A Matter Of Attrition
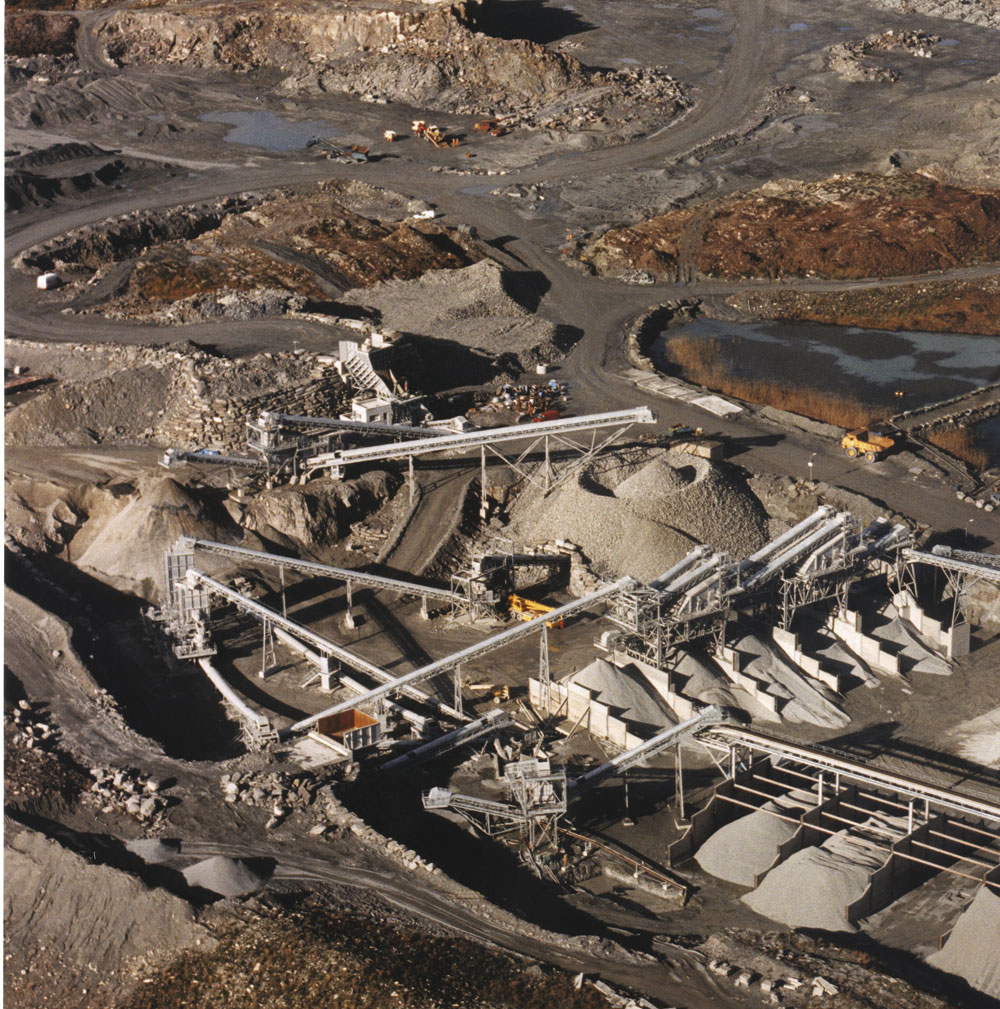
The application and benefits of attrition crushing principles using high-performance cone crushers
In recent years some very important changes have affected the quality requirements for finished aggregates in the construction industry. Aggregate users are no longer prepared to accept ‘any product shape’ that the supplier provides.
Customers’ requirements are now much more sophisticated and demand a cubical product shape because this offers the following benefits to the end-user:
- It increases the shear strength of structural concrete by providing a more homogeneous mix.
- It reduces the water (and hence the cement) content in ready-mixed concrete for a given structural strength, thereby reducing the cost per cubic metre.
- It increases the skid-resistance of asphalt wearing courses by presenting more angular faces to the tyre than a series of very flat particles.
- It helps to reduce aquaplaning in wet weather when used for asphalt wearing courses because it reduces the amount of flat surfaces in contact with the tyre.
Continually increasing energy costs mean that producers have constantly to examine their operations to ensure that their plants are as energy efficient as possible. But producers also naturally demand that the equipment they use maximizes the production of their most saleable product sizes. Aggregate plants also have to be flexible enough to be able to change product mix easily to suit varying customer demands.
The days have gone when producers could afford to carry tens of thousands of tonnes of stock material. In today’s highly competitive markets they need to be able to produce materials using ‘just in time’ methods. This reduces stock and inventory pressure on the producer and increases his return on invested capital. It also avoids the stock deterioration problems that can occur when aggregates have been stored for any length of time.
Principles of attrition crushing
Looking back to the 1970s, a typical 3ft cone crusher would have had a capacity of around 75 tonnes/h when used in a secondary application. Such a machine may have followed a 1000 x 600 single- or double-toggle jaw crusher after the undersize had been removed. This would result in a –175mm +50mm fraction, for example, being fed to the secondary cone crusher, in some cases via a surge bin but in many cases by trickle feed.
