No Stone Unturned
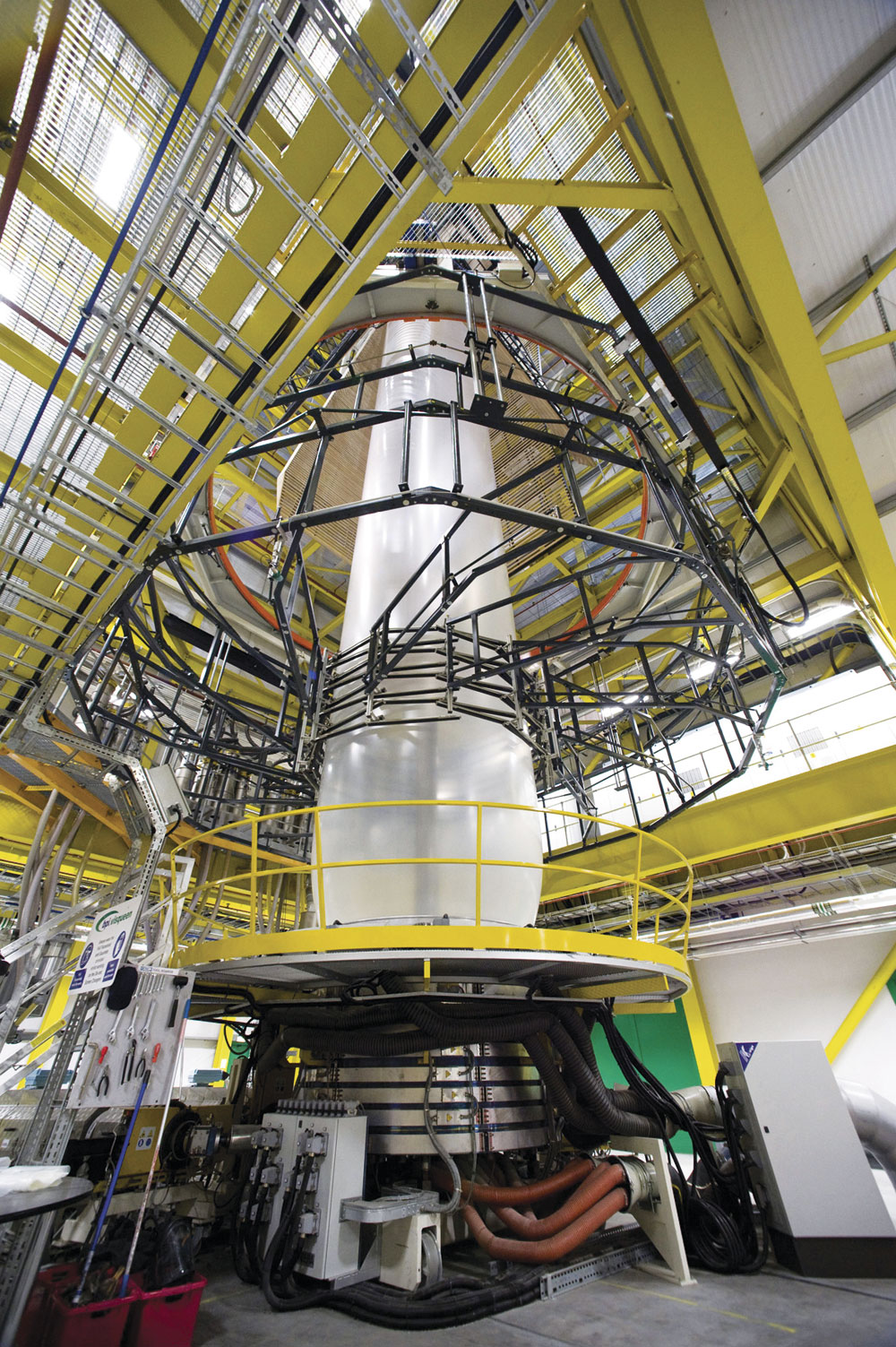
With the advent of new technology, a whole range of next-generation polythene packaging solutions are now available, as David Khanna, sales director with bpi.visqueen, explains
For all those involved in quarry management, the quest for better margins, greater customer satisfaction, enhanced productivity and improved environmental credentials is a relentless pursuit. In order to achieve these goals, it is necessary continually to look at areas such as extraction methods, production techniques and product quality, to see where refinements can be made. But when was the last time you reviewed your packaging operations? If it has been some time, the reality is, you could be missing a trick.
Packaging, like so many areas of modern quarry management, has evolved enormously over recent years. With the advent of new technology and by distilling their hard-won expertise, many packaging suppliers now offer access to a whole range of next-generation solutions that provide next-generation benefits. One supplier helping to lead this evolution is British-based bpi.visqueen.
‘There’s no denying the fact that, from a packaging perspective, the aggregates sector is a mature market,’ commented David Khanna, sales director (Construction Sector) at bpi.visqueen. ‘Solutions such as sacks, pallet stretch hoods and pallet shrink hoods have all been around for some time and have served the market’s needs admirably for many years.
