Conveying With Confidence
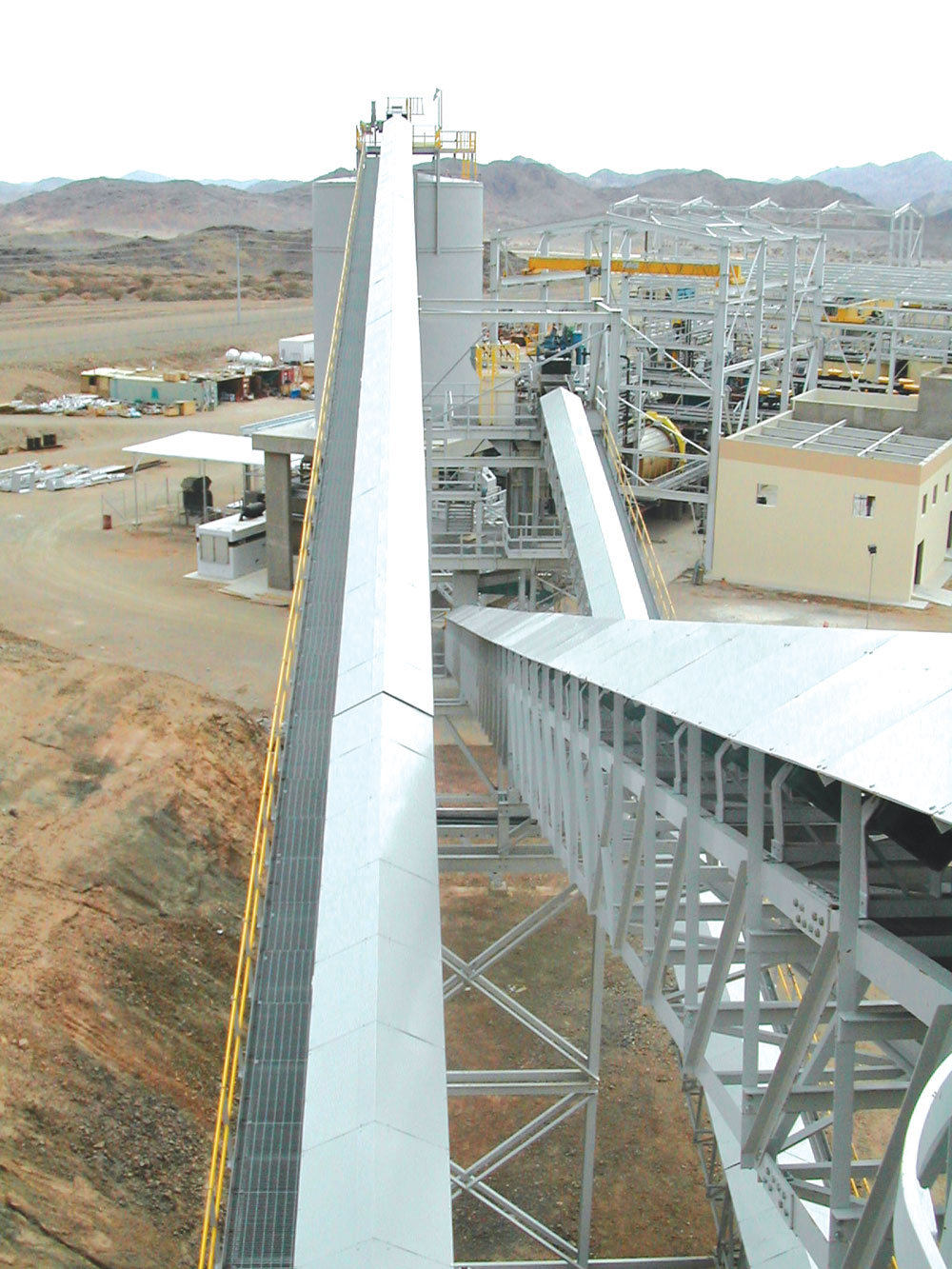
A buyer’s guide to conveyor and materials handling equipment for quarrying operations
By Jon Skidmore, Geo. Robson & Co (Conveyors) Ltd
The harsh environment of a quarrying operation offers no hiding place when it comes to the performance of conveying equipment. Reliability and robust design are the top priority in any quarry manager’s mind when selecting and purchasing conveyor equipment. Tight production deadlines and even tighter maintenance budgets mean downtime is not an option. However, choosing the right company to design, build and install robust, reliable bulk material handling conveyor equipment for quarrying operations can be a minefield.
