Intelligent Installation
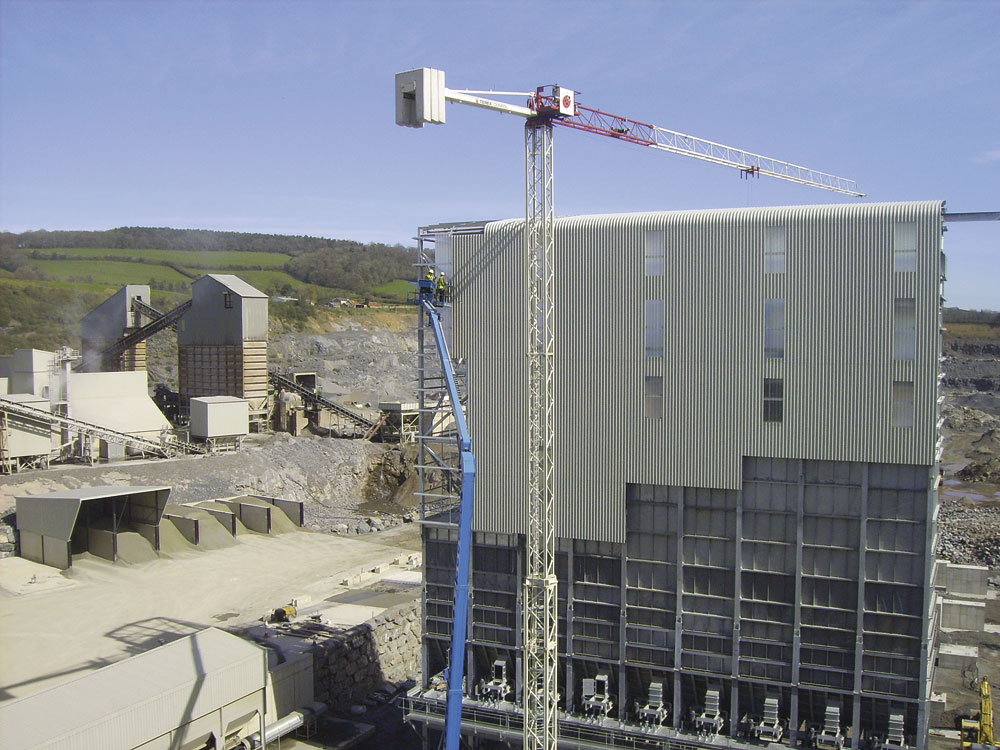
Centristic Ltd utilize innovative design and installation techniques for major replant at E&JW Glendinning’s Linhay Hill Quarry
Established in 1958 and now employing over 230 people, E&JW Glendinning are the largest independent suppliers of quarried and concrete products in Devon and Cornwall. The company’s Linhay Hill Quarry, near Ashburton, Devon, is a primary producer of limestone products in the area, with an output of around 500,000 tonnes per year.
In November 2009, bespoke materials handling equipment providers Centristic Ltd were awarded a contract by E&JW Glendinning to design, build and install a new screen house and dry storage bin system capable of handling limestone direct from the quarry face.
This would replace the quarry’s existing plant, which is around 30 years old and sits on top of valuable limestone reserves. As Glendinning were looking to release these sterilized reserves, it was decided to locate the new plant on a lower level at the extremities of the quarry floor.
Whereas the old plant was housed in two separate buildings, one for coarse and one for fine materials, the new plant is contained within a single building with a substantially smaller footprint. Moreover, all conveyors and walkways are now fully interlinked within the building, providing a safe working environment and allowing for ease of maintenance.
Plant design
The new plant has been completely designed using the 3D package Tekla. This has allowed a far greater degree of information and visualization to be passed on to the customer during the design process.
Centristic have taken drawings from equipment supplier Metso Minerals and created 3D models for use in the design process. This allows access and clearances to be precisely modelled and provides an increased levels of accuracy in areas where items of equipment interface with one another.
Centristic have taken part in several approval sessions with the engineers and maintenance teams at Glendinning, where they have been able to demonstrate the entire model to gain an input into the design and to help with the approval process.
The use of this type of software has provided many benefits throughout the design and production process. For example, material lists are now compiled much more quickly and accurately, and nuts and bolts lists are generated automatically.
The Tekla program is also capable of generating DSTV data for use by drilling lines and profilers. This, in turn, ensures that materials are delivered to site with the correct holes and cut-outs already in place, thereby minimizing exposure to human error and reducing the amount of time spent on on-site fabrication.
One of the major benefits, however, comes into focus during on-site erection of the plant. Due to the time spent in generating the model, far fewer clashes and missing holes are experienced than would generally be the case in a typical bespoke erection contract. Moreover, the assembly lists and drawings that are generated are also easier for the site teams to understand, and the 3D views allow for quick and easy interpretation of the assembly details.
Centristic maintain a viewing copy of the software on site, allowing site manager Mark Hewett to examine the model and provide immediate answers to questions that previously might have resulted in an enquiry to the drawing office or further on-site site discussion.
Installation
Perhaps the key difference and most original installation technique employed on this project, compared with other similar schemes, was the use of a hired-in tower crane throughout the building process. With a lifting envelope sufficient to cover all parts of the construction site, this meant that once the planning and design work had been completed, the entire build could be conducted from a single tower crane location.
Having decided upon this method of construction, a variety of tower crane types/suppliers were reviewed and the most fit for purpose was found to be the Terex CTT 51 Comedil – a remotely controlled crane measuring 40m in height and offering a 40m outreach (2-tonne load capacity out to 20m and 1-tonne load out to 40m).
This provided the erection team with complete flexibility and control over the movement and installation of any component part, as the crane operator was in close proximity to the job site and had an unrestricted view of any structure or equipment that was being fitted. Moreover, with the tower crane remaining in a single, fixed location throughout the build project, this method is said to be considerably more cost-effective than the traditional alternatives.
In addition, working in conjunction with the tower crane were two special work platforms/bays, each measuring 3m x 2.5m and providing a safe working load capacity of 0.5 tonnes, to avoid any issues regarding confined-space working or other hazardous construction practices.
Designed by Centristic and equipped with all-round handrails and safety harness points, these platforms could be lifted into position, as required, by the tower crane and relocated as the construction progressed, thereby providing a much safer working environment for the site engineers at each stage of the project.
A full report on the replant at Linhay Hill Quarry will be featured in a future issue of Quarry Management. In the meantime, for further information contact Tom Jones at Centristic Ltd on tel: (01626) 834310; email: tom.jones@centristic.co.uk; or visit: www.centristic.co.uk