Cleaning The Cleaners
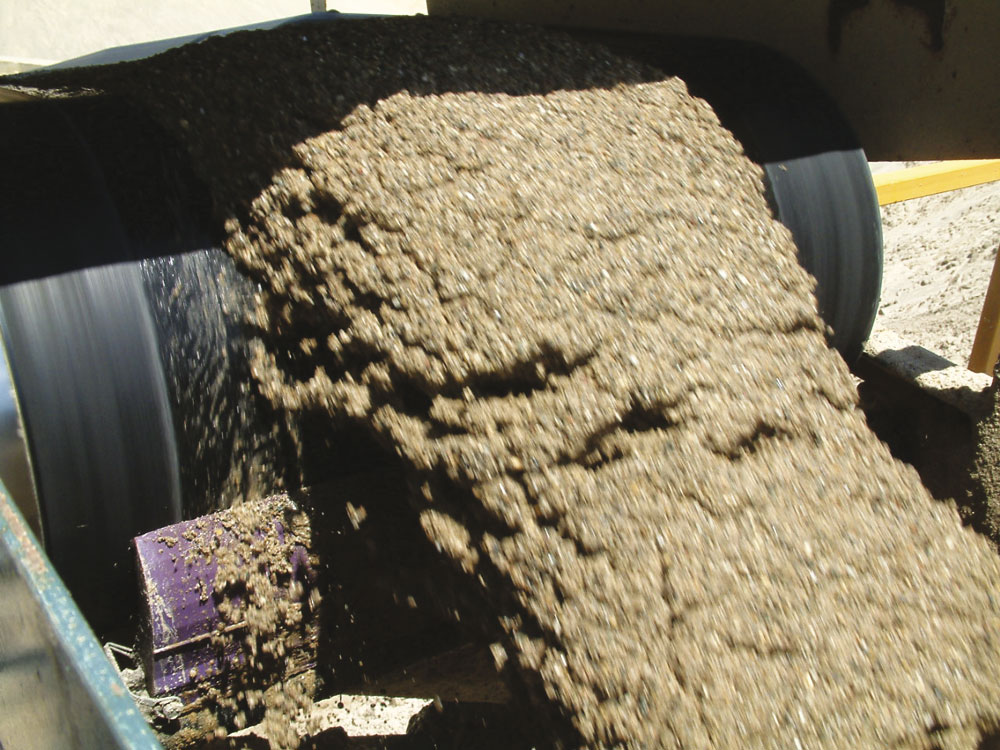
A healthy conveyor system begins and ends with cleaning and maintenance
By Ryan Grevenstuk, product manager, Flexco
When you buy a product, you expect it to perform as well on day 365 as it did on the first day you installed it. You do not have time to spend wondering if or when it will break and you certainly do not have time to buy a new one. The truth is that effective maintenance can make all the difference with equipment, and this is especially true with belt conveyor cleaners.
In the aggregates business, where equipment is subjected to harsh materials and adverse weather, belt cleaners play an important role in keeping systems clear and running. Downtime is simply not an option. But while the cleaners are busy maintaining your belts, what are you doing to keep your cleaners running smoothly?
Why maintain belt cleaners?
Over the years, advances in belt cleaner technology have not only made them easier to use, but also easier to maintain. Maintaining cleaners enhances the performance of the cleaner itself, as well as the other components in the conveyor system. Keeping a watchful eye on the cleaners also extends the life of the cleaners, the belt and the belt splices, as properly maintained cleaners are less likely to cause damage to belts and fasteners in comparison with cleaners that are installed and ignored until it is time to replace them.
In today’s economy, it would be difficult to find a business anywhere in the world that is not trying to cut costs. That is why it is more important than ever to maintain existing systems. Often, there is not the money in the budget to replace something if it breaks, or the time to withstand a major shutdown that potentially could have been prevented.
Carryback costs, for example, can affect a site’s overall budget multiple times. Maintenance costs and safety costs top the list, but the cost of the material wasted and the housekeeping costs to remove the material can also be expensive. In North America, CEMA (Conveyor Equipment Manufacturers’ Association) conservatively estimates carryback to be as high as three tons per week, given a 60in wide belt travelling at 800ft/min. Over the course of a year, that adds up to 150 tons of material for a single belt.
Poor belt cleaning also contributes to after-the-fact maintenance costs related to belting, pulleys, idlers etc. While good maintenance and quality replacement parts cost a little more to purchase initially, they can be worth it in the long term.
Maintaining the cleaners
When approaching cleaner maintenance, there are three simple principles to remember: clean it; inspect it; and tension it.
Clean it
This may sound obvious, but the first rule of thumb with cleaners is to remove any debris from the blade and tension springs. Tensioners cannot do their job with debris stuck in them, and removing material build-up from the blades will make them much more effective. Moreover, a dirt-free cleaner is much easier to inspect.
Inspect it
A simple visual inspection can do wonders for a cleaner. Check to see that everything is in working order and replace any damaged components. With the blades, inspect the visual wear lines to ensure that the blades have not reached the end of their lives. During the inspection, make a note of how close the blades are to complete wear and the approximate amount of time it took to get to that point.
Tension it
Tension the blade to accommodate the blade wear. This can be done quickly and easily by referencing the tension check decal and measuring the tension spring to ensure the blade is properly tensioned.
Complete maintenance plan
It is important to think of cleaner maintenance as part of an overall plan, instead of a specific task. In addition to regular maintenance, there are two other aspects that can enhance the performance of the belt conveyor system – the quality of products and replacement parts.
Choosing the right products and replacement parts is integral not only to the cleaning system, but to the entire conveyor operation. Taking time to consider factors such as blade life, the material path of the product, and the ease of tension checking will save time and money.
Operators should look for a blade with a long wear life. Often this is determined by the material from which the blade is made. In the case of urethane, the quality of the urethane and the volume of this material found on the blade is the key to long wear life.
Monitoring the path the material actually takes on the belt can also save the cleaner. A blade that follows the material path is the most efficient because it wears evenly, rather than wearing in the center. Utilizing a blade that covers only the material path boosts cleaning performance and extends the life of the blade.
With regard to visual tension checks, the philosophy is simple. The easier it is to check the tension, the more it will be inspected by the crew. Over- or under-tensioning the blade can lead to shortened blade life (as much as 20% less in some cases). Improperly tensioned blades compromise cleaning efficiency and blade life, and have a negative impact on the budget.
A complete system
In a belt conveyor system, a myriad of products work together towards a common goal – to keep things moving and get the job done. While belt cleaners are a small part of a much larger system, a healthy conveyor system begins and ends with cleaning and maintenance. Operators should consider the entire system when putting their belt cleaner maintenance plan into effect. It is a good rule of thumb to inspect and perform maintenance on all conveyor system components as part of an overall maintenance plan. Ultimately, being proactive can save time, money and aggravation in the long term.
For further information visit: www.flexco.com