Under Pressure
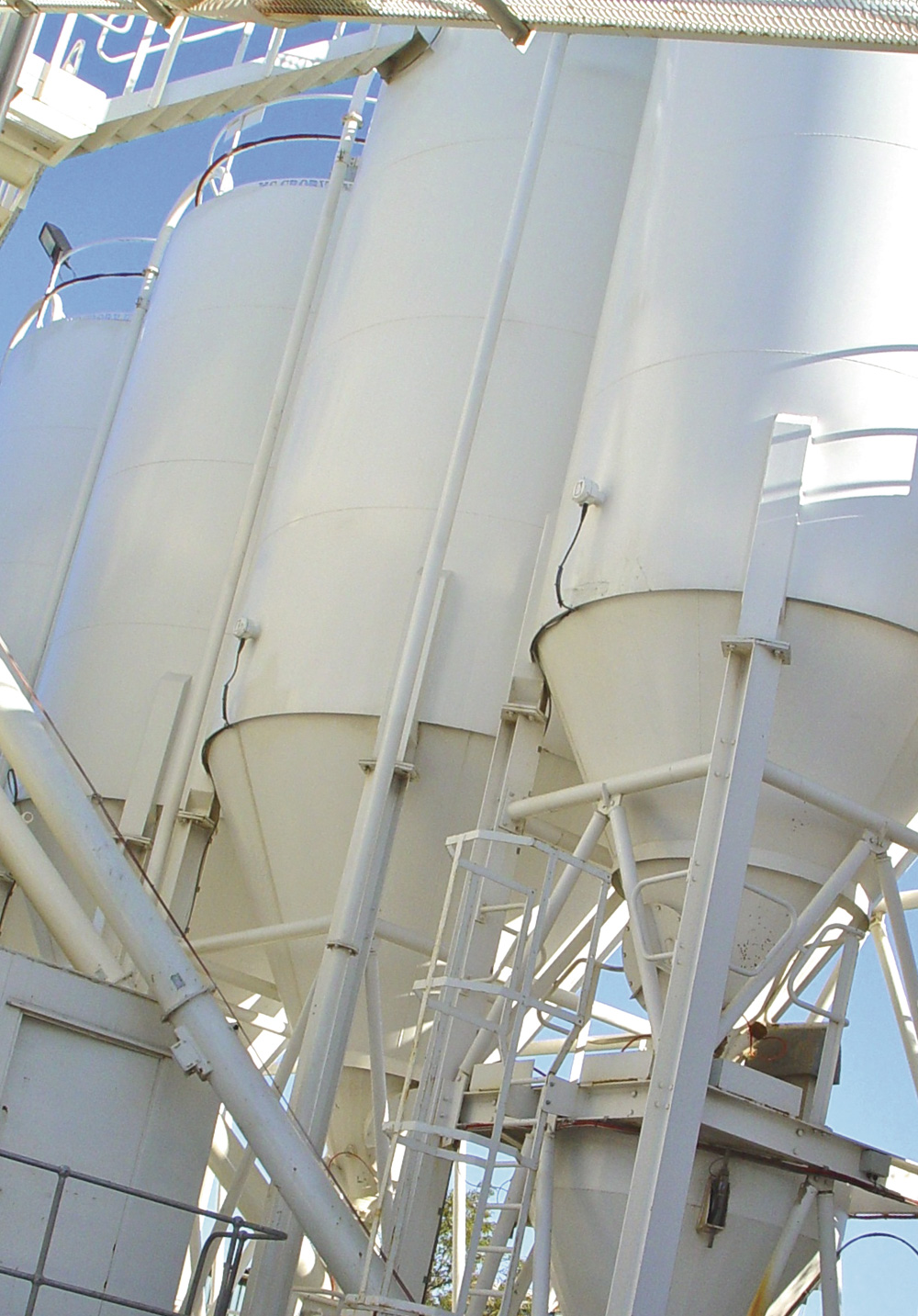
Meeting the new MPA guidelines on cement deliveries
To help reduce accidents within the quarry and cement industry, new guidelines have been introduced by the Mineral Products Association (MPA) to address the problem of over-pressurization of storage silos during tanker delivery of cement. This new document is an update of the earlier version which was produced in conjunction with the Health and Safety Executive (HSE) to help tackle the problem and standardize on a best-practice solution.
The objectives are simple; to reduce or eliminate risk and improve health and safety by following best-practice guidelines for silo protection.
The consequences of over-pressurization of a typical cement silo range from an expulsion of cement into the atmosphere and surrounding area, causing environmental issues, to damage to the silo and the filters with the consequential risk of death or serious injury to personnel and members of the public in the vicinity.
In order to understand what is required for a safe silo protection system during a fill, it is necessary to explore the dynamics of the delivery process and the typical problems that can arise during bulk delivery to site. By applying logic to the control and monitoring of this process, a safe system for both site and delivery tanker operators is provided.
The guidance notes set out by the MPA state that over-pressurization can occur due to one or more of the following:
- An increase in the flow rate of air from the tanker at the end of a discharge.
- Overfilling of the silo.
- Failure of the pressure-relief valve to vent the flow rate from the tanker.
