Confidence In Silo Level Control
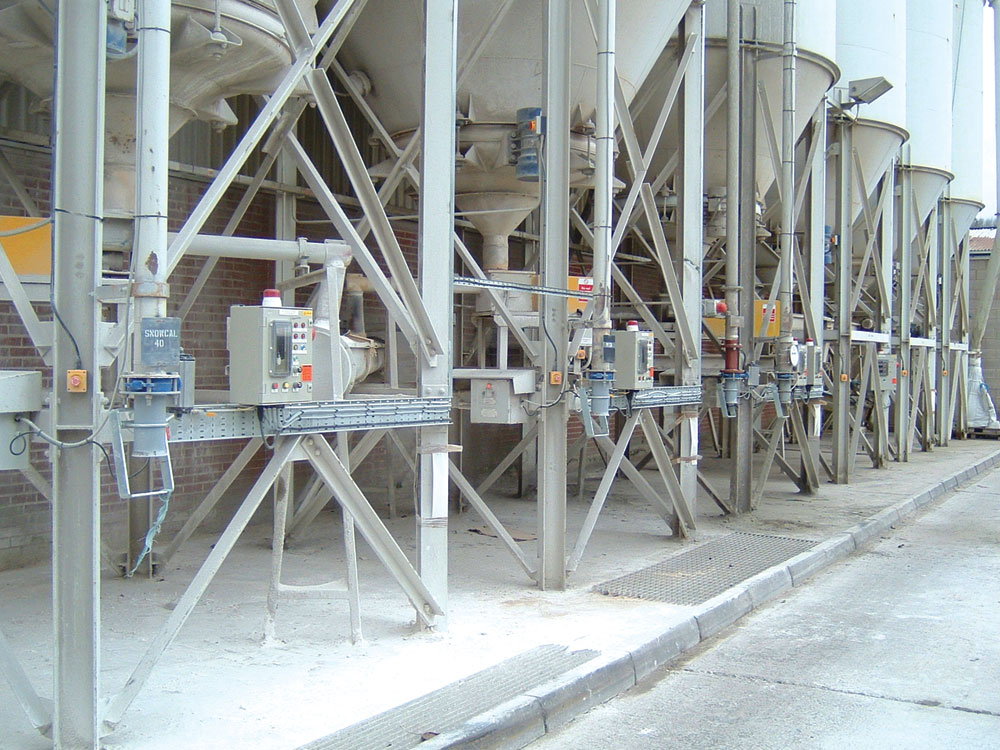
Why operators should not gamble with the integrity of their silo-protection system
by Nigel Allen
The past decade has seen significant improvements in quarry health and safety, whereby dedicated programmes, such as the ‘Hard Target’ initiative, have resulted in a steady decline in incidents involving deaths and injuries. However, despite this welcome reduction, everyone concerned knows that there is no room for complacency and the recent high-profile campaign on accidents in the workplace by the Health and Safety Executive (HSE) highlights the need for ongoing vigilance, especially when it comes to the potential dangers of slips, trips and falls. According to the HSE, 61 people died and more than 14,000 suffered serious injury as a result of a slip, trip or fall from a height in UK workplaces in 2007, while 15% of all major injury accidents at quarries result from people falling when working at height.
One particular breakthrough where significant strides in safety improvement have been made is in the installation of silo-protection systems on bulk-material storage vessels, to prevent problems of overfilling or over-pressurization arising during pneumatic filling from road tankers. Although problems are relatively rare, added to the potential dangers of system failure is the risk to maintenance operatives if regular checks on the systems have to be made directly on top of the silos.
Redditch-based Hycontrol, one of the leaders in the design of level-based safety systems for quarry environments, have made a significant contribution to silo-protection system design and implementation, working closely with quarry operators and in line with guidelines from bodies such as the Quarry Products Association and the British Cement Association (both now part of the newly formed Mineral Products Association). However, despite the implementation of comprehensive guidelines, endorsed by Defra and the HSE, the company’s sales and marketing director, Nigel Allen, believes many operators are still gambling with the health and safety of their operatives and the environment when it comes to having fully effective silo-protection systems.
‘Installing a system to meet regulations is one thing, but ensuring its ongoing integrity, day in day out, is quite another matter,’ he explained. ‘Many quarry managers just do not know whether their system will work reliably when it’s needed, which may be during the next delivery.’
According to Mr Allen there is a case to argue that in the current economic downturn, when plant and equipment is used less frequently, the odds of relief valves and filters becoming seized or blocked could increase. As a result, therefore, the ability to fully check silo protection systems in a safe manner, just prior to each delivery, is even more important.
Hycontrol believe their Silosafe protection system is the only one that provides a 100% safety guarantee, where all critical components can be tested in one action from ground level. ‘Competitive systems typically rely on partial testing and visual inspections, often placing the onus on the operator to make informed decisions on the condition of vital components,’ said Mr Allen. ‘New restrictions on working at height now prevent operatives routinely climbing to the top of silos to carry out inspections. Given these restrictions, comprehensive checks may only be done infrequently, rather than just prior to each delivery.’
