Eliminating Wet Stockpiles
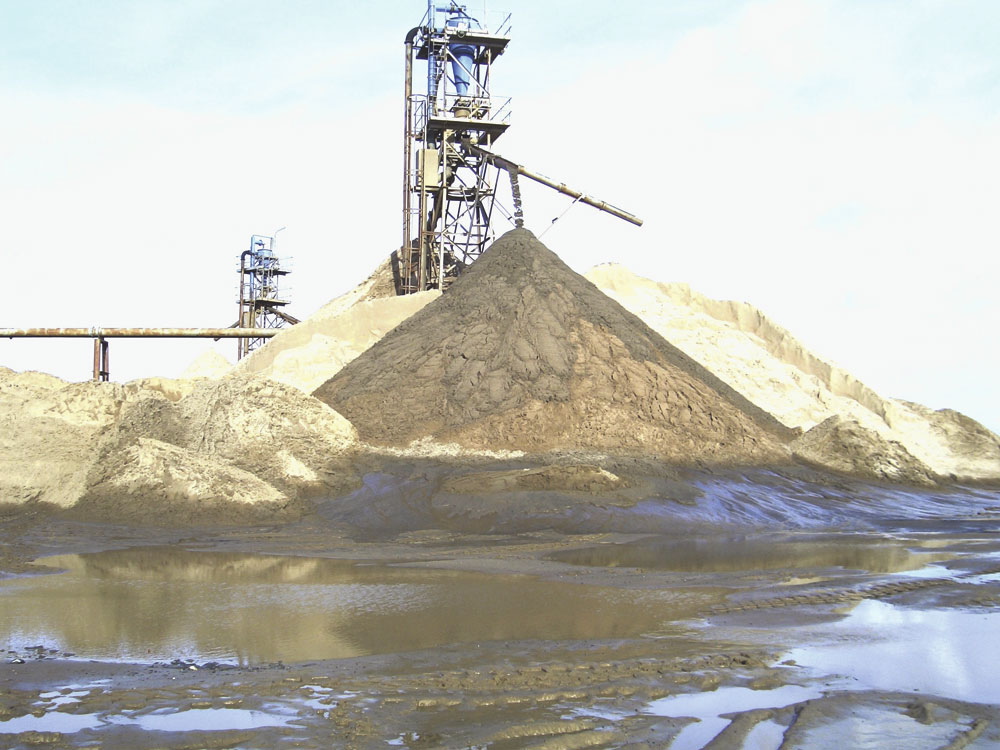
Moisture reduction system solves stockpile drainage problem for Lough Neagh sand producer
In February 2004 Quarry Management reported on a system capable of achieving accelerated moisture reduction in sand stockpiles, reducing gravity drainage times from a period of days or weeks to a matter of hours, and significantly reducing the costs associated with force drying material in kilns, dryers or oil-fired furnaces.
The patented system is the creation of geotechnical consultant and dewatering expert Len McGarry, founder of Congleton-based Moisture Reduction Systems Co. Ltd, who first devised the concept several years ago during his time as managing director and chief executive of his former company, Groundwater Control Ltd.
Moisture Reduction Systems’ subsequent research and development work on accelerated vacuum-assisted drainage has culminated in the production of a cost-effective moisture-reduction pumping system, which is now available in the form of a complete design and installation service package that can be tailored to suit most material producers’ requirements.
One of the latest companies to benefit from such a system is Norman Emerson & Sons Ltd, a family run sand and gravel business based in Derryadd, near Lurgan. Their system — the first of its kind in Northern Ireland — has been installed at the company’s Ardmore sand quay on the shores of Lough Neagh, where, according to general manager Colin Emerson, it has quite literally ‘transformed’ the company’s operations.
Emerson’s system was designed to alleviate serious site drainage problems being caused by run-off from their six Linatex cyclone sand stockpiles. Before the installation of the moisture reduction system earlier this year, the Ardmore site was prone to considerable surface saturation and flooding from the stockpile run-off, resulting in large puddles around the site and multiple streamlets discharging directly into Lough Neagh. As well as causing operational difficulties on site, this was proving to be of considerable concern to Northern Ireland’s Water Management Unit, part of the Environment & Heritage Service, which was pressing Emersons to find a solution to the problem.
Having rejected the possibility of creating an extensive drainage system around the entire site on cost grounds, the company decided to investigate the possibility of using an accelerated moisture reduction system. To find out more, Emerson’s management team travelled to England to visit Bathgate Silica Sand Ltd’s Arclid Quarry in Cheshire, where they were able to examine an operational moisture reduction system at first hand. The team were so impressed with what they saw that managing director George Emerson placed an order for a similar system while on the way back to the airport.
The system now installed at Ardmore sand quay consists of a series of horizontal, special prewrapped drainage pipes located under each sand stockpile. These are connected to a manifold, which in turn is coupled directly to an automatic self-priming electrically driven pump set, equipped with a large-capacity vacuum pump. Each take-off on the manifold is controlled by a gate valve, allowing Emerson’s to rotate their stockpile drying programme as required. Stockpile drainage water is now channeled through sub-surface engineered suction points via an integrated pipe network to an existing central collection point. This centralized water-processing management system passes all water through an enlarged settlement pond before releasing the treated water to Lough Neagh.
The entire system was successfully installed and fully operational in less than a week, and Emerson’s say they are fully confident the system will pay for itself within two years.
Since the system was installed at Ardmore the site has been rendered virtually water free, resulting in a huge improvement in operational efficiency and successfully resolving the company’s environmental issues. In addition, drying time has been reduced from three or four days to around six or seven hours, resulting in a much faster turnaround of products, and the moisture content in the finished stock destined for further kiln drying has been greatly reduced, resulting in considerable energy-cost savings.