Conveyor Belt Cleaner Tensioners
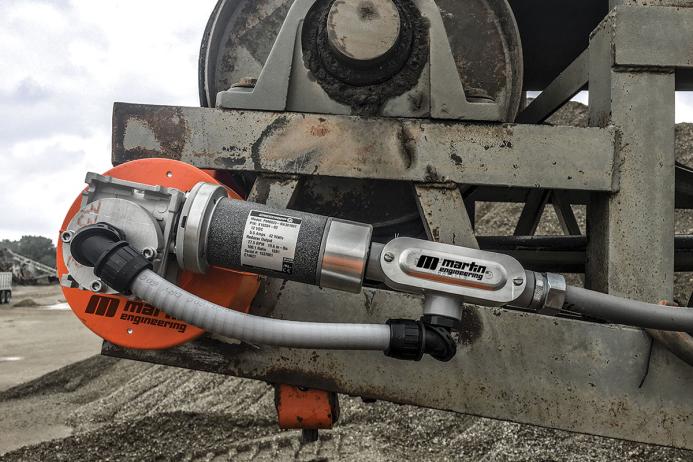
First published in the March 2023 issue of Quarry Management
Options for safe and efficient operation
There are many issues to consider when specifying the most appropriate conveyor belt cleaner, not the least of which is maintaining proper tension to achieve optimum cleaning performance without introducing related problems. Inadequate tensioning causes carryback to cling to the belt and spill along its path, piling up under the conveyor and emitting excessive dust. This requires extra labour for clean-up and can affect air quality. Over-tensioning leads to friction damage to the carrying side of the belt, premature blade wear and potential splice damage. Both scenarios contribute to unsafe work conditions and raise the cost of operation.
‘There are two basic approaches to applying tension to the belt cleaner: linear and rotary,’ said Dave Mueller, conveyor product manager at Martin Engineering. ‘The blade’s cleaning position and angle of approach to the belt often dictate whether a linear or rotary tensioner is used.’
The Conveyor Equipment Manufacturers Association (CEMA) defines the cleaning positions as primary, secondary, or tertiary. Primary cleaners typically function with a ‘peeling’ action, while secondary and tertiary cleaners are usually scrapers. Belt cleaners mounted in the primary position generally employ a rotary-style tensioner, while most units mounted in the secondary or tertiary positions use linear-style tensioners.
In most cases, belt tensioners have to be monitored and adjusted manually so they can maintain optimum pressure and carryback removal. Estimating when blades need changing is often a guessing game that, if left too long, could lead to unnecessary complications.
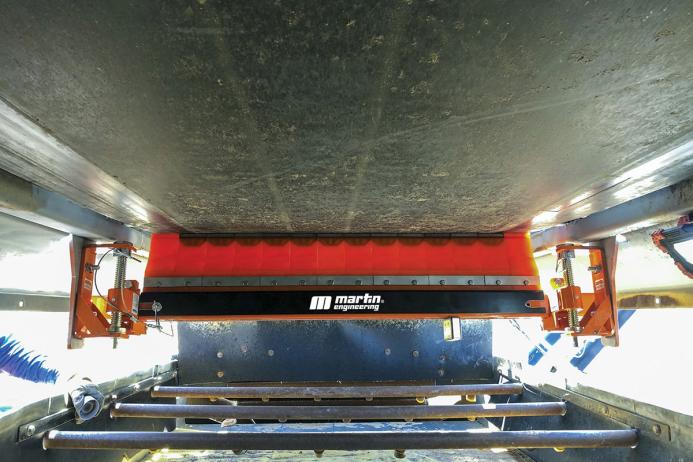
Linear tensioners
‘Linear tensioners are most often applied where the compensation for wear is required in small increments, such as with hard metal-tipped cleaners located in the secondary cleaning position or with brush cleaners,’ said Mr Mueller.
The simple design of linear tensioners often allows just one setting for full blade wear. Moreover, these tensioners can accommodate actuator deflection for accurate adjustment of cleaning pressure, delivering the ability to accommodate uneven mounting positions or asymmetrical blade wear.