The niche market of bespoke-designed conveyor systems suited to the material, environment and climate of a particular quarrying operation is very competitive, but can it deliver? With modern computer-aided design packages that can combine traditional heavy engineering with new design and engineering techniques, it has never been easier to design ‘robustness’ into the conveyor, and this is what today’s customer expects from a conveyor system manufacturer.
Moving bulk material
Belt conveyors are the backbone of any mining or quarrying operation. Systems that ensure the movement of bulk material at rates in excess of 1,000 tonnes/h are commonplace within the industry. With the carrying length of a conveyor system being virtually unlimited, such systems can convey material from the quarry to the processing plant without the need for heavy transport. Belt conveyors also have the flexibility of design to accommodate inclines and declines, allowing their structures to follow hillsides or to bridge obstacles, and combinations of conveyors, weighers, crushers, magnets and screens will ensure the end product is sized and free from tramp metal, ready for the next process.
The risk of heavy material ripping or damaging the belt when being loaded by a bucket loader has always been a problem. This can be minimized by using multi-plied, state-of-the-art belt compounds and materials. This manufacturing technique ensures that conveyor belts are more rigid and durable, and less likely to stretch and give. Also, by using impact rollers or boards, the impact of the material can be cushioned, very much like the shock absorbers on a car. Loading bunkers or chutes offer extra options for enhancing the loading operation by softening the impact of the load, with the added benefit of reducing the dust clouds that are often caused by dry materials.
Belt tension is critical to effective conveyor operation. If the tension of the conveyor belt is not set correctly the belt will slip when under load, at start-up or in wet conditions. Ceramic-lagged pulleys are widely regarded as the ultimate product for these conditions, as the extra grip achieved ensures a smooth start-up and, similar to a car tyre, the grooves on the ceramic pulley displace water from the belt, giving optimum grip and conveying continuity without slippage. In addition, the extra grip can compensate for slight differences in belt tension.
Depending upon the material being quarried, the conveyor can be either open or enclosed. Coarse, wet material is normally transported on open conveyors, whereas dry, dusty material tends to be enclosed to provide protection from the elements. The conveyor covers themselves are available with many options depending upon their use and operating environment. In some cases fully enclosed gantries incorporating walkways and/or maintenance access routes are provided.
Drives and gearboxes are critical components within the conveyor design, and in the author’s experience the best solution is to source drives from manufacturers with proven track records of reliability. This is not always the cheapest solution at the outset, but reliability does pay for itself in the longer term. When considering spare parts and service requirements, international motor and gearbox manufacturers such as SEW, David Brown, ABB, are generally just a phone call away from anywhere in the world. The same can be said for bearings, where again recognizable names such as Cooper or SKF are often used because of their reputation for reliability and their worldwide availability.
Loading and slewing conveyors are commonplace within the quarrying industry and are often produced by the same manufacturers as standard belt conveyors, so purchasers can insist on the same proven components, always bearing in mind, of course, that while the purchase price may be a little higher, downtime is usually even more expensive.
Another variation of the belt conveyor is the tripper conveyor, which is used to distribute granular materials into warehouse/toastrack-type facilities. Here, an inclined conveyor elevates the material to the tripper conveyor, situated in the roof space of the warehouse, whereupon the train of the tripper conveyor, which runs on tracks extending the full length of the warehouse, feeds the conveyed material into bays or compartments below. Programming and switching allows the tripper to feed a certain area or length to suit warehousing needs. Once again, the use of high-quality components will prove beneficial in the longer term.
Troughed belt conveyors use carrying idlers that are fitted in groups of three to create a troughed shape to hold the material in place while being conveyed. This method works well with either wet or dry materials. Idlers normally feature maintenance-free, sealed-for-life bearings, as greasing the entire length of a conveyor can be a time-consuming and costly activity.
