Mobile Harbour Equipment
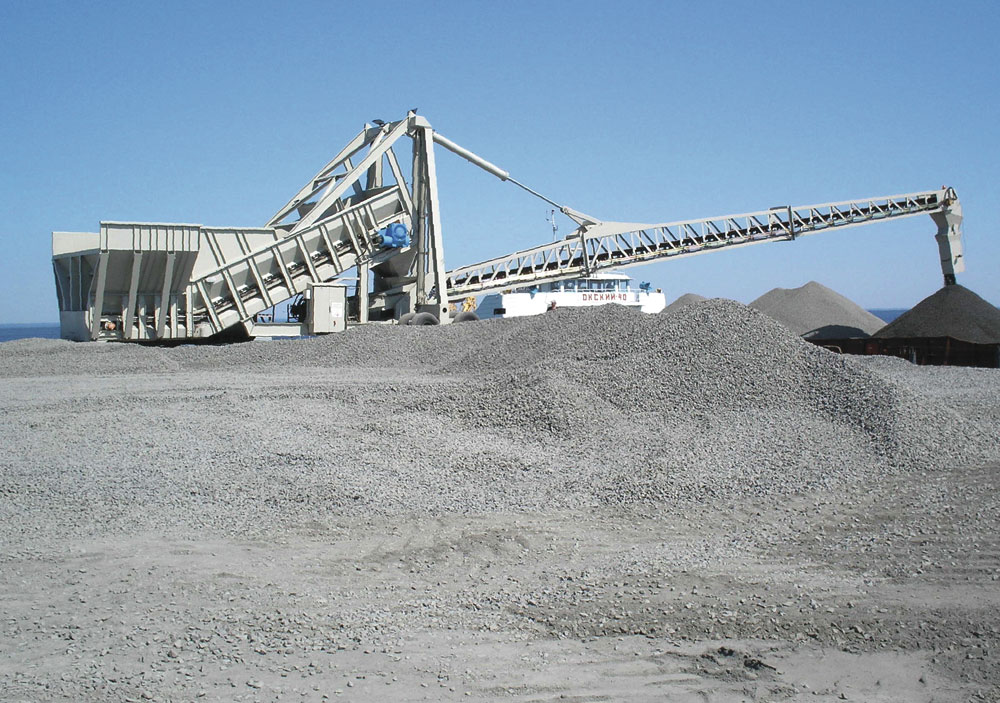
The Aumund Group, including Schade and B&W Mechanical Handling, are developing and diversifying their activities throughout the ports and terminals industry worldwide with major new projects involving bulk material export, storage and handling, including dust-controlled equipment
By Andrew Mitchell, managing director, B&W Mechanical Handling Ltd
Mobile shiploaders offer an attractive option for the export of dry bulk cargo direct from truck to ship, eliminating costly fixed-conveyor installations and port infrastructure, and allowing almost any berth to be utilized for bulk exports.
By combining Group resources, Aumund are able to offer a comprehensive range of solutions, including the B&W surface-mounted Samson feeder, Stormajor mobile radial-boom stacker and mobile shiploaders, along with the established range of Schade stacking and reclaiming solutions for enclosed dust-controlled storage applications.
Samson surface feeder
By incorporating a Samson surface feeder into the shiploader as a single mobile unit, almost any bulk material may be received direct from tipping trucks, providing integral buffer storage and controlled-rate discharge to minimize truck turnaround times.
As illustrated in figure 1, for maximum performance twin Samson feeders may be mounted to a single shiploader chassis to achieve loading rates from truck to ship in excess of 2,000 tonnes/h.
With the addition of powered travel facilities, the high-performance mobile shiploader offers a viable alternative to conventional fixed installations.
Reacting to the demands of clients, B&W have developed their mobile shiploader with facilities specifically geared to the handling of cement clinker – an extremely aggressive and dusty material.
The mobile shiploader shown in figure 2 is one of two units delivered to the port of Gizan in the kingdom of Saudi Arabia. It is dedicated to the export of cement clinker and typically loads ships of Handymax size at rates of up to 1,200 tonnes/h.
In this project clinker is produced at the cement plant of Southern Province Cement, located some 50km inland, and transferred to the port by a fleet of tipping trucks working on a merry-go-round principle. At the port the clinker is stored locally and transferred from storage to the shiploader, mainly by loading shovel.
The equipment includes an integral Samson surface feeder unit mounted to the machine chassis and designed to accept material by loading shovel or direct from dumptrucks bypassing the local storage facility.
This is a fully mobile unit with powered travel and an independent on-board diesel genset, thus eliminating the need for any permanent conveyor system, shore-side power supplies or fixed port infrastructure.
