Splicing Solution
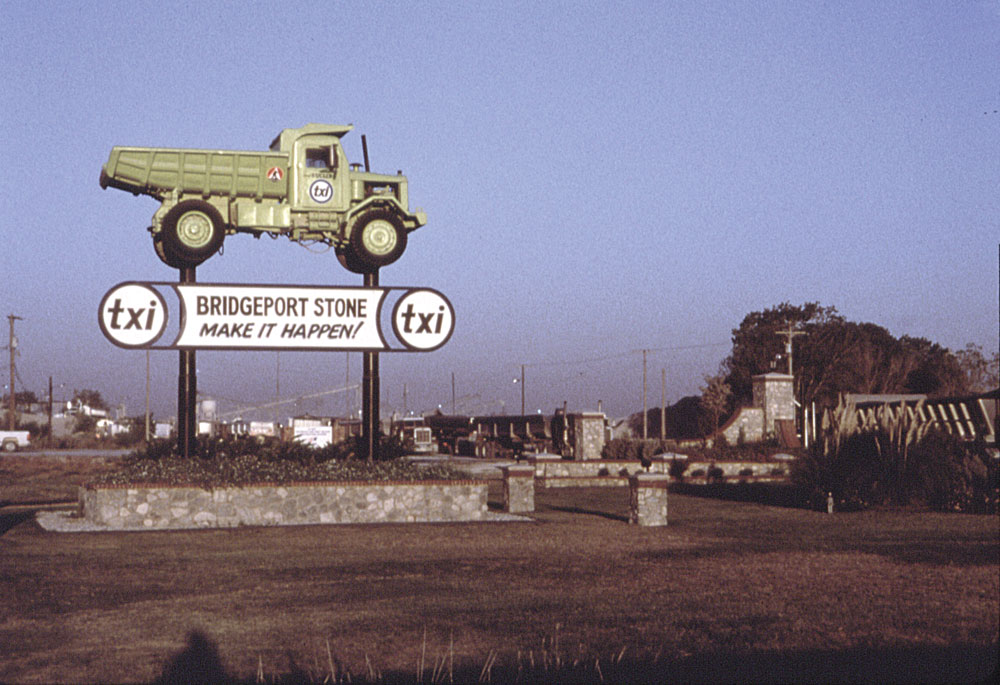
Texan quarry combats wet-belt splicing wear with abrasion-resistant alloy fasteners
Aggregate producers often find that producing clean crushed stone leads to the frequent replacement of mechanical conveyor-belt splicing, especially on conveyors carrying stone that is still wet from scrubbers and washing screens. One theory is that washing removes the fines and dirt that would otherwise serve as a cushion between the splicing and the stone’s sharp edges. Another theory suggests that wetness makes fines cling to the fasteners, coating them with grit which amplifies the stone’s abrasiveness. Yet another suggestion is that water enhances the cutting action of sharp-edged stones, similar to the way cutting oil enhances the efficiency of threading dies and metal drilling bits, or that the accelerated corrosion caused by the water is what hastens the splicing to wear out.
Whatever the reason, Bridgeport Stone in Texas, the flagship plant of TXI (Texas Industries, Inc.), one of America's largest producers of construction products, have overcome this problem by using a special bolted-plate belt fastener, resulting in the wet-belt splice life at the site being tripled. Production time and maintenance manhours that were previously lost to resplicing have also been recouped.
Ranked among the country’s 15 largest limestone quarries and employing over 100 people, Bridgeport, which is 200ft deep in places, extracts approximately 7 million tons of 350 million year old Pennsylvanian limestone a year. About 70% of production is processed into five sizes of aggregate ranging from 3/8in to 11/2in, with the remainder sold as sand, rip-rap and base material. Most of this output ends up in road and building construction within a 100-mile radius of the quarry, primarily encompassing the Dallas-Fort Worth Metroplex, with about half of it going to TXI’s cement, asphalt and ready-mixed concrete plants.
Aggregate production at Bridgeport is divided into two plants, one for concrete aggregate, the other for asphalt aggregate. At the concrete aggregate plant lorries and rail wagons are loaded by wheel loader directly from stockpiles. At the asphalt aggregate plant three overhead load-out bins straddle one side of an oval-shaped rail spur which loops around both plants. The bins are fed by a blending-tunnel belt that draws from five stockpiles of different aggregate sizes to funnel custom-blend orders into rail wagons or lorries passing underneath. In total, a typical day will involve loading 900 25-ton trucks and 70 100-ton rail wagons, although exceptionally busy days have pushed the truck-loading record to 1,130.
With volumes such as these, minimizing the belt resplicing workload is a high priority at Bridgeport. There are 82 belts in total with an average of two bolted-plate splices per belt which have the potential to consume a lot of maintenance time. Mining engineer/production co-ordinator Jennifer Hise says: ‘From shutdown to restart, replacing a bolted-plate splice will take two of us at least two to three hours, depending on belt width.’
