It’s In The Bag At Scorton
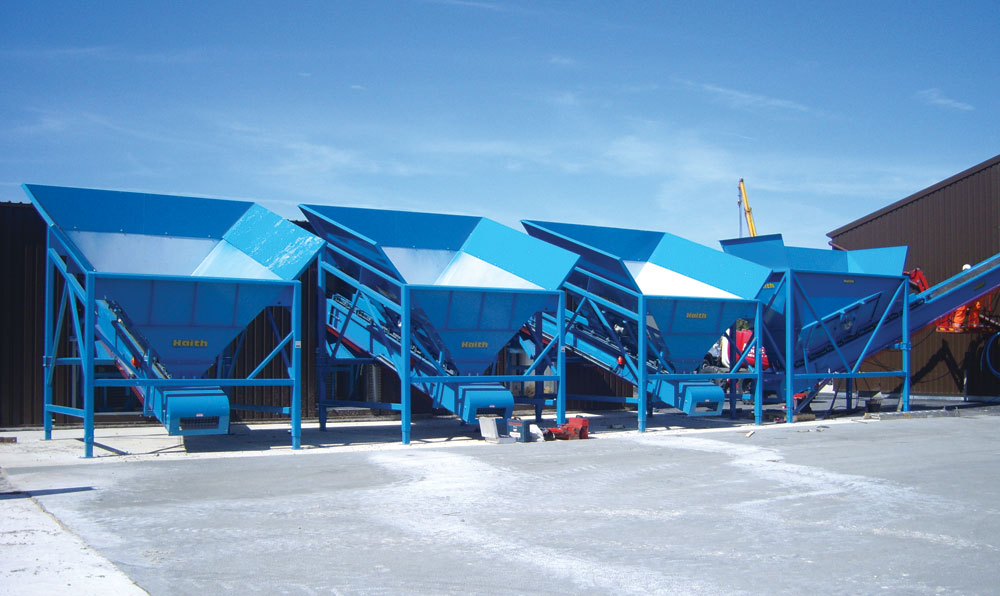
Haith supply new form, fill and seal bagging line for Tarmac Trupak
Supplying a comprehensive range of quality products in varied pack sizes to both trade and retail stores, Tarmac Trupak are the UK’s leading suppliers of pre-packed building and decorative aggregates.
At the company’s new site in Scorton, North Yorkshire – which now combines the business from two other Trupak plants, one at Blaydon and the other at Farnham, which closed due to the expiry of planning consent – Trupak bag a full range of building and decorative aggregates for delivery to builders’ merchants, DIY stores and garden centres throughout the North East.
With the help of Haith Industrial, Trupak transferred the existing bagging line from the Blaydon plant to Scorton, where the system was reinstalled along with a new control panel, bag-kicker transfer conveyor and weigh conveyor. However, for Scorton to maintain the combined level of business achieved through the Blaydon and Farnham sites, a second bagging machine was needed to meet the required level of output.
Therefore, a brand new form, fill and seal bagging line was also installed at Scorton, together with a new robot for palletizing the bags. Haith Industrial sourced the new bagging machine from Premier Tech in Canada, based on the success of a previous Premier Tech machine installed by Haith at Trupak’s bagging plant in Sevenoaks, Kent.
Scorton’s Premier Tech line
Material is fed to the new Premier Tech bagging line at Scorton via a 10m3 end-loaded bulk holding hopper equipped with a 14.3m long x 0.6m wide discharge conveyor. The Premier Tech FFS-200 bagging machine was supplied with a volumetric feeder to provide an automatic horizontal form, fill and seal process complete with dust-collecting ports. In this application, the line can produce 25kg bags of aggregate at the rate of 1,200 bags per hour.
The FFS-200-series horizontal form, fill and seal bagging system makes its own bags from rolls of pre-printed, center-folded polyethylene film. The horizontal configuration allows the use of a large film roll, which provides many hours of continuous operation. The filled aggregate bags are weighed on a standard, totally enclosed Haith belt weigher mounted on a set of four load-cells.
