Building In Reliability
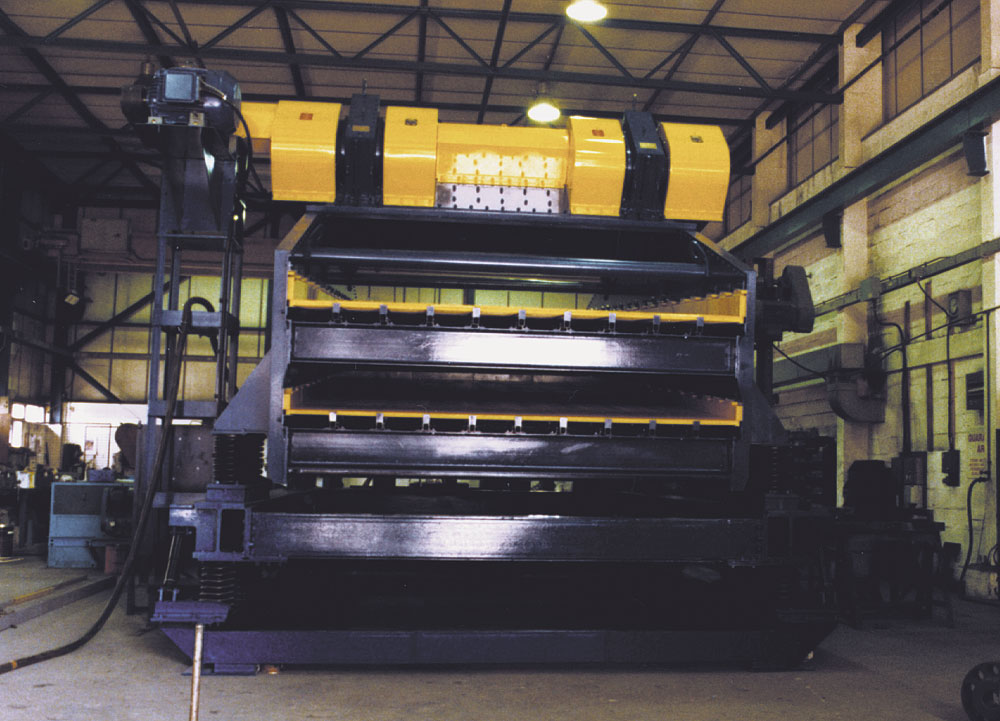
The case for more flexibility in the design and budgeting of a new screening plant
The author, Barry Smith, is managing director of Don Valley Engineering Co. Ltd
In the never ending drive to increase market share, quarrying companies are constantly looking for ways to reduce production costs by developing larger quarries and producing higher tonnages using bigger machines. But this is only part of the answer because any kind of stoppage then results in a greater tonnage lost for every hour the plant is stood idle.
For the past 20 years Don Valley Engineering (DVE) have been meeting the requirements of an ever changing minerals industry by designing and building larger screening machines to cater for the increasing tonnages being produced. They have supplied the front-line machines to virtually all of the high-capacity plants built in the last 10 years and in doing so have created an unequalled range of bespoke machines for all manner of applications, and have gained a wealth of experience in the design of bunker tops that they believe should be considered for all future applications.
In any minerals-handling plant two of the most problematic areas that cause the greatest hardship and downtime are the transfer points between equipment where spillage, dust emissions and build-up occur, and the drive mechanisms to the various machines where electrical or mechanical failings can render the machine inoperable. While it will never be possible to achieve a totally transfer- and drive-free plant, logic dictates that the closer manufacturers and operators can get to achieving it the more reliable a plant will be. To this end, any reduction in the number of drives and transfer points is a step in the right direction.
In the latest plant designs, the bunker-top arrangement attempts to employ this philosophy to the full by utilizing the minimum number of machines to achieve the mineral sizing required, with transfers between machines taking place via chutes that can be enclosed and sealed. Large numbers of screens fed by a multitude of conveyors and transfer points are things of the past. They were necessary in times gone by because large screening machines were not available, but the machines of today have the size and flexibility to both size and transport material if required. The following two examples show how this approach has been successfully employed by Tarmac Northern on their new-build plant at Swinden and their uprated plant at Barrasford.
Example 1
Swinden Quarry – New Build
Main Contractor – Fairport Engineering Co. Ltd
The diagram in example 1 shows the result of co-operation between the producer, main contractor and screen supplier from the inception of the project and illustrates how initial consultation between all parties has allowed the screens and bunker top to be arranged to complement each other. This arrangement has been used in a number of recent builds in various forms to suit the tonnages and bunker capacities required, but in all respects the philosophy of arranging the screens and bins to complement each other so that a minimum number of machines and transfer points are used remains.
In example 1 the input feed tonnage to the plant is in excess of 1,250 tonnes/h, requiring a twin-stream arrangement with each stream handling 630 tonnes/h of –100mm crusher-run and recirculated material. The screens are arranged in a single-pass layout developed by DVE to allow them to sit sequentially in line directly above the bin tops. This involves the extraction of the dust element first followed by the progressively larger size fractions. To achieve this the primary receiving screens are large triple-deck units measuring 3.4m in width x 8.9m in length. They are arranged to size at 10mm on the top deck with the underflow being received on the middle deck, which is arranged to size at 6mm before passing its underflow to the 4mm bottom deck for dust extraction into the first bin as underflow. The –6mm +4mm bottom deck overs are directed by chute into the –6mm bin together with further –6mm material derived from the initial section of the second screen’s bottom deck. The –10mm +6mm middle deck overs are carried by the initial section of the bottom deck of the second screen and directed into the –10mm bin.
