New field conveyor system for Swinderby Quarry
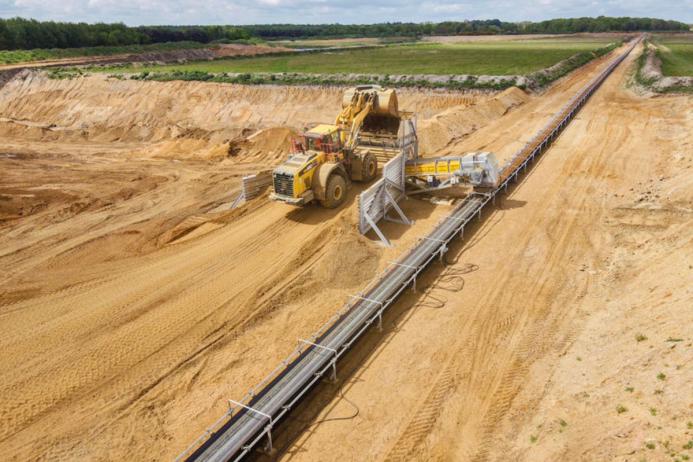
First published in the March 2023 issue of Quarry Management
CEMEX invest in a Canning Conveyor system to help reduce CO2 emissions
Last year CEMEX made a sizable investment in a new field conveyor system at Swinderby Quarry, in Lincolnshire, which will make a significant contribution to reducing diesel fuel use and CO2 emissions at the site. The system, which includes a 20-tonne feed hopper, several field conveyors and a radial stockpiler, has a total length of 1,600m and will carry sand and gravel from the extraction area directly to the site’s processing plant.
Designed, manufactured, supplied and installed by Worksop-based Canning Conveyor, the 900mm wide modular stringer field conveyor system offers ease of transport and assembly on site and operates at up to 400 tonnes/h with a 900mm wide belt carrying material with a density of up to 1.6 tonnes/m3 and a maximum lump size of 150mm.
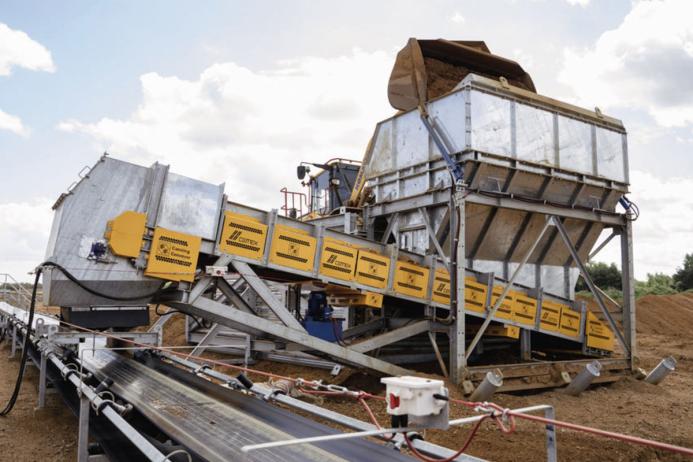
The system comprises a total of five separate conveyors that are fed via a 20-tonne feed hopper unit equipped with wheels and a towing point to allow for movement around the site. The hopper features a pivoting grizzly screen with 150mm apertures to separate oversize from the feed material. Actuated by hydraulic cylinders, the grizzly is able to eject the collected material when necessary and can be unhooked and separated from the hydraulics for transportation.
Designed for robustness and torsional rigidity, the field conveyor’s high-strength modular stringer sections are fabricated from rolled hollow-section steel. Each section is 3m in length with bolted connections to make the design easy to assemble and maintain. Moreover, all the modular sections have been designed to use common parts throughout, thereby reducing the need to keep high stock levels of spares.
A simple feed boot is fitted at each conveyor tail, whilst a chute at the head of the conveyor includes a crash-box design to help reduce wear while maintaining efficient discharge without spillage. A loop tensioning device is incorporated at the head end of each conveyor, with a standalone gravity take-up (GTU) included for conveyor CV2. At the head end a gradient section has been incorporated to ensures a smooth transition from the field conveyor. Primary and secondary scrapers are fitted at the head drum of each conveyor to ensure efficient belt cleaning, whilst ploughs prevent any build-up on the tail drums.
The primary conveyor, CV1, is a wing conveyor configured both for ease of movement and to facilitate a reduction in length if required. This feeds on to CV2 which is 900mm wide by 900m in length and incorporates a moveable feed section to allow multiple loading points. Driven by a 90kW drive, CV2 is made up of 3m modular sections and is fitted with primary and secondary scrapers to maximize cleaning. A heavy-duty tail-end loading section is fitted with impact rollers to reduce the impact of the material with the tail pulley.
CV3, which is 390m in length, receives material from CV2 and feeds on to CV4, which is 117m in length and discharges on to the radial stockpile conveyor, which is 100m in length and can be inclined up to a height of 5m. With a continuous feed, this 900mm wide conveyor can create a kidney-shaped stockpile of 7,000 tonnes.
As CEMEX move into the next phase of extraction at the site, the new conveyor system will minimize the use of dumptrucks, saving a projected 300,000 litres of diesel fuel per year, as well as reducing noise and dust at the quarry.
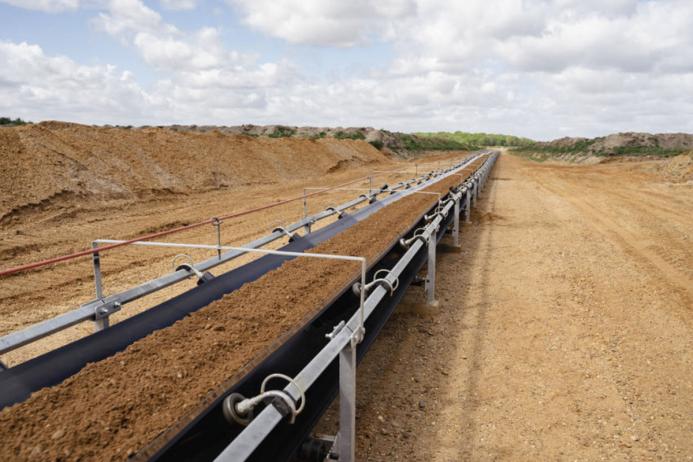
Steve Sheller, CEMEX’s head of business development for West Europe Materials, commented: ‘Swinderby is a crucial site in our portfolio; it supports our customers in the Birmingham metro-market and wider Midlands area and has a considerable reserve potential of more than 10 million tonnes. We are, therefore, investing heavily in the site to ensure it can meet demand for years to come, while also achieving the sustainability targets set as part of our Future in Action global strategy.
‘By using a conveyor, we’ve calculated that we can cut CO2 emissions by around 50% per tonne of aggregate, compared with working the next phase of the quarry using mobile plant, alongside further efficiency and cost savings. Considering forecasted production figures, this is a total CO2 saving of approximately 74%.’
Additionally, a new processing plant is being installed at Swinderby, which will nearly double the site’s production capability. This investment is due to be completed early this year and, together with the new conveyor system, will futureproof the site, allowing continued supply to the key Midlands market, whilst meeting increased customer demand. Further investment opportunities for the site are also being explored regarding renewable energy sources. For more information, visit: www.canningconveyor.co.uk
- Subscribe to Quarry Management, the monthly journal for the mineral products industry, to read articles before they appear on Agg-Net.com