Easy Stroke Adjustment For GP300 Cones
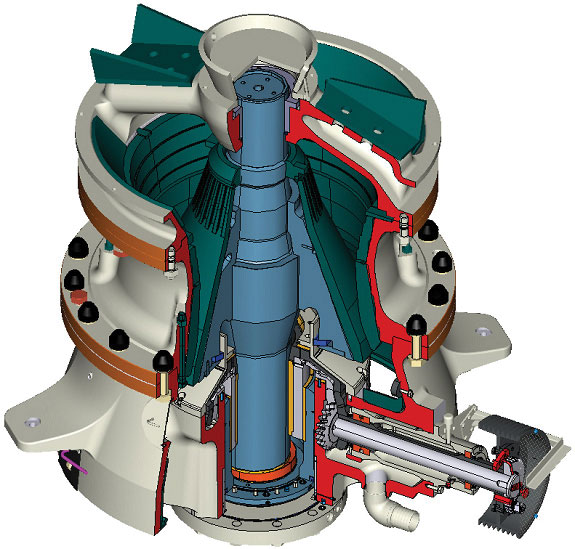
Traditionally, stroke adjustment in a cone crusher has not been used to optimize production in crushing plants. This is mainly due to the difficulty in accessing the eccentric bushing, as the top frame and main shaft need to be dismantled. However, the stroke influences cone crusher performance in several significant ways. Not least among these is that, in varying operational conditions, choosing the right stroke (larger/smaller) provides an opportunity to maximize the end-product capacity and product shape with GP300 and GP300S cone crushers.
The idea of externally adjustable stroke came from a Metso Minerals customer, Reijo Savolainen, who is chief executive of Rudus Murskaus. Recalling how he first thought of the adjustable stroke in the mid-1980s when faced with bearing problems in a crusher, Mr Savolainen said: ‘We had an old G14 cone crusher and were running it at too tight a setting to make fine fractions or achieve a good product shape. As a result of overloading the crusher, we had problems with the bearings. While I was dismantling it, I thought that the dirty work and crusher downtime could have been avoided if the crusher had not been loaded by too high a stroke compared with the closed-side setting. Decreasing the stroke without dismantling the crusher would have been the solution to the problem.
‘We did the stroke change a couple of times, but dismantling the crusher at the quarry is a demanding job,’ said Mr Savolainen. ‘There is always the risk of a mounting fault and of dust entering the bearing faces. Because of the potential risks, we prefer not to perform the stroke change in the quarry. This means that the stroke often isn’t changed at all during the crusher’s lifetime.’
Mr Savolainen resurrected the idea a decade later in the mid-1990s when he was working as technical director at Lohja Rudus Oy. He said: ‘We were looking for ways to improve our company’s profitability. On realizing that our plants were running with similar layouts and the same stroke in GP cones – even if the crushing requirements and the rock hardness changed every day, we began to study which stroke and setting combination would yield the best production in each job. Since we were aware of the risks of stroke adjustment involved in dismantling the crusher, we were forced to find another way,’ he explained.
The idea of externally adjustable stroke took several years to develop, but Mr Savolainen finally demonstrated his idea in scale-model form to Metso Minerals in early 2000. Further development of the concept took several more years but, after more than 10,000h of testing, Metso now offer it as an option on their GP300 and GP300S series crushers.
The benefits of externally adjustable stroke
Rudus Murskaus have two Metso Lokotracks and a Nordberg NW300GP wheel-mounted crushing plant equipped with the externally adjustable stroke. The crushers are running in two-, three- and four-stage crushing plants, and their work takes them all over Finland. The Lokotrack plant, which consists of LT125, LT300GPS and LT300GPB units, typically operates in two ways; either with the LT125 and LT300GPS producing 0–32mm or with the full train attached with the LT300GPB producing 0–5mm and 5–16mm.
‘When we are producing 0–32mm with a two-stage crushing plant, we typically adjust the secondary GP300S stroke to 25mm, because then we are able to use a small enough setting,’ explained Mr Savolainen. ‘Thus, we are able to maximize the amount of quality product we produce.’
The optimal stroke and setting combination changes when the plant takes on the third stage. ‘We are making two products in our three-stage Lokotrack plant: 0–5mm and 5–16mm,’ he said. ‘Depending on the market need and stockpiles, we may need to make more of either 0–5mm or 5–16mm. For example, if we want to maximize the 5–16mm fraction at our present quarry in Helsinki, we change the GP300S stroke to 18mm and the GP300 stroke to 25mm. However, if we want to maximize the 0–5mm fraction, we use a 32mm stroke in the GP300S and a 40mm stroke in the GP300. By changing the stroke in different jobs and with different rock types, we are able to get the best performance and product shape from the Lokotrack train at all times.’
Stroke increase improves product shape
Explaining how the stroke increase improves the quality of the end product, Mr Savolainen said: ‘In one of our quarries, the end product’s flakiness index was 11–12%. This was produced mainly by the GP300 at a 25mm stroke. The stroke was increased to 32mm and the shape improved so much that we met the requirement for under 10% flaky particles in the end product. We did not, therefore, need to use a VSI to shape the end product, which was a huge benefit for us.’
The financial benefit of stroke adjustment is shown in figure 1. If there is the possibility to upgrade production by increasing the stroke from the normal 25mm to 32mm and the change is not made, the blue curve illustrates the annual lost production in relation to the average contract size.
If the stroke is changed the traditional way, ie by dismantling the crusher, the red curve demonstrates the annual production lost because of the extra time needed to change the stroke. It is assumed here that changing the stroke in the traditional way takes 8h, while the externally adjustable stroke takes 10min. Apart from lost production, the additional costs incurred for labour, crane work etc amount to around €2,500 a year (example cost from Finland).
Metso Minerals, Crushing and Screening, Lokomonkatu 3, PO Box 306, FIN-33101, Tampere, Finland; tel: +358 20 484 142; fax: +358 20 484 143; website: www.metsominerals.com
Benefits of an externally adjustable stroke:
- No need to dismantle the crusher while changing the stroke
- Easier balancing of the crushing plant
- The possibility of adjusting the plant’s production according to market needs
- Easier to achieve a choke-feed arrangement
- Less need for silos and buffers to keep the GP cone choke fed
- Removes the need to change liners on a small contract to reach tighter settings
- Wider usable setting range
- End-product shape can be optimized