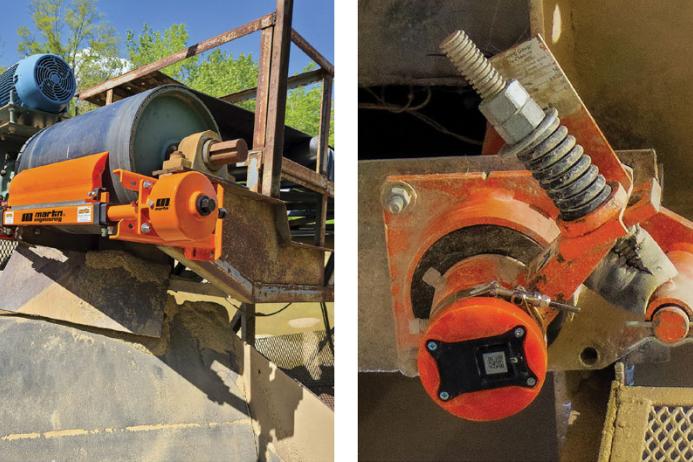
Rotary tensioners
The required tensioning forces can be applied by springs, hydraulic or pneumatic cylinders, electric actuators or from torque stored in an elastomeric element. Rotary tensioners such as the Martin Twist tensioner are often used with urethane blades, where the change in blade height and thickness as it wears is significant. Rotary designs tend to be compact and, in most cases, the actuator(s) can be mounted at any orientation, which provides options for installing the belt cleaner in the optimum position.
Air tensioners
Air tensioners use the resilience of a pneumatic cylinder to cushion impact. The tensioners can use Martin’s air connection kit to plug them directly into an existing air system, allowing for a more streamlined installation process.
Spring tensioners
Spring tensioners maintain efficient belt cleaning with a rugged coil spring. The Martin XHD spring tensioner delivers effective cleaning while cushioning splice shock to prevent damage, well suited for tensioning heavy-duty belt cleaners while standing up to tough conditions. Dual tensioning is recommended for belt cleaners installed on belts wider than 48in (1,200mm). However, dual tensioning does not change the fact that regular adjustment is required to maintain suitable cleaning pressure on the belt, which is where Martin’s N2 smart technology comes into play.
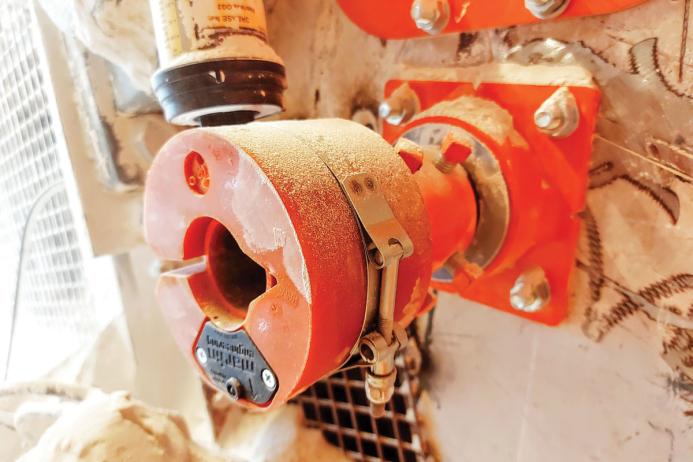
Auto tensioner/position indicator
Martin Engineering’s smart technology platform includes the company’s patented N2 position indicator (PI) to monitor primary cleaner blade wear and inform operators when the blade needs changing. The system uses a cellular gateway that relays data to the cloud and then to the user via a mobile app or desktop dashboard, delivering actionable information in real time and telling users when servicing is required, easing the burden on managers and workers so they can focus their attention on other critical details of the operation.
Designed for any belt cleaner using a polyurethane blade, the N2 position indicator (PI) system tracks belt cleaner performance and allows maintenance managers to keep on top of belt cleaner performance, eliminating needless inspection visits, reducing human exposure to moving conveyors, and helping to increase production uptime. The N2 PI has met all the requirements for CE Marking in Europe.
Robert Whetstone, vice-president of Martin Engineering’s EMEAI region, said: ‘Martin have a long track record for outstanding innovations that keep industrial processing plants running safely and efficiently. Our N2 system is a game-changer that combines tried and tested technologies into one easy-to-use package, so users can monitor their conveyor belt cleaners remotely.
‘With this smart yet simple upgrade, the technology does the legwork, providing real-time data on each belt cleaner blade to give an early indication of when servicing is needed. In the meantime, plant managers can be confident that material carryback, spillage, and build-up is being controlled by the belt cleaner, so they can keep the plant running to maximize productivity.’
