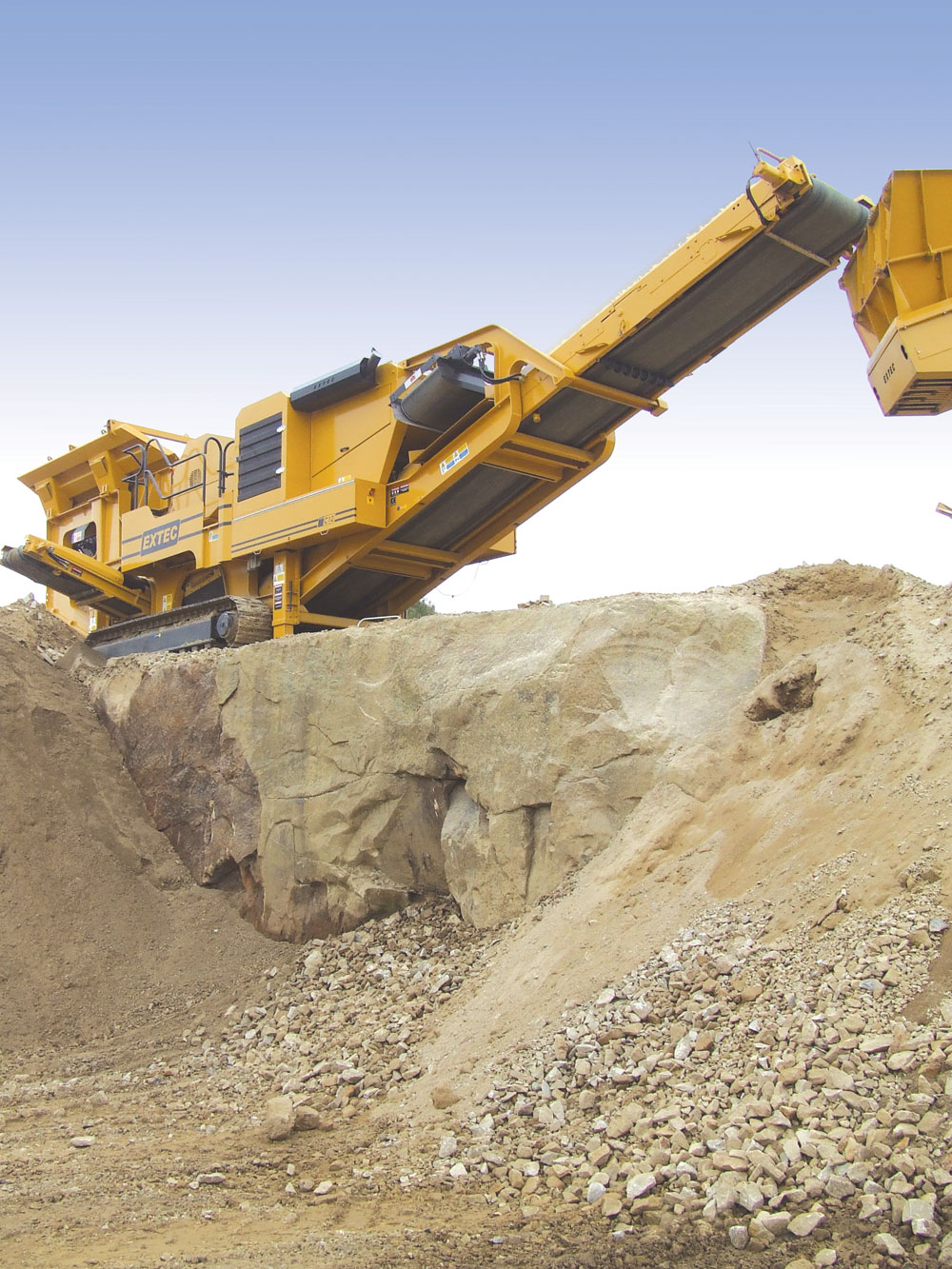
Extec machines turn waste product into revenue stream for Gillson
West Yorkshire-based decorative stone producers Dennis Gillson & Sons Ltd are maximizing their profitability by using a pair of Extec crushers to convert a waste product into a revenue stream. Based in Keighley, the family-owned firm is using a C-12+ mobile jaw crusher and an X38SBS mobile cone crusher to turn overburden, fines and waste material derived from the decorative stone production process into a valuable high-quality aggregate.
Although there has been active quarrying on the site for several hundred years, the 7ha Naylor Hill Quarry has been in the Gillson family since the business was formed some 70 years ago by Dennis Gillson, grandfather of current managing director Darrell Gillson. Following family tradition, the company quarries decorative sandstone for flagstones, architectural finishing features and complicated masonry products.
The quarry itself is on two levels and extends down to a depth of approximately 25m at its deepest point. This new lower level consists of hard millstone grit, while the upper level of the workings comprises fine-grained ashlar sandstone covered by around 9m of overburden, which, until recently, was viewed as a waste material.
Rock is extracted at the site using a hydraulic excavator equipped with a hydraulic hammer, as blasting causes too much damage to the valuable stone. Blocks weighing up to 5 tonnes are taken to the saw mill and cut into shape before being finished by hand to give a natural texture.
The Extec crushers were purchased to deal with the overburden from the upper level of the quarry and to utilize the waste from the cutting and finishing process. ‘We pride ourselves on the quality of our finished stone products, so we have traditionally seen the overburden purely as a waste,’ explained Dennis Gillson. ‘But, with the purchase of the Extec machines, we are now using that same material, together with the waste from the finishing processes, to produce a valuable commodity.’
The Extec C-12+ is fed by a Cat 365BL hydraulic excavator in mass-excavation configuration. The crusher is fitted with a grizzly screen that removes the fines prior to crushing to help maintain the quality and consistency of the end product. The C-12+ feeds its –90mm product directly into the X38SBS cone crusher, which, in turn, produces a 38mm primary aggregate product. The output from this track-mounted unit is then screened to produce a variety of other fractions: 10mm, 6mm and 4mm, together with a sand product.
According to Mr Gillson, the combination of Extec machines can easily produce a throughput of more than 200 tonnes/h, but he says he is more interested in quality than quantity.
‘We purchased the Extec units because, in my opinion, they are the best machines on the market. They are well built and have lots of excellent features, such as the self-lubricating system,’ he said. ‘What is a real boon though is the ability to change the size of the product so easily. In fact, the systems on the two crushers are so well automated that I can set them up to produce the required products and then simply load the rock in at one end and watch a perfect product come out the other, without the need for additional help.