Towards the later part of the 1980s several manufacturers began to revolutionize the way they built their cone crushers. They realized that by making some subtle changes to the crusher design they could significantly increase the performance of their machines.
Terex Pegson were one of these manufacturers. The inherent strength and all roller bearing design of the Autocone machine made it an ideal candidate to be modified to operate at a significantly higher speed and with a larger motor. The result of this was a very significant increase in crushing performance, the main reasons for which are summarized below.
First, it was found that there was no need to pre-screen the feed to the cone crusher due to the minimal frictional losses with the roller bearing design. This dramatically reduced the plant capital cost and plant complications because the feed material could pass directly from one crushing stage to another, as shown in figure 2. This increased plant reliability and reduced the running costs as the quantity of installed equipment was greatly reduced.
Secondly, the plant capacity increased dramatically because the smaller material in the feed was able to pass through the crusher quite easily by simply filling the voids between the larger pieces of rock in the crushing chamber. As a result the capacity of the equivalent size of cone crusher jumped by at least 40%. Figure 3 shows a cross section through the crushing chamber of an attrition crusher compared to a conventional compression cone crusher.
It was also found that by filling the voids in the crushing chamber product cubicity was much improved. Another benefit of filling the voids was that much higher reduction ratios could be obtained; field testing showed that over 90% of the product would be less than the crusher closed-side setting in many applications (fig. 4).
These higher reduction ratios reduced the number of crushing stages required for a given application; a good example of this is the production of Type 1 sub-base material in the UK. The standard specification calls for between 40% and 70% passing 10mm. This can now be regularly achieved using a jaw crusher and just one attrition crusher, as indicated in figure 5. Previously three crushing stages and two screening plants would have been required to achieve the same finished product specification.
Thirdly, it was also found that attrition crushing allowed producers to manufacture more of the sizes demanded by customers. An interesting phenomenon was discovered whereby it was found that, in general, changing the setting only affected the quantity of oversize and undersize. This may not seem too surprising but the result was that the middle sizes, eg –20mm +5mm, stayed fairly constant regardless of the setting. As attrition crushing, particularly in tertiary applications, maximizes these highly desirable fractions the benefits to the customer were considerable (fig. 6).
Fourthly, in general, attrition crushers operate at wider settings than conventional cone crushers. This is because attrition crushing always gives higher reduction ratios and so, for a given setting, the finished product has a much higher fines modulus.
The wider settings used by attrition cone crushers also help to reduce the load on the crusher components and limit the risk of packing in the crushing chamber. Packing can be a problem when using conventional cone crushers at tight settings, as the power and pressure increase enormously when this occurs.
Finally, the need for impact crushing has been eliminated in many applications. The reduction in wear, dust, filler etc, together with the more consistent output produced by attrition crushing, offers many advantages to producers and end-users alike.
Application and installation
There are a number of important points to remember when considering the application and installation of attrition crushers. These are highlighted here as a guide for plant designers and end-users:
First, the crusher must be designed from the outset for attrition crushing applications. Machines such as the Automax, which have been specifically developed with this in mind, need to be used. Conventional style cone crushers cannot be used successfully for attrition applications.
Secondly, the crushers must be continually choke fed — this is also a useful rule for conventional cone crushers.
Thirdly, the feed must be reasonably well mixed to ensure that a homogenous mixture is created in the crushing chamber. This is easily achieved using a dead box above the crusher feed ring to ensure that the coarse and fine fractions are mixed at the feed entry point (fig. 7).
Finally, attrition crushers such as the Automax range and other similar models can accept fines in the feed provided they are not excessively moist and do not represent an excessive proportion of the total feed to the machine. A typical example would be a –175mm feed with around 20% passing 10mm and up to 10% passing 5mm.
There are many successful examples of attrition crushing principles in operation and the benefits are immediately obvious. The layout is very simple with the jaw crusher product being fed directly into the secondary cone crusher without intermediate screening. The resulting finished product can be used as a sub-base material but in some cases is even suitable for use as higher-value aggregate.
Where the material is naturally more difficult to shape, the specification is very high or more fines are required, it can be passed to a tertiary crusher (fig. 8). The quality of the finished product in these cases can be extremely high with flakiness figures often in the low- to mid-teens or even single figures.
Attrition crushers can also be used very successfully for the re-crushing of very flaky feed material. If the various sizes are combined to give an all-in feed the results can be very impressive.
The author has been involved in a number of applications where a single attrition crusher has replaced two crushers and a screen and yet still produces better shape, more chippings, less dust and a higher throughput than the previous multi-unit installation.
As well as offering big advantages for static plants (fig. 9), attrition crushers also have many benefits in portable applications. Self-contained track-mounted Maxtrak crushers have become extremely popular with crushing contractors, civils contractors and quarrying customers for the same reasons.
Product shape and elongation have been affecting customers in some European countries for many years. The demand for high-quality aggregates is increasing around the world, especially in areas such as the US, the Middle East and India. Aggregate producers need to equip themselves with plant to be able to achieve these stringent requirements otherwise they risk being left behind by those competitors who do have the foresight to modify their plants to suit the needs of their customers.
The author, Andrew Dakin, is sales director with Terex Pegson