Floating On Air
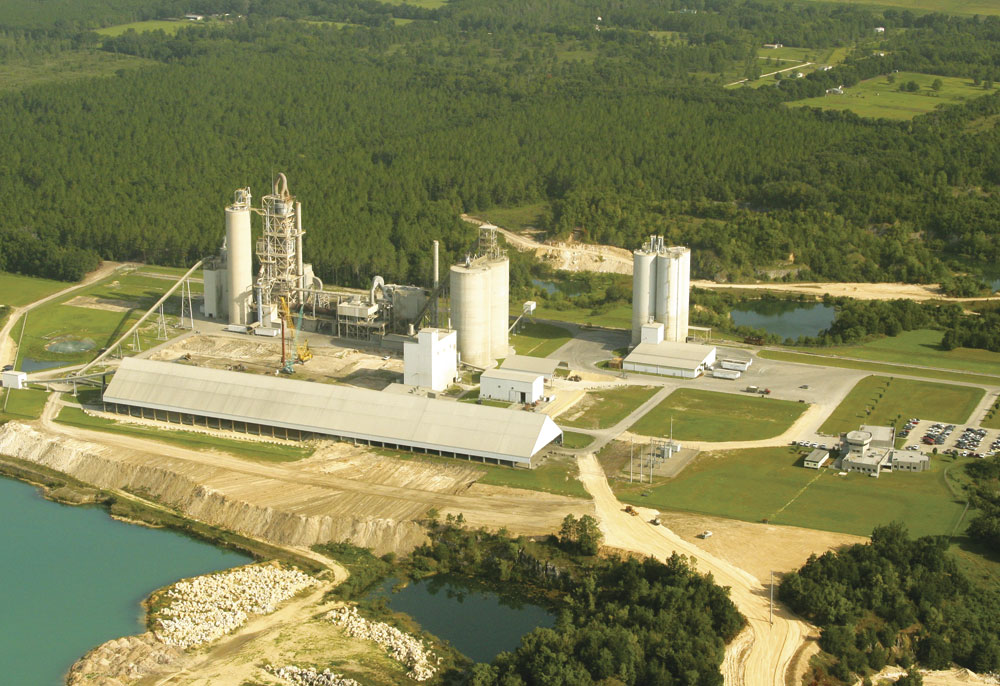
Air-supported conveyor fulfils requirement for clean, low-maintenance operation
The US’s largest producer of construction aggregates has employed an innovative air-supported conveyor system to serve its new railcar loading station, allowing the firm to ship clinker in bulk quantities to its grinding facilities in Port Manatee and Tampa. With its stable ride and fully-enclosed construction, the system contains fugitive dust and reduces maintenance requirements, while making best use of very limited space.
When company officials at the Vulcan Materials cement plant in Newberry, Florida, decided to ship clinker to remote grinding facilities, they knew it would require the addition of a new conveyor and load-out structure. The challenge was to design the system so that it would fit with the plant’s existing silos and conveyors.
‘The only practical option was to locate the railcar loading conveyor next to the existing pan conveyor, which carries clinker to the finish mill,’ explained maintenance manager Jim Kerns. ‘It was determined that the new conveyor would fit in a hallway running under the silos, but we knew that, once installed, it would completely fill the available space,’ he said.
As a result, clean-up of any fugitive material accumulating under or around the conveyor would be extremely difficult and potentially dangerous without stopping the adjacent pan conveyor and shutting down production. That realization led to the search for a highly reliable conveying system with proven ability to operate for extended periods with very little maintenance, one that could prevent the escape of fugitive material and also protect the load from rain that would introduce unwanted moisture to the product.
Selecting an air-supported system
After reviewing a variety of designs and proposals, the company specified a Martin Engineering air-supported conveyor, a simple and economical system that resolves many of the issues encountered with conventional belt conveyors. With no moving parts that require maintenance on the load-carrying side, the system could be installed in the close quarters of the hallway under the clinker silo.
‘Air-supported conveyors eliminate the carrying-side idlers used on conventional conveyors and instead use a film of air rising from a troughed pan to lift the belt,’ explained Greg Bierie, global project manager for Martin Engineering. ‘By removing a source of friction that requires periodic maintenance, air-supported designs offer significant advantages – including energy, environmental and safety benefits – yet the cost is competitive with traditional belt conveyors,’ he said.
The Martin Engineering system does not require a compressor, powering up to 600ft (183m) of conveyor supported by means of a single low-power centrifugal fan. According to the company, the extremely low friction inherent to the design can reduce overall drive power requirements by as much as 30% on a horizontal conveyor.
The use of air-supported conveyors also eliminates the need for idler adjustment to correct belt tracking issues. Advantages include extended belt life and reduced maintenance costs, as well as improved safety by limiting employee exposure to moving components.
Simple concept for a smooth ride
The concept of the air-supported design is relatively simple, with the load zone and carrying sections contained in a plenum that is pressurized by the centrifugal fan. The carrying surface of the plenum is typically shaped to the parabolic curve profile of a conventional belt conveyor with a 35° trough. Holes in the top of the plenum create an air film between the plenum and belt, which supports the moving load.
The return run does not require air support, and many systems incorporate conventional idlers on the return side. By using standard take-up drives, chutes and support structures, the air-supported design allows conversions of, or connections to, existing standard belt conveyors.
At the Newberry plant, the 24in (610mm) wide air-supported conveyor negotiates a vertical curve to elevate the load 25ft (7.6m) over the 290ft (88m) length from the bottom of the clinker silo to the top of the load-out structure. Capacity is set at 363 tonnes/h of –25mm material, with a belt speed of 350 ft/min (106.7 m/min). The troughed conveyor is moved by a 25hp (18.6kW) drive motor, and the air-support system uses a 15hp (11.2kW) blower to raise the belt.
The air-supported design from Martin Engineering eliminates maintenance issues such as idler lubrication and belt alignment, and the modular system allows replacement of existing conveyor sections with CEMA-standard construction. In addition, air-supported and conventional roller sections can be mixed to accommodate loading zones, tracking idlers, belt scales or other requirements. Moreover, with its stable path, an air-supported conveyor can operate at a steeper incline than roller conveyors, which can reduce the overall length and installed cost.
Two belt feeders at the Newberry plant meter the material through rolling blade gates to deliver a consistent load to the conveyor and prevent the ‘starve and flood’ conditions that can impede smooth operation. The material flows into ceramic-lined transfer chutes and then on to the conveyor.
As the material enters the discharge tower, it passes over a belt scale and into a retractable dustless discharge chute, which extends down into the railcar opening. The discharge chute is installed on a positioner that allows up to 6ft (1.8m) of travel perpendicular to the tracks to accommodate various loading hatch arrangements. An insertable dust collector is installed at the head pulley to catch any material that becomes airborne.
‘Fugitive material control was a critical element of this system,’ commented Jim Kerns. ‘We wanted to prevent the need for maintenance in the confined-space location, but we also had environmental objectives. Alligators and other protected species inhabit this area, and we wanted to ensure that dust didn’t migrate from the process.’
The results at Vulcan’s Newberry plant have been very positive, and the company has reported virtually maintenance-free service from the air-supported system. ‘The product condition is excellent from the smooth handling,’ concluded Mr Kerns. ‘And with the fully enclosed system, there is no contamination of the conveyed material or escape of fugitive dust.’