How Trommel Screens can Recover Clean Rock from Waste Materials
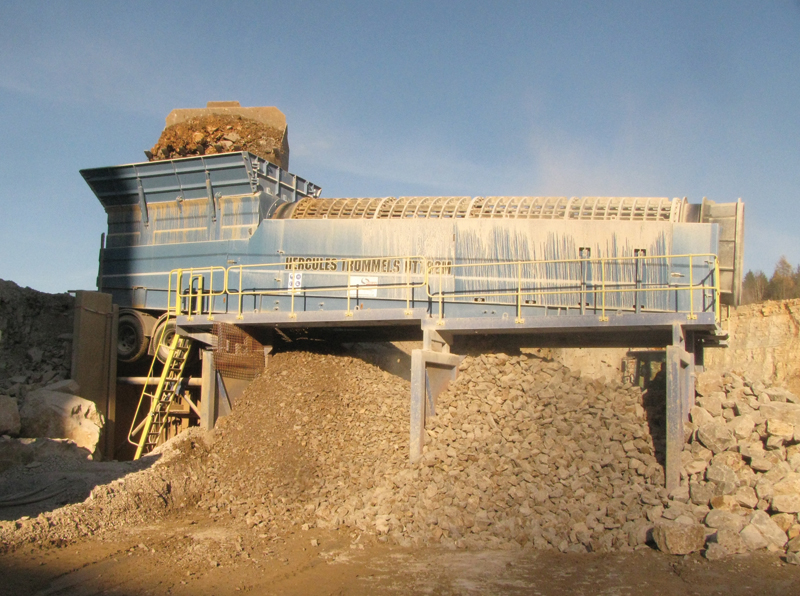
First published in the February 2014 issue of Quarry Management as Lifting the Burden of Overburden
The use of heavy-duty trommel screens to recover good-quality clean rock from waste materials
Demand for good-quality stone has risen in recent years and although much of the UK quarrying industry is currently suffering from the effects of the economic downturn, operators are still looking to maximize their potential reserves in order to make their operations both economic and profitable.
Restrictions on the opening of new quarries and the development of existing sites has meant that matching production to demand has become a challenging balancing act. Companies are now looking at the often vast hidden reserves of waste that were left behind as the quarrying of more easily accessible good rock became the prime objective. As good-quality rock reserves become less abundant, new methods for both cleaning and sizing have been developed to capitalize on these material assets.
The development of the heavy-duty trommel screen has been at the forefront of this recent trend and has resulted in very high recovery rates of good, clean rock from waste overburden. This, in turn, has helped quarry companies to increase their operating profits.
History
Trommel screens have been in use since mechanized quarrying began in the late-eighteenth century. At this time the screens consisted of circular steel meshes bolted together to form a single barrel, which rotated around a long central shaft set at a slight inclination. Crushed material travelling through the barrel was graded out according to the size of the apertures making up the cylinders. These screens were used extensively until the 1950s, when vibrating flat-bed versions started to appear on the market. The development of bigger, more robust, high-capacity trommels in the 1980s, largely for the production of rip rap and armour-stone, paved the way for heavy-duty trommels purpose built to handle high tonnages of material and very large lump sizes. The tumbling action within the barrel breaks up any unwanted clays to produce a clean product. The barrel itself is self-cleaning and the entire unit works without a permanent operator.
Aperture sizes in the barrel are selected to suit individual customers’ project requirements. As well as cleaning dirty and contaminated feed materials, trommels have been used for taking out fines prior to crushing. Other duties include the high-volume production of sea/river defence rock and sized material used for gabion baskets to support road and rail cuttings.
Demonstration
During a recent extended demonstration at a major quarrying company site in the UK, a Hercules HT182M mobile trommel was used to process heavily contaminated waste material to recover the clean stone contained within it. The waste, which had amassed over a number of years and amounted to several millions of tonnes, was the product of previous quarry extensions along with continued areas of dirty feed material within the quarry face. The quarry was rapidly running out of space within the waste area and this would have an impact on valuable areas for further excavation work in the future.
The feed material in the quarry is notoriously sticky in wet conditions and during the period of the demonstration the weather was particularly bad with long spells of heavy rain. However, the versatility of the Hercules trommel controls allowed the barrel rotation speed and reciprocating feeder rate to match the feed material and weather conditions in order to maximize the screening efficiency and throughput. The barrel apertures on the trommel were selected to suit the customer’s project requirements and were also suitable to cope with the demanding feed material. A barrel section for gabion sizes was also introduced, thereby adding a new product and allowing the customer to generate extra sales revenue.
The trommel was fed at a rate of up to 500 tonnes/h using an excavator that was already operating at the site. The rejected material and clean stone were removed from under the trommel using loading shovels, while the oversize material exiting the end of the trommel was dropped over the existing bench and allowed to build up until removed by loading shovel when required.
During the demonstration an accurate record was made of the daily weather conditions, where the feed material was located within the waste pile, the throughput of the trommel and the recovery percentage achieved. Calculations were also made on the costs for blasting, royalties, loading and hauling, and fuel. It was quickly apparent that a significant saving could be made in many areas with the trommel in place, such as:
- Reduced fuel costs for mobile plant
- Reduced haulage costs with fewer mobile plant movements leading to less mobile plant being required on site
- Planned quarry extensions suspended while still giving extended life to the quarry
- Less pressure on other crushing/ screening plant within the quarry as the stone reaching the plant is not contaminated. This leads to improved reliability
- New products produced by the trommel giving extra sales revenue.
Various locations were used within the vast waste pile to select the feed material for the demonstration. In some of these locations the feed material had been sitting in the same place for many years, which made the contamination very compact, especially lower down where finer material had washed through. Even with the heavy rain during the demonstration the trommel coped well with the difficult feed material and excellent recovery rates in excess of 60% were recorded. This rate of recovery would have been almost impossible by any other current method.
The amount of unwanted waste material returning to the waste pile after passing through the trommel was greatly reduced and further working of the waste pile will result in more quality stone being recovered and more room on the quarry floor as the waste pile reduces in size. And because the existing waste pile can be worked on for many months to come, possible planned quarry extensions can be put on hold, which will result in further cost savings from not having to submit expensive planning applications.
The clean gabion removed from under the trommel is made available for immediate sale as a new product from the quarry. Meanwhile, the clean oversize material off the end of the trommel is sent to the primary crusher without the additional problem caused by the contamination, thereby helping to prevent future breakdowns and allowing the rest of the plant to be much more efficient and reliable.
Future
The increasing requirement to reclaim and recycle a greater proportion of primary rock, and the need to clean materials containing heavy contamination, will ensure that heavy-duty trommels continue to play a major role in these projects worldwide for many years come.
For further information visit: www.herculestrommels.co.uk
- Subscribe to Quarry Management, the monthly journal for the mineral products industry, to read articles before they appear on Agg-Net