The Best Of Both Worlds
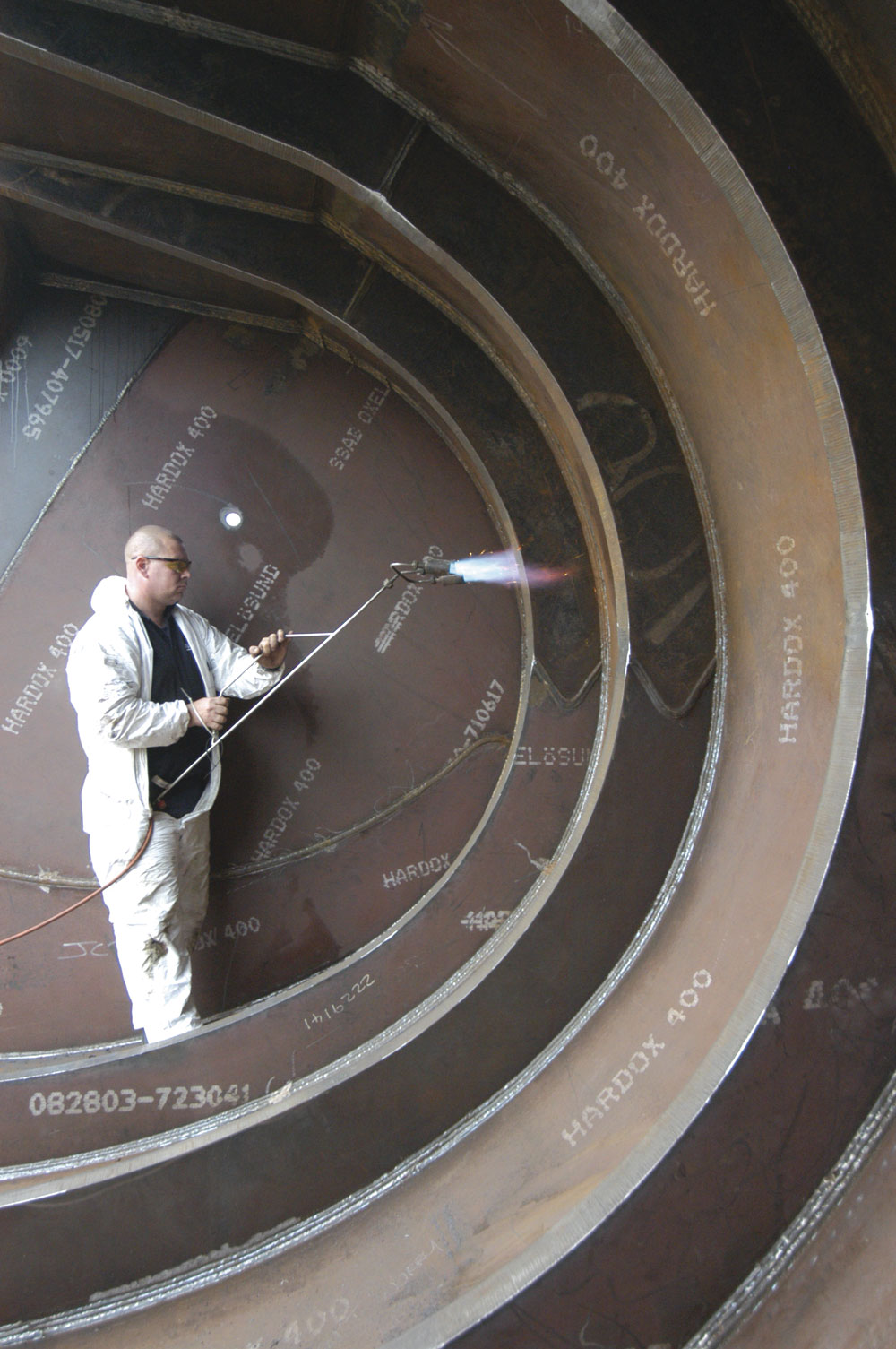
MST outline the market trends in bucket repair and refurbishment, and buying new buckets
MST, manufacturers of high-specification buckets and attachments, say they have noticed – in the current economic climate – a marked increase in the level of customers enquiring about repairing and refurbishing worn-out buckets, as opposed to replacing them with new ones.
