Bulk Materials Handling
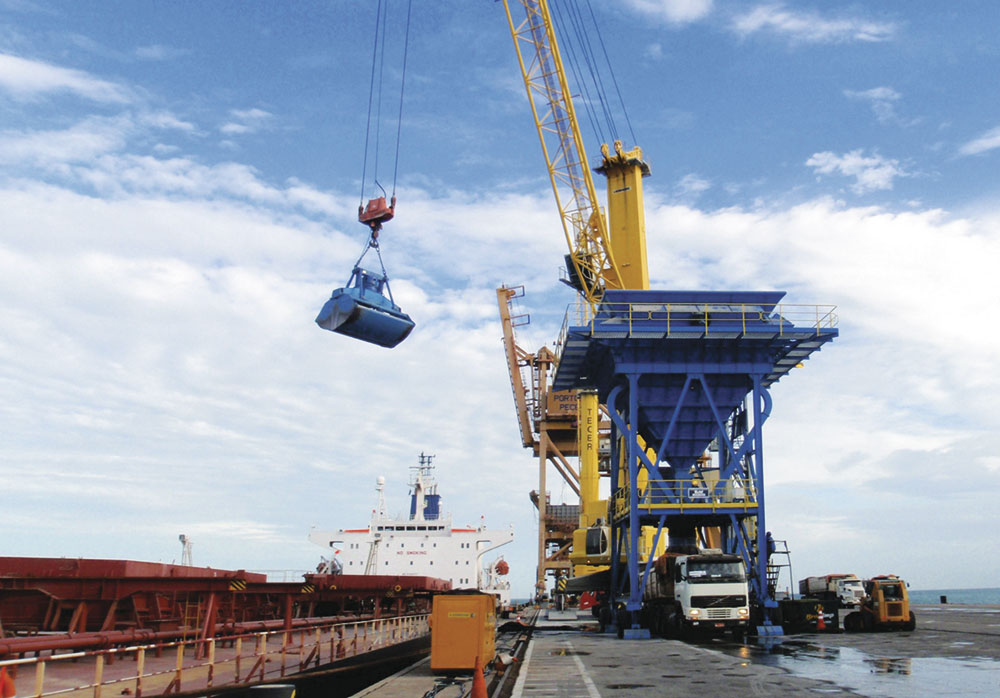
Logistics solutions from the mine or quarry to the processing plant
In years past the location of a mineral processing plant was generally governed by the availability of raw material and fuel, and the market for the finished goods. Over time, however, this link has effectively been broken with the raw material and fuel sources often on different sides of the world.
Industrial minerals are now shipped across the globe in vast volumes, demanding efficient logistics to minimize both the cost of transportation and the carbon footprint. Aumund Group have developed a range of bulk handling solutions from the mine site to the processing plant, allowing operators to take maximum advantage of any combination of truck, rail, barge or deep-sea shipment.
Figure 1 shows an ungeared (ie without deck cranes) Panamax-size vessel being discharged by a grab-equipped mobile harbour crane to an Eco-Hopper and then to standard road tipper trucks for onward movement to local storage or direct to the processing plant. In this particular case, it is cement clinker that is being imported, but it could equally be any mineral or concentrate.
At the mine or quarry site, the fundamentals of extracting raw minerals have not changed in centuries; the rock is blasted from the face and loaded to trucks to be taken to a central primary crusher and then conveyed to a secondary crushing and screening station to be stockpiled before despatch/export.
Figure 2 shows an Aumund type BPB-SF plate feeder receiving as-mined rock. The apron feeder provides a controlled feed rate to the primary crusher with, typically, an electrical interface to match the feeder to the crusher performance to avoid over-feeding.
The Aumund feeder design is based on tracked vehicle type chains with a rupture strength up to two times 3,600kN (type D9), supported on close-pitch matching rollers plus central skids to absorb impact loads.
Each plate is made in two overlapping parts with milled edges, thereby ensuring the plates articulate at the head and tail sprocket, while an effective seal is maintained to reduce the risk of spillage between the plates (fig. 3). Available with a total plate thickness of 80mm and maximum plate width of 3m, these machines can be matched to the largest haul trucks for handling rates of up to 3,000 tonnes/h.
However, the blast–haul–crush concept with a remote, central, fixed primary crusher is expensive to operate when the hauling distance increases. Trucks are expensive to own, even more expensive to operate and have a very high carbon footprint.
