Ventilated Turbo Pulley
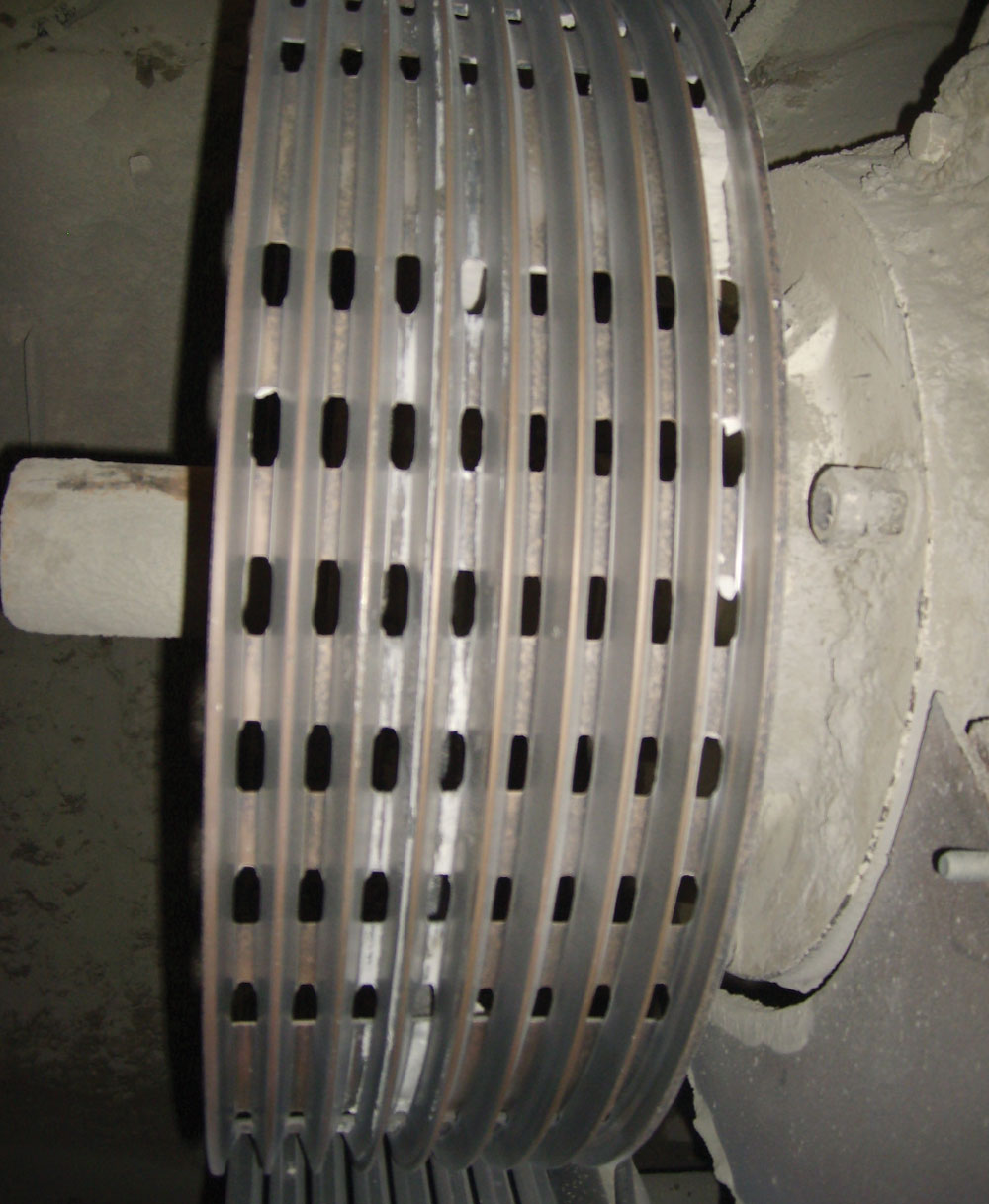
New V-belt pulley design aims to revolutionize performance and reduce costs
In November 2007 RailCorp were approached to trial BIRN VTP pulleys at their Bombo quarry site in New South Wales, Australia. The VTP (Ventilated Turbo Pulley), which represents a completely new approach to V-belt pulley design, is believed to have the potential to offer considerable cost savings in the quarrying industry.
Compared with conventional V-belt pulleys, the VTP pulleys are said to be: 50–60% lighter than grey-iron pulleys; have less internal tension; allow up to twice the rim speed (up to 100m/s) compared with other off-the-shelf products; and can lower belt temperatures by up to 17°C due to their ventilated grooves (a 10°C reduction theoretically doubles the belt life).