A 2.0m long x 0.45m wide transfer/kicker rubber-belt conveyor sends the bags to a flattening conveyor. The flattener has three powered rollers driven by a shaft-mounted geared motor, all housed within a common frame and supported on adjustable legs fixed to the conveyor. The bags then continue on to a powered-roller pick-up table ready for robot palletizing. Reject bags from the kicker conveyor go to pallet waste trays.
A Haith-Kawasaki ZD 130-S robotic stacking machine is used to stack the 25kg plastic bags at a rate of up to 20 bags per minute. Fresh pallets on which the bags are stacked are issued from a pallet magazine that holds 15 pallets measuring 1,200mm x 1,000mm x 100mm. Once stacked with bags, the pallets travel along and accumulate on 8.0m long x 1.3m wide conveyor featuring heavy-duty powered rollers, seven geared motor drives along its length and sets of control beams on each of the powered sections. From here, the full pallets are collected by forklift truck and taken to storage.
The Premier Tech bagging line control panel utilizes a PLC controller for full automatic or manual control. To ensure operator safety, the robot stacking cell compound is protected by light guards across each of the forklift truck access openings, and two man-access gates fitted with Castell key systems are also provided. There is also a compound guard unit with two man-access gates fitted with Castell key systems interlocked into the panel for the bag kicker and flattener.
Moving Trupak’s Blaydon bagging line
Haith also stripped out the existing bagging line at Tarmac Trupak’s Blaydon site and transferred it to Scorton, where it received upgraded wiring, a new control panel to control the new bag kicker, and a new transfer conveyor and weigh conveyor.
The bagging line itself features a Haith 10m3 end-loaded bulk holding hopper with a 7.2m long x 0.6m wide discharge conveyor. This sends material to a high-throughput Haith 10–50 bagging machine suitable for use with granular or fibrous materials. A manually set control gate is fitted to the mouth of the hopper and a pneumatic trickle gate is fitted over the head pulley to reduce material flow for topping up. Rubber skirts are fitted around the hopper and an automatic control system is used to start/stop bag filling and to clamp/unclamp the bags. A pair of cut-off doors is fitted above the bag clamp to reduce the in-flight material and increase bag fill accuracy. Material is fed through the machine by a rubber belt conveyor, which is driven by an adjustable-speed geared motor unit.
An auto infeed device automatically presents the filled bags to a Saxon SH1000 continuous hot air heat sealer. The weigh belt conveyor consists of another standard Haith totally enclosed type, mounted on a set of four load-cells and controlled by a single controller with LED readout. The readout is fed into the 10–50 machine’s PLC control system for in-flight material adjustment. Bags then travel along a 3.6m long x 0.45m wide bag transport conveyor to a palletizing robot that formed part of the existing line.
This reinstalled and upgraded bagging line operates at a rate of 600 bags per hour.
Bulk bagging
Haith also installed a bulk bagging facility at Scorton. Three Haith 10m3 end-loaded bulk holding hoppers, each with a 7.2m long x 0.6m wide discharge conveyor, serve three Haith bag support frames for loop or tunnel bulk bags. The facility is made from channel and box-sections with the inner frame having two up-turned channel sections to support the bags. This frame is also fitted with four wheels, which run on the inside of the outer support frame. Also fitted to the inner frame is a manually operated screw jack to adjust the position of the bag relative to the floor and feed conveyor. A load-cell fitted within this mechanism is wired to the weigh controller, which stops the feed conveyor at the pre-set weight. The programmable controller has an LED readout showing the weights and settings.
Commenting on the facilities at Scorton, Tarmac Trupak director Cliff Ogden said: ‘The new equipment is working very well. We also took the opportunity to build some ‘just-in-time’ production features into the bagging process, which includes the pre-loading of parked trailers so that the delivery HGV tractor only has to carry out a trailer swap (ie swap an empty trailer for a pre-loaded trailer). We are very happy with the new equipment installed by Haith Industrial and the overall operation of the new site, which is achieving all the designed production efficiencies.’