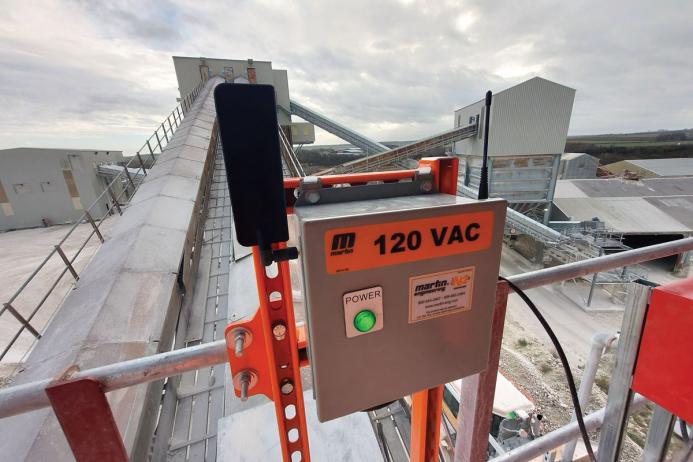
By tracking the individual performance and status of each belt cleaner, N2 PI delivers continuous, real-time feedback and eliminates guesswork. The detailed historic data also provide a maintenance log so service dates can be tracked, and wear rates calculated. The result is an improved return on belt cleaner investments plus the ability to budget and forecast for essential replacement parts. Replacements can also be scheduled for just-in-time delivery, helping users to better manage their inventory.
Development of the N2 PI involved extensive technical research, as well as long-term customer trials at major material processing facilities in more than 10 countries worldwide. In the UK, the system was tested for more than 12 months at the country’s largest lime production plant, operated by Singleton Birch.
Stuart Howden, engineering manager at Singleton Birch, who oversaw the UK trials from the start, said: ‘Martin Engineering’s N2 PI is a clever system that eliminates the need for repeated visits to each conveyor belt – we will never need to go back to doing regular physical inspections of all our belt cleaners. With more than 90 conveyors across our production site, the ability to monitor our belt cleaner blades remotely is a massive advantage.
‘Initial trials on six conveyors showed us that the N2 PI not only cuts inspection time, but also helps reduce exposure to moving conveyors and associated hazards. The Martin app shows us when belt cleaner servicing is needed, and we can arrange inspections at the end of shifts or during planned stoppages, which decreases unscheduled downtime. The app also allows us to monitor blade performance over time and budget accordingly.’
The N2 PI can be retrofitted to most conveyor belt cleaner mainframes that use polyurethane belt cleaner blades, or it can be introduced as part of a new installation. The battery-powered device feeds data about the performance and condition of conveyor belt cleaners to a central, cellular ‘gateway’ unit. The gateway then sends the information to a cloud-based server, which delivers it to Martin’s dedicated mobile app and/or desktop dashboard on a computer.
The N2 PI itself is a small, robust, and self-contained device with a proprietary grade polyurethane housing that can withstand punishing industrial environments. The device can be mounted up to 1,000m from the gateway, which is located on a high part of the plant to achieve the strongest signal. The system does not require a cellular link for each PI – connection is via radio frequency, allowing as many as 1,000 PIs to be monitored through a single gateway.
Supporting Martin Engineering on the technology side are two trusted Amazon Web Services (AWS) ‘Internet of Things’ partners. The result, say Martin Engineering, is a fully automated, seamlessly integrated, and secure cloud-based system that delivers super-reliable connectivity.
Operating independently of any plant communications infrastructure, the low power requirements of the PI device give a projected battery life of at least two years. Only the gateway requires a constant power supply, and it works with a wide range of input voltages to match local standards in any country around the world.
The PI system works by recognizing how much rotation of the belt cleaner mainframe is acceptable before tensioner adjustment is required. The mobile app tracks and displays blade status, remaining life, next scheduled tensioning, run time, wear rate, cleaner model, blade type, and other details. Alerts are provided automatically when a blade change is required, re-tensioning is needed, or an unusual condition or change is detected.
By relying on actual operating conditions instead of human judgement to monitor blade wear and tension for optimal cleaning performance, the N2 PI maximizes the cleaner blade’s usable surface area and reports with certainty when a blade is nearing the end of its useful life.
Conclusion
Whilst manufacturers continue to improve belt cleaner effectiveness, it has become clear that there is no single or ideal solution for belt cleaning and tensioner selection. Safety of personnel and the belt itself is the primary consideration when selecting a tensioner. Ease of inspection and maintenance is critical for belt cleaner effectiveness, so the tensioner must allow quick and safe service. Martin Engineering offer all the services and tensioning products that are necessary to meet the multifaceted demands of belt cleaning.
- Subscribe to Quarry Management, the monthly journal for the mineral products industry, to read articles before they appear on Agg-Net.com