One solution is to bring the crusher to the face, thus eliminating intermediate handling by haul truck. B&W Mechanical Handling Ltd, part of the Aumund Group since 2002, pioneered the concept of mobile link conveyors used with a track-mounted mobile crusher and hydraulic excavator, such that all the equipment operating at the face remained mobile and could be moved back during blasting.
Figure 4 shows a mobile link conveyor installation where the mobile primary face crusher is equipped with an integral screen and rejects-handling system, ensuring the final maximum material size is controlled within close limits.
From the link conveyors, the sized material may be conveyed by conventional fixed or semi-permanent field conveyor equipment to the secondary crusher and final screening station and stockpile.
While the link conveyor solution eliminates all truck haulage, there is little doubt that for short distances, the flexibility of haul trucks is still attractive for most operators.
Figure 5 shows a Samson surface feeder integrated with a twin-shaft rotary sizer which forms a mobile feed point for a moveable overland conveyor system. Figure 6 shows the field conveyor mounted to sledge runners which also carry the rail-mounted sizer.
In this operation, the sizer and feeder combination may be moved easily along the length of the conveyor to bring the feed point as close as possible to the working face. The working face therefore runs parallel to the field conveyor and, when the workable length of the field conveyor has been exhausted, the complete package can be moved sideways towards the face on the lateral sledges and the whole process is repeated.
This keeps the haul length for the trucks to a minimum; in this particular application handling limestone, the system is able to achieve a performance rate of up to 800 tonnes/h using only two articulated trucks.
For economic conveying, the sizer reduces the as-mined and loaded material from, typically, 800mm down to 150mm to be conveyed overland to a cement plant several kilometres distant. With complex highways between the mine and the plant, haulage by truck would have been difficult, thus adding to the attraction of long-distance conveyor haulage. This is a typical example of how the best attributes of truck and conveyor haulage have been combined to achieve the least operating cost and minimum carbon footprint.
Where the mine or quarry is close to the processing plant, that is the end of the external logistics story, but in many operations there is a large disconnect between the extraction site and processing plant requiring complex logistic operations in between.
Where distances permit, truck haulage is generally the most flexible option and in this situation Aumund’s Samson surface feeder solution is an attractive option for the intake of raw material. The Samson unit combines the benefit of a wide apron-plate feeder with the cleanliness of a belt system, allowing material to be received direct from trucks without the need for deep underground pits or hoppers.
Figure 7 shows a Samson 800-Series feeder receiving –25mm crushed limestone at a power plant in the US. The limestone is sourced from a local quarry some 10 miles distant then further crushed and milled on site before making the slurry used for flue-gas desulphurization.
Figure 8 reveals that the equipment is completely surface-mounted, including the ongoing conveyor system taking the limestone to a ground storage facility, and shows how the Samson has a deflected chassis allowing the intake section to be near horizontal, thus simplifying the truck interface.
Where the mine and processing plant are in the same locality and both are either rail connected or close to suitable sidings, haulage by rail is by far the better solution, being more economical and much less polluting with a very low carbon footprint. At the mine site railcars can be loaded simply using a silo and loading chute system mounted to a suitable support structure above the rails.
However, many sites are not directly rail connected although there may be rail sidings close by. In this situation the Stormajor mobile loader, developed by B&W, offers a solution by allowing railcars to be loaded direct from road trucks at an existing rail siding without the need for fixed plant or infrastructure.
Figure 9 shows a Stormajor providing a railcar loading facility for a silica sand quarry near Paris. The sand is trucked from the quarry to the siding some 20 miles away, and then loaded on to the stationary train comprising around 20 railcars. The railcars are delivered by locomotive in the morning, loaded during the day and collected in the evening.
Figure 10 shows a more recent installation at Poznan, in Poland, where basalt rock is delivered to the Stormajor by articulated dumptrucks and loaded at a rail siding close to the mine. In this particular case the Stormajor (which is clad in flexible PVC sheeting to minimize dust escape) loads flat-bottom railcars using the radial boom feature, which includes a rotating trimming chute, to accurately place the material.
Delivery by truck is a temporary solution pending installation of link conveyors and is a good example of how mobile loading equipment can be used to take advantage of a short-term market position; in this case the Stormajor was delivered only 13 weeks after order placement, providing a genuine fast-track solution.