There are many types of speciality conveyor technologies that complement belt conveyors, often working in unison with the belt or performing other processes on the same plant or site. Vibration technology is one such speciality that allows systems to be designed to feed, dose, measure, transfer, screen, scalp, dry, grade or dewater materials. Systems that combine of all these processes can be designed to meet customers’ specific requirements.
Vibratory systems are often used in quarrying, as their robust design and lack of mechanical moving parts make them well suited to harsh environments. The application of vibratory screening and scalping is widely used throughout all types of quarrying and opencast mining. Low maintenance is often the number-one customer requirement, especially with systems purchased for installation in remote areas where reliability is crucial.
Kiln feed systems, where continuity and purity of product is paramount, also make use of vibratory feeders and screens. The screens ensure the correct particle size is fed to the furnace or kiln, while regulated feeders ensure a continual dosed feed.
Making the grade
Grading and sizing is a major application for vibratory-type systems and, by using a number of decreasing sized grids, such systems can grade various sizes or separate the oversize/undersize from the product. In the aggregates industry, vibratory systems also allow chutes to divert graded products either to further processing (grinding, crushing etc) or to stockpile/transport.
Troughed feeders are often used when the bulk movement of product is required. Using either an electromagnetic drive or unbalanced motors, the troughed feeder accurately delivers the amount of product required. Commonly used within the glass industry for precise dosing, the vibratory feeder is also widely used throughout industry for many other dosing and filling operations.
Vibratory systems have also found a niche with wet products; almost any type of wet solids can be conveyed, dewatered or filtered. In the water-treatment and sewage industries, the dewatering process allows solids to be separated and processed.
Waste and recycling industries use many types of vibratory systems; applications include ash removal, to ensure the smooth operation of incinerators, while the glass recycling industry is a major user of vibration technology and troughed feeders to transport cullet and other ingredients for reprocessing.
Fine-grade materials often pose problems for bulk processing. One development is the tubular feeder to ensure full enclosure of the material, thereby keeping the product in and contaminates out. Similarly, the compact feeder is used for the charging and dosing of fine materials with flow rates ranging from a few kilograms per hour up to 25m3/h.
New developments in the vibratory products field mean that designs can now meet certification criteria for the ATEX regulations, for use in explosive atmospheres. Other developments include reversible vibro-feeders, providing the option of a central infeed with twin feed out at opposite ends of the trough, suitable for measuring and dosing.
Conveying materials using screw conveyors is one of the more traditional conveyor techniques. Used throughout many industries as a reliable workhorse, variations in flight design allow screws conveyors to convey, mix, feed or elevate wet or dry materials. Screw conveyors are also tailored to the customer’s individual requirements, providing infinite choices in terms of size, speed, material or application. The type of material the screw is manufactured from depends upon the process and material being conveyed. Wet material screws are usually made from stainless steel, while those for other applications are generally made from mild steel.
Screw conveyors comprise only a few mechanical parts but each one is critical to its operation. A single drive motor unit and gearbox drives a rotating screw or scroll, which is supported by two bearings and pushes the material from the infeed to the discharge end. Longer designs may incorporate hanger bearings to support the weight of the screw within the conveyor casing. Because of their concealed nature and proximity to the conveyed product, additional maintenance checks should be carried out on hanger bearings to monitor their condition and to ensure their continued performance.
By utilizing the same tried and tested motor and bearing manufacturers as those used for belt conveyors, the reliability of performance and robust construction of screw conveyors can be guaranteed. Used in many industries, the screw conveyor’s versatility and low maintenance requirements are its key benefits.
Insist on the best
Purchasing budgets may be tight in today’s economic climate, and insisting on reliable components and robust construction will undoubtedly raise the initial outlay, but the risk of downtime and breakdowns will be significantly reduced. Service is another important factor; spare part turnaround times and the availability site service engineers when needed should always be considered at the tender stage. No matter what product is being quarried, the price of downtime is always far higher than the extra premium for quality components and service.