Going With The Flow
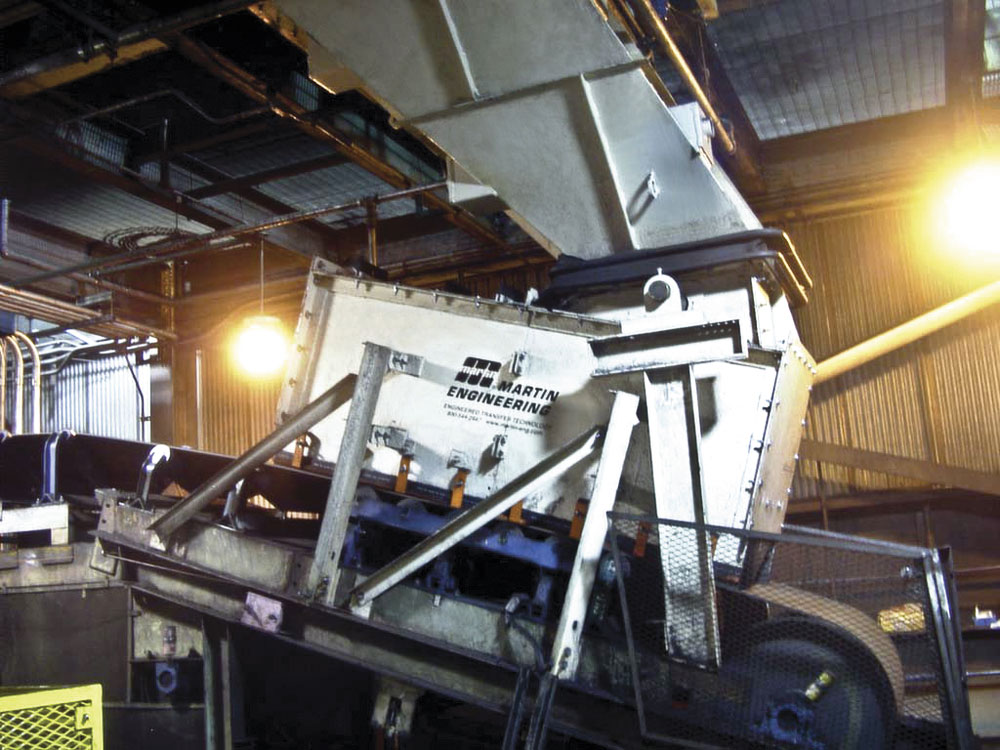
Custom-designed transfer chutes from Martin Engineering help improve conveyor loading and reduce blockages
Bulk materials handling specialists Martin Engineering have developed their own custom-engineered transfer chutes designed to help deliver better control of materials, from the time it leaves the conveyor discharge pulley unit until reaching the receiving belt.
According to the company, by managing the speed and direction of the materials, Martin Inertial Flow Transfer Chutes can minimize the tear and wear on liners and belts whilst containing the dust and spillage that can often happen at transfer points.
The engineered flow chute features special geometries that capture and concentrate the material steam as it travels through the tube. Every design, however, is tailored to suit the specific material characteristics and conveyor systems of the individual customers, rather than using stock products and attempting to make them work.
The inertial flow transfer units are said to provide the dual benefits of minimizing aeration and preventing build-up within the chute. This is particularly important when dealing with combustible materials.
‘Transfer points should never be a production bottleneck,’ said Justin Malohn, product development manager at Martin Engineering. ‘By testing the customer’s specific bulk materials and applying those properties as the initial step in chute design, we can develop a transfer that meets capacity while minimizing the potential for build-up and chute plugging.’
Martin Inertial Flow Transfer Chutes also incorporate replaceable liners, allowing operators to unbolt the enclosure for simplified replacement of worn components without confined space entry.
Engineered flow transfers
Engineered chutes typically employ a ‘hood and spoon’ transfer, with the hood discharge chute at the top of the system and the spoon receiving chute placing material on to the belt being loaded.
Martin Engineering components are custom designed to suit the characteristics of the conveyed product and the chute construction specification. ‘The hood minimizes the expansion of the material, directing it downwards,’ explained Mr Malohn. ‘The spoon provides a curved loading chute for a smooth line of descent, consistently feeding the material at a specific speed and direction to minimize impact in the loading zone.’
The aim is to confine the material stream and reduce air entrainment, while directing the moving materials on to the receiving belt with minimal impact. Successful designs reduce spillage, abrasion, dust and premature wear. In addition, this control helps ensure that the product is center loaded on to the belt, avoiding mistracking and fugitive material.
To achieve the optimum hood, spoon and settling area, Martin Inertial Flow Transfer Chutes are designed using 3D computer-based flow and modelling software to define the geometry. ‘The direction and force of impact should maintain as much momentum as possible, ideally with an impact angle of no more than 8-12º ,’ said Mr Malohn.
Designers use detailed information about the specific material characteristics and the parameters of the conveyor system itself, including the feed system, belt properties, support structure and transfer distances
Martin Engineering have in-house capability to perform comprehensive bulk material testing to obtain critical friction values, using customer-specific materials, belt construction and liner materials.
By controlling the velocity and force of impact in the load zone to match the belt speed and direction, the engineered systems are said to mitigate material splash, turbulence and dust.
Martin Engineering also say the low-turbulence, low-impact loading and controlled airflow can eliminate the need for baghouse dust collection systems, and the stable material path contributes to improved transfer, while minimizing belt abrasion and spillage.