‘However, bpi.visqueen have never been the kind of business to adopt an ‘if it isn’t broken, don’t fix it mentality’. We’re committed to driving our success, and that of, our customers by taking these effective solutions and making them even better.’
Evolving solutions for an established market
Evidence of bpi.visqueen’s commitment to creating value-adding packaging for the aggregates sector can be found in abundance. By drawing upon the resources and extensive knowledge base they enjoy as a business with decades of experience and that currently produces well in excess of 100 million sacks a year, the manufacturer has become a key exponent of new concepts such as packaging downgauging.
‘Downgauging is like all the best ideas – simple, yet highly effective,’ explained Mr Khanna. ‘In essence, it entails the creation of packaging that offers more from less. More performance but from less material, which means major reductions in the volume of packaging used and subsequent waste created.’
While the principles behind downgauging packaging are simple enough, the actual process of creating it is anything but. In order to develop these solutions, bpi.visqueen have had to draw upon their considerable expertise, the very latest polymers and cutting-edge extrusion technology – including equipment housed at the company’s Ardeer site, the recent focus of a £12 million investment.
By combining these factors, the company is able to produce polythene film for conversion into pallet stretch hoods, polythene sheeting, open-mouth sacks and tubular sacks on the reel which offers all the performance of conventional products but from a film profile that is up to 25% thinner.
These thinner films, which entail no sacrifice in performance, allow users to create packaging using less film by volume and reduce the amount of packaging waste they create. This reduced waste, in the case of bpi.visqueen’s downgauged products, is also 100% recyclable.
But the green benefits do not end there. As downgauged films are thinner, manufacturers such as bpi.visqueen can also accommodate more product on a standard reel. This greater yield per reel reduces delivery requirements and, as a result, associated vehicle emissions.
There are even commercial advantages to be enjoyed too. ‘Downgauged packaging’s capacity to deliver more from less is as beneficial from a commercial point of view as it is for the environment,’ said Mr Khanna.
‘For instance, the greater yield of film offered by reels of downgauged packaging allows users to create more sacks, pallet stretch hoods or other forms of packaging with fewer stoppages for reel changes. Not only does this maximize machine and operator time, but the improved efficiency also tends to lower per-unit packaging costs.
‘On top of this, the need for fewer film deliveries reduces associated administrative demands, such as the need to order film, to deal with deliveries at goods inwards and to process related paperwork. This frees up time and resources which can then be spent on other higher value or more profitable activities.’
Sacks of innovation
Aside from downgauged packaging, bpi.visqueen have also created innovations such as their Ventisack product.
‘Ventisack was initially created to meet the needs of the cement industry,’ explained Mr Khanna. ‘It sets out to address two important packaging challenges that are specific to the sector.
‘First, that cement is packed on high-speed lines where air needs to be able to vent from the packaging quickly. And secondly, that cement is often stored outdoors at the mercy of the elements and at risk from water ingression.
‘Ventisack tackles both of these challenges admirably. It’s a next-generation, high-strength and tear-resistant co-extruded FFS film that can be used to create sacks with a revolutionary back seam. This unique seam allows air to vent but still has the ability to keep the weather, water in particular, out.’
But these impressive fit-for-purpose characteristics are just the start. There are also other major benefits to Ventisack which are helping to drive its success and industry popularity.
‘Modern cement packaging is no longer just about function,’ said Mr Khanna. ‘It’s also about form. We live in brand-conscious, consumer-aware times and, as such, packaging needs to offer strong aesthetics and an immediate visual impact. This is especially true when packaging products are sold in competitive sales environments, such as merchants’ yards.’
For this reason, bpi.visqueen have gone to great lengths to ensure Ventisack offers exceptional design possibilities and print qualities. It can be printed in up to four colours and, perhaps even more notably, with 360° print coverage around the entire film tube. This means no wasted areas of white space along the sidewalls and no lost opportunities to promote brand or marketing messages.
In addition, it is natural to expect any new product to be a greener product, and again Ventisack does not disappoint. It is made from 100% recyclable polythene, which means that the resultant sacks are far easier to recycle than those made from paper and a liner. In addition, Ventisacks are particularly suited to downgauging.
Recognizing the different and diverse requirements of cement producers, Ventisack film is now offered in a variety of sizes and thicknesses, allowing sacks from 300mm to 650mm in diameter, 400mm to 1,200mm in length and 90–200 microns in thickness to be created. The venting characteristics can also be tailored to suit specific customer needs, while features such as embossing can be included to provide anti-slip properties, if desired.
‘Ventisack is a prime example of the possibilities now offered by modern packaging to the cement or aggregate producer,’ concluded Mr Khanna. ‘But we’re nowhere near the zenith point yet. In bpi.visqueen’s case, the immense versatility of polythene as a material, coupled with our expertise, our use of increasingly advanced manufactured technology and our staunch commitment to R&D, means there are many, many avenues still to explore.
‘No matter how capable today’s solutions are, the best is still to come.’
For further information visit: www.bpipoly.com