- Inadequate flow through the filters.
- Inadequate maintenance or design of the above equipment.
- Uncontrolled discharge of residual air from the tanker.
In order to identify a solution to the above points, it is necessary to explore how these problems arise and how they can be controlled in a safe manner.
Delivery process
Road tankers delivering cement carry loads of up to 44 tonnes and are fitted with compressed-air blowing systems that provide the air to transport the powder from the tanker to the silo. These tankers operate at pressures of up to 2 bar (29 lb/in2) and the belly or tank on the vehicle is a pressure-tested and certified vessel. The tank is pressurized by means of the on-board compressor, and the powder is fluidized through a distributor plate ready for discharge through the control valve on the vehicle. All these parameters are controlled manually and are monitored by the tanker driver during the discharge process.
The outlet from the tanker is connected via a flexible hose and couplings to the inlet pipe of the silo. The pipe and fittings are all pressure tested and certified to a pressure of approximately 5 bar (73 lb/in2). At the bottom of the inlet pipe to the silo is an automatic shut-off valve which is triggered by a pressure or level alarm in the silo, although this does not feature on many older systems.
From the point where the cement leaves the delivery truck, no other components in the system are pressure certified, including the silo itself. Typically, silos will not withstand a pressure greater than 0.07 bar (1 lb/in2) before rupturing, as they are designed to withstand only the load of the material inside. With supply pressures 30 times greater than this, the risk of accidents is clear.
During filling air is blown into the silo along with the cement, whereupon the cement falls out of suspension as it enters the silo and the air is vented through the silo filter to atmosphere. Not all of the cement dust falls from suspension, as a small percentage will get drawn into the outlet filter. However, most designs automatically clean themselves to prevent blockages during delivery.
When a delivery is taking place it is imperative that the tanker driver has sufficient experience to monitor the noise of the product being discharged and the movement of the flexible hose, as these are the only indicators he or she has of the flow rate of the powder into the silo. Mass flow of the powder being discharged into the silo is very important because the airflow into the silo will increase when the powder density is reduced. This is particularly important towards the end of a delivery, to prevent a surge of air into the silo. This part of the filling process relies on the experience of the delivery driver and must be monitored very carefully during each delivery. One of the main cause of incidents, as identified by the MPA, is an increase in flow rate at the end of discharge.
The maximum air flow rate into the silo is most likely to occur at the end of the delivery process, when the tanker is nearly empty and may be pressurized up to 2 bar (29 lb/in2). At this point the silo will be close to being full with the minimum of ullage or free space. Under these conditions the 2 bar pressure is connected directly to the silo, which, as mentioned earlier, generally cannot withstand a pressure much above 0.07 bar, so this air needs to be vented very rapidly to atmosphere through the silo ventilation filters. If the filters cannot discharge this air quickly enough, the pressure-relief valve, which must be sized to pass the maximum free flow from the delivery vehicle compressor, will activate releasing product into the atmosphere. However, if this valve is not operational or is incorrectly sized, there is a risk of the silo rupturing or the filter housing being blown off the silo roof. Incidents of this kind have occurred in the past.
It should be noted that while tankers have ‘on-board discharge units’ to avoid venting the tank via the silo, these systems rely on the experience of the driver to recognize when the silo is nearly full and to take manual control of this facility.
In an effort to prevent the above scenario from occurring, it is good practice to test the operation of the pressure-relief valve on a regular basis and, ideally, before each delivery. This is not always practical as it will require someone to climb to the top of the silo and this person must be qualified and equipped to comply with the Working at Heights Regulation 2005.
As there were 44,152 reported slips trips and falls in 2009/10, accounting for 36% of all reported industrial injuries to employees, and 28% of all fatal injuries to workers involved a slip, trip or fall incident, it is obviously essential to reduce the risk of accidental falls. To this end, most leading cement companies have introduced several adaptations to their tanker delivery fleets to reduce the need for drivers to climb on them, by providing ground-level air and electrical lines for coupling semi-trailers, as well as ground-level sampling points to allow drivers to provide their customers with product samples. Both of these avoid the need for ‘working at height’ to reduce the risk of falls, and since the tanker height is much lower than the height of a silo, any silo protection system should follow the same example.
The solution is available and relatively simple – fit an automatic monitoring and control shut-off system to the silo.
Auto-shut-off silo-protection systems
It is the build up of pressure that can threaten the environment, damage a silo and endanger site personnel or the public. Because of the nature and speed of this pressure increase, which could be due to any one of a number of faults, the safety control system must be automatic and fail-safe. It must respond immediately without the need for any human intervention.
At the very least, an auto-shut-off silo-protection system must consist of a pressure sensor, a high level probe and a pressure-relief valve, all linked to an auto shut-off control panel with outputs for control and alarm. It must be capable of being tested to ensure that all the major elements are working correctly before every delivery, without the need for an operator to have access to the top of the silo, ie ground-level testing.
The auto-shut-off system will control the silo inlet valve, closing it if a preset high pressure or high level condition occurs. If it fails to close the inlet valve and the pressure continues to rise, the pressure-relief valve will open to vent the excess pressure.