Mr Allen’s confidence in the Hycontrol silo-protection system was highlighted recently when the company received a call from a quarry customer reporting an apparent fault with their Silosafe system. Although the system had passed the ground-level test, when they started to fill the silo, the system had shut off the inlet valve, indicating an overpressure in the silo. This scenario was repeated a second time leading the customer to conclude that the problem lay with the Hycontrol system. When it was explained that there must have been a problem with some part of the silo’s operational equipment, the customer was adamant that this had only recently been serviced and that the problem must lie with the Silosafe system. However, having persuading the customer to recheck the silo for a third time, Hycontrol soon received a more penitent call to say there had indeed been a problem with the silo and that maintenance work that should have been carried out had not been completed satisfactorily.
‘Had the customer tried to bypass our system and allowed the filling to take place, there would undoubtedly have been very serious consequences,’ commented Mr Allen.
Silo protection system overview
Silo-protection system implementation is designed to address two main unrelated issues focused on the safety of site personnel and environmental problems associated with the emission of particulate material to the atmosphere. Current guidelines mandate that silos filled via pneumatic conveying should be fitted with automatic protection systems to prevent over-filling or over-pressurization. Such systems should have three independent sensing elements – a pressure relief valve, a pressure sensor and a high level alarm.
Effective and safe filling relies on the controlled release of air through the air filter, to ensure that pressure does not build up inside the silo. Problems typically arise through air filters becoming blocked or from excess discharge pressures generated by the tanker filling system. Most storage silos are not designed as pressure vessels and even an overpressure of 1–2 lb/in2 may be sufficient to cause serious damage. Theoretically, any excess pressure should be detected by the pressure sensor, allowing the filling to be halted. If all else fails the pressure relief valve (PRV) should act as the final backstop, allowing rapid silo venting, albeit at the expense of atmospheric contamination. In reality, however, the PRV could be prone to sticking unless it has been physically tested on a regular basis.
So how can operators be sure their systems will work when necessary? The latest guidelines stipulate that the system’s critical sensors must be regularly checked to ensure they are in good working order.
‘Under ideal working conditions, the three-fold safety regime should be more than adequate to prevent problems, but the only way to ensure equipment is fully operational is to carry out physical checks just prior to each and every filling, explained Mr Allen. ‘Carrying out adequate checks on a regular basis can be difficult, particularly if the main protection components are not part of an integrated system. In practice, especially in busy working environments, the checking procedure is often not carried out.’
The Hycontrol Silosafe solution provides an easy-to-use, fool-proof and fail-safe system, which mandates the automatic testing of the key components directly from the system’s integrated control panel situated at ground level. The panel also incorporates twin multi-segment bar graphs for continuous level and pressure monitoring, as well as digital displays for both parameters.
When a delivery driver reports on site he is issued with a dedicated panel key for the particular silo to be filled. Having activated the panel with the key, the driver must then press the ‘Sensor Test’ button and release it. At this stage the discharge butterfly valve is locked. Each of the primary sensing elements is collectively tested by this single button press and any malfunction is immediately highlighted. Should any faults be detected, the valve will remain locked and not allow filling to take place until the problem has been remedied. If the sensors pass the test, a white ‘ready to fill’ lamp is illuminated indicating that the discharge valve has opened and delivery can proceed.
The pressure sensor module is the first line of defence, measuring the pressure in the silo as filling takes place. If this exceeds a preset value it first provides an audible alarm, followed by a flashing red beacon and then an output signal which immediately closes the discharge valve in the fill pipe. Hycontrol have developed an innovative method for checking the integrity of the sensor and cleaning it at the same time. During the ground-level test, a small air supply connected to the sensor applies a fixed pressure of approximately 90% of full-range output directly to the sensor face. This change in pressure is measured by the system and verifies correct operation. As the air escapes through the porous membrane at the end of the sensor tube, it removes any build up of material. If the membrane is blocked, the system alerts the operator and does not allow filling to take place until the situation has been remedied.
Although current requirements call for a high level probe to be fitted to silos to prevent overfilling, Hycontrol recommend the use of an additional continuous level-monitoring system. This will not only give an accurate level reading in the silo prior to filling, ensuring that the load to be discharged will fit in safely, but also an ongoing indication during the filling process. A wave-guided TDR radar system is well suited to this task and will give stable and accurate readings, even during dusty filling conditions. Dual-redundancy, best engineering practice of this kind provides unrivalled safety. However, where only a high level probe is fitted the Silosafe ground-level test will automatically check its operational integrity. If a high level condition is reached during filling, warning is given via the siren and flashing red beacon. A countdown timer then closes the discharge valve after 30s, giving the driver time to cease filling and clear down the line.
The pressure relief valve is the last line of defence and, theoretically, should never have to be used. The Hycontrol system allows for optional full testing of this vital component. Using small air cylinders, the system can lift the valve to check its operation, with proximity switches detecting correct lifting and closing. This regular physical activation has the added benefit of significantly reducing the chances of the PRV sticking.
‘We are confident that our silo-protection system can reduce incidences of slips, trips and falls to provide a safer working environment,’ said Mr Allen. ‘By offering an integrated solution, with the ability to carry out tests on all the key elements in one action at ground level just prior to filling, we take the gambling risk away from operators and ensure the system will work in earnest if required.
‘During filling, operators and drivers can clearly follow the conditions inside the silo via the bar graphs and displays, giving them ample time to react to any dangers of overfilling or over-pressurization. If any preset level or pressure limits are reached, the system will automatically close the inlet valve to the silo.’
Hycontrol Ltd, Larchwood House, Orchard Street, Redditch B98 7DP; tel: (01527) 406800; fax: (01527) 406810; email: sales@hycontrol.com