Bridgeport’s conveyor belts range from 24in to 54in wide, typically of two- to four-ply rubber construction with mechanical belt fastener ratings of around 330 lb/in of width. Most are troughed at 35o, with the shortest being around 18ft and the longest about 3,150ft between end-pulley centres. Conveyor speeds typically range from 320ft/min to 550ft/min.
In the conveying sequence, two in-pit crushers reduce blasted rock to –5in, with rip-rap and/or base material being screened out when required. The remainder of the material is transfered on to two conveyors which deliver it to the asphalt and concrete aggregate plants. Here both material streams pass via rotating drum scrubbers en route to the surge piles. At the scrubbers –9/32in fines are screened out and sent to the nearby sand plant.
From the rotating scrubbers loads are wet to the point of being a slurry. In the concrete aggregate plant stone taken from the primary surge pile goes directly to a bank of three washing screens. Two screens remove –1in +3in material as aggregate product, while oversize material, which is literally dripping wet, transfers via a conveyor to a pair of secondary cone crushers. Discharge from these comes back through the third washing screen where any oversize material makes a return trip to the secondary crushers. From all three washing screens undersize material is conveyed to a secondary stockpile for lorry loadout while the –1in +3in aggregate product is conveyed to a bank of three logwashers then on to two final re-wash screens before being delivered, via a stacker conveyor, to the stockpile. Bridgeport say it is this multiple washing that gives them their premium product.
‘However, wherever belts carry wet material the standard mild steel belt fasteners that work so well on dry belts wear out more quickly,’ says senior master welder Jimmie van Hoose. ‘In many cases we found ourselves replacing the same splice three times a year, so resplicing tended to be my biggest problem.’
While visiting a trade show, Mr van Hoose mentioned the problem to staff on the Flexco stand and was informed of a possible solution — belt fasteners made of MegAlloy. This proprietary alloy, which is heat-treated to maximize hardness against wear, is one of six special metals available in Flexco’s bolt- or rivet-attached heavy-duty belt fasteners to help them work better in hostile environments. It was specifically designed by Flexco for high resistance to abrasion and as a much lower-cost alternative to stainless steel splices, which cost over six times the price of standard mild steel fasteners.
‘In all our highest wear areas, where we were resplicing three times a year, MegAlloy plates now last at least a full year,’ says Mr van Hoose. ‘They cost us about 85% more than standard mild steel plates but they end up saving about 38% of what three sets of standard plates would have cost over the same period of time. That saving is even better when you consider the maintenance time avoided on the two splices we didn't have to install — probably worth at least $240 to $360 in labour.’
Less resplicing also improves productivity. Of the concrete plant’s 12 conveyor belts, only three can be bypassed. Stopping any of the other nine belts stops the entire plant, so lengthy downtime can result in substantial loss of production and, consequently, revenue.
Apart from the benefit of fewer splice installations, the resplicing task is faster now that Flexco bolt-solid plate fasteners have been improved with new piloted bolts. In a typical bolt-solid plate installation, holes are drilled through the belt ends guided by a special template, then bottom plates and bolts are inserted from the underside of the belt. Top plates are then placed over the bolts protruding through the belt's top cover and secured with special tapered nuts, usually tightened with a special powered socket wrench.
The new piloted bolts feature a 6mm threadless shank at the tip of each bolt. This makes it possible to place the tapered nuts loosely on to the upward protruding bolts without the need to secure them in that position by hand-turning. The added shank length holds the nuts in place until the wrench is applied. By narrowing the tip of the bolt, the threadless shank also quickens the usually blind insertion of the bolts from the underside of the belt.
As tightening compresses the plates into the belt cover, the tapered bottom on the nuts positions them into matching countersunk pockets formed into the plates. This results in a flat, low-profile splice that is compatible with belt cleaners and skirtboards designed for fastener-friendly operation. Before tightening, a strip of rigid nylon tape is threaded between the plates and belt surface along the top and bottom of the tightly butted belt ends to prevent the belt ripple that would otherwise result from plate compression. The tape also helps to protect the belt ends against moisture and prevents fines from sifting through the splice.
Jimmie van Hoose is continuing to experiment with Flexco’s stainless steel fasteners in the most demanding areas, and he uses them exclusively in the sand plant because of the extremely high levels of abrasion and corrosion. Two of the six sizes of Flexco bolt-solid plate fasteners offered in MegAlloy now account for about 70% of the fasteners in use at Bridgeport.
Targeting specific belts for conversion to MegAlloy splices was at first intuitive at Bridgeport, but is now becoming strongly influenced by a relatively new MP2 maintenance database management program. This program builds histories of when various repairs were done and when to expect future repairs. ‘When certain repairs are becoming too repetitive we either start looking for a superior repair product or change our repair procedures,’ says Mr van Hoose.