Rory Whitehall, sales director at MST, explained: ‘Two to three years ago, we would have said bucket refurbishment and repair accounted for no more than 5% of our income. Ever since the early years of the business, bucket refurbishment and repair was an avenue we had always catered for, but there simply wasn’t a huge call for it from our customers.’
Indeed, many of the company’s sales have been in the undercarriage area (65%) and almost a third in bespoke, newly manufactured buckets.
However, in the last 18 months, bucket refurbishment and repair sales have more than doubled for MST. ‘Bucket repairs now account for more than 10% of our income,’ continued Mr Whitehall. ‘It is now so much more than a simple add-on.’
With depots in Scotland and the West Midlands, MST have a team of eight staff working on bucket repair/refurbishment. Heading the team is Alan Barnes, who was brought into the company three years ago to grow that section of the business.
‘For obvious reasons, everyone is currently looking at ways to save money,’ commented Mr Barnes. ‘With a refurbished bucket costing a third of the price of a new one, we understand why their popularity is growing.’
MST say they are well equipped to meet the rising demand for repaired/refurbished buckets, as one of the company’s major priorities is to ensure a reduction in attachment downtime for its customers.
MST have a full on-site inspection and servicing facility, and provide loan buckets for the most popular excavator and loader types. They have also recently introduced a special weekend service for customers in the UK where they will collect the worn bucket on Friday and have the fully refurbished attachment delivered back to site on Monday morning.
‘We listen hard to our customers, and the thing they worry about most with refurbishment is idle time,’ said Mr Barnes. ‘We’ve shaped our service to ensure we do all we can to reduce that downtime to an absolute minimum.’
MST are also providing their refurbishment and repair services to the overseas market through their ‘wear package’ programme. Under the scheme, the company can supply a full set of replacement parts, including new wear plates, teeth, undersides, shoulders and domite sections.
‘The overseas market is something we are beginning to explore with our new wear packs,’ said Mr Barnes. ‘The economics don’t always add up, but we have been out to Finland recently to help a customer with their refurbishment requirements.’
In addition to providing repair and refurbishment services, the market for new buckets is still a key area for MST. One of the company’s longest-serving customers, Jones Bros., has been using MST’s bespoke solutions, including their bucket repair and undercarriage services, for more than 15 years.
In the undercarriage market, MST say many customers are now turning to new parts rather than repairs and refurbishment. Several years ago, it was cost efficient to refurbish/repair tracks, idlers and rollers due to the perceived high costs of buying new parts.
Today, however, customers are starting to see that for just a small extra investment in parts, such as the MST expander pins, they are buying a much more hard-wearing product with a longer lifespan.
‘Technology has caught up,’ said Rory Whitehall. ‘It means buying new is not that much more expensive than refurbishing worn undercarriage parts. We are constantly sourcing new suppliers of our raw materials and products, and the costs have come down dramatically because of that.
‘The immediate impact for buckets may well follow that pattern, where good-quality products can be sourced from the Far East at a smaller cost. We might see a slight levelling out of the costs of new versus refurbished in years to come, and the current popularity of refurbishment might just start to wane.’
One source of material that MST refuse to comprise on is the use of Hardox steel for their newly manufactured buckets. Mr Whitehall continued: ‘MST buckets are known as being one of the hardest wearing in the industryy. When you create a reputation like that, it’s hard to turn your back on all the products and suppliers that have got you there.
‘We know we won’t be the cheapest new bucket manufacturer, but we are comfortable with that, knowing there is absolutely no compromise on the quality. It’s why we think both our new bucket and refurbishment operations will continue to thrive side by side for many years to come.’
MST, Nortrac Works, Shadon Way, Portobello Industrial Estate, Birtley Co., Durham DH3 2SW; tel: (0191) 4105311; fax: (0191) 4105311; email: websales@msttracks.com