Likewise, the Stormajor can be utilized for the loading of barges for material distribution via inland waterways, as illustrated in figure 11. In this operation gabbro rock is delivered to the lakeside from an adjacent quarry and loaded on to barges of around 5,000dwt for distribution to Moscow and St. Petersburg.
The equipment operates on a simple berth using the long cantilevered outloading boom on the Stormajor to load the barges moored just offshore in deeper water, thus avoiding costly dredging and an expensive permanent concrete dock.
B&W Mechanical Handling Ltd pioneered the concept of direct loading from truck to railcar, ship or barge. Figure 12 shows an early system for exporting marble chips from the port of Marina di Carrara, in Italy, incorporating a Samson surface feeder and a mobile loading boom for delivery into Handysize vessels.
Whether shipped by rail, barge or deep-sea vessel, the final link in the logistics chain is the intake and storage of these materials at the processing plant.
Figure 13 shows a typical railcar intake facility where hopper-bottom railcars are discharged to an underground hopper and feeder. A typical hopper/feeder combination is illustrated in figure 14, where an Aumund type PKF armoured chain feeder is employed to provide a controlled discharge rate to the ongoing conveyors. Comprising scraper bars mounted to round link chains (fig. 15), this is a well established and proven solution which has the advantage of being fully enclosed and thus dust-tight and spillage-free. For underground installations clean operation is essential to minimize housekeeping costs in difficult-to-access areas.
In addition to underground feeders and associated conveyors, a typical package would include an enclosure building with the option of comprehensive dust-collection equipment, depending upon the material handled and the sensitivity of the location.
From the rail or road intake facility the bulk mineral will, typically, be conveyed to a local storage facility, such as a dome or silo system. For larger volumes, a horizontal storage system, perhaps including a blending facility where material may be supplied from a range of sources, may be appropriate. Schade (Aumund Group) offer a range of storage systems based on travelling stackers and chain scraper type reclaimers for automated operation.
Figures 16 and 17 show a typical longitudinal storage solution with travelling and luffing boom stacker, plus a cantilevered boom style reclaimer recovering dissimilar materials from discrete storage bays.
The boom-type chain scraper reclaimer concept draws material from the inclined stockpile face and discharges to a collecting conveyor running parallel to the stockpile. The recovered material can be conveyed to silo storage or bunkers where it may be blended and delivered in controlled proportions to, for example, a milling system before processing.
For more efficient blending at the storage facility, the bridge reclaimer system shown in figure 18 offers true homogenization, producing a reliable and consistent material specification for the process plant.
Both boom-type and bridge-type reclaimers may be supplied in a circular format with the option of a lightweight dome enclosure. This is the most economical storage solution in terms of both total capital cost and plant footprint.
In most processing applications, at some point in the handling systems material is stored in silos of either concrete or steel construction. To raise the bulk mineral to the storage silo the Aumund type BWZ central chain bucket elevator (fig 19) has proven an effective solution with around 2,500 installations worldwide.
Vertical elevation minimizes the plant footprint and the system is totally enclosed with no risk of dust escape or material spillage. The elevator plus feeder equipment can be integrated with a package for road intake, as shown in figure 20, or for rail intake as shown in figure 13.
The equipment illustrated for intake from rail is based on the use of hopper-bottom or side-door self-discharge railcars where the material falls naturally, under gravity, to a hopper below. However, not all countries have a sufficient supply of such railcars, as illustrated in figure 21, which shows a train with a combination of new hopper railcars and old flat-bottom types.
Obviously, the hopper-bottom cars are easy to discharge but flat-bottom cars will need manual excavation, a time-consuming and expensive process that can slow the operation considerably.
Figure 22 shows an Aumund railcar tippler installed at a Polish port, which handles flat-bottom railcars by clamping them in the tippler frame and rotating them to discharge the contents to a hopper and feeder below.
In the complex market that exists today, many minerals of vastly different handling characteristics must be transported from the mine or quarry to the processing site, often with many logistical steps along the way.
In addition to extracted minerals, it is necessary to consider the movement of industrial by-products, such as synthetic gypsum from power plants and slag from steel works, which have become important assets in the global fight to reduce greenhouse gas emissions.
This article demonstrates some of the logistics challenges to be found along the way and provides examples of how these challenges have been met with ingenious and economical solutions in terms of capital and operating costs, and carbon footprint.
For further information visit: www.aumund.com