By exploring the individual components, it is possible to gain an understanding of how total silo safety with advanced ground-level testing is achieved, and how the six major areas of concern, as raised by the MPA in their guidance notes, can be eliminated, with the added benefit of reducing maintenance costs in situations where these systems are fitted.
Silo pressure sensor
In order to control the pressure in the silo it is essential to monitor it continuously. The pressure sensor module is the critical first line of defence, measuring the pressure in the silo as filling takes place. If this pressure exceeds the safe working pressure of the vessel the sensor must take action, activating alarms and closing the discharge valve in the fill pipeline.
Hycontrol have developed an innovative method for completing the ground-level test and checking the integrity of all the major components within the silo protection system. One press of a button before every delivery is all that is required.
Hycontrol’s patented pressure sensor, which is protected by a porous membrane, is electronically tested and cleaned in a single operation. It is activated by a small air supply connected to the sensor which applies a fixed pressure of approximately 90% of full range output directly to the pressure sensor face. This change in pressure is measured by the system and verifies correct operation over its full operating range. As the air escapes through the porous membrane at the end of the sensor tube it removes any build up of material. If the membrane is blocked or damaged and the air pressure cannot pass through, the system alerts the operator and does not allow filling to take place until the situation has been remedied.
This device requires air to test its functionality, and this is commonly taken from the air used to clean the filters, as it is readily available close by. An added benefit is that the sensor will not pass the ground-level test if the air to the filter is not switched on or is at an insufficient pressure, thus providing an additional safety check. This pressure sensor will eliminate uncontrolled discharge into the silo at the end of the delivery cycle, or the discharge of residual air into the silo, by automatically closing the inlet valve before over-pressurization can occur.
Inadequate flow through the filters
Silos that are pneumatically filled incorporate a filter on the silo roof which is sized for the peak airflow during filling. The most common filter system used is the filter bag or filter cartridge. Both require cleaning to remove the dust, which is usually carried out automatically either by reverse-jet (blowing air back through the filters) or mechanical shaking. It is extremely important that these filters do not lose efficiency due to blockages. The Hycontrol silo-protection system logs any high-pressure events which occur, providing a valuable record showing how often high pressure has been reached. This record is invaluable as it indicates that either the filters require maintenance or the tanker drivers are transferring powder at too high a pressure, both of which require action to prevent future risks of over-pressurization.
Overfilling of the silo
Overfilling of the silo is prevented by an integrated level control device, typically a capacitive or vibrating level probe that is designed to activate when the product reaches and buries the probe’s sensitive tip, indicating near-full capacity and that filling should stop.
Failure to stop filling can result in product release into the environment, blocked lines, blinded filters and potential damage to the pressure-relief valve.
The type of high level probe selected is also vitally important. Vibrating probes with a single diamond knife blade provide reliable high level switching for powdered materials without any need for calibration. Importantly, they have a ground-level test facility to ensure that the probe is operating and functioning correctly before every delivery. While overfilling a cement silo with cement can cause an environmental issue, the greatest danger is blinding of the filters, which can have catastrophic results. The Hycontrol system logs every high level event to allow operators to analyse their deliveries and improve their working practices.
Failure of the pressure-relief valve
If the pressure in the silo exceeds the maximum operating pressure allowed, the safety valve will open to atmosphere, releasing not only air but also product into the surrounding area. The valve is designed to protect the silo against physical damage and should be the last line of defence in a well-designed silo-protection system.
A common misconception is that by fitting a pressure-relief valve to a silo, the silo is then ‘safe’ and it is acceptable for the pressure-relief valve open on a regular basis. However, if a pressure-relief valve is venting to atmosphere it is primarily because the silo-protection system has failed and/or because the air can not escape to atmosphere quickly enough. Both of these scenarios need to be addressed as they could indicate a filter problem due to a blockage, incorrect filter size or air entering the silo is not being controlled by the tanker driver in the correct manner.
The Hycontrol pressure-relief valve has an integral test facility which can be operated from ground level. This physically lifts the valve at the correct pressure and confirms its operation as part of the ‘one-button, one-press’ ground-level test. Hycontrol’s pressure-relief valve has the added advantage of a local test button so that the valve can be opened for inspection and cleaning without the need for any special tools.
Next generation of silo safety
The new MPA guidance notes indicate that one of the major contributory factors to incidents of over-pressurization is poor maintenance, and that all equipment used in the tanker discharge/silo filling process must be properly maintained to ensure correct functionality. To date, this has not always been practical or possible, as the removal of pressure sensors and pressure-relief valves for valves testing and checking is costly and time-consuming and necessitates working at heights.
The new generation of silo safety systems from Hycontrol are fully compliant with the latest guidelines, allowing full testing of all primary elements before each delivery. Only when all these safety devices have passed the checks will the safety interlock allow the silo inlet valve to open, thus ensuring that no delivery commences without all elements functioning correctly. By fully testing the pressure-relief valve, high level probe and the pressure sensor, the new Hycontrol silo protection system offers greatly improved silo safety, peace of mind for site operatives and, as an added bonus, reduced maintenance costs to help the site’s budget.
For further information visit: www.hycontrol.com