The +10mm top deck overflow from the primary screen passes, via a chute, to the top deck of the secondary screen, a 3.0m wide x 8.5m long double-deck unit arranged to size at 10mm on the initial portion of its top deck and at 20mm for the remainder. The bottom deck of this double-deck unit comprises a split deck arrangement designed to collect both the middle deck overs from the primary screen and the underflow from the initial 10mm portion of the deck above, and to carry the whole forward on a 6mm deck to feed the –10mm bin. The remainder of the bottom deck is designed to receive the underflow from the 20mm portion of the top deck and size at 14mm, passing its underflow directly into the bin positioned below it. Overs from this bottom deck are carried forward and discharged from the end of the screen directly into the –20mm product bin.
The third screen in the series is a 2.4m wide x 7.5m long single-deck unit that receives the +20mm overflow from the top deck of the secondary screen. This screen first extracts the 28mm product from its feed as an underflow from the first section of deck before extracting the –40 mm product as underflow from the remainder of the deck. In both cases the sized products are discharged into receiving bins positioned directly below the screen. The +40mm overs from this screen are discharged from the end of the screen into the oversize bin, again sited directly below the screen.
Once the feed material has been delivered on to the receiving area of the primary triple-deck machine the screens both size and transport the stone to the respective bins without further mechanical assistance.
It will be appreciated from the compact arrangement, which allows the screens to be mounted close together and directly on the bunker tops, that a number of other advantages are also gained in pursuit of an efficient and effective plant that allow further reliability to be built in. For example, the chutes transferring the stone between screens, being relatively short, allow the installation of expensive exotic wear-resistant liners that might normally be rejected because of their costs. Also, screens discharging directly into bunkers do not require chutes and the whole system can be readily encapsulated to prevent dust emissions and consequent downtime due to build-up.
There are also commercial advantages to the arrangement, for while the cost of bespoke screening machines is obviously greater than for other more standardized machines, their size and flexibility allows fewer machines and drives to be used to achieve the desired result, which in turn delivers overall reductions on the total plant cost.
Example 2
Barrasford Quarry – Capacity increase
Main Contractor – Don Valley Engineering Co. Ltd
Example 2 is a revision to an existing plant where the feed conveyor enters the bunker top housing at 90° to the screens, necessitating that a high-level splitter screen be used initially.
Originally the screen house on top of the bunkers was equipped with a large number of screens and conveyors collecting material and transporting it to the next sizing stage or into the relevant bunker. The aim in revising the plant was to replace this aging equipment, increase processing capacity and improve plant reliability by removing as many drives as possible.
Squeezing larger machines into existing plants is no easy task but if control is maintained over how the machines are designed and built there is usually a bespoke solution that will achieve the desired result. In this particular case the primary splitter screen is a double-deck unit with an elongated top deck to assist in feeding the overs to a large stone-classifying screen. This makes for a longer screen than normal but in return allows the classifying screen to be mounted directly over the existing reception bunkers and allows material to be transferred from one screen to the other by a chute instead of a conveyor, thereby resulting in an overall cost reduction on the installation while providing a better arrangement.
The two underflow products from the splitter screen are also fed via enclosed chutes to their destinations; in the case of the –14mm +10mm product directly into the bunker, and in the case of the –10mm material to the fine classifying screens for the sizing of the dust to 10mm fractions. Making these units bespoke allowed deck lengths to be adjusted to assist in the delivery of the various sizes fraction to the correct bunkers or, as in this case, to produce specialist flaked material.
The entire installation met the clients requirement of replacement and increased tonnage while simplifying the sizing process and creating a more reliable plant with fewer machines requiring maintenance.
In attempting to build reliability into plants the one thing that is certain is that the mineral being processed will wear the plant out, the only question is when. Screen manufacturers, by using ‘G’ force to effect the means of separation and sizing, aid and abet this process by applying 4 to 5 ‘G’ to each particle 900 times per minute as it makes its way along the deck, which results in high impact forces and enhanced deck wear. To help overcome this many exotic deck materials have been developed ranging from hard-faced steel plates to resilient rubber and polyurethane materials. Probably the most significant development in the last 20 years has been the introduction of the polyurethane modular system. The modular system is compatible with most screening machines and has proved to be a robust installation capable of high performances under the most arduous conditions. The flat screening surface, coupled with the inherent self-cleaning nature of high-quality polyurethane materials, guarantees maximum screening efficiency with minimum risk from blinding and pegging.
Since the first use of polyurethane decks suppliers have maintained continuous a development program to increase both the durability and availability of all manner of materials and apertures to meet the ever increasing market demand. The result is a reduction in lost time caused by deck maintenance and replacement, while maintaining the required specifications for longer. Today’s polyether-based elastomer materials have excellent resistance to abrasion, corrosion and water hydrolysis. They may be more expensive than some of the cheaper alternatives but their extended life, flexibility and performance make them more cost-effective by some considerable margin.
Reliability is an unusual characteristic to quantify. With an unreliable plant, knowing how long it has been out of action and how much production has been lost makes it easy to work out what it is costing, but if a plant is reliable and does what it should, when it should, it is very difficult to quantify how much this is actually worth. It is clearly worth something and it is probably quite substantial, but how can this be factored into a budget evaluation for a plant, particularly when the budget strategy calls for payback within a given time otherwise it will not be approved. This is a dilemma many engineers face each day when trying to balance the scheme that is correct for the plant against what the company budget restrictions will actually allow. All too often the scheme is compromised to make it fit an arbitrary budget figure rather than considered against realistic whole-life costs and returns.
The purpose of this article is to give a brief indication of the type and range of bespoke screening machines available and the advantages they offer, and to make the argument for more flexibility when considering the initial design and budgeting of a new plant. Reliability, longevity and ease of operation are ideals which may be hard to quantify but they should, nevertheless, be at the top of every plant designer’s wish list because they are worth paying for.