Autonomous Crushing Technology
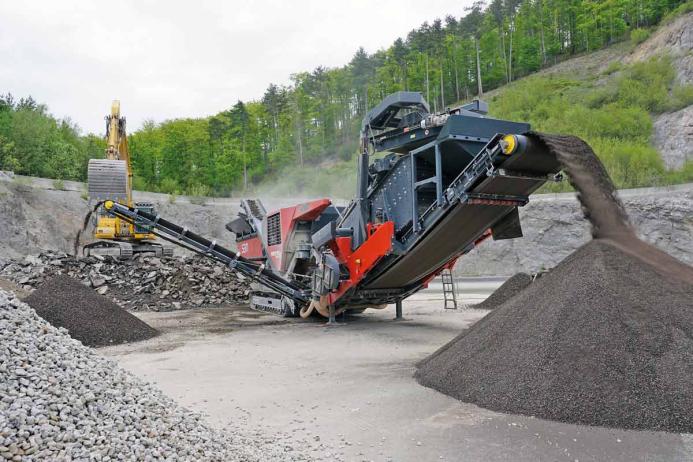
First published in the September 2024 issue of Quarry Management as Right on Schedule
SBM Mineral Processing’s flagship REMAX 600 track-mounted impact crusher is a central component of the Austrian OEM’s ‘Autonomous Crushing’ project, which is set to revolutionize mobile aggregate processing. Working in partnership with the University of Leoben, SBM are hoping to make this ambitious operating concept a reality with the first-production autonomous crusher expected to be ready for market by 2026
The aggregates and mineral products industry is facing an array of challenges, including constantly increasing environmental requirements, extreme cost pressure due to rising energy prices, a shortage of skilled labour, and unchanged high demands on production conditions and quality.
In response to these challenges, crushing equipment specialists SBM Mineral Processing have launched the ‘Autonomous Crushing’ project in partnership with renowned University of Leoben. The Austrian partners have been working on the necessary ‘reactive’ plant technology for the past four years and are developing innovative sensors to recognize the feed material and reliably monitor end-products.
At the same time, both organizations are creating a global 24h-a-day, seven-days-a-week network for the fundamentally new AI-supported processing of material and process-relevant data. This is being carried out based on powerful cloud-based communication in a constant exchange between the crushers on site, their ‘digital twins’ at the SBM base, and the databases in Oberweis and Leoben, which are constantly fed with new global reference results.
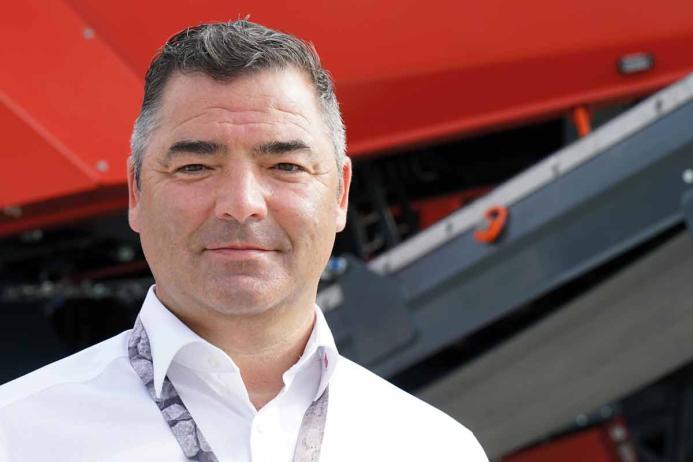
From automation to autonomy
The path to autonomous crushing is comparable with the development steps and stages towards self-driving cars. The driver’s workload is already being reduced by largely automated control and assistance functions (eg engine/vehicle status, cruise control etc). And new sensors are already allowing for controlled ‘hands-free’ driving in some cases.
In autonomous automobility, the vehicle is ready with a full tank of petrol in good time, has preselected both the route and driving mode according to the destination and desired arrival time, and takes its passengers to their destination in a safe, economical, and environmentally friendly way, and above all, without a steering wheel.
‘Translated into processing practice, this means that the customer can optimally equip their systems before use based on the starting material and the desired end products – regardless of whether they want to complete the job as quickly or as economically as possible,’ explained Helmut Haider, sales director of SBM Mineral Processing.
‘Before a planned job, the operator also knows whether maintenance work is due within the duration of the work or the expected production tonnage, or whether individual tools are reaching their wear limit. This significantly increases availability.’
Additionally, the autonomous SBM crushers can take over the incoming material inspection at the feed hopper. The AI-supported sensor system will correctly recognize raw materials or different types of construction waste.
On track
SBM’s Crush Control plant control system, which was presented back in 2018 and is now used in all second-generation SBM crushers, provided an important basis for the development of the company’s autonomous crushing operating concept. The PLC-based system makes full use of the advantages of the largely electrified main and auxiliary drives and continuously records all load conditions, crusher settings, and weighing data.
By specifically adjusting the feeder speed, for example, Crush Control automatically controls the production process according to preset parameters, ensuring trouble-free operation. All settings and automated routines (eg start/stop function) can be selected intuitively via a large 10in touchscreen display, which also provides continuous information on the operating status.
Crush Control already offers a proven cloud-based communication platform with easy-to-use app access and extensive telemetry support. In addition to the large amount of rock and process-relevant data from the SBM test laboratory and University of Leoben archives, the current operational data forms an indispensable basis for AI-supported autonomous crushing.
The first machine-specific values were collected during the prototype tests of the REMAX 600 impact crusher. At the same time, the developers made a significant breakthrough last year in the optical real-time detection of grain sizes produced, which are recorded by a specially developed sensor system on the main discharge conveyor in front of the screening module.
The SBM flagship machine was put through its paces in comprehensive 1:1 testing under typical quarrying and recycling conditions. The analysis process and its algorithms were optimized for fast recording and processing, particularly taking into account the applicable quality requirements such as DIN EN 932/933. All results were successfully validated using weighing belt data and product tests.
A new, fully hydraulic crushing gap adjustment system for the impact crusher of the REMAX 600 is currently being integrated. This system will enable fully automatic adjustment of the crushing characteristics to the feed material and end-products. It will reliably prevent excessive wear, while special sensors will record the condition of any tools to continuously ensure high-end product quality.
An important development stage of autonomous crushing is the categorization of the feed material. Here, AI-supported detection systems evaluate the production-related properties of the source material (degree of hardness, size distribution, filler content etc) in real time.
Mr Haider concluded: ‘SBM are well on schedule here. We are currently optimizing the AI-supported real-time detection and classification of feed material and crushed products as the basis for a fully automated crushing process. The technology is expected to be ready for market launch and use in other crusher classes as early as 2026.’
Subscribe to Quarry Management, the monthly journal for the mineral products industry, to read articles before they appear on Agg-Net.com