As illustrated in figure 3, the mobile shiploader has been extensively developed to include full dust-control measures, such as the Cascade chute, to control dust pollution down to the hold floor. In the application shown, the equipment is handling kaolin at a peak rate of around 1,000 tonnes/h direct from tipping trucks via twin integral Samson feeder units.
In this case, simple, flexible, PVC-clad enclosures are provided for the Samson units and the out-loading boom, with no fan-assisted or other type of dust-extraction system, even though kaolin is an extremely dusty material and the equipment is operating at the Port of Par, which is located in an extremely popular tourist area of the UK.
By virtue of the handling characteristics of the Samson feeder, material is effectively drawn into the Samson body by the forward moving belt, thus eliminating free fall and substantially eliminating dust generation at source.
For receiving material from tipping trucks, the Samson surface feeder offers a flexible and economical alternative to conventional underground pits or hoppers, with the added benefit of much-reduced dust generation and complete flexibility of location irrespective of local ground conditions. Being surface mounted, the Samson unit can offer real cost advantages in a port environment where the normally high water table makes conventional deep pits extremely expensive to construct.
Stormajor radial-boom stacker
For barge-loading operations the B&W Stormajor radial-boom stacker (fig. 4.) is proving popular in a number of diverse industries and different global locations. Thanks to the long outreach of the cantilevered out-loading boom, the traditional B&W Stormajor can operate on a simple river berth and discharge direct to barges moored to a pontoon or similar berth, thereby eliminating the need for any permanent civil works and providing maximum operational flexibility.
For importation in the port or bulk terminal, the B&W mobile Stormajor radial-boom stacker offers considerable flexibility and can be used for stacking, barge loading and rail-car loading, making it an extremely versatile piece of equipment.
Figure 5 shows a new machine constructed for the port of Neuss Düsseldorf, in Germany. The Stormajor receives imported iron ore from bulk carriers via grab crane and loads directly into rail wagons at a controlled rate. In this application, the Stormajor features a continuous weighing system to monitor the contents of each rail car in order to avoid overloading.
Figure 6 shows a similar machine loading rail cars direct from tipping trucks at a siding in northern France. In this case the Stormajor is equipped with powered travel capabilities, allowing the unit to move along the wagon train and eliminating the need for a locomotive, thus saving on operational costs while maximizing flexibility.
A second new and significant order, being manufactured for Basalt AG of Germany but destined for Russia, is shown in figure 7. This Stormajor unit will be used to export hard stone (gabbro), which is delivered to the shipping berth in large off-highway dumptrucks.
This is the largest Stormajor to be designed by B&W to date and it incorporates a large Samson 1600-Series feeder plus a 30m long outloading boom with sufficient outreach to load barges moored to offshore dolphins.
Developed for the mining and cement industries, Samson 1600-Series feeders are designed to handle as-mined rock with lump sizes up to 500mm, acting as primary feed units for crushing or similar primary intake plant. Available with holding capacities up to 100 tonnes in mobile configurations, the Samson 1600 expands the application range of the Stormajor to extreme-duty operations in the most arduous conditions.
In this particular case, the equipment will be designed and built for operations in extremely low temperatures (down to –40°C). This will require specialized construction techniques and component selection to ensure reliable operation.
At the opposite extreme, Salgaocar Mining Industries of India have chosen the Stormajor for the loading of iron ore on to barges at a rate of 1,250 tonnes/h in temperatures up to 45°C.
A total of six Stormajor units were delivered for operation on various river berths in and around Goa. Since there are no deep-water ports nearby, the iron ore is transported by self-propelled barges to a floating transhipment facility anchored offshore, where, typically, vessels up to Panamax size are loaded.
In this application the Samson 800-Series feeder section, with its extended loading area, receives material from up to three tipping trucks simultaneously to achieve the required average loading rate. Figure 8 shows one of the units during commissioning.
Eco-Hopper
For bulk material imports, the B&W Eco-Hopper offers a solution for the grab-discharge handling of heavy and abrasive materials, such as cement clinker, or light and dusty materials, eg biofuels.
The hopper includes integral dust filters mounted between the inner and outer cones around the periphery of the hopper inlet. Combined with flexible baffles directly below the reject grill, dust is contained within the hopper bowl and fugitive emissions are minimized to reduce environmental pollution.
The Eco-Hopper is available for direct discharge to a belt conveyor, as shown in figure 9, or with an Aumund dust-controlled truck-loading spout for direct discharge to tipping trucks.
All of the above examples of B&W Aumund Group products are designed to offer port or terminal operators effective materials-handling solutions, while providing maximum operational flexibility and minimum investment risk.
For further information, contact B&W Mechanical Handling Ltd on tel: (01353) 665001; fax: (01353) 666734; email: sales@bwmech.co.uk.