For the purposes of the trial, the Bombo site’s Jaques 4ft secondary cone crusher – chosen because it experiences some of the most extreme conditions at the site – was fitted with a 475mm diameter eight-groove VTP pulley on the drive and an 800mm diameter eight-groove VTP pulley on the crusher.
Background
The purpose of this secondary cone crusher is to reduce –600mm basalt to a –60mm product at up to 600 tonnes/h. Historically, the crusher was driven using grey-iron pulleys and SPC belts. Operating approximately 10h a day, these pulleys had a service life of six to eight months, with the belts being replaced, on average, every 10 weeks.
The three main problems that were being encountered using the grey-iron pulleys were dust accumulation, excessive wear in the belt grooves and premature belt failure.
Dust accumulation was a major issue for two reasons. First, build-up on the inner circumference of the pulleys was causing the drive to run out of balance if left uncleared. This, in turn, was causing a significant shortening of the bearing life on both the motor shaft and the crusher drive shaft. To overcome this problem, the quarry maintenance team were required to remove the guarding and clean the pulleys on a regular basis.
The other problem caused by dust accumulation was excessive wear in the belt grooves of the pulleys. Even with the pulleys rotating at speed, dust would become trapped within the grooves causing excessive wear on both the belts and the pulleys themselves.
As with all V-belts heat is a problem, and with the grey-iron pulleys this was a contributing factor to reduced belt life. During normal operation, and especially with a heavy workload (largely due to a percentage of oversize material), the pulleys would run extremely hot.
Aims
The aims of the trial were to ascertain:
- The ability of the VTP pulleys to perform in extreme conditions.
- The life expectancy of the VTP pulleys compared with grey-iron pulleys.
- The life expectancy of the belts running a VTP rather than a grey-iron equivalent.
- The ability of VTP pulleys to perform in a high-debris environment.
- The ability of VTP pulleys to absorb the shock loads transmitted through the crusher drive shaft.
- Any savings obtained through reduced downtime, maintenance and spares during the first 12 months of operation.
- Whether dust build-up on the inner circumference was lessened or eliminated.
- The occupational health and safety impacts.
In December 2007 the crusher pulleys were changed to the BIRN VTP type, and at the time of the last audit in December 2008, these pulleys were still in operation and not due for replacement until mid-2009.
Results
The VTP pulleys performed so well in this application that other items of plant which utilize a V-belt drive system are currently being re-evaluated, with a view to standardizing all drives with the VTP as and when the current grey-iron pulleys become due for renewal.
The VTP trial proved:
- The pulleys are able to work within the extreme conditions without failing.
- To date, the VTP pulleys have outlasted their grey-iron equivalents by a ratio of 2:1, with the expectation that, by the time the pulleys are changed, the ratio will be approximately 3:1 or better.
- To date, belt life has been extended by five times (the only failure being caused by a piece of steel jamming in the crusher).
- Dust build up on the inner circumference has virtually been eliminated with no cleaning required to date. Also, wear in the grooves caused by dust build up has been reduced, as proven by the increased service life.
- Significant savings in maintenance and belt replacement have been achieved over the first 12-month period.
- As VTP pulleys are much lighter than grey-iron pulleys, the installation of the VTP was much safer and easier. The 800mm diameter, eight-groove pulley, at 77.5kg, was safely lifted by two men (grey iron for this size range is approximately 168kg). While not completely eliminating manual handling issues, the VTP does lessen them. Also, moving the pulleys around on the catwalk and setting the pulley on to the taper lock while positioning the pulley in line with the drive proved to be easier. The ease of manual handling in this particular installation therefore made the job safer for the maintenance staff.
Savings/Costs
Although it has not been possible to give a detailed breakdown of the costs/savings in this report, due to commercial confidentiality, a general overview of cost versus savings is given below.
The initial cost, ie the price difference between the grey-iron pulley and the VTP pulley, was approximately 38% higher. However, total savings over the 12-month period, including extended pulley life, V-belt usage, labour/maintenance and downtime, were in the order of A$12,000. As a result, the balance of savings for the trial was approximately A$10,500.
Summary of key advantages
Key advantages of using VTP pulleys include:
- Reduced weight of the VTP design allows for ease of handling.
- Installation cost savings.
- Ease of installation and alignment.
- Increased service life of the pulley.
- Increased belt life.
- Reduced maintenance costs.
- Reduced inventory costs.
For further information regarding this trial, contact Keith Robinson at Wearco NSW on tel: +61 2 4272 6400. Alternatively, contact Lewis Pulleys on tel: +61 2 9319 5541.